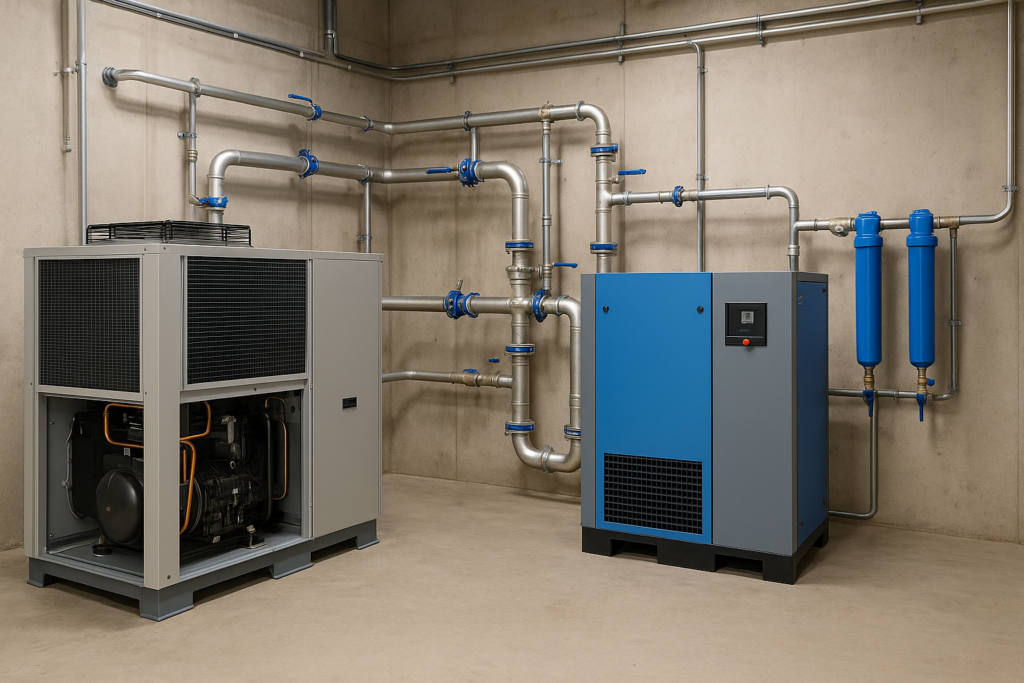
Dans l’univers industriel moderne, la quête d’efficacité énergétique, de fiabilité des process et de maîtrise des coûts passe inévitablement par une exigence : le juste dimensionnement des utilités. Loin d’être un simple choix technique, dimensionner précisément un équipement (compresseur, groupe froid, sécheur, pompe, etc.) au plus proche du besoin – autour de 100 % – constitue une démarche scientifique et stratégique.
Dans cet article, nous explorons les fondements techniques, scientifiques et opérationnels du juste dimensionnement, en mettant en lumière ses conséquences concrètes sur la stabilité des process, la durée de vie des composants et l’optimisation énergétique. Suivez le guide.
I. Le juste dimensionnement : qu’est-ce que cela signifie ?
1. Une capacité adaptée aux besoins réels
Dimensionner un équipement à 100 %, c’est viser la capacité nominale correspondant aux charges normales de fonctionnement, en prenant en compte :
- Les débits moyens constatés sur site
- Les pics raisonnables de consommation
- Le facteur de simultanéité des usages
- Le profil temporel (variation journalière, hebdomadaire, saisonnière)
2. Intégrer une marge de sécurité contrôlée
Le juste dimensionnement n’exclut pas les imprévus. Une marge de 10-15 % est souvent admise pour faire face aux fluctuations de charge et éviter la sous-capacité ponctuelle.
3. À l’inverse des extrêmes
- Sous-dimensionnement (<90 %) : surcharge, usure, instabilité
- Surdimensionnement (>120-150 %) : surconsommation, cycles inefficients, surcoûts
Le bon compromis technique se situe à équilibre.
II. Stabilisé du process et continuité de production
1. Compresseurs : rendement volumétrique optimal
Un compresseur d’air fonctionnant à 95-100 % de son rendement volumétrique :
- Maintient une pression constante dans le réseau
- Répond rapidement aux sollicitations
- Limite les pertes de charge
Un fonctionnement dans cette plage garantit un réseau pneumatique performant, sans chute de pression en cas de pics.
2. Groupes froids : Delta T maîtrisé
Le Delta T (écart entre température d’entrée et de sortie) reste stable si la charge thermique est bien couverte :
- Meilleure régulation des températures
- Réduction des cycles marche/arrêt
- Pas de surconsommation due à une compensation thermique excessive
3. Filtres et réseaux : perte de charge minimale
Des filtres correctement dimensionnés assurent :
- Une filtration efficace sans contrainte excessive sur le débit
- Une réduction des pertes de charge, donc de la consommation énergétique en amont
III. Durée de vie optimisée des équipements
1. Moins d’usure mécanique
Les composants mécaniques (paliers, moteurs, courroies, engrenages) sont conçus pour fonctionner dans une zone de charge optimale. Le juste dimensionnement permet :
- Une répartition homogène des efforts
- Une diminution des frottements inutiles
- Moins de contraintes thermiques
2. Réduction des cycles marche/arrêt
Les cycles marche/arrêt brutaux sont la première cause d’usure :
- Ils créent des pics d’intensité électrique
- Ils provoquent des chocs mécaniques
- Ils augmentent les risques de casse prématurée
Un équipement bien dimensionné fonctionne plus longtemps en continu, dans une zone stable.
3. Maintenance espacée et planifiée
Le juste dimensionnement allonge les intervalles de maintenance préventive :
- Diminution du nombre d’interventions correctives
- Réduction du temps d’arrêt non planifié
- Maîtrise des coûts de maintenance (pièces, main d’œuvre, pertes de production)
IV. Optimisation énergétique
1. Fonctionnement dans la zone de performance optimale
Chaque utilité industrielle possède une plage de rendement maximal. À 100 % de charge nominale :
- Le moteur électrique atteint son point de fonctionnement efficace (cos ϕ optimal)
- Les compresseurs et groupes froids exploitent au mieux leur rapport kWh/produit utile
2. Réduction des pertes thermiques
Un équipement bien dimensionné :
- Évite la surchauffe
- Fonctionne sans excès d’inertie thermique
- Améliore l’isolation globale du système (moins de rejets inutiles)
3. Diminution des appels de puissance
Les appels de puissance au démarrage (Inrush) sont réduits grâce à :
- Des durées de cycle allongées
- Une charge répartie uniformément sur le réseau
- Une programmation optimisée (soft starter, variation de vitesse)
4. Moins de pics d’intensité
Les équipements tournant à pleine charge de manière sporadique provoquent des fluctuations dangereuses pour le réseau électrique. Un bon dimensionnement :
- Stabilise les intensités consommées
- Réduit les pertes par effet Joule
- Protège les composants électriques en amont
V. Conséquences positives en cascade
1. Stabilisé du réseau industriel
- Moins de fluctuations de pression/température
- Moins de sollicitations imprévues
- Meilleure synchronisation des machines
2. Productivité accrue
- Moins de micro-arrêts
- Process plus fluides
- Moins de rebuts ou de non-conformités
3. Qualité de produit maintenue
- Régulation thermique stable pour les process sensibles (agro, pharma, chimie)
- Pas d’écarts critiques à compenser
4. RSE et image environnementale renforcée
- Réduction des émissions indirectes (scope 2)
- Moins de déchets de production
- Amélioration du score écologique global (ISO 50001)
VI. Comment atteindre ce juste dimensionnement ?
1. Audit technique sur site
- Relevés de consommation (débitmètres, capteurs, supervision)
- Analyse des courbes de charge
- Identification des pics et cycles d’utilisation
2. Simulation numérique (CFD / modèles thermiques / jumeaux numériques)
- Prévision du comportement dynamique
- Anticipation des interactions entre équipements
- Optimisation globale des flux
3. Choix d’équipements adaptés
- Variation de vitesse pour l’ajustement fin
- Modules en parallèle pour la flexibilité
- Systèmes intelligents (régulation automatique, supervision connectée)
4. Intégrer la maintenance et le pilotage
- Suivi en temps réel de la performance
- Maintenance prédictive basée sur l’analyse des données
- Mise à jour des paramètres en fonction de l’évolution des besoins
Le juste dimensionnement est une science de l’équilibre : ni trop, ni trop peu. Il constitue la pierre angulaire d’une exploitation industrielle efficace, durable et compétitive. En ciblant précisément les besoins, en adaptant la capacité des utilités à la réalité du terrain, les industries peuvent améliorer leur productivité, réduire leurs coûts et accroître la durée de vie de leurs installations.
En somme, le dimensionnement n’est pas un acte isolé en phase de conception, mais un levier continu d’optimisation, à revisiter régulièrement à l’aune des évolutions techniques, des innovations et des contraintes de production. Adoptons cette logique d’ajustement fin : c’est la clef d’une industrie plus intelligente, plus résiliente et plus sobre.
En somme, l’ingénierie des fluides industriels est une discipline importante et diversifiée qui joue un rôle clé dans de nombreuses industries. Elle nécessite une expertise technique et une connaissance approfondie des systèmes de circulation des fluides, de la thermodynamique, de la mécanique des fluides, de la régulation et du contrôle des processus, ainsi que de la sécurité.
Notre blog est une ressource complète pour tout ce qui concerne les fluides industriels. Nous vous encourageons à explorer nos articles, nos guides pratiques et nos ressources de formation pour approfondir vos connaissances et améliorer vos performances énergétiques. N’hésitez pas à nous contacter pour bénéficier de nos services d’ingénierie personnalisés ou pour trouver les produits dont vous avez besoin via notre site de commerce en ligne. Ensemble, nous pouvons aller plus loin dans l’apprentissage et réaliser des économies d’énergie significatives. Contactez-nous dès aujourd’hui à l’adresse suivante :
Lien : Tuyauteries et Flexibles
Lien : Electricité et électricité industrielle
Lien: Robinetterie et tuyauterie
Lien : Échangeurs et transferts thermiques
Lien : Eau surchauffe (industrie et génie climatique)
Lien : Hydraulique et Graissage
Lien :Mesures Physique et appareils de mesures
Lien : Les sondes de mesure de température
Lien : outils de mesures (thermomètre, manomètres,…)
Lien : Matériaux en industrie (galva, acier, inox …)
Lien : Eau – filtration et traitement
Lien : Gazs réfrigérants (frigorifiques)
Lien : Filetages et taraudages
Lien : Unités de mesure et conversion
Lien: R.I.A. (Réseau Incendie Armé)
Lien : ATEX (Atmosphères Explosibles)
Lien : Agitation dans les Fluides Industriels
Lien : Le Chauffage Industriel : Un Processus Complexifié
Lien : L’Eau Glacée en Génie Climatique
Lien : Réaliser un Bilan Thermique en Génie Climatique
Lien : L’Isolation en Génie Climatique
Lien : Les Méthodes de Soudure et de Brasage : Comment Faire le Bon Choix »
Lien : Fixations Industrielles : La Clé de la Solidité et de la Sécurité
Lien : Les E.P.I. (Equipements de Protections Individuels)
0ien : Les E.P.C. (Equipements de Protection Collectifs)
Lien : Principaux de transfert thermique : la conduction, la convection et le rayonnement
Lien : Le Cercle Vertueux en Industrie : L’Écologie au Cœur des Fluides Industriels
Lien : Courroies Trapézoïdales en Industrie : L’Art de Transmettre la Puissance avec Précision
Lien : Optimisation de la Stabilité Industrielle : Lutte Efficace Contre les Vibrations des Machines
- La Gestion des Pièces Détachées en Industrie : Obsolescence, Durée de Vie et Stockage
- L’Impact de la Nature de la Surface et de la Couleur : Bilan Thermique et Transfert de Chaleur
- Comprendre les Classes de Protection IP : Un Guide Technique
- L’Art de l’Ingénierie en Mesures Physiques Industrielles : Optimisation, Contrôle et Dimentionnement des Fluides Industriels
- Innovation et Durabilité : L’Ingénierie des Fluides Industriels au Service de l’Économie Verte
- L’Énigme des Fluides Industriels : Explorons l’Inclassable
- Optimisation Énergétique dans l’Industrie : Réduire les Coûts liés aux Fluides Industriels
- Solutions Sur Mesure en Électrovannes pour Projets Spécifiques : Une Expertise Unique
- Vannes Motorisées: Standard ou Sur Mesure, Trouvez la Solution Adaptée pour Votre Application
- Guide Complet des Vannes Pneumatiques : Personnalisation, Qualité et Expertise
- Découvrez la Révolution Pneumatique : Les Vérins Sur Mesure
- Optimisation Pneumatique : Explorez Notre Gamme de Moteurs Pneumatiques
- Comment choisir le bon matériau pour vos équipements industriels : Une approche personnalisée
- Optimisation Cruciale: Les Répercussions d’un Réseau Industriel Mal Équilibré sur la Performance et la Sécurité
- Démystification des Moteurs Électriques: Un Guide Complet des Types, Avantages et Inconvénients
- Comprendre les éléments constitutifs des machines spéciales : Un guide technique pour les ingénieurs et techniciens de maintenance
- Impact Environnemental des Fluides Industriels et des Méthodes de Production
- L’évolution des systèmes de maintenance et la gestion des équipements industriels
- L’Évolution des Technologies dans les Systèmes Industriels : Air Comprimé, Groupes Froids et au-delà
- L’Importance de la Formation Continue pour les Techniciens des Fluides Industriels
- Tolérances de Côtes et Rugosité en Mécanique : Précision et Qualité en Ingénierie
- Méthodes Statistiques et Échantillonnage : L’Art d’Anticiper les Dérives Industrielles (SPC, …)
- Maîtriser l’Art du Filtrage Industriel : Comment Choisir, Lire et Entretenir les Filtres pour Optimiser Performance, Énergie et Durabilité
Lien pour achats :