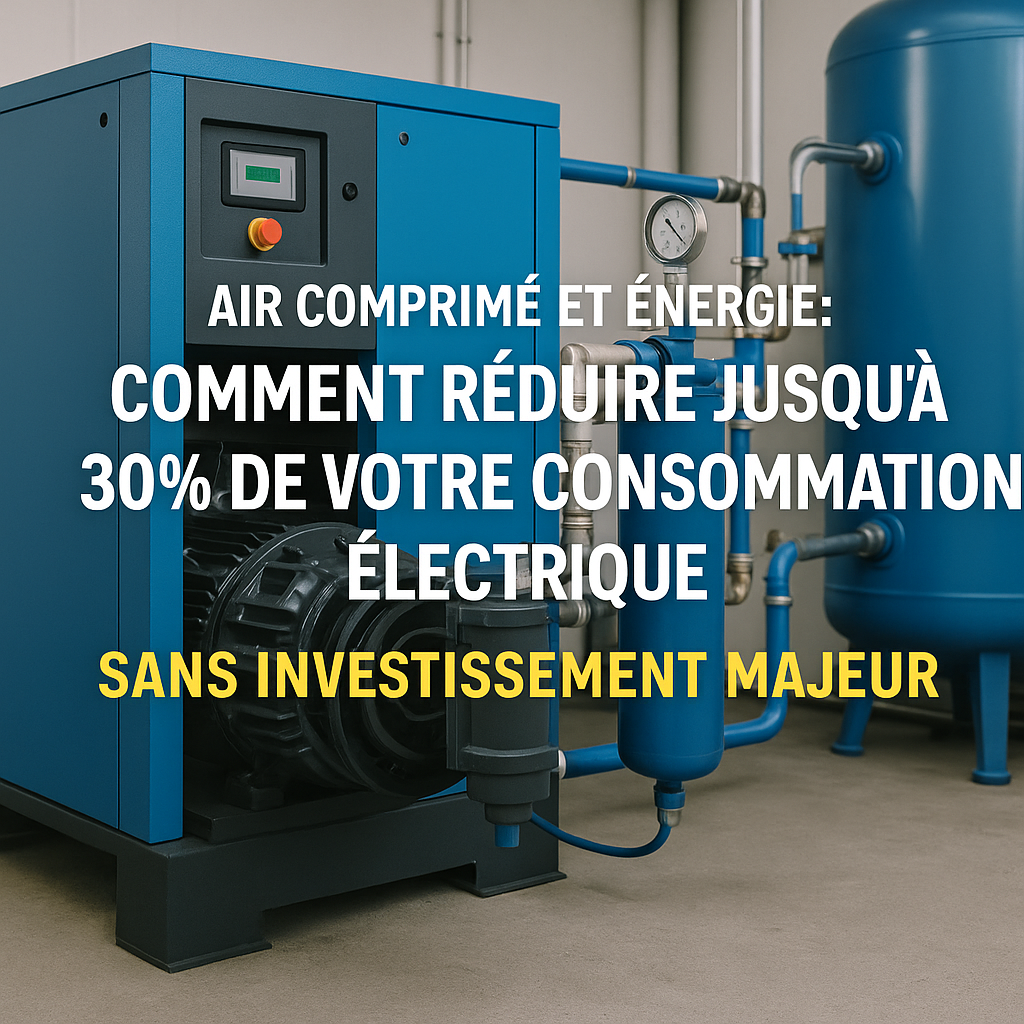
L’air comprimé est indispensable dans l’industrie moderne. Il fait fonctionner les outils, les machines, les systèmes d’automatisation… Pourtant, peu de responsables industriels ont conscience du véritable coût énergétique de ce « quatrième fluide ». Pourquoi ? Parce que jusqu’à 90% de l’énergie utilisée pour produire de l’air comprimé est perdue en chaleur, en fuites, en surpression, ou en mauvais dimensionnements.
👉 Cet article a pour objectif de vous ouvrir les yeux, mais surtout de vous armer d’actions concrètes pour réduire les pertes, mesurer les gains, et optimiser durablement vos installations.
1. L’air comprimé : un fluide énergivore par nature
1.1 Une efficacité énergétique historiquement faible
Contrairement à l’électricité ou à la vapeur, l’air comprimé est très coûteux à produire. Il faut environ 7 à 8 kWh d’énergie électrique pour générer 1 m³ d’air comprimé à 7 bars. Mais attention, seulement 10% de cette énergie sera utile à l’utilisateur final. Le reste ? Perdu, principalement en chaleur lors de la compression.
🧠 À retenir :
- L’air comprimé est un fluide « luxueux ».
- 90% de l’énergie électrique injectée est dissipée.
- Il faut donc raisonner sobriété, efficacité, et recyclage.
1.2 Pourquoi l’air comprimé est si peu efficace ?
La compression de l’air engendre des pertes physiques :
- Chaleur (70 à 80% de l’énergie consommée)
- Fuites (20 à 40% de l’air comprimé produit selon les sites)
- Surpression (chaque bar inutile coûte +7% d’énergie)
- Mauvais rendements des équipements terminaux
- Tuyauteries sous-dimensionnées ou encrassées
2. Où part l’énergie ? Décryptage des déperditions majeures
2.1 La chaleur : ennemi ou opportunité ?
La majorité de l’énergie consommée par un compresseur est transformée en chaleur. Cette chaleur est :
- Dissipée dans l’air ambiant (refroidisseurs d’huile ou d’air)
- Perdue sans valorisation dans 80% des cas
🔥 Bon à savoir : Un compresseur de 75 kW peut rejeter jusqu’à 65 kW sous forme de chaleur utilisable !
👉 Solution concrète :
- Installer un système de récupération de chaleur pour :
- Chauffer un atelier
- Préparer de l’eau chaude sanitaire
- Préchauffer des process industriels
💡 Astuce : Une récupération bien dimensionnée peut faire économiser 10 000 à 20 000 € par an sur un compresseur de 75 à 100 kW en fonctionnement continu.
2.2 Les fuites : le cancer silencieux des réseaux d’air
C’est LA première source de gaspillage. Une simple fuite de 3 mm à 7 bars = 2700 € de pertes par an, 24h/24.
📊 Statistiques :
- En moyenne, 25 à 35% de l’air produit fuit dans les installations industrielles.
- Sur un réseau ancien, ce chiffre peut dépasser 40% !
👉 Solutions applicables immédiatement :
- Campagne de détection de fuites ultrasonore
- Étiquetage des points de fuite
- Mise en place de contrôles trimestriels
- Remplacement des raccords rapides non étanches
- Surveillance des zones non utilisées la nuit
🛠️ Outils recommandés :
- Caméra ultrasonique (type FLIR, UE Systems)
- Logiciels de suivi, …
- Check-list des points critiques : raccords, vannes, purgeurs, tubes PE rigides
2.3 La surpression : une dérive courante et coûteuse
La tentation est grande d’augmenter la pression pour « compenser » une faiblesse réseau. Or :
📉 Chaque bar de surpression = +7 à 8% de consommation électrique !
Et pire :
- Les outils consomment plus, sans gain de performance
- Les fuites s’aggravent (fuite ∝ √pression)
- Les compresseurs tournent plus = usure prématurée
👉 Solutions immédiates :
- Installer un régulateur de pression différentiel (PRV)
- Réduire la pression réseau par palier (0,2 bar tous les 2 jours)
- Utiliser un réservoir tampon pour absorber les pics
- Découpler les réseaux : outil sensibles / général
🎯 Objectif optimal : 6,5 bars réseau avec régulation dynamique.
3. Chiffres clés : L’ampleur des pertes énergétiques dans les réseaux
Type de perte | Pourcentage moyen | Coût estimé annuel (base 1 compresseur 75 kW) |
---|---|---|
Chaleur non valorisée | 70% | 10 000 à 25 000 € |
Fuites réseau | 20 à 35% | 5 000 à 12 000 € |
Surpression | 7% par bar | 2 500 à 6 000 € |
Mauvaise régulation | 5 à 10% | 2 000 à 8 000 € |
🧠 À méditer :
Sur un compresseur de 75 kW fonctionnant 6 000 h/an, les pertes non traitées peuvent dépasser 40 000 €/an.
4. Bon à savoir : Quel est le coût réel de l’air comprimé ?
4.1 Le coût moyen de production : un piège sous-estimé
❗ Trop de sites estiment leur coût d’air comprimé à 0,01 €/m³… Mais en intégrant électricité + maintenance + investissement, on atteint vite :
💰 0,015 à 0,035 €/m³ voire 0,05 €/m³ sur de petits réseaux.
4.2 Simulation concrète :
➡️ Réseau produisant 100 m³/h d’air à 7 bars
➡️ Fonctionnement 5j/7, 3x8h, 50 semaines/an = 120 000 m³/an
➡️ Coût moyen de production réel = 0,03 €/m³
📈 Coût annuel réel = 3 600 €
⚠️ Avec 30% de fuites → 1 080 € gaspillés
👉 Rajoutez surpression, chaleur non récupérée, purgeurs inefficaces… On peut atteindre 6 000 à 10 000 € de pertes cachées.
5. Solutions concrètes, mesurables et applicables dès maintenant
✅ Étape 1 : Mesurez votre réseau
- Installez un débitmètre thermique ou à effet vortex
- Ajoutez des capteurs de pression et température
- Utilisez des enregistreurs de données
- Créez un bilan énergétique de l’air comprimé
🎯 Objectif : avoir une courbe de charge réelle, et identifier les pics, les fuites, les dérives.
✅ Étape 2 : Détection et suppression des fuites
- Campagne trimestrielle de détection
- Équipez les opérateurs de spray moussant ou détecteur ultrason
- Instaurez un « fugitive leak protocol » en interne
- Remplacez systématiquement les raccords fuyards
💡 Astuce : créer un « contrat d’intéressement énergie » : si l’équipe réduit les pertes → prime collective.
✅ Étape 3 : Optimisez la pression
- Installez un contrôleur de pression intelligent
- Diminuez par paliers les consignes
- Scindez les zones à pression différenciée
📦 À retenir : chaque bar inutile, c’est 7% de conso en plus ET 10 à 20% de fuites aggravées.
✅ Étape 4 : Valorisez la chaleur
- Récupérez la chaleur pour :
- Eau chaude de process ou de chauffage
- Préchauffage d’air dans les zones de production
- Chaufferie secondaire
💡 Bon plan : certains fournisseurs proposent des kits de récupération prêts à poser avec échangeur + ventilation intégrée.
✅ Étape 5 : Pilotez et digitalisez votre réseau
- Mettez en place une supervision énergétique
- Suivez vos indicateurs (kWh/m³, % charge, % fuites)
- Programmez des alertes de dérive
- Intégrez à votre GMAO ou ERP
📊 Exemples de gains mesurés :
- -15% de consommation en 3 mois
- Retour sur investissement d’un débitmètre = < 6 mois
L’air comprimé n’est pas un « consommable gratuit », mais une énergie noble, précieuse et très coûteuse. L’optimisation de son usage est un levier de compétitivité majeur, souvent sous-exploité. En agissant dès aujourd’hui sur les pertes thermiques, les fuites, la pression et la récupération, vous pouvez réduire vos coûts de 20 à 40% en moins de 12 mois.
🛠️ Et surtout : tout commence par la mesure. Pas de pilotage sans instruments.
📌 Résumé des actions immédiates :
Action | Impact | ROI estimé |
---|---|---|
Détection de fuites | -10 à -25% | < 3 mois |
Baisse pression de 1 bar | -7% énergie | Immédiat |
Récupération chaleur | -15 à -20% global | 6 à 12 mois |
Suivi par capteurs | -10% conso | 3 à 6 mois |
Supervision énergétique | Visibilité + anticipation | Durable |
Besoin d’un diagnostic complet de votre réseau ou d’un accompagnement pour choisir vos capteurs, vos sécheurs ou vos équipements de récupération ? Contactez notre bureau d’ingénierie spécialisé en air comprimé industriel.
✉️ Contact : billaut.fabrice@gmail.com
🌐 www.envirofluides.com
En somme, l’ingénierie des fluides industriels est une discipline importante et diversifiée qui joue un rôle clé dans de nombreuses industries. Elle nécessite une expertise technique et une connaissance approfondie des systèmes de circulation des fluides, de la thermodynamique, de la mécanique des fluides, de la régulation et du contrôle des processus, ainsi que de la sécurité.
Notre blog est une ressource complète pour tout ce qui concerne les fluides industriels. Nous vous encourageons à explorer nos articles, nos guides pratiques et nos ressources de formation pour approfondir vos connaissances et améliorer vos performances énergétiques. N’hésitez pas à nous contacter pour bénéficier de nos services d’ingénierie personnalisés ou pour trouver les produits dont vous avez besoin via notre site de commerce en ligne. Ensemble, nous pouvons aller plus loin dans l’apprentissage et réaliser des économies d’énergie significatives. Contactez-nous dès aujourd’hui à l’adresse suivante :
- Guide Ultime pour Choisir le Compresseur d’Air Comprimé Idéal
- Guide Pratique pour la Mise en Service des Compresseurs d’Air Comprimé : Astuces et Bonnes Pratiques
- FAQ sur l’Air Comprimé : Optimisez Votre Énergie, Votre Fiabilité et Votre Productivité
- FAQ : foire aux questions spécifiques sur les cuves d’air comprimé
- FAQ : Sécheurs d’Air Comprimé à Détente Directe
- FAQ : Sécheurs d’Air Comprimé à Masse Thermique
- FAQ : Sécheurs d’Air Comprimé par Adsorption
- Configurations de Montage pour Compresseurs d’Air Comprimé : Optimisation, Performance et Intégration
- Guide Complet : Pourquoi de l’Eau Apparaît Lors de l’Utilisation de l’Air Comprimé et Comment Résoudre Ce Problème
- Guide complet pour choisir et dimensionner un compresseur comprimé : Méthodes, Besoins et Critères Essentiels (piston-s, vis, palettes, centifuge, )
- Guide complet pour choisir et dimensionner un sécheur d’air comprimé : Méthodes, Besoins et Critères Essentiels
- Guide Avancé pour la Sélection des Filtres d’Air Comprimé : Approche Technique, Scientifique et Pédagogique
- Guide Pratique pour le Choix d’une Cuve d’Air Comprimé : Matériau, Pression, Durée de Vie et Capacité
- Guide de Choix pour Purgeurs d’Air Comprimé : Économie d’Énergie et Gestion des Fuites
- Guide Complet pour Choisir et Dimensionner un Réseau d’Air Comprimé : Méthodes, Besoins et Critères Essentiels
- Optimiser l’Énergie : Deux Approches Innovantes pour Récupérer la Chaleur d’un Compresseur d’Air Comprimé
- Optimisation du Réseau d’Air Comprimé : Les Clés d’un Dimensionnement Stratégique
- Choisir le Diamètre Idéal pour Votre Tuyau d’Air Comprimé selon pression : Un Guide Technique Approfondi
- L’Impact des Fuites d’Air Comprimé sur le Débit : Guide Pratique
- Traitement air comprimé / Optimisation de la Qualité de l’Air Comprimé : Guide Complet
- Pourquoi l’eau peut être un problème dans un réseau air comprimé ?
- Traitement écologique et la gestion des condensats d’air comprimé
- Maîtrisez l’Air Comprimé : 10 Astuces pour Optimiser son Utilisation et Réduire les Coûts dans Votre Entreprise
- Comment Réduire les Pertes d’Énergie dans Votre Système de Distribution d’Air Comprimé
- Guide pour Choisir le Sécheur d’Air Comprimé Idéal pour Votre Entreprise
- Sécurité de l’Air Comprimé : Risques, Prévention et Protection
- Guide Essentiel de l’Air Comprimé : Questions Clés Répondues
- Les causes courantes de panne des sécheurs d’air comprimé?
- Mesurer le point de rosée sous pression dans votre système d’air comprimé est crucial pour garantir la qualité de l’air et prévenir les problèmes liés à l’humidité
- Guide ultime pour réparer votre compresseur d’air : Défauts courants, remèdes efficaces et conseils de maintenance
- La sélection du bon raccord rapide air comprimé
- Optimisation Cruciale: Les Répercussions d’un Réseau Industriel Mal Équilibré sur la Performance et la Sécurité
- L’Air Comprimé : Le Pouvoir Invisible au Cœur des Technologies Avancées et des Applications Insolites
- Révolutionner l’Air Comprimé avec l’IoT et l’IA : Entre Solutions High Tech, Low Tech, et Approches Hybrides
- Les Applications et Innovations des Systèmes d’Air Comprimé dans l’Industrie : Guide Complet
- L’Azote en Industrie : Production, Purification et Avantages
- Optimisation des Systèmes d’Air Comprimé : Techniques et Technologies pour Améliorer l’Efficacité Énergétique et Réduire les Coûts Opérationnels
- Lien : Cuves d’Air Comprimé : Déclaration, Vérification et Requalification pour la Sécurité Opérationnelle
- Lien : Exemples d’applications courantes pour des compresseurs d’air comprimé à différentes pressions
- Lien : . Comprendre l’air comprimé
- Lien : Comprendre les équipements d’air comprimé
- Lien : Sélection d’équipements d’air comprimé
- Lien: Les avantages de l’utilisation d’équipements d’air comprimé
- Lien : Maintenance et entretien des équipements d’air comprimé
- Il est important de noter que la conversion entre Nm3/h et m3/h est sensible aux variations de température et de pression, et une conversion précise nécessite des valeurs exactes pour ces paramètres
- FAQ sur l’Air Comprimé : Optimisez Votre Énergie, Votre Fiabilité et Votre Productivité
- Quels sont les matériaux couramment utilisés pour les tuyauteries d’air comprimé ?
- Air Comprimé et Écologie : Vers une Industrie Plus Verte et économie d’énergies
- Les Dangers de l’Air Comprimé et Comment les Éviter
- Maîtrisez la Filtration de l’Air Comprimé : Guide Approfondi sur le Changement et l’Entretien des Éléments Filtrants
- Optimisation de la Pulvérisation : Techniques Avancées pour l’Application de Peinture Automobile
- Régulateurs de Débit et de Pression pour Air Comprimé : Guide Technique et Scientifique
- Optimisation des Systèmes d’Air Comprimé : Techniques et Technologies pour Améliorer l’Efficacité Énergétique et Réduire les Coûts Opérationnels
- Régulation de Température de l’Air Comprimé en Industrie
- Innovations dans l’air comprimé : De la production à l’utilisation
- La conception d’un système d’air comprimé est une tâche complexe
Lien pour achats :