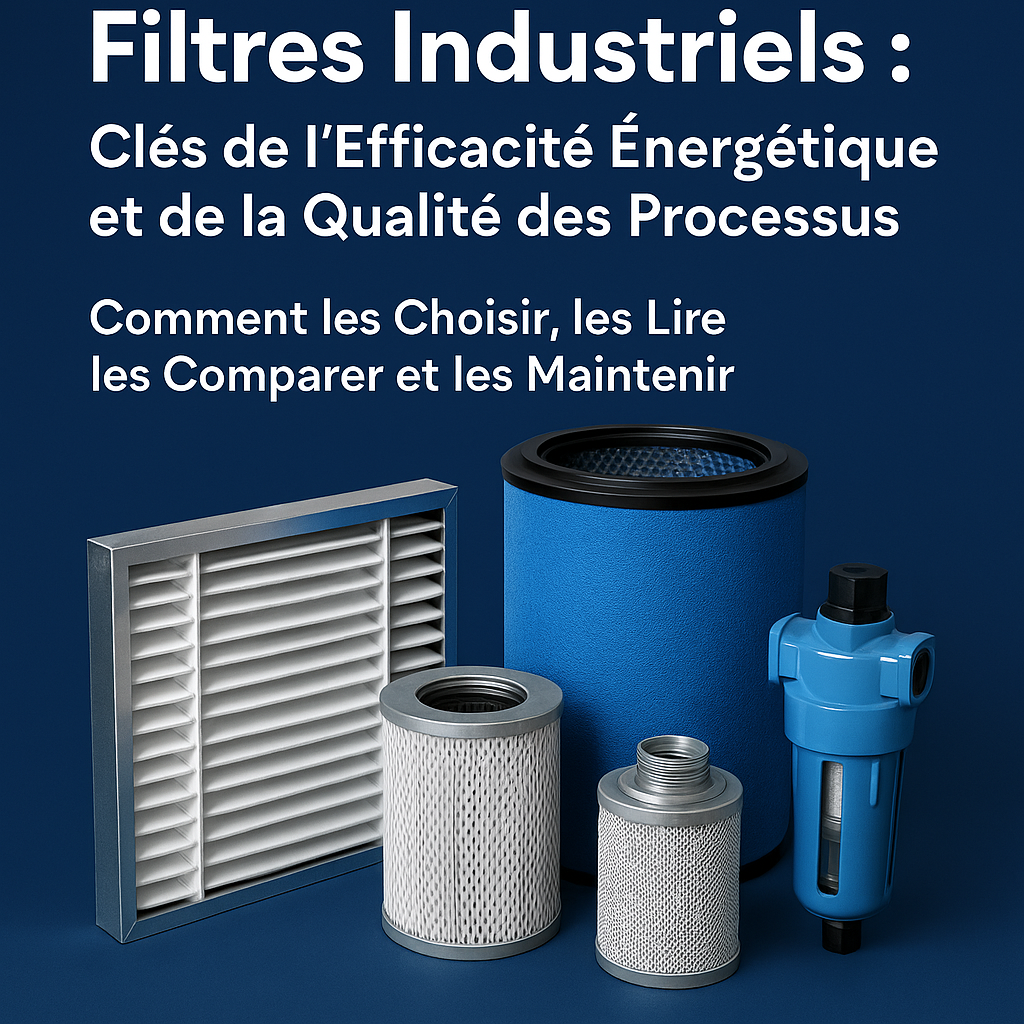
🔍 Le Filtre, Maillon Souvent Négligé mais Essentiel pour la Performance Industrielle
Dans les coulisses de toute installation industrielle performante, des composants silencieux agissent comme des gardiens invisibles de la qualité, de la sécurité et de l’efficacité énergétique. Parmi eux, le filtre tient un rôle fondamental — et pourtant, il est bien trop souvent relégué au second plan. On le considère comme un simple consommable, un détail du process, un élément interchangeable. Cette perception est non seulement injuste, mais surtout dangereuse et coûteuse pour les exploitants.
Un filtre mal choisi, mal dimensionné ou mal entretenu peut générer une série d’effets en cascade : surconsommation énergétique, dégradation prématurée du matériel, baisse de qualité du produit fini, voire contamination de l’environnement ou des produits transformés. Ce composant discret influence pourtant directement la fiabilité d’un système, la rentabilité des équipements, et la conformité réglementaire.
Dans un réseau d’air comprimé par exemple, un filtre colmaté ou mal adapté peut contraindre un compresseur à fournir un surcroît de pression pour maintenir le débit nominal. Résultat : augmentation de la consommation électrique, usure mécanique accélérée, risque de coupures imprévues, et perte de productivité. Dans les systèmes de ventilation ou de climatisation industrielle, une perte de charge excessive induite par un filtre bouché peut faire grimper la consommation énergétique de plusieurs dizaines de pourcents.
Le filtre est souvent perçu à tort comme une simple « barrière à saletés ». En réalité, il agit comme un régulateur de pureté, un protecteur du process et un garant de la performance globale. Il doit être sélectionné en fonction de multiples paramètres : le type de fluide à filtrer (air, vapeur, gaz, liquide, vide), le débit nominal, la granulométrie des particules à intercepter, la température, la pression, la compatibilité chimique avec le matériau filtrant, ou encore l’environnement de fonctionnement.
Dans l’industrie de l’air comprimé, par exemple, on distingue plusieurs niveaux de filtration : préfiltration grossière, filtration fine, coalescence pour les aérosols, adsorption pour les vapeurs d’huile ou d’hydrocarbures. Chacun de ces filtres est indispensable pour garantir un air de qualité conforme à la norme ISO 8573-1, en fonction des exigences du process industriel (agroalimentaire, pharmaceutique, électronique…).
Autre exemple critique : dans les circuits de fluide caloporteur ou de refroidissement, un filtre mal calibré peut laisser passer des impuretés qui vont obstruer des échangeurs de chaleur ou endommager des pompes. À l’inverse, un filtre trop fin ou mal entretenu provoque une perte de charge importante, source d’instabilité hydraulique et de déséquilibre thermique.
La lecture d’une fiche technique de filtre est donc une compétence stratégique. Il ne suffit pas de regarder la taille ou la marque : il faut analyser les données clés comme le débit nominal, la perte de charge initiale (ΔP), la classe de filtration (souvent exprimée selon les normes ISO 16890, EN779 ou ISO 16889), la surface filtrante, le type de média utilisé (papier, fibre de verre, polyester, nanofibres…) et la capacité de rétention.
Un piège fréquent est de comparer deux filtres sans tenir compte de la vitesse de passage du fluide. Or, un filtre testé à une vitesse plus faible affichera une efficacité apparente meilleure et une perte de charge plus faible — ce qui biaise totalement la comparaison. Il est donc essentiel de ramener les caractéristiques à des unités communes, et de demander les protocoles de test (pression, température, particules utilisées, conditions de saturation…).
Autre astuce importante : se méfier des indicateurs de perte de charge installés sur les filtres. Si cet indicateur affiche une chute brutale du ΔP, cela peut signifier que le filtre est colmaté… ou qu’il s’est fissuré. Dans ce dernier cas, le fluide passe sans être filtré, mettant en danger tout le système aval. Il est donc impératif d’intégrer une inspection visuelle régulière dans le programme de maintenance, et de ne pas se reposer uniquement sur un manomètre.
Sur le plan énergétique, le filtre est un levier d’optimisation majeur. Un filtre propre, bien dimensionné, permet de réduire drastiquement les consommations. Un compresseur industriel de 90 kW, par exemple, peut économiser jusqu’à 5 000 euros par an simplement grâce à une meilleure gestion de sa chaîne de filtration. Les pertes de charge cumulées, invisibles à l’œil nu, peuvent représenter 10 à 15 % de la consommation énergétique totale d’un système. Autrement dit : négliger ses filtres, c’est laisser s’échapper des milliers d’euros par an.
Le suivi rigoureux de l’état des filtres est également un enjeu de maintenance préventive. La durée de vie d’un filtre dépend directement de l’environnement de travail. Dans une atmosphère poussiéreuse, saturée en huiles ou en humidité, un filtre aura une durée de vie bien plus courte que dans une salle blanche. Il convient donc de définir des plages de contrôle adaptées et de tenir un registre de maintenance précis, intégrant la date de remplacement, les observations de colmatage, la perte de charge constatée, et toute évolution anormale.
Avec l’arrivée des technologies numériques et des capteurs IoT, certains filtres deviennent aujourd’hui « intelligents ». Ils embarquent des capteurs de pression différentielle, de température ou d’humidité, et peuvent alerter automatiquement les techniciens via un système de supervision. Ces filtres connectés permettent de déclencher une maintenance prédictive, en remplaçant les filtres au bon moment, ni trop tôt (gaspillage), ni trop tard (risques de non-conformité). Cette évolution s’inscrit dans la logique du retrofit intelligent, visant à prolonger la vie des équipements en les dotant de nouvelles capacités sans modifier l’infrastructure d’origine.
Par ailleurs, les matériaux filtrants évoluent rapidement. Les membranes en nanofibres, le graphène ou encore les mousses polymères multi-couches permettent aujourd’hui d’atteindre des rendements de filtration extrêmes avec des pertes de charge très faibles. Certains filtres auto-nettoyants, utilisés dans les environnements très pollués (tunnels, mines, cimenteries…), fonctionnent en circuit fermé avec des cycles automatiques de régénération.
Il est temps de considérer le filtre comme un élément stratégique de l’ingénierie industrielle. Il ne s’agit plus d’un simple consommable mais d’un composant actif, qui influence les résultats, la sécurité, la rentabilité et la durabilité de toute la chaîne de production.
Pour une entreprise industrielle, adopter une politique de filtration intelligente, c’est investir dans la continuité de service, la maîtrise des coûts d’exploitation, et la conformité réglementaire. Cela implique de former les équipes, de sélectionner rigoureusement les filtres, d’analyser les retours terrain, de surveiller en temps réel les performances, et de travailler avec des fournisseurs capables de justifier leurs performances avec des données vérifiables et traçables.
En résumé, un bon filtre, bien choisi et bien entretenu, prolonge la vie des équipements, améliore la qualité des produits, réduit les coûts, et protège l’environnement de travail. Un mauvais filtre, en revanche, transforme chaque gain potentiel en risque latent.
L’ingénierie des fluides industriels, l’optimisation énergétique, et la gestion de la maintenance intelligente ne peuvent plus se concevoir sans une stratégie de filtration robuste, documentée, et proactive. À l’heure où chaque kWh compte, où la traçabilité est un enjeu règlementaire, et où les marges se réduisent, repenser le rôle du filtre est un acte de performance industrielle durable.
🔧 Tableau 1 : Conséquences d’un Filtre Mal Choisi ou Mal Entretenu
Conséquence | Impact sur le Processus |
---|---|
Surconsommation énergétique | Hausse des coûts d’exploitation, réduction de la rentabilité |
Dégradation des équipements | Usure prématurée, pannes fréquentes, maintenance imprévue |
Baisse de qualité du produit final | Non-conformité, retours clients, réputation dégradée |
Contamination de l’environnement | Risques sanitaires, rejets polluants, sanctions réglementaires |
Perte de pression / Débit irrégulier | Déséquilibres hydrauliques, performances aléatoires du système |
Arrêt de production | Temps d’arrêt coûteux, retards, insatisfaction client |
🧠 Tableau 2 : Critères de Sélection d’un Filtre Industriel
Critère | Détails à considérer |
---|---|
Type de fluide | Air, gaz, liquide, vapeur, vide |
Niveau de filtration | Préfiltration, filtration fine, coalescence, adsorption |
Débit nominal | Doit être adapté au système sans provoquer de perte de charge excessive |
Pression de fonctionnement | Compatibilité avec le réseau (ex. : haute pression en air comprimé) |
Température | Résistance du matériau filtrant à la température du fluide |
Compatibilité chimique | Compatibilité avec huiles, solvants, acides, bases… selon le process |
Classe de filtration (normes) | ISO 8573-1 (air), ISO 16890 / EN779 (air ambiant), ISO 16889 (liquides) |
Perte de charge initiale (ΔP) | Indicateur clé de performance énergétique |
Dimensions / encombrement | Compatibilité avec le système existant |
Accessibilité pour maintenance | Facilité de démontage, nettoyage ou remplacement |
🧪 Tableau 3 : Technologies et Matériaux Filtrants
Type de Filtrant | Avantages | Applications typiques |
---|---|---|
Fibre de verre | Haute efficacité, bon rapport ΔP/efficacité | Air comprimé, filtration fine |
Polyester / cellulose | Économique, recyclable | Préfiltration, milieux secs |
Nanofibres | Faible perte de charge, filtration très fine | Pharmaceutique, électronique |
Charbon actif / adsorption | Absorption des vapeurs, odeurs, gaz | Air comprimé, traitement des COV |
Mousse polymère multi-couche | Auto-nettoyant, durable | Environnements très poussiéreux ou encrassants |
Métal fritté | Résistant aux hautes températures, nettoyage possible | Vapeur, huiles, hydrocarbures |
🧰 Tableau 4 : Astuces et Bonnes Pratiques de Maintenance
Bonne pratique | Pourquoi c’est important |
---|---|
Suivre la perte de charge réelle | Détecter colmatage ou rupture du filtre |
Comparer les filtres à débit équivalent | Éviter les biais de test (ΔP trop favorable à bas débit) |
Tenir un registre de maintenance | Suivi précis pour prédiction des remplacements |
Planifier le remplacement en conditions réelles | Adapter la fréquence selon l’environnement (poussières, humidité, huiles…) |
Vérifier visuellement les cartouches | Détection de fissures, défauts d’étanchéité |
Choisir des filtres certifiés | Assurer traçabilité et qualité (normes ISO, tests indépendants) |
Utiliser des filtres connectés (IoT) | Supervision à distance, maintenance prédictive, alertes automatiques |
⚡ Tableau 5 : Bénéfices d’une Stratégie de Filtration Optimisée
Bénéfice | Explication |
---|---|
Économies d’énergie | Réduction des pertes de charge, meilleure efficacité des équipements |
Moins d’arrêts imprévus | Prévention des pannes grâce à une filtration efficace |
Amélioration de la qualité produit | Air, fluide ou vapeur propre = produit conforme et stable |
Respect des normes (ISO, qualité, sécurité) | Obligations respectées dans l’agroalimentaire, pharma, chimie, etc. |
Durabilité accrue des installations | Moins de particules abrasives = longévité des pompes, vannes, échangeurs… |
Environnement de travail plus sain | Moins de poussières, aérosols ou contaminants libérés dans l’atmosphère ambiante |
En somme, l’ingénierie des fluides industriels est une discipline importante et diversifiée qui joue un rôle clé dans de nombreuses industries. Elle nécessite une expertise technique et une connaissance approfondie des systèmes de circulation des fluides, de la thermodynamique, de la mécanique des fluides, de la régulation et du contrôle des processus, ainsi que de la sécurité.
Notre blog est une ressource complète pour tout ce qui concerne les fluides industriels. Nous vous encourageons à explorer nos articles, nos guides pratiques et nos ressources de formation pour approfondir vos connaissances et améliorer vos performances énergétiques. N’hésitez pas à nous contacter pour bénéficier de nos services d’ingénierie personnalisés ou pour trouver les produits dont vous avez besoin via notre site de commerce en ligne. Ensemble, nous pouvons aller plus loin dans l’apprentissage et réaliser des économies d’énergie significatives. Contactez-nous dès aujourd’hui à l’adresse suivante :
Lien : Tuyauteries et Flexibles
Lien : Electricité et électricité industrielle
Lien: Robinetterie et tuyauterie
Lien : Échangeurs et transferts thermiques
Lien : Eau surchauffe (industrie et génie climatique)
Lien : Hydraulique et Graissage
Lien :Mesures Physique et appareils de mesures
Lien : Les sondes de mesure de température
Lien : outils de mesures (thermomètre, manomètres,…)
Lien : Matériaux en industrie (galva, acier, inox …)
Lien : Eau – filtration et traitement
Lien : Gazs réfrigérants (frigorifiques)
Lien : Filetages et taraudages
Lien : Unités de mesure et conversion
Lien: R.I.A. (Réseau Incendie Armé)
Lien : ATEX (Atmosphères Explosibles)
Lien : Agitation dans les Fluides Industriels
Lien : Le Chauffage Industriel : Un Processus Complexifié
Lien : L’Eau Glacée en Génie Climatique
Lien : Réaliser un Bilan Thermique en Génie Climatique
Lien : L’Isolation en Génie Climatique
Lien : Les Méthodes de Soudure et de Brasage : Comment Faire le Bon Choix »
Lien : Fixations Industrielles : La Clé de la Solidité et de la Sécurité
Lien : Les E.P.I. (Equipements de Protections Individuels)
0ien : Les E.P.C. (Equipements de Protection Collectifs)
Lien : Principaux de transfert thermique : la conduction, la convection et le rayonnement
Lien pour achats :