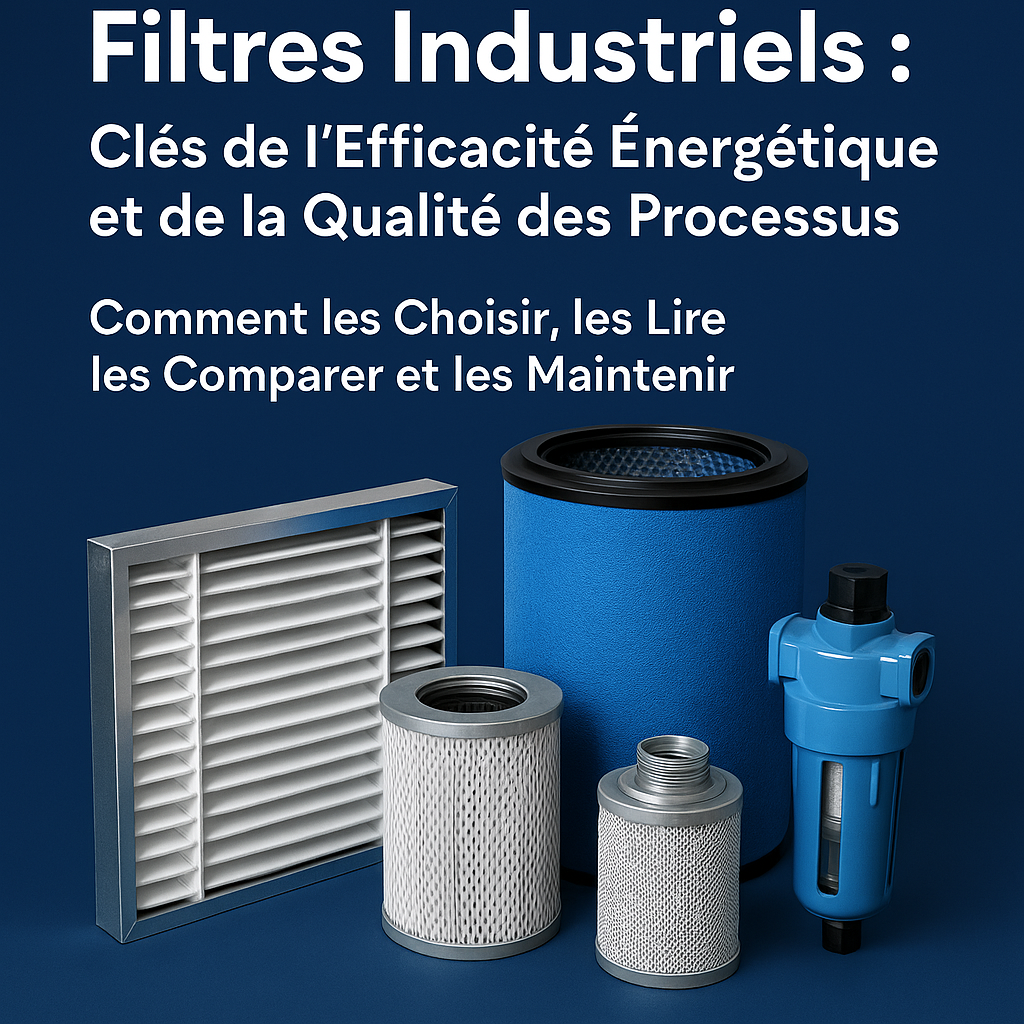
Dans le monde industriel où chaque kilowatt-heure compte, la filtration est trop souvent considérée comme une simple formalité technique, alors qu’elle est au contraire un levier puissant d’efficacité énergétique et de performance économique durable. En production, dans les utilités ou en environnement contrôlé, les filtres jouent un rôle de gardien invisible : ils purifient, protègent et conditionnent l’air, l’eau, la vapeur, les huiles ou encore les gaz utilisés dans les process. Pourtant, derrière leur apparente simplicité, les filtres dissimulent une vérité physique incontournable : plus un filtre est performant, plus il crée une perte de charge, et plus cette perte est importante, plus le système consomme d’énergie.
Le véritable défi est donc de trouver l’équilibre subtil entre qualité de filtration, faible perte de charge et sobriété énergétique. Et ce n’est pas un sujet secondaire : dans une usine de taille moyenne, la mauvaise gestion de la filtration peut représenter jusqu’à 15 % de la facture électrique, notamment dans les réseaux d’air comprimé, de ventilation industrielle, ou de refroidissement.
Comprendre ce lien entre efficacité de filtration, perte de charge et consommation énergétique, c’est poser un regard d’ingénieur sur la question. Un filtre retient des particules (solides ou liquides), mais cette rétention génère une résistance à l’écoulement du fluide. Cette résistance, appelée perte de charge, oblige les compresseurs, pompes ou ventilateurs à travailler davantage pour maintenir le débit ou la pression souhaités. Plus le média filtrant est dense ou encrassé, plus cette résistance augmente. Résultat : surconsommation électrique, usure prématurée des machines, baisse de productivité et alourdissement des coûts.
Voici un tableau récapitulatif du lien direct entre filtration, perte de charge et consommation :
Paramètre technique | Impact sur le système | Conséquence énergétique |
---|---|---|
Média filtrant très fin (0,01 micron) | Haute efficacité de filtration | Perte de charge initiale plus élevée |
Colmatage progressif du filtre | Augmentation progressive de la résistance au fluide | Hausse de la consommation des moteurs |
Température du fluide | Viscosité plus élevée = débit plus difficile | Effort plus important du groupe motopompe |
Vitesse d’écoulement trop rapide | Chute de pression anormale | Surcharge du compresseur ou pompe |
Filtre sous-dimensionné | Saturation accélérée | Interventions fréquentes et pics de consommation |
🧠 Bon à savoir : La perte de charge acceptable dans un filtre dépend du fluide, du média, et du type de process. En air comprimé, on vise souvent < 0,2 bar pour les filtres principaux. Au-delà, le coût énergétique grimpe en flèche.
Le problème devient critique lorsque les filtres ne sont pas remplacés ou entretenus à temps. Un filtre colmaté agit comme un étranglement dans le circuit, forçant les moteurs à fonctionner en surrégime pour compenser. Dans un compresseur d’air, par exemple, une perte de charge de 1 bar équivaut à 7 à 8 % de surconsommation d’électricité. Sur l’année, cela peut représenter plusieurs milliers d’euros. Le pire ? Beaucoup d’entreprises n’en ont même pas conscience.
Prenons un exemple concret : un compresseur de 75 kW fonctionne 4000 heures par an. Si les filtres ne sont pas changés et que la perte de charge augmente de 1 bar, la surconsommation peut atteindre 8 %, soit :
75 kW × 0,08 × 4000 h = 24 000 kWh/an supplémentaires, soit environ 3600 € à 0,15 €/kWh. Et ce, pour un simple oubli de maintenance !
Voici un tableau synthétique des impacts directs d’un filtre colmaté sur la facture énergétique :
Type de filtre | Périmètre d’impact | Écart de consommation à perte de charge élevée | Coût annuel estimé (exemple réel) |
---|---|---|---|
Filtre à air comprimé coalescent | Réseau de compresseurs industriels | +7 à 12 % selon le niveau de colmatage | +2500 à 5000 €/an par compresseur |
Filtre de soufflage en ventilation | CVC de site ou tunnel | +10 % sur la consommation des ventilateurs | +1500 €/an pour un moteur 15 kW |
Filtre hydraulique | Circuit d’huile industrielle | +5 à 8 % sur les pompes | +1800 €/an pour 2 pompes de 11 kW |
Filtre de tour de refroidissement | Eau ou glycol en circuit fermé | Sur-régime de pompes + déperdition thermique | +8 à 10 % sur la facture globale |
⚠️ Astuces pratiques :
- Installer un manomètre différentiel ou un capteur ΔP sur les filtres stratégiques.
- Intégrer les seuils de ΔP dans votre GMAO ou automate.
- Programmer les remplacements non pas « à date », mais en fonction de la perte de charge réelle mesurée.
Le monde industriel de demain sera sobre, intelligent, et orienté écoconception. Cela implique de penser la filtration non plus comme un poste de dépense, mais comme un levier d’optimisation énergétique et de performance durable. C’est ici qu’intervient la notion de filtration écoconçue : des filtres pensés pour durer, à médias recyclables, à faible perte de charge initiale, compatibles avec des indicateurs connectés, et intégrés dans une boucle vertueuse.
Des fabricants innovent dans cette direction : géométries de média optimisées, plis profonds pour maximiser la surface utile, matériaux biosourcés ou composites allégés, filtres auto-nettoyants, capsules intégrées à lecture RFID ou NFC pour suivi digitalisé… L’écoconception, ce n’est pas seulement « vert », c’est intelligent, mesurable et rentable.
Voici un tableau des solutions écoconçues et leurs bénéfices directs :
Innovation d’écoconception | Bénéfices techniques | Avantage énergétique / économique |
---|---|---|
Média filtrant en nanofibres | Faible perte de charge initiale | Moins d’énergie pour maintenir le débit |
Filtre auto-nettoyant à impulsion | Pas de colmatage, cycle de vie prolongé | Moins de remplacements, moins de déchets |
Filtres avec indicateur ΔP intégré | Maintenance à l’état réel | Pas de remplacement anticipé inutile |
Capsules RFID/NFC intégrées | Suivi automatisé du cycle de vie | Optimisation de la rotation des stocks |
Matériaux recyclables / réutilisables | Réduction de l’empreinte carbone | Moins de déchets, image RSE valorisée |
🌿 Bon à savoir : Dans certaines industries agroalimentaires ou pharmaceutiques, une perte de charge réduite sur les réseaux de filtration d’air HEPA permet de baisser la consommation des CTA de 20 à 30 %, tout en maintenant les classes de propreté ISO.
En résumé, dans une logique d’excellence opérationnelle, de réduction de l’empreinte énergétique, et de systèmes intelligents, la filtration ne doit plus être le maillon négligé de la chaîne industrielle. Elle est au contraire un multiplicateur de performance. Bien conçue, bien dimensionnée, bien surveillée, elle peut faire économiser des milliers d’euros par an, tout en améliorant la durabilité de vos équipements, la sécurité de vos installations, et l’efficacité de vos processus.
Un filtre, ce n’est pas juste un consommable : c’est une barrière intelligente, une pièce d’ingénierie, un révélateur de l’état de votre installation, et un acteur stratégique de votre politique énergétique. Le négliger, c’est payer la facture – en énergie, en pannes, et en non-conformité.
💡 Dernier conseil d’ingénieur : pensez à intégrer vos filtres critiques dans un bilan énergétique global d’atelier ou d’unité. Vous serez surpris de voir combien ils peuvent peser. Et si vous ne les voyez pas… c’est peut-être déjà trop tard.
En somme, l’ingénierie des fluides industriels est une discipline importante et diversifiée qui joue un rôle clé dans de nombreuses industries. Elle nécessite une expertise technique et une connaissance approfondie des systèmes de circulation des fluides, de la thermodynamique, de la mécanique des fluides, de la régulation et du contrôle des processus, ainsi que de la sécurité.
Notre blog est une ressource complète pour tout ce qui concerne les fluides industriels. Nous vous encourageons à explorer nos articles, nos guides pratiques et nos ressources de formation pour approfondir vos connaissances et améliorer vos performances énergétiques. N’hésitez pas à nous contacter pour bénéficier de nos services d’ingénierie personnalisés ou pour trouver les produits dont vous avez besoin via notre site de commerce en ligne. Ensemble, nous pouvons aller plus loin dans l’apprentissage et réaliser des économies d’énergie significatives. Contactez-nous dès aujourd’hui à l’adresse suivante :
Lien : Tuyauteries et Flexibles
Lien : Electricité et électricité industrielle
Lien: Robinetterie et tuyauterie
Lien : Échangeurs et transferts thermiques
Lien : Eau surchauffe (industrie et génie climatique)
Lien : Hydraulique et Graissage
Lien :Mesures Physique et appareils de mesures
Lien : Les sondes de mesure de température
Lien : outils de mesures (thermomètre, manomètres,…)
Lien : Matériaux en industrie (galva, acier, inox …)
Lien : Eau – filtration et traitement
Lien : Gazs réfrigérants (frigorifiques)
Lien : Filetages et taraudages
Lien : Unités de mesure et conversion
Lien: R.I.A. (Réseau Incendie Armé)
Lien : ATEX (Atmosphères Explosibles)
Lien : Agitation dans les Fluides Industriels
Lien : Le Chauffage Industriel : Un Processus Complexifié
Lien : L’Eau Glacée en Génie Climatique
Lien : Réaliser un Bilan Thermique en Génie Climatique
Lien : L’Isolation en Génie Climatique
Lien : Les Méthodes de Soudure et de Brasage : Comment Faire le Bon Choix »
Lien : Fixations Industrielles : La Clé de la Solidité et de la Sécurité
Lien : Les E.P.I. (Equipements de Protections Individuels)
0ien : Les E.P.C. (Equipements de Protection Collectifs)
Lien : Principaux de transfert thermique : la conduction, la convection et le rayonnement
Lien pour achats :