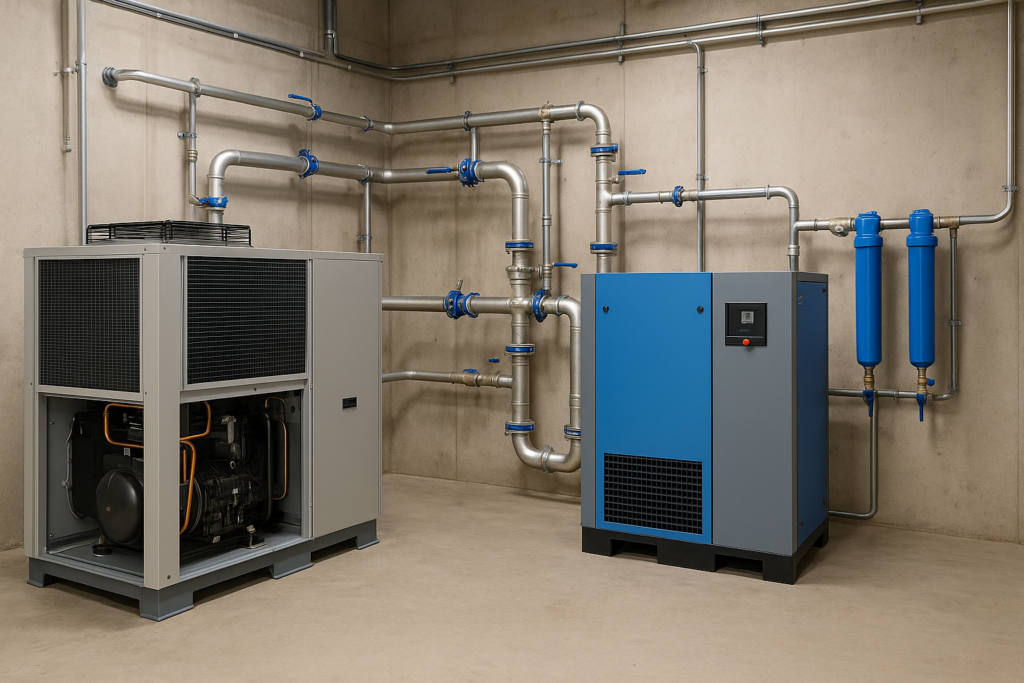
Le bon dimensionnement d’un sécheur d’air comprimé est essentiel pour garantir un air sec, fiable, et conforme aux exigences du process. Un mauvais choix peut entraîner des coûts inutiles, une usure prématurée, ou une inefficacité dans les applications critiques (pneumatique, instrumentation, procédés sensibles).
Dans cet article, nous vous proposons une analyse technique, scientifique et opérationnelle des paramètres déterminants à intégrer dans vos calculs de dimensionnement, quelle que soit la technologie choisie (réfrigération, adsorption, membrane ou dessiccant passif).
1. Le Débit Maximal d’Air Comprimé (m³/h ou l/min)
1.1 Pourquoi c’est la base du dimensionnement
- Le débit représente le volume d’air que le sécheur devra traiter.
- Il s’exprime en conditions standards (généralement à 1 bar abs et 20 °C).
1.2 Attention aux erreurs fréquentes
- Confusion entre débit à pression de service vs débit normalisé
- Débit moyen ≠ débit maximal → le sécheur doit supporter les pointes de consommation
✅ Astuce : toujours prendre le débit de pointe ou ajouter une marge de 10 à 20 %.
2. La Pression de Service (bar)
2.1 Influence directe sur la capacité de déshumidification
- Plus la pression est élevée, plus l’air est dense, donc plus il contient d’eau par m³.
- Les courbes de performance des sécheurs varient selon la pression.
Pression | Facteur de correction |
---|---|
4 bar | 0,7 |
7 bar | 1 (valeur de référence) |
10 bar | 1,3 |
13 bar | 1,5 |
2.2 Adapter les filtres et purgeurs à la pression réelle
- Surdimensionnement possible si non corrigé
✅ Astuce : utiliser les facteurs constructeurs pour corriger le débit nominal.
3. La Température d’Entrée de l’Air
3.1 Impact critique sur la performance
- Plus l’air est chaud, plus il contient de vapeur d’eau
- Le sécheur est plus sollicité → risque de saturation
Température d’entrée | Facteur de correction |
20 °C | 1 |
30 °C | 1,2 |
40 °C | 1,5 |
50 °C | 1,8 à 2 |
3.2 Pourquoi c’est souvent sous-estimé
- L’air peut chauffer dans les réseaux avant d’atteindre le sécheur
💡 Conseil d’ingénieur : prendre une température d’entrée > température ambiante + 10 °C pour anticiper les pics d’été.
4. La Température Ambiante
4.1 Conséquence sur l’échange thermique
- Pour les sécheurs à réfrigération, la température ambiante affecte la capacité de condensation.
- Au-delà de 35 °C, les rendements chutent fortement.
4.2 Ventilation et environnement technique
- Local mal ventilé = échauffement = baisse de performance
- Nécessité de prévoir aération forcée ou implantation adaptée
✅ Privilégier un local à température constante ou climatisé si besoin.
5. Le Point de Rosée Souhaité
5.1 Dépend du process industriel
Application | Point de rosée requis | Type de sécheur |
Pneumatique standard | +3 °C | Réfrigération |
Alimentation instrumentation | -20 °C | Adsorption sans chaleur |
Industrie pharmaceutique | -40 °C | Adsorption avec chauffage |
Environnement cryogénique | -70 °C | Adsorption spéciale |
5.2 Plus le point de rosée est bas → plus le sécheur est complexe et énergivore
✅ Ne pas surdimensionner inutilement : un point de rosée trop sec peut être contre-productif.
6. La Technologie Utilisée
6.1 Chaque technologie a ses contraintes
Technologie | Avantages | Limites |
Réfrigération | Simple, économique | +3 °C max, sensible à la température ambiante |
Adsorption | Point de rosée très bas | Complexe, énergivore |
Membrane | Compact, sans électricité | Faible débit, coût élevé |
Mini dessiccant | Autonome, économique | Usage ponctuel uniquement |
6.2 Bien choisir selon les priorités
- Budget
- Criticité du process
- Conditions d’environnement
✅ Intégrer les coûts d’exploitation dans le raisonnement (pas que le prix d’achat).
7. La Variabilité de la Demande
7.1 Débit constant ou variable ?
- En fonctionnement cyclique, la taille du sécheur peut être optimisée
- En cas de fortes variations : prévoir un tampon ou une régulation adaptative
7.2 Équipements complémentaires
- Ballon tampon d’air sec pour lisser la demande
- Séquenceur de compresseurs couplé à un sécheur modulaire
✅ Pour les industries avec pic de consommation soudain (soufflage, purge, process batch), penser inertie.
8. Le Taux de Charge sur 24h
8.1 Temps de fonctionnement réel du sécheur
- Utilisation 24/24 → sécheur permanent avec purge automatique
- Utilisation 4h/jour → option dessiccant ponctuel ou mini sécheur
8.2 Éviter le surdimensionnement inutile
- Une charge faible avec un gros sécheur = marches/arrêts fréquents, usure accélérée
✅ Adapter la taille au profil réel de consommation (enregistrement sur 7 jours recommandé).
9. Cas Pratique : Simulation de Dimensionnement
Données de base
- Débit d’air nominal : 420 m³/h
- Pression de service : 8 bar
- Température d’entrée : 40 °C
- Température ambiante : 32 °C
- Point de rosée souhaité : +3 °C
Application des coefficients correcteurs (exemple réfrigération)
- Température d’entrée : x 1,5
- Pression : x 1,15
- Température ambiante : x 1,2
→ Capacité corrigée nécessaire : 420 x 1,5 x 1,15 x 1,2 = 867 m³/h
💡 Il faudra donc sélectionner un sécheur prévu pour 850 à 900 m³/h nominal.
10. Un exercice de précision
Le dimensionnement d’un sécheur d’air comprimé est une discipline d’ingénierie à part entière. Il ne s’agit pas de choisir un appareil sur catalogue au hasard, mais de :
- Connaître les contraintes de l’installation
- Identifier les priorités du process
- Appliquer les correcteurs de température, pression, humidité
- Intégrer les variations de charge
✅ Une bonne pratique consiste à travailler avec les fabricants, à l’aide de leurs logiciels ou fiches de dimensionnement, et surtout à mesurer la réalité terrain (température, débit, humidité).
🎯 Un sécheur bien dimensionné est un atout majeur pour la qualité de production, la durabilité des équipements, et la maîtrise énergétique de vos installations industrielles.
En somme, l’ingénierie des fluides industriels est une discipline importante et diversifiée qui joue un rôle clé dans de nombreuses industries. Elle nécessite une expertise technique et une connaissance approfondie des systèmes de circulation des fluides, de la thermodynamique, de la mécanique des fluides, de la régulation et du contrôle des processus, ainsi que de la sécurité.
Notre blog est une ressource complète pour tout ce qui concerne les fluides industriels. Nous vous encourageons à explorer nos articles, nos guides pratiques et nos ressources de formation pour approfondir vos connaissances et améliorer vos performances énergétiques. N’hésitez pas à nous contacter pour bénéficier de nos services d’ingénierie personnalisés ou pour trouver les produits dont vous avez besoin via notre site de commerce en ligne. Ensemble, nous pouvons aller plus loin dans l’apprentissage et réaliser des économies d’énergie significatives. Contactez-nous dès aujourd’hui à l’adresse suivante :
Lien : Tuyauteries et Flexibles
Lien : Electricité et électricité industrielle
Lien: Robinetterie et tuyauterie
Lien : Échangeurs et transferts thermiques
Lien : Eau surchauffe (industrie et génie climatique)
Lien : Hydraulique et Graissage
Lien :Mesures Physique et appareils de mesures
Lien : Les sondes de mesure de température
Lien : outils de mesures (thermomètre, manomètres,…)
Lien : Matériaux en industrie (galva, acier, inox …)
Lien : Eau – filtration et traitement
Lien : Gazs réfrigérants (frigorifiques)
Lien : Filetages et taraudages
Lien : Unités de mesure et conversion
Lien: R.I.A. (Réseau Incendie Armé)
Lien : ATEX (Atmosphères Explosibles)
Lien : Agitation dans les Fluides Industriels
Lien : Le Chauffage Industriel : Un Processus Complexifié
Lien : L’Eau Glacée en Génie Climatique
Lien : Réaliser un Bilan Thermique en Génie Climatique
Lien : L’Isolation en Génie Climatique
Lien : Les Méthodes de Soudure et de Brasage : Comment Faire le Bon Choix »
Lien : Fixations Industrielles : La Clé de la Solidité et de la Sécurité
Lien : Les E.P.I. (Equipements de Protections Individuels)
0ien : Les E.P.C. (Equipements de Protection Collectifs)
Lien : Principaux de transfert thermique : la conduction, la convection et le rayonnement
Lien : Le Cercle Vertueux en Industrie : L’Écologie au Cœur des Fluides Industriels
Lien : Courroies Trapézoïdales en Industrie : L’Art de Transmettre la Puissance avec Précision
Lien : Optimisation de la Stabilité Industrielle : Lutte Efficace Contre les Vibrations des Machines
- La Gestion des Pièces Détachées en Industrie : Obsolescence, Durée de Vie et Stockage
- L’Impact de la Nature de la Surface et de la Couleur : Bilan Thermique et Transfert de Chaleur
- Comprendre les Classes de Protection IP : Un Guide Technique
- L’Art de l’Ingénierie en Mesures Physiques Industrielles : Optimisation, Contrôle et Dimentionnement des Fluides Industriels
- Innovation et Durabilité : L’Ingénierie des Fluides Industriels au Service de l’Économie Verte
- L’Énigme des Fluides Industriels : Explorons l’Inclassable
- Optimisation Énergétique dans l’Industrie : Réduire les Coûts liés aux Fluides Industriels
- Solutions Sur Mesure en Électrovannes pour Projets Spécifiques : Une Expertise Unique
- Vannes Motorisées: Standard ou Sur Mesure, Trouvez la Solution Adaptée pour Votre Application
- Guide Complet des Vannes Pneumatiques : Personnalisation, Qualité et Expertise
- Découvrez la Révolution Pneumatique : Les Vérins Sur Mesure
- Optimisation Pneumatique : Explorez Notre Gamme de Moteurs Pneumatiques
- Comment choisir le bon matériau pour vos équipements industriels : Une approche personnalisée
- Optimisation Cruciale: Les Répercussions d’un Réseau Industriel Mal Équilibré sur la Performance et la Sécurité
- Démystification des Moteurs Électriques: Un Guide Complet des Types, Avantages et Inconvénients
- Comprendre les éléments constitutifs des machines spéciales : Un guide technique pour les ingénieurs et techniciens de maintenance
- Impact Environnemental des Fluides Industriels et des Méthodes de Production
- L’évolution des systèmes de maintenance et la gestion des équipements industriels
- L’Évolution des Technologies dans les Systèmes Industriels : Air Comprimé, Groupes Froids et au-delà
- L’Importance de la Formation Continue pour les Techniciens des Fluides Industriels
- Tolérances de Côtes et Rugosité en Mécanique : Précision et Qualité en Ingénierie
- Méthodes Statistiques et Échantillonnage : L’Art d’Anticiper les Dérives Industrielles (SPC, …)
- Maîtriser l’Art du Filtrage Industriel : Comment Choisir, Lire et Entretenir les Filtres pour Optimiser Performance, Énergie et Durabilité
Lien pour achats :