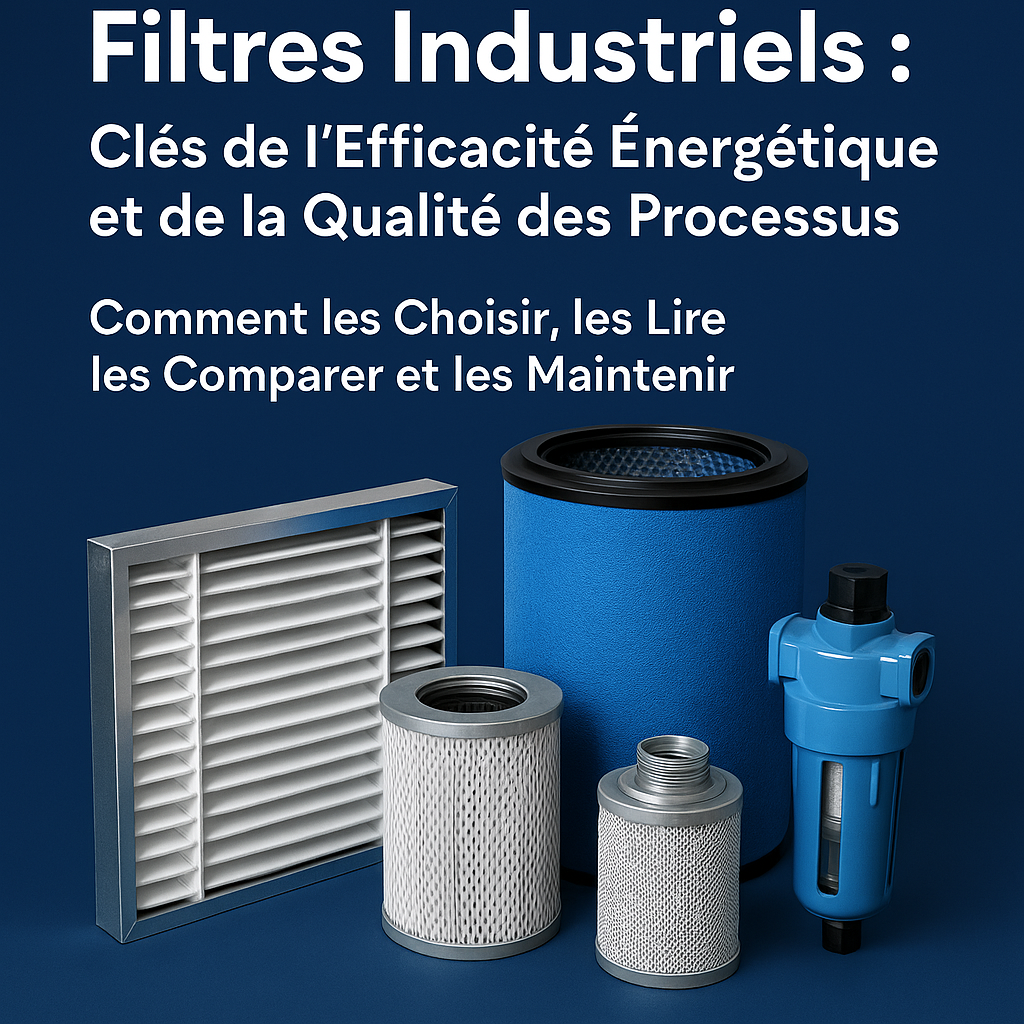
Dans le monde industriel moderne, un filtre n’est jamais qu’un simple consommable. Il est l’un des maillons critiques d’un système de production efficace, fiable et énergétiquement optimisé. Et pourtant, il est trop souvent relégué au second plan, remplacé au dernier moment ou oublié jusqu’à la panne. Erreur fatale. Car un filtre encrassé, fissuré ou colmaté peut causer bien plus qu’une simple chute de débit : il peut compromettre l’intégrité d’un process entier, fausser les indicateurs de performance, augmenter drastiquement la consommation énergétique, ou même provoquer un arrêt brutal de production.
C’est ici qu’entre en jeu la maintenance intelligente des filtres industriels. C’est une science, une stratégie, et surtout une guerre permanente contre l’usure silencieuse.
🎯 L’enjeu caché derrière un filtre : bien plus qu’un simple changement de cartouche
Un filtre industriel — qu’il soit utilisé en traitement de l’air comprimé, en HVAC, en filtration de liquides techniques ou de fluides gazeux — n’est jamais éternel. Il a une durée de vie fonction de la nature du fluide, de la concentration en polluants, du débit, de la température, et surtout de l’environnement industriel dans lequel il opère.
Or, contrairement à ce que l’on pourrait penser, un filtre colmaté ne ralentit pas seulement le système : il peut provoquer l’effet inverse, c’est-à-dire une chute brutale de la perte de charge. Ce phénomène est trompeur, car il peut faire croire à une « amélioration » du système (moins de résistance à l’écoulement), alors qu’en réalité le média filtrant a craqué ou s’est déchiré, ne filtrant plus rien.
👉 Résultat ? Pollution du réseau, détérioration accélérée des équipements en aval, contamination du process, retour client, défaut de qualité produit, ou même incident de sécurité.
📈 Le coût réel d’un mauvais entretien
Un filtre négligé ne coûte pas seulement le prix d’un remplacement tardif. Il alourdit la facture énergétique, car la pompe, le compresseur ou le ventilateur associé devra fournir un effort supplémentaire pour maintenir le débit demandé.
🧮 Exemple concret : Un compresseur d’air qui fonctionne avec un filtre colmaté peut consommer jusqu’à 10 à 15 % d’énergie en plus. Sur une année, cela représente plusieurs centaines voire milliers d’euros perdus.
De plus, un filtre trop chargé :
- Réduit la durée de vie des équipements sensibles en aval (vérins, capteurs, buses, etc.).
- Augmente la fréquence des interventions SAV non planifiées.
- Entraîne des micro-arrêts de production qui, cumulés, coûtent une fortune en productivité.
⏱ Maintenance préventive vs. curative : une philosophie de performance
Le remplacement des filtres ne doit jamais se faire « à la sensation » ou au simple visuel. L’approche moderne repose sur un plan de maintenance prédictif ou préventif, basé sur plusieurs indicateurs techniques mesurables :
🔹 1. La durée d’utilisation (heures de service)
La majorité des fabricants donnent une plage horaire indicative de remplacement :
- 3 000 h pour des filtres air comprimé classiques.
- 5 000 h pour des filtres à liquide ou à charbon actif.
- 10 000 à 15 000 h pour des filtres haute performance (HEPA, ULPA, etc.), sous réserve d’environnement contrôlé.
Mais cette indication ne suffit pas seule. Elle doit être croisée avec des indicateurs de performance dynamique.
🔹 2. Le différentiel de pression amont-aval (∆P)
C’est l’indicateur clé. Dès qu’un écart de pression commence à dépasser les valeurs de consigne du fabricant, cela indique que le filtre est colmaté et freine le passage du fluide.
💡 Astuces ingénieur :
- Intégrer un pressostat ou manomètre différentiel sur les réseaux critiques.
- Coupler ces données à une supervision automatisée (IoT ou BMS) pour un déclenchement d’alerte.
- Tenir un historique de la variation de ∆P pour anticiper le moment optimal de remplacement.
🔹 3. Inspection visuelle : un filet de sécurité
Malgré tous les capteurs, un filtre peut se déchirer mécaniquement (pression trop forte, vibration, choc thermique) sans nécessairement modifier la pression différentielle.
Il est donc primordial d’avoir un contrôle visuel régulier, en particulier dans les environnements où la qualité du fluide a un impact critique (agroalimentaire, pharmaceutique, électronique).
⚠ Rappel crucial : un filtre fissuré = perte de filtration réelle, même si les capteurs indiquent une valeur normale. Ne jamais se fier uniquement aux instruments !
🧰 Maintenance intelligente : mise en place d’un protocole efficace
Voici les bonnes pratiques mises en place dans les industries de pointe :
- Suivi de consommation : historiser l’évolution de la perte de charge.
- Tableaux de bord de maintenance : avec seuils d’alerte et actions correctives planifiées.
- Stock de sécurité : prévoir un stock de filtres de remplacement pour ne pas attendre un réapprovisionnement en urgence.
- Identification par QR Code : chaque filtre porte une étiquette avec son type, sa date de mise en service, son seuil d’alerte.
- Maintenance prévisionnelle assistée par IA/IoT : systèmes connectés qui prévoient le remplacement avant la rupture de performance.
🛠 Bon à savoir : cas particuliers à surveiller
Type de filtre | Risque spécifique | Fréquence de vérification recommandée |
---|---|---|
Filtres à charbon actif | Saturation invisible à l’œil nu | Tous les 3 mois ou suivi chimique |
Filtres HEPA/ULPA | Chute d’efficacité silencieuse | Test DOP ou fuites tous les 6 mois |
Filtres à coalescence | Saturation en huile, risque de relargage | Vérif. différentielle + vidange |
Filtres à liquide | Détérioration par pression ou corrosion | Vérif. hebdo ou pression de rupture |
🌱 Un filtre bien entretenu, c’est aussi une démarche environnementale
Changer un filtre au bon moment, c’est :
- Réduire la consommation énergétique → moins d’émissions de CO₂.
- Éviter le gaspillage de fluide (eau, huile, air).
- Préserver la durée de vie des machines → moins de pièces de rechange produites.
- Moins de déchets (évite les interventions d’urgence avec surconsommation de pièces ou de transport express).
Certaines industries vont même jusqu’à régénérer les filtres en interne ou à les recycler via des filières spécialisées, intégrant la maintenance dans une logique d’économie circulaire.
🔎 Zoom technique : le piège du faux retour à la normale
Quand un filtre est trop colmaté, le média peut se fissurer sous la pression. Résultat : la perte de charge chute brutalement, ce qui fait croire à une amélioration… alors que le fluide circule librement sans aucune barrière.
❗ Conséquences :
- Le système croit que tout va bien.
- Le capteur de pression affiche une baisse.
- L’opérateur pense que le filtre « s’est nettoyé ».
- En réalité, le réseau entier est en train d’être contaminé.
Ce piège classique, bien connu en génie des procédés, justifie l’intérêt d’un double contrôle (capteur + inspection visuelle), voire d’un système redondant dans les installations sensibles.
📊 Chiffres clés à retenir
Indicateur | Valeur indicative |
---|---|
Surcharge énergétique par filtre colmaté | +10 à +20 % d’énergie par pompe/ventilateur |
Dépassement ∆P critique | > 250 Pa pour filtre air comprimé |
Durée de vie moyenne filtre HVAC | 6 à 12 mois (selon classe ISO) |
Risque de déchirement | dès ∆P > 300 Pa sur filtre usé |
TCO amélioré | jusqu’à -25 % si remplacement optimisé |
🎯 Un petit geste pour un grand gain industriel
Changer un filtre ne semble pas être un acte stratégique à première vue. Et pourtant, il touche à la qualité, à la sécurité, à la performance énergétique et à la longévité des machines. C’est un point névralgique de toute maintenance industrielle bien pensée.
Adopter une politique proactive de maintenance et de remplacement des filtres, c’est non seulement garantir une production fiable et maîtrisée, mais aussi se donner les moyens d’optimiser l’énergie, de réduire l’empreinte carbone, et d’anticiper les défaillances invisibles.
👉 Mieux vaut changer un filtre une semaine trop tôt qu’une minute trop tard.
📌 1. Signes indiquant qu’un filtre doit être remplacé
✅ Critère de remplacement | 🔍 Détails / Signes à surveiller |
---|---|
Durée d’utilisation atteinte | Selon recommandations constructeur (ex : 2 000 à 5 000 h) |
Différentiel de pression élevé | Mesuré par manomètre ou pressostat (> 250 Pa souvent critique) |
Évolution rapide de ∆P | Colmatage accéléré → environnement trop chargé |
Chute brutale de perte de charge | Risque de fissure → plus de filtration réelle |
Inspection visuelle | Fissures, déformation, encrassement massif visible |
Résultats qualité anormaux | Contamination du produit final, retour client, défaut qualité |
⚙️ 2. Risques liés à un filtre trop encrassé ou oublié
⚠️ Problème | 🔄 Conséquences potentielles |
---|---|
Colmatage total | Surcharge des équipements (pompe, compresseur) |
Rupture du média filtrant | Plus aucune filtration → pollution du réseau |
Surconsommation énergétique | +10 à +20 % d’énergie utilisée pour compenser |
Fausse lecture des capteurs | Baisse ∆P → illusion de bon fonctionnement |
Dégradation aval (machines) | Usure prématurée, contamination de composants sensibles |
Augmentation TCO | Coûts de réparation + pertes de production + SAV non planifié |
📈 3. Bonnes pratiques de maintenance des filtres industriels
🛠️ Action recommandée | 🧩 Objectif / Bénéfice |
---|---|
Suivre les heures d’utilisation | Anticiper l’usure normale et planifier les remplacements |
Installer un manomètre ou pressostat | Surveiller le ∆P en temps réel |
Réaliser un historique de pression | Identifier les tendances et pics anormaux |
Planifier des inspections visuelles | Détection manuelle des fissures ou anomalies |
Maintenir un stock tampon | Éviter les urgences et ruptures de production |
Créer une fiche de suivi par filtre | Traçabilité, QR code, date de remplacement, etc. |
Utiliser des solutions IoT/IA | Maintenance prédictive basée sur données en temps réel |
🔍 4. Spécificités selon type de filtre
🧪 Type de filtre | ⚠️ Particularité / Surveillance | ⏱️ Fréquence conseillée |
---|---|---|
Filtres à charbon actif | Saturation invisible / relargage possible | Tous les 3 mois ou par test chimique |
Filtres HEPA / ULPA | Nécessite test DOP, contrôle fuites | Tous les 6 mois ou après maintenance |
Filtres coalescents | Risque de relargage d’huile si saturation | Par ∆P + inspection visuelle |
Filtres à liquide | Risque corrosion ou surpression → fissures | Vérification hebdomadaire recommandée |
💡 5. Chiffres clés à retenir pour décision rapide
📊 Indicateur | 🧮 Valeur typique / seuil d’alerte |
---|---|
Perte énergétique filtre colmaté | +10 à +20 % selon système |
Seuil ∆P critique pour changement | > 250 à 300 Pa pour filtres air comprimé classiques |
Durée de vie filtre HVAC | 6 à 12 mois (selon classe ISO et environnement) |
Gain TCO avec maintenance optimisée | Jusqu’à -25 % sur le cycle de vie d’un équipement |
Risque de fissuration filtre | Dès ∆P > 300 Pa ou après 5 000 h selon pression fluide |
En somme, l’ingénierie des fluides industriels est une discipline importante et diversifiée qui joue un rôle clé dans de nombreuses industries. Elle nécessite une expertise technique et une connaissance approfondie des systèmes de circulation des fluides, de la thermodynamique, de la mécanique des fluides, de la régulation et du contrôle des processus, ainsi que de la sécurité.
Notre blog est une ressource complète pour tout ce qui concerne les fluides industriels. Nous vous encourageons à explorer nos articles, nos guides pratiques et nos ressources de formation pour approfondir vos connaissances et améliorer vos performances énergétiques. N’hésitez pas à nous contacter pour bénéficier de nos services d’ingénierie personnalisés ou pour trouver les produits dont vous avez besoin via notre site de commerce en ligne. Ensemble, nous pouvons aller plus loin dans l’apprentissage et réaliser des économies d’énergie significatives. Contactez-nous dès aujourd’hui à l’adresse suivante :
Lien : Tuyauteries et Flexibles
Lien : Electricité et électricité industrielle
Lien: Robinetterie et tuyauterie
Lien : Échangeurs et transferts thermiques
Lien : Eau surchauffe (industrie et génie climatique)
Lien : Hydraulique et Graissage
Lien :Mesures Physique et appareils de mesures
Lien : Les sondes de mesure de température
Lien : outils de mesures (thermomètre, manomètres,…)
Lien : Matériaux en industrie (galva, acier, inox …)
Lien : Eau – filtration et traitement
Lien : Gazs réfrigérants (frigorifiques)
Lien : Filetages et taraudages
Lien : Unités de mesure et conversion
Lien: R.I.A. (Réseau Incendie Armé)
Lien : ATEX (Atmosphères Explosibles)
Lien : Agitation dans les Fluides Industriels
Lien : Le Chauffage Industriel : Un Processus Complexifié
Lien : L’Eau Glacée en Génie Climatique
Lien : Réaliser un Bilan Thermique en Génie Climatique
Lien : L’Isolation en Génie Climatique
Lien : Les Méthodes de Soudure et de Brasage : Comment Faire le Bon Choix »
Lien : Fixations Industrielles : La Clé de la Solidité et de la Sécurité
Lien : Les E.P.I. (Equipements de Protections Individuels)
0ien : Les E.P.C. (Equipements de Protection Collectifs)
Lien : Principaux de transfert thermique : la conduction, la convection et le rayonnement
Lien pour achats :