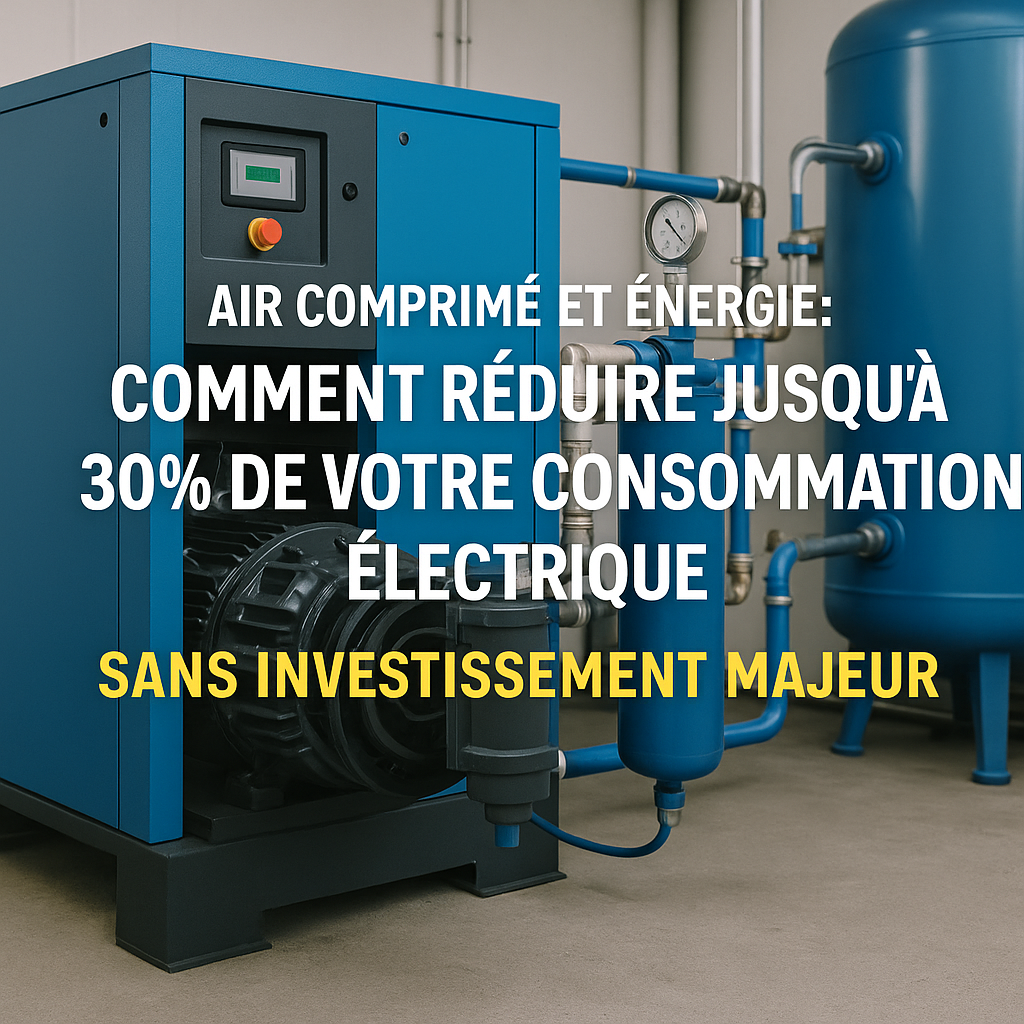
Dans le monde industriel, l’air comprimé est un fluide indispensable… mais aussi redoutablement coûteux. Parmi les leviers d’optimisation énergétique souvent sous-estimés, la réduction de la pression générale du réseau est l’un des plus efficaces, à condition d’être maîtrisé avec rigueur. En effet, abaisser la pression de seulement 1 bar permet en moyenne de réaliser jusqu’à 7 % d’économies d’énergie. Mais attention, la démarche doit être progressive et adaptée aux contraintes spécifiques de chaque installation.
Dans cet article, nous allons explorer en profondeur les enjeux, la méthodologie et les effets secondaires (parfois méconnus) liés à la baisse de pression dans un réseau d’air comprimé. Vous y trouverez également de nombreux bons à savoir, des trucs de terrain et des conseils d’experts pour une mise en œuvre réussie.
1. Pourquoi réduire la pression du réseau d’air comprimé ?
L’air comprimé est l’un des fluides les plus énergivores de l’industrie. On estime qu’à peine 10 % de l’énergie électrique absorbée par un compresseur se retrouve réellement sous forme d’énergie utile à l’outil final. Le reste part en chaleur, en pertes mécaniques et surtout… en pertes liées à la surpression.
1.1 La loi de la physique : 1 bar en moins = 7 % d’économie
C’est une règle d’or dans le monde de l’air comprimé. Chaque bar de pression en moins sur le réseau principal permet en moyenne de réaliser entre 6 % et 8 % d’économie d’énergie (la valeur usuelle retenue est 7 %). Pourquoi ? Parce que :
- Le compresseur travaille moins : donc consomme moins d’électricité.
- Les fuites (inévitables dans toute installation) deviennent mécaniquement moins importantes (car le débit de fuite diminue avec la pression).
- Les équipements en aval (soufflette, vérins, machines-outils…) consomment moins d’air pour la même efficacité dans bien des cas.
1.2 Ce qu’il faut bien comprendre : surpression = gaspillage
Il n’est pas rare de voir des installations fonctionner à 8 bar, voire 9 bar, « par sécurité », alors que les besoins réels des équipements tournent autour de 6 bar. Cette surpression chronique est souvent due à un manque de cartographie des besoins réels, une peur de la chute de performance, ou une tentative de compenser les fuites.
🧠 Bon à savoir : Une surpression de 1 bar sur une installation de 100 kW peut représenter plus de 6 000 € de surcoût énergétique annuel (à 0,12 €/kWh et 4 000 h de fonctionnement). Et encore, sans compter les effets domino sur les équipements en aval.
2. Comment abaisser la pression sans risque pour la production ?
2.1 Phase 1 : Audit technique précis
Avant toute action, il est impératif de mesurer et comprendre. Un audit de pression détaillé permettra :
- D’identifier la pression minimale réellement nécessaire sur chaque secteur de production.
- De repérer les points de chute de pression anormaux (souvent dus à un mauvais dimensionnement de tuyauterie ou des filtres encrassés).
- De localiser les équipements sensibles à la pression (soufflettes, agitateurs, visseuses, etc.).
🔧 Astuce pro : Utilisez des enregistreurs de pression temporaires type data loggers placés à divers points clés du réseau pour suivre les variations sur une semaine complète.
2.2 Phase 2 : Baisse progressive et contrôlée
Il est risqué de baisser brutalement la pression. Voici une méthode simple utilisée par les experts :
- Baisser par palier de 0,2 bar toutes les 48 à 72 heures.
- Observer les effets : performance des équipements, stabilité du réseau, retours des opérateurs.
- Continuer jusqu’à atteindre la limite basse acceptable (souvent autour de 6 bar dans l’industrie classique).
🧰 Truc terrain : Intégrez les opérateurs de production dans le processus ! Leur ressenti est un indicateur précieux de performance réelle.
3. Les effets domino positifs de la baisse de pression
3.1 Réduction automatique des fuites
C’est mathématique : la fuite étant liée à la pression différentielle, plus la pression est basse, moins le débit de fuite est important. Par exemple, une fuite de 3 mm à 8 bar consomme presque 12 m³/h, contre 10 m³/h à 6 bar.
💡 Bon à savoir : À l’année, cela représente environ 200 € d’économie par fuite. Multipliez par le nombre de microfuites, vous verrez l’impact.
3.2 Allègement de la consommation des outils pneumatiques
Un grand nombre d’équipements pneumatiques ne nécessite pas autant de pression qu’on le pense. En fait, la consommation d’air d’un vérin ou d’une soufflette augmente linéairement avec la pression.
📏 Exemple concret : Une soufflette utilisée 30 min/jour à 8 bar consomme environ 10 000 litres/mois. À 6 bar, ce chiffre tombe à 7 500 litres, soit 25 % de gain immédiat, sans perte d’efficacité dans 90 % des cas.
4. Cas pratiques et chiffres clés
4.1 Étude de cas : usine agroalimentaire
Contexte : Réseau fonctionnant à 8,5 bar, pressostat de démarrage compresseur réglé à 8 bar, arrêt à 9 bar. Beaucoup de soufflettes utilisées pour le nettoyage.
- Audit pression : besoins réels autour de 6,5 bar.
- Plan d’action : baisse par paliers sur 2 semaines, remplacement de quelques régulateurs sur les postes critiques.
Résultat :
- Baisse de 2 bar.
- Gain énergétique : 14 % sur la consommation globale du compresseur (équivalent à 9 800 €/an).
- Réduction significative des fuites et usure des composants.
5. Bonnes pratiques pour sécuriser la baisse de pression
✅ Installer des régulateurs locaux
Sur certains postes critiques, on peut augmenter la pression localement à l’aide de micro-régulateurs, tout en maintenant une pression générale plus basse.
🎯 Astuce : Installer des régulateurs auto-vidangeables avec filtres intégrés pour éviter les pollutions et garantir un air stable à pression ajustée.
✅ Optimiser le dimensionnement des tuyauteries
Une tuyauterie sous-dimensionnée crée des pertes de charge, ce qui oblige à augmenter la pression générée.
📌 Rappel : Pour un débit d’air donné, doubler le diamètre de la tuyauterie peut diviser par 4 la perte de charge !
✅ Ne pas négliger les traitements d’air
Les sécheurs, filtres, purgeurs doivent être régulièrement entretenus. Un filtre colmaté peut créer 0,3 à 0,5 bar de perte à lui seul.
🛠️ Truc terrain : Notez la pression avant et après chaque élément filtrant. Un écart > 0,2 bar = filtre en fin de vie.
6. Bonus : Calculer les économies potentielles liées à la baisse de pression
🔢 Formule simple
Économie annuelle estimée (kWh) = Puissance compresseur (kW) x heures de fonctionnement x % d’économie selon baisse (7 % par bar)
📈 Exemple chiffré
- Compresseur : 75 kW
- Fonctionnement : 4 000 h/an
- Baisse de pression de 1,5 bar
➡️ Économie : 75 x 4000 x (1,5 x 0,07) = 31 500 kWh
➡️ À 0,12 €/kWh = 3 780 € économisés par an
7. Pour aller plus loin : instrumentation & supervision
La gestion fine de la pression passe par une supervision continue :
- Pressostats connectés
- Débitmètres et compteurs m³
- Historique de pression sur cloud
- Alertes en cas de dérive
🧠 Bon à savoir : Certains systèmes IA/IoT analysent en temps réel les données pour proposer automatiquement des consignes de pression optimales selon l’activité de la production.
Moins, c’est Mieux !
La réduction de la pression générale d’un réseau d’air comprimé est un levier simple, efficace et économique à la portée de toutes les industries. Avec une approche progressive et méthodique, il est possible de réaliser des économies substantielles, améliorer la fiabilité des équipements et réduire l’empreinte carbone.
Souvenez-vous :
- 1 bar en moins = 7 % d’économie
- Baissez progressivement, validez les effets
- Ne jamais sacrifier la qualité de la production, mais remettre en question les « habitudes »
Et surtout : mesurez, testez, ajustez.
En somme, l’ingénierie des fluides industriels est une discipline importante et diversifiée qui joue un rôle clé dans de nombreuses industries. Elle nécessite une expertise technique et une connaissance approfondie des systèmes de circulation des fluides, de la thermodynamique, de la mécanique des fluides, de la régulation et du contrôle des processus, ainsi que de la sécurité.
Notre blog est une ressource complète pour tout ce qui concerne les fluides industriels. Nous vous encourageons à explorer nos articles, nos guides pratiques et nos ressources de formation pour approfondir vos connaissances et améliorer vos performances énergétiques. N’hésitez pas à nous contacter pour bénéficier de nos services d’ingénierie personnalisés ou pour trouver les produits dont vous avez besoin via notre site de commerce en ligne. Ensemble, nous pouvons aller plus loin dans l’apprentissage et réaliser des économies d’énergie significatives. Contactez-nous dès aujourd’hui à l’adresse suivante :
- Guide Ultime pour Choisir le Compresseur d’Air Comprimé Idéal
- Guide Pratique pour la Mise en Service des Compresseurs d’Air Comprimé : Astuces et Bonnes Pratiques
- FAQ sur l’Air Comprimé : Optimisez Votre Énergie, Votre Fiabilité et Votre Productivité
- FAQ : foire aux questions spécifiques sur les cuves d’air comprimé
- FAQ : Sécheurs d’Air Comprimé à Détente Directe
- FAQ : Sécheurs d’Air Comprimé à Masse Thermique
- FAQ : Sécheurs d’Air Comprimé par Adsorption
- Configurations de Montage pour Compresseurs d’Air Comprimé : Optimisation, Performance et Intégration
- Guide Complet : Pourquoi de l’Eau Apparaît Lors de l’Utilisation de l’Air Comprimé et Comment Résoudre Ce Problème
- Guide complet pour choisir et dimensionner un compresseur comprimé : Méthodes, Besoins et Critères Essentiels (piston-s, vis, palettes, centifuge, )
- Guide complet pour choisir et dimensionner un sécheur d’air comprimé : Méthodes, Besoins et Critères Essentiels
- Guide Avancé pour la Sélection des Filtres d’Air Comprimé : Approche Technique, Scientifique et Pédagogique
- Guide Pratique pour le Choix d’une Cuve d’Air Comprimé : Matériau, Pression, Durée de Vie et Capacité
- Guide de Choix pour Purgeurs d’Air Comprimé : Économie d’Énergie et Gestion des Fuites
- Guide Complet pour Choisir et Dimensionner un Réseau d’Air Comprimé : Méthodes, Besoins et Critères Essentiels
- Optimiser l’Énergie : Deux Approches Innovantes pour Récupérer la Chaleur d’un Compresseur d’Air Comprimé
- Optimisation du Réseau d’Air Comprimé : Les Clés d’un Dimensionnement Stratégique
- Choisir le Diamètre Idéal pour Votre Tuyau d’Air Comprimé selon pression : Un Guide Technique Approfondi
- L’Impact des Fuites d’Air Comprimé sur le Débit : Guide Pratique
- Traitement air comprimé / Optimisation de la Qualité de l’Air Comprimé : Guide Complet
- Pourquoi l’eau peut être un problème dans un réseau air comprimé ?
- Traitement écologique et la gestion des condensats d’air comprimé
- Maîtrisez l’Air Comprimé : 10 Astuces pour Optimiser son Utilisation et Réduire les Coûts dans Votre Entreprise
- Comment Réduire les Pertes d’Énergie dans Votre Système de Distribution d’Air Comprimé
- Guide pour Choisir le Sécheur d’Air Comprimé Idéal pour Votre Entreprise
- Sécurité de l’Air Comprimé : Risques, Prévention et Protection
- Guide Essentiel de l’Air Comprimé : Questions Clés Répondues
- Les causes courantes de panne des sécheurs d’air comprimé?
- Mesurer le point de rosée sous pression dans votre système d’air comprimé est crucial pour garantir la qualité de l’air et prévenir les problèmes liés à l’humidité
- Guide ultime pour réparer votre compresseur d’air : Défauts courants, remèdes efficaces et conseils de maintenance
- La sélection du bon raccord rapide air comprimé
- Optimisation Cruciale: Les Répercussions d’un Réseau Industriel Mal Équilibré sur la Performance et la Sécurité
- L’Air Comprimé : Le Pouvoir Invisible au Cœur des Technologies Avancées et des Applications Insolites
- Révolutionner l’Air Comprimé avec l’IoT et l’IA : Entre Solutions High Tech, Low Tech, et Approches Hybrides
- Les Applications et Innovations des Systèmes d’Air Comprimé dans l’Industrie : Guide Complet
- L’Azote en Industrie : Production, Purification et Avantages
- Optimisation des Systèmes d’Air Comprimé : Techniques et Technologies pour Améliorer l’Efficacité Énergétique et Réduire les Coûts Opérationnels
- Lien : Cuves d’Air Comprimé : Déclaration, Vérification et Requalification pour la Sécurité Opérationnelle
- Lien : Exemples d’applications courantes pour des compresseurs d’air comprimé à différentes pressions
- Lien : . Comprendre l’air comprimé
- Lien : Comprendre les équipements d’air comprimé
- Lien : Sélection d’équipements d’air comprimé
- Lien: Les avantages de l’utilisation d’équipements d’air comprimé
- Lien : Maintenance et entretien des équipements d’air comprimé
- Il est important de noter que la conversion entre Nm3/h et m3/h est sensible aux variations de température et de pression, et une conversion précise nécessite des valeurs exactes pour ces paramètres
- FAQ sur l’Air Comprimé : Optimisez Votre Énergie, Votre Fiabilité et Votre Productivité
- Quels sont les matériaux couramment utilisés pour les tuyauteries d’air comprimé ?
- Air Comprimé et Écologie : Vers une Industrie Plus Verte et économie d’énergies
- Les Dangers de l’Air Comprimé et Comment les Éviter
- Maîtrisez la Filtration de l’Air Comprimé : Guide Approfondi sur le Changement et l’Entretien des Éléments Filtrants
- Optimisation de la Pulvérisation : Techniques Avancées pour l’Application de Peinture Automobile
- Régulateurs de Débit et de Pression pour Air Comprimé : Guide Technique et Scientifique
- Optimisation des Systèmes d’Air Comprimé : Techniques et Technologies pour Améliorer l’Efficacité Énergétique et Réduire les Coûts Opérationnels
- Régulation de Température de l’Air Comprimé en Industrie
- Innovations dans l’air comprimé : De la production à l’utilisation
- La conception d’un système d’air comprimé est une tâche complexe
Lien pour achats :