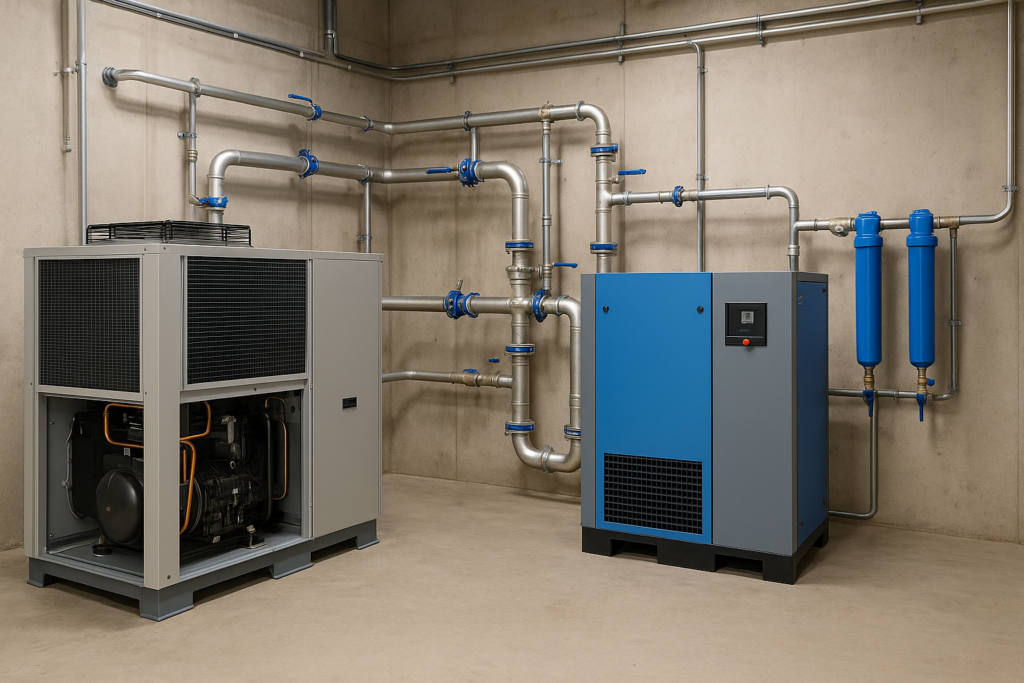
Dans l’univers industriel, le dimensionnement des utilités de process (air comprimé, eau glacée, vapeur, vide, etc.) est un enjeu stratégique. Il conditionne la performance énergétique, la disponibilité des équipements, la qualité de la production et les coûts d’exploitation. Pourtant, cette étape essentielle est souvent négligée ou mal maîtrisée.
Dimensionner un système industriel ne consiste pas à « gonfler les chiffres » pour se rassurer, ni à se contenter d’un dimensionnement théorique basé sur des tableaux de puissance. Cela demande une approche scientifique, technique et pragmatique, en lien étroit avec les usages réels du process et les conditions spécifiques du site.
Cet article présente les fondamentaux du bon dimensionnement, à travers les méthodologies de calcul, les critères opérationnels à intégrer, et les bonnes pratiques d’ingénierie.
I. Comprendre les besoins réels du process
1. Éviter le dimensionnement sur le « théorique »
- Ne pas se baser uniquement sur les fiches fabricants, les hypothèses de bureau d’étude, ou des scénarios extrêmes
- Analyser les consommations réelles mesurées sur site : débits, puissances, températures, pressions, durées
2. Identifier les usages effectifs
- Quels équipements utilisent quel fluide ? À quels moments ? Pour quelle durée ? À quelle fréquence ?
- Ex : un moule peut consommer de l’eau glacée 2 min toutes les 30 min… inutile de le dimensionner comme un usage continu
3. Travailler avec les opérateurs de terrain
- Observation des cycles machine
- Identification des pertes, des pics, des arrêts
- Intégration des pratiques réelles (soufflage d’air, nettoyage, purge…)
II. Calcul des charges : approche technique par nature de fluide
1. Charges thermiques (groupes froids, échangeurs)
- Formule de base : Q = m × Cp × ΔT 1.16
- Données à relever : débit (m³/h ou kg/h), température d’entrée et de sortie, type de fluide, coefficients de correction (viscosité, glycol, etc.)
- Ex : refroidir 10 m³/h d’eau de 18 °C à 8 °C avec 10 % de glycol → besoin réel = 116 kW
2. Charges pneumatiques (compresseurs, réseau d’air)
- Calcul en Nm³/h ou l/min
- Intégration des simultanéités : plusieurs machines tournent-elles en même temps ?
- Intégration des pertes dans les accessoires (filtres, sécheurs, purgeurs)
3. Charges hydrauliques (circulateurs, pompes)
- Calcul du débit et des hauteurs manométriques totales (HMT)
- Intégration des pertes de charge linéaires et singulières (coudes, vannes, échangeurs)
III. Intégrer les régimes de fonctionnement réels
1. Fonctionnement continu vs cyclique
- Un compresseur qui tourne 24/7 n’a pas les mêmes exigences qu’un compresseur de secours utilisé 2 h/semaine
- Importance de moduler les puissances installées selon la durée et la fréquence d’utilisation
2. Profil jour / nuit / week-end
- Certains équipements tournent en sous-régime la nuit
- D’autres s’arrêtent le week-end → adaptation de la régulation pour éviter le cycling ou la marche à vide
3. Variabilité saisonnière
- Températures ambiantes influencent fortement la performance des groupes froids et des compresseurs
- Hygrométrie impacte les sécheurs d’air
- Intégrer une marge climatique dans les calculs : +10 à +20 % en cas de canicule
4. Courbes de charge dynamiques
- Utilisation de superviseurs, IoT, capteurs pour tracer la consommation horaire/journalière
- Outils d’analyse pour identifier les pointes, les cycles, les périodes de sous-utilisation
IV. Prendre en compte les pertes de charge réseau et accessoires
1. Pertes de charge linéaires
- Dépendent du diamètre de tuyauterie, de la longueur, du débit, de la rugosité
- Ex : 100 m de tuyau DN32 avec 8 m³/h d’air → perte de 0,4 bar
2. Pertes de charge singulières
- Coudes, vannes, réducteurs, filtres, flexibles, silencieux…
- À intégrer dans les calculs pour garantir une pression/débit effectif suffisant en bout de ligne
3. Réseau mal équilibré = pertes globales
- Bouclage asymétrique, longueurs trop importantes, réseaux en étoile non équilibrés = déséquilibres et surconsommation
4. Filtres et équipements annexes
- Perte de charge initiale + perte d’encrassement → à compenser dans la pression du compresseur ou du circulateur
- Anticiper le remplacement et le colmatage
V. Anticiper les évolutions futures
1. Croissance capacitaire
- Une usine double ses lignes en 5 ans : le réseau et les utilités doivent le permettre
- Prévoir des surdimensionnements stratégiques (pré-câblage, tuyauterie prête, réserve de puissance sur transfo…)
2. Modularité et flexibilité
- Préférer 2 groupes froids de 100 kW plutôt qu’un de 200 kW : possibilité d’adaptation, de rotation, de maintenance sans arrêt
3. Redondance
- Pour les postes critiques (ex : vide, vapeur, air comprimé process), prévoir des secours actifs ou passifs
- Permet de garantir la continuité en cas de maintenance ou de panne
4. Prédisposition IoT et supervision
- Installer dès le départ des capteurs de débit, température, pression pour suivre la performance
- Intégrer les systèmes de supervision pour aider à la régulation et à la maintenance prédictive
VI. Bonnes pratiques de dimensionnement
✅ Approche collaborative entre production, maintenance, ingénierie
- Chacun apporte un regard complémentaire : usage, contraintes, longévité, coût
✅ Utiliser des logiciels de simulation
- Thermique, hydraulique, pneumatique, énergétique (Coolselector, FluidSIM, Pipe Flow, etc.)
✅ Comparer plusieurs scénarios
- Pic extrême, fonctionnement moyen, basse charge
- Simuler les effets de variation climatique ou de croissance future
✅ Privilégier les systèmes modulables et évolutifs
- Ex : groupes froids en cascade, compresseurs VSD + ballon tampon, circulateurs à vitesse variable
✅ Documenter les hypothèses
- Ce qui est mesuré, simulé, extrapolé
- Cela facilite les ajustements ultérieurs
Le bon dimensionnement des utilités de process repose sur une démarche rigoureuse, technique et évolutive. Il ne s’agit pas de viser au plus juste ou au plus large, mais de dimensionner selon les usages réels, les conditions de site et les perspectives d’évolution.
Un système bien calibré, c’est un réseau fiable, économe, facile à maintenir, capable d’absorber les variations et de s’adapter dans le temps.
🎯 À retenir : un bon dimensionnement, c’est l’art d’allier précision d’ingénierie, souplesse opérationnelle et vision stratégique.
En somme, l’ingénierie des fluides industriels est une discipline importante et diversifiée qui joue un rôle clé dans de nombreuses industries. Elle nécessite une expertise technique et une connaissance approfondie des systèmes de circulation des fluides, de la thermodynamique, de la mécanique des fluides, de la régulation et du contrôle des processus, ainsi que de la sécurité.
Notre blog est une ressource complète pour tout ce qui concerne les fluides industriels. Nous vous encourageons à explorer nos articles, nos guides pratiques et nos ressources de formation pour approfondir vos connaissances et améliorer vos performances énergétiques. N’hésitez pas à nous contacter pour bénéficier de nos services d’ingénierie personnalisés ou pour trouver les produits dont vous avez besoin via notre site de commerce en ligne. Ensemble, nous pouvons aller plus loin dans l’apprentissage et réaliser des économies d’énergie significatives. Contactez-nous dès aujourd’hui à l’adresse suivante :
Lien : Tuyauteries et Flexibles
Lien : Electricité et électricité industrielle
Lien: Robinetterie et tuyauterie
Lien : Échangeurs et transferts thermiques
Lien : Eau surchauffe (industrie et génie climatique)
Lien : Hydraulique et Graissage
Lien :Mesures Physique et appareils de mesures
Lien : Les sondes de mesure de température
Lien : outils de mesures (thermomètre, manomètres,…)
Lien : Matériaux en industrie (galva, acier, inox …)
Lien : Eau – filtration et traitement
Lien : Gazs réfrigérants (frigorifiques)
Lien : Filetages et taraudages
Lien : Unités de mesure et conversion
Lien: R.I.A. (Réseau Incendie Armé)
Lien : ATEX (Atmosphères Explosibles)
Lien : Agitation dans les Fluides Industriels
Lien : Le Chauffage Industriel : Un Processus Complexifié
Lien : L’Eau Glacée en Génie Climatique
Lien : Réaliser un Bilan Thermique en Génie Climatique
Lien : L’Isolation en Génie Climatique
Lien : Les Méthodes de Soudure et de Brasage : Comment Faire le Bon Choix »
Lien : Fixations Industrielles : La Clé de la Solidité et de la Sécurité
Lien : Les E.P.I. (Equipements de Protections Individuels)
0ien : Les E.P.C. (Equipements de Protection Collectifs)
Lien : Principaux de transfert thermique : la conduction, la convection et le rayonnement
Lien : Le Cercle Vertueux en Industrie : L’Écologie au Cœur des Fluides Industriels
Lien : Courroies Trapézoïdales en Industrie : L’Art de Transmettre la Puissance avec Précision
Lien : Optimisation de la Stabilité Industrielle : Lutte Efficace Contre les Vibrations des Machines
- La Gestion des Pièces Détachées en Industrie : Obsolescence, Durée de Vie et Stockage
- L’Impact de la Nature de la Surface et de la Couleur : Bilan Thermique et Transfert de Chaleur
- Comprendre les Classes de Protection IP : Un Guide Technique
- L’Art de l’Ingénierie en Mesures Physiques Industrielles : Optimisation, Contrôle et Dimentionnement des Fluides Industriels
- Innovation et Durabilité : L’Ingénierie des Fluides Industriels au Service de l’Économie Verte
- L’Énigme des Fluides Industriels : Explorons l’Inclassable
- Optimisation Énergétique dans l’Industrie : Réduire les Coûts liés aux Fluides Industriels
- Solutions Sur Mesure en Électrovannes pour Projets Spécifiques : Une Expertise Unique
- Vannes Motorisées: Standard ou Sur Mesure, Trouvez la Solution Adaptée pour Votre Application
- Guide Complet des Vannes Pneumatiques : Personnalisation, Qualité et Expertise
- Découvrez la Révolution Pneumatique : Les Vérins Sur Mesure
- Optimisation Pneumatique : Explorez Notre Gamme de Moteurs Pneumatiques
- Comment choisir le bon matériau pour vos équipements industriels : Une approche personnalisée
- Optimisation Cruciale: Les Répercussions d’un Réseau Industriel Mal Équilibré sur la Performance et la Sécurité
- Démystification des Moteurs Électriques: Un Guide Complet des Types, Avantages et Inconvénients
- Comprendre les éléments constitutifs des machines spéciales : Un guide technique pour les ingénieurs et techniciens de maintenance
- Impact Environnemental des Fluides Industriels et des Méthodes de Production
- L’évolution des systèmes de maintenance et la gestion des équipements industriels
- L’Évolution des Technologies dans les Systèmes Industriels : Air Comprimé, Groupes Froids et au-delà
- L’Importance de la Formation Continue pour les Techniciens des Fluides Industriels
- Tolérances de Côtes et Rugosité en Mécanique : Précision et Qualité en Ingénierie
- Méthodes Statistiques et Échantillonnage : L’Art d’Anticiper les Dérives Industrielles (SPC, …)
- Maîtriser l’Art du Filtrage Industriel : Comment Choisir, Lire et Entretenir les Filtres pour Optimiser Performance, Énergie et Durabilité
Lien pour achats :