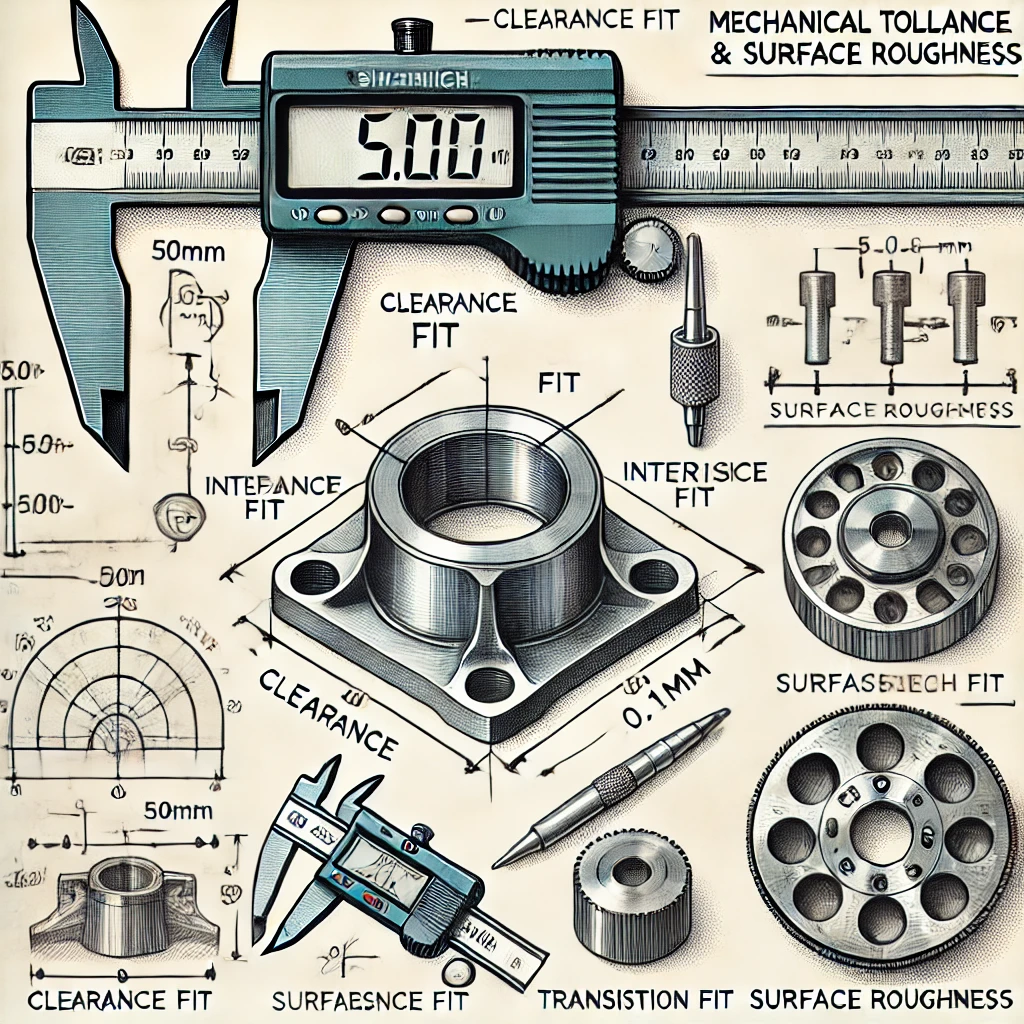
Les tolérances et ajustements jouent un rôle fondamental dans la fabrication de pièces mécaniques. Ces éléments sont essentiels pour garantir l’interchangeabilité, la précision, et la performance des produits finis. Les ajustements permettent de définir comment deux pièces s’assembleront, qu’il s’agisse d’un jeu fonctionnel ou d’une liaison serrée.
Les tolérances sont souvent définies en fonction des besoins spécifiques de l’application, mais elles doivent aussi être optimisées en termes de coût et de faisabilité. L’application correcte des normes ISO 286 est donc primordiale pour garantir la qualité des assemblages, la réduction des coûts et le respect des délais de production.
Dans cet article, nous allons explorer les systèmes de tolérances et les différents types d’ajustements, leur notation selon la norme ISO, et comment choisir les ajustements appropriés en fonction de l’application. Nous aborderons aussi les facteurs influençant le choix des ajustements et les meilleures pratiques à suivre pour optimiser la fabrication.
2. Les Normes ISO 286 : Le Système International pour les Tolérances et Ajustements
La norme ISO 286 est un système international qui définit les tolérances dimensionnelles et les ajustements. Cette norme est largement utilisée dans l’industrie pour garantir que les pièces fabriquées s’assemblent correctement, tout en permettant une certaine variation des dimensions réelles par rapport à la dimension théorique (nominale).
Concepts clés dans ISO 286 :
- Cote nominale : Dimension théorique de la pièce, celle qui est indiquée dans le dessin technique.
- Tolérance : L’écart acceptable entre la dimension réelle et la dimension nominale. Cela permet de prendre en compte les variations dues aux méthodes de fabrication.
- Position de la tolérance : Définie par la lettre dans les notations comme H7, g6, p6, etc.
- Ajustement : La relation entre les dimensions de deux pièces qui s’emboîtent l’une dans l’autre, et qui définit s’il y a jeu ou serrage entre elles.
La norme ISO 286 permet de garantir que des pièces fabriquées à des moments différents ou par différents fabricants peuvent s’assembler de manière correcte, sans risque de mauvais ajustement.
3. Les Différents Types d’Ajustements
3.1. Ajustement Glissant (ex. : H7/g6)
Un ajustement glissant permet un jeu fonctionnel entre les pièces, ce qui signifie qu’elles peuvent se déplacer l’une par rapport à l’autre. Cela est utilisé pour des applications où un mouvement fluide est nécessaire sans interférences ou blocages.
- Exemple : Un arbre H7 et un alésage g6 permettent un jeu suffisant pour un montage facile tout en garantissant que l’arbre peut tourner librement dans l’alésage.
- Application typique : Les roulements, les moteurs, et les systèmes de transmission où un mouvement est nécessaire.
3.2. Ajustement Serré (ex. : H7/p6)
Un ajustement serré crée une liaison fixe entre les pièces, ce qui signifie qu’elles ne bougeront pas sous l’effet de forces normales. Ce type d’ajustement est couramment utilisé dans des applications où il est essentiel que les pièces restent en place sans déplacement.
- Exemple : Un arbre H7 et un alésage p6 assurent un ajustement plus serré, avec un faible jeu ou aucune possibilité de mouvement.
- Application typique : Les engrenages, les joints, et les fixations où une connexion permanente ou semi-permanente est requise.
3.3. Ajustement Indifférent
Un ajustement indifférent signifie qu’il n’y a ni jeu ni serrage spécifique entre les pièces. Cela est souvent utilisé lorsque la tolérance n’a pas d’impact critique sur l’assemblage.
- Exemple : Une cote nominale avec une tolérance plus large, souvent utilisée pour des pièces structurelles comme les supports et les cadres.
- Application typique : Des pièces non critiques où une légère variation dans les dimensions ne perturbe pas la fonction de l’ensemble.
4. Comprendre la Notation des Ajustements (ISO 286)
Les ajustements sont indiqués à l’aide de notations spécifiques qui définissent la position de la tolérance ainsi que son niveau de précision. Par exemple, la notation H7/g6 suit un système qui permet de comprendre rapidement le type d’ajustement et les écarts de dimension admissibles.
- H7 : Indique un ajustement avec un jeu centré autour de la dimension nominale. Cela signifie que l’écart de dimension est égal dans les deux sens, vers l’intérieur et l’extérieur.
- g6 : Indique une tolérance avec un jeu vers l’extérieur, où la dimension réelle de la pièce sera légèrement plus petite que la dimension nominale.
Exemple de notation :
- H7/g6 : Tolérance pour un arbre H7 et un alésage g6, créant un ajustement glissant avec un jeu précis entre les pièces.
5. Choisir l’Ajustement Adapté à l’Application
Le choix du type d’ajustement dépend principalement de la fonction de la pièce, du matériau et de l’application spécifique. Par exemple :
- Ajustement glissant : Utilisé dans les applications où un mouvement libre est nécessaire, comme les roulements à billes.
- Ajustement serré : Utilisé dans des applications où des forces de fixation doivent être appliquées pour empêcher tout mouvement entre les pièces, comme dans les engrenages.
- Ajustement indifférent : Choisi pour des pièces où la fonctionnement est moins sensible aux variations dimensionnelles, telles que les pièces de structuration.
6. Impact des Tolérances et Ajustements sur la Fabrication
Les ajustements et les tolérances influencent directement les coûts et la précision de la fabrication. Par exemple :
- Ajustements serrés : Requérant une précision élevée dans l’usinage, ils augmentent les coûts de production.
- Ajustements glissants : Généralement plus faciles et moins coûteux à produire, mais peuvent entraîner des problèmes d’interférences si mal dimensionnés.
Il est essentiel de choisir des ajustements adaptés pour minimiser les coûts tout en garantissant la qualité et la performance des assemblages.
7. Bonnes Pratiques pour Appliquer les Systèmes de Tolérances et Ajustements
Voici quelques bonnes pratiques pour garantir un assemblage optimal :
- Comprendre l’application : Choisir un ajustement basé sur la fonction de la pièce et les contraintes mécaniques.
- Vérification des tolérances : Utiliser des instruments de mesure comme des micromètres ou des machines à mesurer tridimensionnelles (MMT) pour vérifier la conformité des ajustements.
- Contrôle des jeux et interférences : Tenir compte de la dilatation thermique et des contraintes mécaniques pour éviter tout problème lors de l’assemblage.
8. Le Rôle des Jeux et Interférences dans les Assemblages
Lorsque des ajustements sont effectués, il est important de prendre en compte :
- Les jeux fonctionnels : L’espace entre deux pièces qui permet le mouvement sans friction excessive.
- Les interférences : Lorsque deux pièces sont trop serrées, ce qui peut entraîner une déformation sous contrainte.
En tenant compte de la dilatation thermique, des contraintes mécaniques et des méthodes d’usinage, vous pouvez optimiser les ajustements et garantir des performances maximales des assemblages.
9. Exemples Pratiques d’Ajustements dans l’Industrie
Application dans l’automobile :
Les pièces mobiles des moteurs nécessitent des ajustements serrés pour garantir une performance optimale, tandis que les éléments structurels comme les châssis peuvent accepter des tolérances plus larges.
Les tolérances et ajustements sont des aspects cruciaux de la fabrication des pièces mécaniques. En comprenant le système ISO 286, vous pouvez garantir des assemblages parfaits, tout en optimisant les coûts et la production. Que vous choisissiez un ajustement glissant, serré, ou indifférent, il est essentiel de bien comprendre l’application et la fonction de chaque pièce avant de définir ses tolérances.
En intégrant ces notions à votre expertise technique, vous pourrez améliorer la précision, la qualité et la rentabilité de vos projets mécaniques.
Notre blog est une ressource complète pour tout ce qui concerne les fluides industriels. Nous vous encourageons à explorer nos articles, nos guides pratiques et nos ressources de formation pour approfondir vos connaissances et améliorer vos performances énergétiques. N’hésitez pas à nous contacter pour bénéficier de nos services d’ingénierie personnalisés ou pour trouver les produits dont vous avez besoin via notre site de commerce en ligne. Ensemble, nous pouvons aller plus loin dans l’apprentissage et réaliser des économies d’énergie significatives. Contactez-nous dès aujourd’hui à l’adresse suivante :
- Tolérances en Mécanique : Comprendre les Différents Types et Leurs Applications
- Tolérances de Côtes et Rugosité en Mécanique : Maîtriser la Précision pour des Assemblages Fiables
- Tolérances de Côtes et Rugosité en Mécanique : Précision et Qualité en Ingénierie
- La Rugosité en Mécanique et en Mécanique de Précision : Guide Complet
- Tolérances en Mécanique et en Mécanique de Précision : Guide Complet
Lien pour achats :