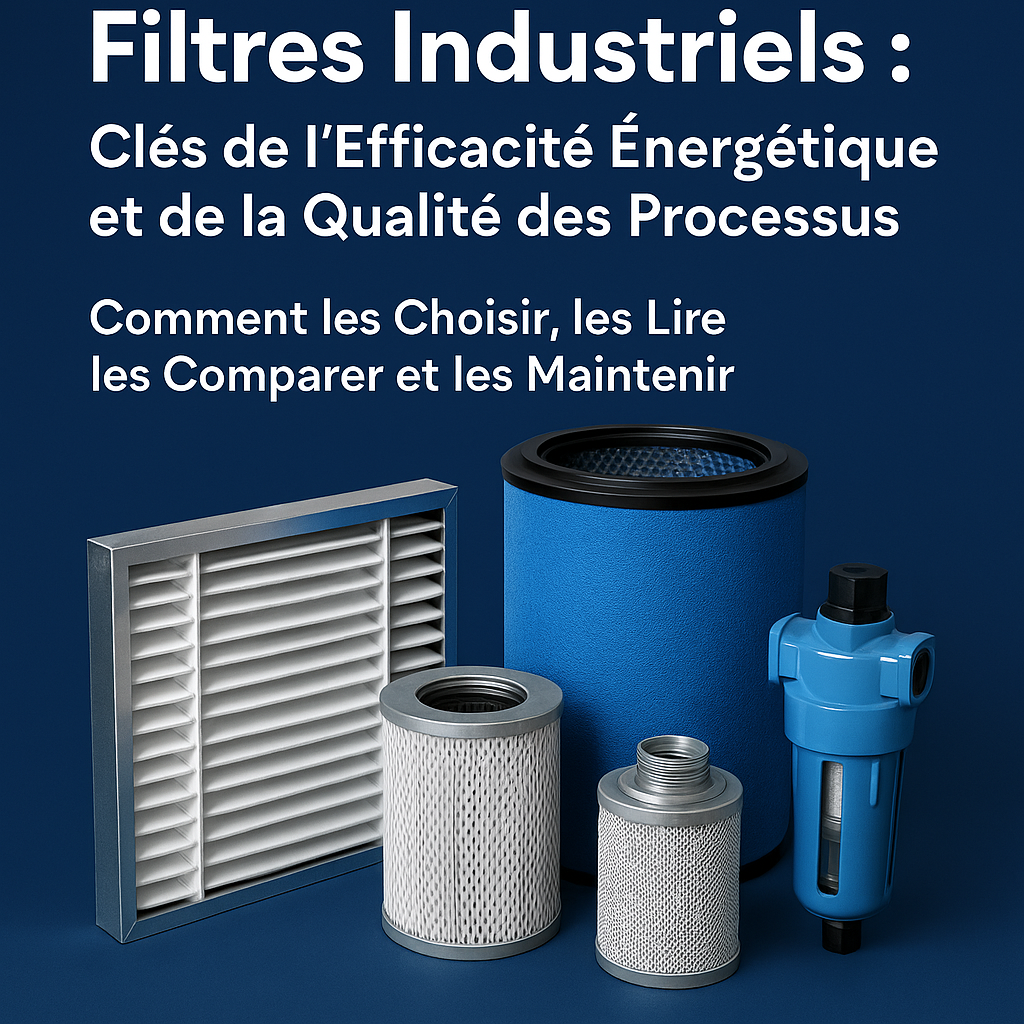
Dans l’univers industriel, l’efficacité énergétique est souvent présentée comme une affaire de gros investissements, de technologies de rupture ou de stratégies de production complexes. Et pourtant, un maillon discret mais fondamental est trop souvent négligé : le filtre. À tort considéré comme un simple consommable de maintenance, le filtre est en réalité un acteur majeur de la performance énergétique et opérationnelle.
Le filtre, un régulateur invisible
Un filtre industriel n’est pas qu’un tamis qui retient des particules. C’est un organe technique intelligent qui agit comme une barrière, un modulateur et un protecteur. Il filtre l’air, les liquides, les gaz, l’huile… en fonction du besoin, du process et de la qualité recherchée. Son rôle est à la fois qualitatif (propreté, pureté, normes) et quantitatif (performance énergétique, débit constant).
Ce qui rend un filtre crucial dans la consommation énergétique, c’est la perte de charge qu’il induit. Cette perte de pression (ou perte de charge) est la résistance qu’un fluide ou un gaz rencontre en traversant le filtre. Et plus cette résistance est élevée, plus le moteur, compresseur, ventilateur ou pompe en amont doit travailler… donc consommer.
Le piège énergétique du filtre colmaté
Prenons un exemple concret. Dans un système de ventilation, si un filtre à air est encrassé par des poussières, il va nécessiter deux fois plus de puissance électrique pour maintenir le même débit d’air. La consommation du ventilateur peut ainsi doubler sans que cela ne soit immédiatement visible — sauf sur la facture énergétique mensuelle.
Dans les réseaux d’air comprimé, même scénario : un filtre colmaté multiplie les pertes de pression. Un simple delta de 1 bar de pression supplémentaire impose jusqu’à 7% de consommation énergétique en plus pour un compresseur. Et cette pression excédentaire se propage dans tout le réseau, dégradant la performance globale du système.
Pourquoi un mauvais filtre coûte (très) cher
Un filtre mal choisi ou mal entretenu ne se contente pas d’augmenter la facture énergétique. Il met aussi en péril l’intégrité des équipements, la qualité des produits finis et même la sécurité des process.
- Matériel dégradé prématurément : des pompes, compresseurs ou vérins pneumatiques reçoivent des particules ou fluides impurs, ce qui use les joints, pistons ou roulements.
- Qualité de production compromise : un fluide non filtré correctement peut contaminer des produits chimiques, alimentaires, pharmaceutiques.
- Maintenance imprévisible : le colmatage brutal d’un filtre peut générer une alarme de perte de pression, stopper une ligne de production, ou provoquer une défaillance en chaîne.
Ce qui devait coûter quelques euros par mois finit par coûter des milliers d’euros en panne, en énergie perdue ou en rebut.
Astuce d’ingénieur : la pression différentielle, baromètre de l’efficacité
La pression différentielle (ΔP) est l’un des meilleurs indicateurs de la santé d’un filtre. Elle mesure la différence de pression entre l’entrée et la sortie du filtre.
- Une ΔP trop faible peut indiquer un filtre inefficace (média percé, non adapté).
- Une ΔP trop élevée montre un filtre encrassé, colmaté, ou sous-dimensionné.
Bon à savoir : installer des capteurs de pression différentielle avec alerte peut permettre une maintenance préventive optimisée et économique. Il suffit d’un seuil ΔP bien paramétré pour déclencher le changement du filtre au bon moment (ni trop tôt, ni trop tard).
Les filtres dans les réseaux d’air comprimé : le levier caché d’économie
L’air comprimé est souvent surnommé « le quatrième fluide industriel » après l’électricité, l’eau et la vapeur. Il est aussi l’un des plus coûteux énergétiquement : produire de l’air comprimé demande entre 6 à 10 kWh pour 1 m³ d’air utile. Autant dire que chaque bar de pression économisé compte.
Et là encore, le rôle du filtre est déterminant.
- Les filtres coalescents éliminent les microgouttelettes d’eau et d’huile. Un colmatage provoque une chute de pression soudaine.
- Les filtres à particules protègent les machines de la poussière, des scories, ou du métal résiduel.
- Les filtres à charbon actif purifient l’air pour les process sensibles (agro, pharma, électronique).
Un réseau mal filtré ou mal conçu entraîne :
- Une pression inutilement élevée à la sortie du compresseur.
- Des purges d’eau mal évacuées.
- Une contamination progressive de tout le réseau.
- Un surdimensionnement des équipements pour compenser les pertes.
Règle d’or : chaque bar compte
Perdre 1 bar de pression sur un réseau, c’est perdre entre 6 et 8% de performance énergétique. Ce bar perdu peut simplement venir d’un filtre non adapté, usé ou encrassé.
Par exemple :
- Un filtre coalescent en fin de vie augmente de 0,3 à 0,6 bar la perte de charge.
- Deux filtres mal positionnés en série provoquent une perte de 1 bar.
- Un filtre mal purgé se transforme en bouchon hydraulique, bloquant l’écoulement.
Dans les grands réseaux, ces détails invisibles sont multipliés par des dizaines de points d’utilisation. Résultat : des dizaines de milliers d’euros d’énergie gâchée par an.
Maintenance des filtres : un investissement, pas une dépense
La maintenance préventive et le suivi intelligent des filtres est un levier ROIste immédiat. Remplacer un filtre à 80 euros qui consommait 1000 euros d’électricité en trop par an… c’est mathématique.
Quelques recommandations clés :
- Planifier un calendrier de remplacement basé sur la ΔP et non sur une durée arbitraire.
- Stocker des filtres compatibles, certifiés, pour éviter les improvisations en cas de panne.
- Former les techniciens à identifier les pertes de charge anormales.
- Installer des systèmes de télémétrie sur les filtres critiques (air comprimé, ventilation, fluides spéciaux).
- Contrôler le taux de colmatage par des tests de débit ou analyse visuelle (filtres transparents, manomètres intégrés).
Optimisation par le design de réseau
Au-delà du filtre lui-même, la conception du réseau de filtration a un impact majeur sur la performance énergétique.
- Préférez une filtration répartie plutôt que centralisée pour éviter les surpressions inutiles.
- Positionnez les purges automatiques en amont et en aval des filtres d’air comprimé.
- Respectez les vitesses nominales de passage dans les carters (évite l’effet venturi destructeur).
- Dimensionnez les filtres pour le débit maximal réel, pas juste théorique.
- Évitez les coudes ou T en entrée/sortie de filtre qui créent des turbulences.
La technologie au service de la filtration
De nombreuses innovations permettent aujourd’hui de transformer la filtration en alliée digitale et prédictive :
- Filtres connectés avec capteurs de pression, de température, d’humidité.
- Médias filtrants intelligents capables de détecter leur saturation (par variation de conductivité, couleur ou résistance).
- IA embarquée dans les systèmes de gestion HVAC ou compresseurs pour prédire les colmatages.
- Jumeaux numériques pour simuler l’encrassement d’un réseau et anticiper les besoins de filtration.
Bon à savoir : les gains d’efficacité énergétique générés par ces technologies sont souvent compris entre 5 à 15% selon le secteur, pour un retour sur investissement entre 6 et 18 mois.
Le filtre, premier levier de performance énergétique cachée
Loin d’être un simple consommable interchangeable, le filtre est un régulateur de flux, un protecteur de qualité, et un allié de l’efficacité énergétique. Dans un contexte où chaque kWh économisé compte, il mérite toute l’attention stratégique des ingénieurs, responsables maintenance et énergéticiens.
Choisir un filtre de qualité, bien l’entretenir, comprendre son comportement… c’est s’offrir une production plus stable, plus propre, plus durable, et surtout plus économe.
Alors posons-nous la vraie question : combien coûtent vraiment vos filtres ? Et combien pourraient-ils vous faire économiser ?
📊 Tableau 1 – Conséquences d’un Filtre Colmaté ou Mal Dimensionné
🚨 Problème identifié | ⚡ Conséquences immédiates | 💰 Impact économique |
---|---|---|
Filtre encrassé (colmaté) | Perte de charge accrue, débit réduit | Surconsommation énergétique (+10 à +30%) |
Filtre mal dimensionné | Vitesse excessive ou sous-filtration | Dégradation de l’équipement, arrêts fréquents |
Absence de capteur ΔP | Remplacement trop tardif ou trop précoce | Coût de maintenance inutile ou pannes non anticipées |
Système de purge inefficace | Eau stagnante dans le filtre | Risque de blocage hydraulique ou corrosion |
Mauvaise installation (coudes) | Turbulences internes, pertes supplémentaires | Usure prématurée, rendement faible |
⚙️ Tableau 2 – Bénéfices de Filtres Performants et Bien Suivis
✅ Action / Pratique recommandée | ⚙️ Résultat technique | 🌱 Gain énergétique & économique |
---|---|---|
Choisir un filtre adapté au débit réel | Pression stable, pas de perte de charge excessive | Économie d’énergie de 5 à 10% |
Remplacer les filtres dès que ΔP atteint seuil critique | Maintien du rendement optimal | Moins de pannes, réduction des coûts de maintenance |
Installer des capteurs ΔP et télémétrie | Suivi en temps réel, alertes automatiques | Maintenance préventive et économies |
Nettoyer régulièrement les zones autour des filtres | Moins de colmatage dû aux contaminants extérieurs | Allongement de la durée de vie du filtre |
Utiliser des médias filtrants de qualité certifiée | Meilleure filtration, pas de relargage de particules | Qualité de production maîtrisée |
🌬️ Tableau 3 – Application spécifique aux Réseaux d’Air Comprimé
🔧 Équipement concerné | 🎯 Filtre utilisé | 🧪 Rôle technique | 💸 Risques en cas de filtre colmaté ou absent |
---|---|---|---|
Compresseur | Filtre à particules / air d’admission | Protège le compresseur de la poussière | Usure prématurée, baisse de rendement |
Sécheur d’air | Préfiltre coalescent | Retire huile/eau avant traitement | Saturation du sécheur, perte d’efficacité |
Réseau de distribution | Filtre ligne/particules | Évite pollution descendante | Contamination globale du réseau |
Point d’utilisation | Filtre fin / charbon actif | Air purifié pour process agro, pharmaceutique, etc. | Rejet produit, mise en cause qualité, arrêt de production |
Purge automatique | Intégrée sous filtre coalescent | Évacue eau et huile en continu | Blocage réseau, surpression, corrosion |
📈 Tableau 4 – Bons à Savoir et Astuces d’Ingénieur
💡 Astuce / Bon à savoir | 🔍 Détail technique ou pratique |
---|---|
1 bar perdu = +7% de consommation | Ajuster la pression pour compenser un filtre colmaté est coûteux |
ΔP > seuil = signal de changement | Installer manomètre différentiel pour contrôle simple |
Filtration décentralisée = meilleure efficacité globale | Limite la surpression généralisée, réduit la perte de charge |
Filtres intelligents = maintenance prédictive | Connectivité, IA, alertes de saturation, durée de vie estimée |
Une bonne purge = longévité du filtre | Une purge automatique évite l’eau stagnante et protège le média |
En somme, l’ingénierie des fluides industriels est une discipline importante et diversifiée qui joue un rôle clé dans de nombreuses industries. Elle nécessite une expertise technique et une connaissance approfondie des systèmes de circulation des fluides, de la thermodynamique, de la mécanique des fluides, de la régulation et du contrôle des processus, ainsi que de la sécurité.
Notre blog est une ressource complète pour tout ce qui concerne les fluides industriels. Nous vous encourageons à explorer nos articles, nos guides pratiques et nos ressources de formation pour approfondir vos connaissances et améliorer vos performances énergétiques. N’hésitez pas à nous contacter pour bénéficier de nos services d’ingénierie personnalisés ou pour trouver les produits dont vous avez besoin via notre site de commerce en ligne. Ensemble, nous pouvons aller plus loin dans l’apprentissage et réaliser des économies d’énergie significatives. Contactez-nous dès aujourd’hui à l’adresse suivante :
Lien : Tuyauteries et Flexibles
Lien : Electricité et électricité industrielle
Lien: Robinetterie et tuyauterie
Lien : Échangeurs et transferts thermiques
Lien : Eau surchauffe (industrie et génie climatique)
Lien : Hydraulique et Graissage
Lien :Mesures Physique et appareils de mesures
Lien : Les sondes de mesure de température
Lien : outils de mesures (thermomètre, manomètres,…)
Lien : Matériaux en industrie (galva, acier, inox …)
Lien : Eau – filtration et traitement
Lien : Gazs réfrigérants (frigorifiques)
Lien : Filetages et taraudages
Lien : Unités de mesure et conversion
Lien: R.I.A. (Réseau Incendie Armé)
Lien : ATEX (Atmosphères Explosibles)
Lien : Agitation dans les Fluides Industriels
Lien : Le Chauffage Industriel : Un Processus Complexifié
Lien : L’Eau Glacée en Génie Climatique
Lien : Réaliser un Bilan Thermique en Génie Climatique
Lien : L’Isolation en Génie Climatique
Lien : Les Méthodes de Soudure et de Brasage : Comment Faire le Bon Choix »
Lien : Fixations Industrielles : La Clé de la Solidité et de la Sécurité
Lien : Les E.P.I. (Equipements de Protections Individuels)
0ien : Les E.P.C. (Equipements de Protection Collectifs)
Lien : Principaux de transfert thermique : la conduction, la convection et le rayonnement
Lien pour achats :