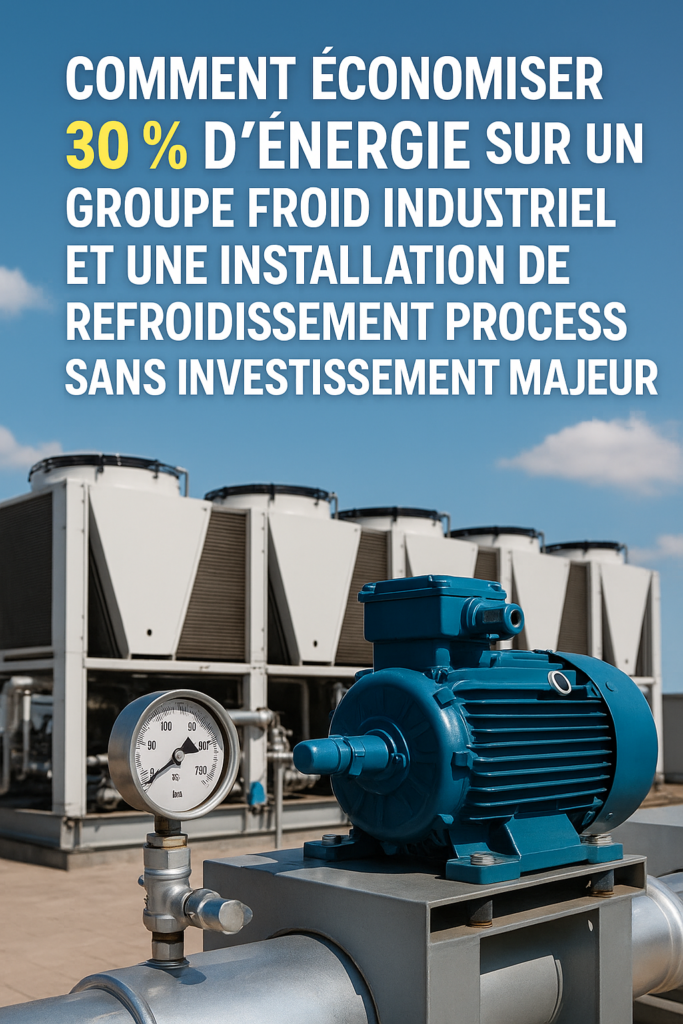
Dans l’industrie, le fonctionnement d’un groupe froid et d’une installation de refroidissement process représente souvent 20 à 40 % de la facture énergétique d’un site. Pourtant, sans engager de lourds investissements, il est possible de réaliser jusqu’à 30 % d’économies simplement en optimisant l’existant.
Cet article ultra-technique, riche en trucs et astuces, vous guide étape par étape vers une performance énergétique améliorée, en agissant avec bon sens, méthode, et pragmatisme.
1. 🧠 Comprendre d’abord où l’énergie est gaspillée
Avant toute action, il est essentiel d’identifier les sources majeures de pertes :
- Températures de consigne excessivement basses → Surconsommation électrique inutile.
- Pressions de condensation élevées → Plus d’effort pour les compresseurs.
- Surcharges thermiques inutiles → Mauvaise utilisation de l’équipement.
- Encrassement des échangeurs → Baisse des rendements thermiques.
- Pertes d’eau / fuites d’air sur les circuits auxiliaires.
- Arrêts/redémarrages fréquents → Moins bon rendement.
- Séquences de compresseurs non optimisées.
Bon à savoir :
Un simple écart de 1°C en consigne peut représenter 2 à 4 % d’économie d’énergie !
2. 🎯 Actions immédiates sur les groupes froids pour des gains rapides
2.1 Relever la consigne de température
🔧 Astuce pratique :
- Analyser précisément les besoins process réels.
- Remonter la température de consigne de 1°C à 3°C si possible.
Exemple : Passer de -7°C à -5°C peut déjà réduire la consommation de 4 à 6 % sans impacter la qualité produit.
Attention : Respecter les contraintes process critiques (sécurité alimentaire, normes ISO…).
2.2 Optimiser la pression de condensation
Un condenseur qui condense à 45°C au lieu de 35°C entraîne une surconsommation importante.
🔧 Actions clés :
- Vérifier l’état des échangeurs (condenseurs).
- Nettoyer les ailettes / tubes (poussières, calcaire, graisse…).
- Ajuster la régulation des ventilateurs (mode flottant conseillé).
- Activer l’option de flottement de pression de condensation si disponible.
Bon à savoir :
Chaque degré de réduction de la pression de condensation permet de gagner 1 à 2 % de consommation électrique.
2.3 Assurer un bon entretien des échangeurs
🔧 Checklist rapide :
- Nettoyage des condenseurs aérauliques ou hydrauliques (décrassage haute pression adaptée).
- Vérification de la perte de charge initiale vs actuelle.
- Traitement anticalcaire éventuel sur circuit d’eau de refroidissement.
Bon à savoir :
Un condenseur encrassé de 2 mm de tartre peut entraîner une surchauffe de 10 % du compresseur.
2.4 Optimiser la séquence des compresseurs frigorifiques
Si plusieurs groupes sont en place :
- Mettre un groupe principal en priorité (le plus récent ou le plus performant).
- Garder les autres en secours automatique.
Astuce :
Utiliser des séquences principal/secondaire basées sur l’efficacité énergétique de chaque machine.
Exemple concret :
Ne pas faire tourner en parallèle deux petits groupes inefficaces si un seul gros groupe peut suffire temporairement.
2.5 Réglage optimal des ventilateurs
Dans les condenseurs aérauliques :
- Utiliser la vitesse variable si disponible.
- Optimiser le seuil de déclenchement.
- Définir des rampes de modulation douces.
Effet : Jusqu’à 10 % d’économie supplémentaire sur le fonctionnement auxiliaire.
3. 📏 Côté installation process : interventions faciles et efficaces
3.1 Supprimer les surcharges inutiles
Erreurs classiques :
- Circulation d’eau froide dans des équipements non utilisés.
- Refroidissement « permanent » de lignes process arrêtées.
🔧 Actions :
- Installer des vannes manuelles / électrovannes.
- Ajouter un pilotage simple avec détecteurs de fonctionnement.
Exemple concret :
Couper le refroidissement d’un process à l’arrêt = économie immédiate de 5 à 8 %.
3.2 Améliorer l’isolation thermique
🔧 Zones prioritaires :
- Réseaux d’eau glacée.
- Réservoirs tampon.
- Chambres froides.
Vérifier et réparer :
- Isolants endommagés, manquants, humides.
Bon à savoir :
Une canalisation d’eau glacée non isolée de 10 mètres peut coûter jusqu’à 500 €/an en pertes thermiques.
3.3 Contrôler et ajuster les débits d’eau
Défaut fréquent :
Débit d’eau surdimensionné → énergie pompée inutilement.
🔧 Solutions simples :
- Réduction des débits sur pompes fixes (bypass, réglage vannes).
- Vérification des régulations automatiques.
4. 📈 Mesurer pour mieux piloter : le suivi énergétique
Même sans système SCADA ou GTC coûteux, il est possible d’assurer un monitoring énergétique basique :
Outil | Usage | Coût | Effet |
---|---|---|---|
Manomètre différentiel | Suivre pertes condenseurs/évaporateurs | 30 € | Diagnostic facile |
Thermomètre infrarouge | Contrôler températures échangeurs | 50 € | Détecter anomalies rapidement |
Compteur kWh clipsable | Suivi de la consommation électrique du groupe | 80 € | Mesure directe de gains |
Astuce terrain :
Créer un tableau Excel pour relever consommations mensuelles, consignes de température, pressions, et températures ambiantes.
5. 📊 Simulation d’économie réelle
Exemple type : Groupe froid de 100 kW électrique installé.
Action | Gain estimé | Impact |
---|---|---|
Remonter consigne de +2°C | 5 % | -5 kW |
Nettoyage condenseur | 8 % | -8 kW |
Optimisation séquence compresseurs | 6 % | -6 kW |
Optimisation ventilateurs | 3 % | -3 kW |
Isolation des tuyauteries | 5 % | -5 kW |
Coupure automatique de process non utilisés | 4 % | -4 kW |
Total :
30 % de réduction soit 30 kW économisés → ~26 000 € économisés/an sur une base de 8000 heures de fonctionnement et un prix de 0,11 €/kWh.
6. ♻️ Bonus : Impact carbone des économies
Réduction d’empreinte carbone associée :
- 1 kWh économisé = 0,08 kg de CO2 évité (moyenne européenne).
- 30 000 kWh/an économisés = 2,4 tonnes de CO2/an évitées.
Un double gain : Économie financière + réduction des émissions = valeur ajoutée pour vos audits RSE, ISO 14001, ou pour valoriser vos démarches clients.
🏆 En résumé
Optimiser l’efficacité énergétique d’un groupe froid industriel sans investissement majeur, c’est possible, rapide et rentable.
Les clés du succès :
- Agir sur les réglages et l’entretien plutôt que de remplacer immédiatement.
- Former et impliquer les techniciens et opérateurs.
- Suivre régulièrement les performances.
- Décider sur des mesures simples, mesurables et vérifiables.
En appliquant rigoureusement ces bonnes pratiques, vous pourrez atteindre jusqu’à 30 % d’économies d’énergie, voire davantage, tout en prolongeant la durée de vie de vos équipements !
🔧 Astuces techniques, bonnes pratiques, réglages intelligents et maintenance préventive pour booster l’efficacité énergétique immédiatement.
1. Pourquoi Chaque Kilowatt Compte ?
- Impact direct du coût énergétique sur les groupes froids industriels
- Lien entre refroidissement process et productivité industrielle
- Objectif : 20 % à 30 % d’économie sans changer tout l’équipement
2. Comprendre les Bases du Fonctionnement Thermodynamique
2.1 Petit rappel : comment fonctionne un groupe froid industriel
- Détente – évaporation – compression – condensation
- COP (Coefficient de Performance) : votre indicateur clé
2.2 Les zones critiques de surconsommation
- Excès de pression de condensation
- Mauvaise surchauffe ou sous-refroidissement
- Encrassements internes invisibles mais dévastateurs
3. Optimisation par Réglages Fins (sans gros investissement)
3.1 Baisser la pression de condensation
- Pourquoi c’est la clé N°1 d’économies massives
- Astuce : comment régler correctement la haute pression selon la température ambiante
- Bon à savoir : limiter le fonctionnement continu des ventilateurs
3.2 Ajuster la surchauffe au plus juste
- Effet direct sur le COP
- Comment contrôler et ajuster la surchauffe avec un simple mano et thermomètre
3.3 Abaisser légèrement la pression d’évaporation
- Comment gagner 5 à 10 % d’énergie avec un simple réglage
- Attention aux limites de fonctionnement de l’évaporateur
4. Maintenance et Nettoyage : Un Gisement Caché d’Économies
4.1 Nettoyer régulièrement les échangeurs (condenseur + évaporateur)
- Pourquoi 1 mm de saleté = +15 % de consommation
- Astuce : fréquence de nettoyage recommandée selon l’environnement industriel
4.2 Vérifier et entretenir les ventilateurs et pompes
- Équilibrage, alignement, nettoyage : des gains rapides
- Signes qui montrent qu’un ventilateur “fatigue” et surconsomme
4.3 Contrôler les niveaux de fluide frigorigène
- Manque ou excès = baisse drastique du rendement
- Test simple pour détecter une fuite lente sans station complexe
5. Piloter l’Installation Plus Intelligemment
5.1 Mettre en place des consignes de température plus réalistes
- Pourquoi on sur-refroidit souvent pour rien
- Comment gagner 3 % à 5 % d’énergie par degré de consigne ajusté
5.2 Prioriser la coupure automatique des équipements
- Asservir la production de froid à la vraie demande
- Astuce : installer des minuteries ou des relais simples pour éviter la marche “à vide”
5.3 Surveillance continue « low tech » avec quelques capteurs
- Températures d’eau de process
- Pressions d’évaporation/condensation
- Enregistrer simplement sur Excel pour détecter les dérives
6. Optimiser la Distribution d’Eau de Refroidissement
6.1 Supprimer les pertes de charge inutiles
- Vérifier les vannes, tuyaux, échangeurs encrassés
- Astuce : comment détecter une perte de charge anormale sans débitmètre
6.2 Ajuster la vitesse des pompes de circulation
- Pourquoi parfois ralentir un peu = énorme économie
- Techniques simples de réglage manuel
6.3 Isolation thermique des réseaux
- Même sur quelques mètres : jusqu’à 5 % d’économie
- Matériaux simples et retour sur investissement ultra-rapide
7. Et si l’air extérieur devenait votre meilleur allié ?
7.1 Utiliser le free-cooling dès que possible
- Abaisser naturellement la température de l’eau sans consommer plus
- Astuce : clapets ou by-pass manuels à bas coût
7.2 Optimiser les échangeurs air/eau
- Nettoyage + bonne orientation = moins de charge frigorifique nécessaire
- Exemple pratique : gain de 7 % sur une installation industrielle existante
8. Focus sur le Comportement des Opérateurs
8.1 Former à la “culture de l’énergie”
- Pourquoi expliquer aux utilisateurs l’intérêt de la consigne correcte
- Astuce : tableau d’affichage simple des gains mensuels
8.2 Éviter les manipulations inutiles
- Mauvais réglages = surconsommation chronique
- Procédures simples pour maintenir les réglages d’origine
9. Résultats Attendus : Simulation de Gains
9.1 Exemples de gains sur installation existante 100 kW frigorifique
- Avant : 0,85 COP / Après : 1,15 COP
- Réduction de 25 à 30 % de la consommation annuelle
- Estimation du gain financier brut annuel
9.2 Lien direct avec le Bilan Carbone
- Réduction des kWh = Réduction des émissions CO₂
- Impact positif sur l’empreinte environnementale
10. Passer à l’Action Dès Maintenant
- Prioriser les actions à “0 €” ou faibles coûts
- Mesurer > Ajuster > Maintenir
- L’énergie la moins chère est celle que vous n’avez pas consommée
📋 Tableau Synthèse – Optimiser un Groupe Froid Industriel et un Refroidissement Process sans Gros Investissement
Action | Effet attendu | Coût | Commentaire technique |
---|---|---|---|
1. Baisser la pression de condensation | Gain de 5 à 10 % d’énergie | 0 € | Ajustement simple des régulations ou thermostat |
2. Ajuster la surchauffe au plus juste | Amélioration du COP de 2 à 5 % | 0 € | Réglage détendeur manuel ou électronique |
3. Nettoyer condenseurs/évaporateurs | Gain de 10 à 15 % d’énergie | Faible (nettoyant spécifique ou eau sous pression) | Récurrence : 2 à 4 fois/an selon environnement |
4. Vérifier/entretenir ventilateurs et pompes | Gain de 2 à 4 % | 0 € à très faible (maintenance interne) | Contrôle équilibrage et alignement, graissage éventuel |
5. Corriger les niveaux de fluide frigorigène | Gain de 5 à 8 % | Faible (contrôle + appoint éventuel) | Evite les surconsommations et usures prématurées |
6. Ajuster les consignes de température process | Gain de 3 à 5 % par °C | 0 € | Souvent sur-refroidissement inutile en production |
7. Asservir fonctionnement ventilateurs/pompes à la demande | Gain de 5 à 10 % | Très faible (relais ou minuterie) | Limite le fonctionnement à vide |
8. Installer quelques capteurs basse technologie (pression/température/débit) | Surveillance + détection précoce de dérives | Faible coût (100-500 €) | Permet un pilotage très efficace sans gros SCADA |
9. Supprimer les pertes de charge dans les circuits d’eau | Gain de 3 à 6 % | Faible (reprise de tuyauteries ou nettoyage) | Vérifier filtres, vannes partiellement fermées |
10. Optimiser l’isolation des réseaux d’eau | Gain de 2 à 5 % | Faible (matériau isolant) | Priorité aux points sensibles (sortie de groupe, vannes, brides) |
11. Exploiter le free-cooling extérieur | Jusqu’à 15 % d’économie saisonnière | Faible (by-pass manuel ou clapets) | Fonctionne idéalement en mi-saison/hiver |
12. Sensibiliser et former les opérateurs | Gain global de 5 à 10 % par bonnes pratiques | 0 € (interne) | Culture de la consigne juste et de l’arrêt intelligent |
13. Mettre en place un tableau de suivi simple (Excel) | Suivi des dérives = économies pérennes | 0 € | Mesurer pour piloter ! |
📈 En résumé :
- Effet cumulatif potentiel : 20 à 35 % d’économie d’énergie selon l’état initial de l’installation.
- Coût global estimé : quasiment nul à quelques centaines d’euros maximum.
- Retour sur investissement : immédiat (dès les premières factures d’électricité).
Modèle de tableau de suivi énergétique mensuel avant/après optimisation, pensé de manière pratique et professionnelle pour :
- Suivre la consommation énergétique réelle.
- Comparer avant et après les actions d’optimisation.
- Calculer automatiquement les gains en énergie, en euros, et éventuellement en CO₂ évité.
📋 Modèle de Tableau de Suivi Énergétique Mensuel (Avant / Après Optimisation)
Mois | Énergie Consommée Avant (kWh) | Énergie Consommée Après (kWh) | Économie (kWh) | % Économie | Coût Énergie Avant (€) | Coût Énergie Après (€) | Économie (€) | Émissions CO₂ Évitée (kg) | Commentaires |
---|---|---|---|---|---|---|---|---|---|
Janvier | |||||||||
Février | |||||||||
Mars | |||||||||
Avril | |||||||||
Mai | |||||||||
Juin | |||||||||
Juillet | |||||||||
Août | |||||||||
Septembre | |||||||||
Octobre | |||||||||
Novembre | |||||||||
Décembre |
🛠️ Explication rapide de chaque colonne :
Colonne | Utilité |
---|---|
Énergie Consommée Avant (kWh) | Mesures ou factures avant optimisations. |
Énergie Consommée Après (kWh) | Mesures après mise en œuvre des actions d’économie. |
Économie (kWh) | Différence entre Avant et Après. (formule = Avant – Après) |
% Économie | Pourcentage de gain d’énergie. (formule = (Économie / Avant) × 100) |
Coût Énergie Avant (€) | Coût basé sur prix du kWh (ex. 0,12 €/kWh) |
Coût Énergie Après (€) | Idem mais après actions. |
Économie (€) | Gain financier mensuel. (Avant € – Après €) |
Émissions CO₂ Évitée (kg) | Conversion standard : 0,084 kg CO₂/kWh électrique (valeur moyenne France) |
Commentaires | Anomalies, événements spéciaux (canicule, travaux, etc.) |
🎯 Objectif final :
- Visualiser très vite l’impact des optimisations.
- Communiquer facilement avec la direction / responsables techniques.
- Détecter rapidement les mois atypiques pour corriger.
Checklist action rapide, conçue spécifiquement pour les techniciens de maintenance industrielle, frigoristes, ou intervenants sur groupes froids et installations de refroidissement process.
Elle est sous forme de tableau imprimable, claire, pratique, et directement actionnable en intervention :
📋 Checklist Action Rapide – Optimisation Énergétique Groupes Froids et Installations de Refroidissement
N° | Action | Détail / Astuce | Fréquence conseillée | Coche ✅ |
---|---|---|---|---|
1 | Vérifier les filtres à air d’admission | Nettoyer ou remplacer si colmatage (>350 mbar de perte) | Mensuel | ⬜ |
2 | Contrôler et nettoyer les échangeurs thermiques (condenseurs, évaporateurs) | Détartrer, dépoussiérer pour maintenir efficacité | Mensuel / Trimestriel | ⬜ |
3 | Mesurer la pression d’évaporation et de condensation | Surveiller les dérives, ajuster si besoin | Mensuel | ⬜ |
4 | Vérifier la consigne de température | Ajuster au plus haut tolérable pour le process | Semestriel | ⬜ |
5 | Surveiller les ventilateurs | Nettoyage des pales, contrôle vibrations | Trimestriel | ⬜ |
6 | Inspecter les purgeurs d’eau et les drains automatiques | Remplacer si défaillants pour éviter perte d’efficacité | Trimestriel | ⬜ |
7 | Vérifier l’isolation des tuyauteries et équipements froids | Réparer si endommagée ou manquante | Semestriel | ⬜ |
8 | Contrôler les pressostats et thermostats de régulation | Réglage fin pour éviter surconsommation | Annuel | ⬜ |
9 | Rechercher les fuites de fluide frigorigène | Utiliser détecteur spécifique / Visite annuelle obligatoire | Annuel | ⬜ |
10 | Mesurer la consommation électrique globale | Comparer aux historiques / détecter surconsommation | Mensuel | ⬜ |
11 | Contrôler les réglages de séquence des compresseurs | Prioriser un compresseur efficace + secours auto | Semestriel | ⬜ |
12 | Installer ou vérifier présence de manomètres différentiels | Lecture rapide des pertes de charge | À l’installation / Remplacement si HS | ⬜ |
13 | Ajuster la plage de régulation de pression | Éviter les plages trop courtes générant surconsommation | Annuel | ⬜ |
14 | Installer un suivi simple (compteur kWh / enregistreur) | Facilite détection immédiate des dérives énergétiques | Dès que possible | ⬜ |
15 | Sensibiliser les opérateurs au bon usage des équipements | Petits gestes = grandes économies (portes fermées, pas d’obstructions) | Annuel / Affichage permanent | ⬜ |
🔧 Conseils pratiques pour l’utilisation de cette checklist :
- Imprimer et plastifier pour un usage terrain durable.
- Utiliser en routine préventive, mais aussi après toute intervention corrective.
- Former rapidement les nouveaux techniciens à son usage.
- Archiver chaque checklist remplie pour constituer une traçabilité énergétique.
- Analyser les points récurrents pour planifier les investissements si besoin.
En somme, l’ingénierie des fluides industriels est une discipline importante et diversifiée qui joue un rôle clé dans de nombreuses industries. Elle nécessite une expertise technique et une connaissance approfondie des systèmes de circulation des fluides, de la thermodynamique, de la mécanique des fluides, de la régulation et du contrôle des processus, ainsi que de la sécurité.
Notre blog est une ressource complète pour tout ce qui concerne les fluides industriels. Nous vous encourageons à explorer nos articles, nos guides pratiques et nos ressources de formation pour approfondir vos connaissances et améliorer vos performances énergétiques. N’hésitez pas à nous contacter pour bénéficier de nos services d’ingénierie personnalisés ou pour trouver les produits dont vous avez besoin via notre site de commerce en ligne. Ensemble, nous pouvons aller plus loin dans l’apprentissage et réaliser des économies d’énergie significatives. Contactez-nous dès aujourd’hui à l’adresse suivante :
- Guide pour choisir un groupe froid industriel
- Lien : Exemple de schémas d’installation
- Lien : Calcul de la puissance nécessaire et facteurs de corrections usuels
- Le Guide Ultime du Choix des Compresseurs Frigorifiques : Optimisation, Puissance et Régulation
- Installation optimale de groupes froids industriels : Pratiques essentielles et paramètres clés
- Guide : La mise en service initiale d’un groupe froid industriel
- Les Applications du Refroidissement Industriel dans Divers Secteurs
- Guide Pratique pour le Choix d’un Groupe Froid Industriel : Calculs, Installations, Méthodes, Besoins et Critères Essentiels
- Optimiser l’Efficacité Énergétique : Deux Méthodes Ingénieuses pour Récupérer la Chaleur d’un Groupe Froid Industriel
- Guide Pratique : Récupération de Chaleur sur Groupe Froid – Avantages et Mise en Œuvre
- Innovations et Stratégies Avancées dans le Refroidissement Industriel: Vers une Ère Durable et Efficace
- Optimisation Cruciale: Les Répercussions d’un Réseau Industriel Mal Équilibré sur la Performance et la Sécurité
- Optimisation du Dimensionnement des Tuyauteries : Préserver la Pression et Réduire les Pertes de Charge
- Calculs et dimensionnement, installation, optimisation et Maintenance des Groupes Froids Industriels : Guide Complet pour Calcul de Puissance, Facteurs de Correction, et Technologies de Contrôle
- La conception d’un système de refroidissement industriel (Industrial Cooling System)
- Révolutionner le Froid Industriel et le Refroidissement Process avec l’IoT et l’IA : Entre Solutions High Tech, Low Tech, et Approches Hybrides
- Optimiser le Refroidissement Process avec l’IoT et l’IA : Révolutions et Techniques pour les Groupes Froids et Groupes d’Eau Glacée Industriels
- Révolution Technologique des Groupes Froids Industriels et Groupes d’Eau Glacée : Quand l’IA et les IoT Façonnent l’Avenir du Refroidissement Industriel
- FAQ : Groupes Froids Industriels et au Refroidissement Process
- Questions / réponses fréquemment posées sur le thème du refroidissement de process, incluant l’eau glacée, le froid industriel, les groupes froids, et les groupes d’eau glacée
- Quelles sont les erreurs courantes à éviter lors du choix d’un groupe froid industriel pour le refroidissement de son process ?
- Refroidissement Industriel : L’Essentiel sur les Groupes Frigorifiques et les Groupes d’Eau Glacée
- Lien: Notions de base
- Lie0n : Fonctionnement des systèmes de réfrigération
- Lien : applications du froid industriel
- Lien : Avantages et inconvénients
- Lien : En conclusion, le froid industriel est un élément clé de nombreuses industries modernes
- Lien : mesure de débit ultrasonique
- Mesure de Débit d’Eau par Ultrasons : Optimisation des Process Industriels
- Lien : Vitesse des fluides dans les tuyauteries
- Pour réaliser des économies d’énergie avec les installations d’eau glacée (froid industriel)
- Lien : Retrouver la performance de vos échangeurs avec le peigne frigoriste (groupe froid industriel, sécheur air comprimé, …)
- Lien : Réfractomètre : Mesurez facilement la concentration en glycol essentielle pour assurer la sécurité et la performance des installations industrielles
- Lien : Analyse d’huile des équipements : Optimisez la maintenance industrielle (compresseur air comprimé, groupe froid industriel, …)
- Les avantages de la connectivité IoT et I.A. dans les groupes froids industriels : Comment tirer parti des données pour améliorer les performances
- Les tendances émergentes dans les groupes froids industriels : Les nouvelles technologies qui transforment l’industrie du refroidissement
- La sélection du groupe froid industriel adapté à vos besoins : Guide d’achat et recommandations pour une solution optimale
- La sécurité dans les groupes froids industriels : Conseils pour prévenir les accidents et assurer la conformité aux normes de sécurité
- Maximisez la fiabilité de votre groupe froid industriel : Les meilleures pratiques pour éviter les pannes et les temps d’arrêt coûteux
- La maintenance préventive des groupes froids industriels : Astuces pour prolonger la durée de vie de votre équipement
- Les solutions respectueuses de l’environnement pour les groupes froids industriels : Astuces pour réduire l’empreinte carbone de votre installation
- La gestion intelligente des groupes froids industriels : Comment utiliser les systèmes de contrôle avancés pour optimiser les performances
- Les dernières avancées en matière de groupes froids industriels : Les technologies innovantes qui améliorent les performances
- Groupe froid industriel : Optimisez les économies d’énergie en adaptant vos consignes de température
- Optimisez l’efficacité énergétique de votre groupe froid industriel : Astuces pratiques pour réduire la consommation d’énergie
- Maîtrisez la poussière : Astuces innovantes et simples pour protéger vos équipements avec des filtres d’air comprimé dans les environnements poussiéreu
Lien pour achats :