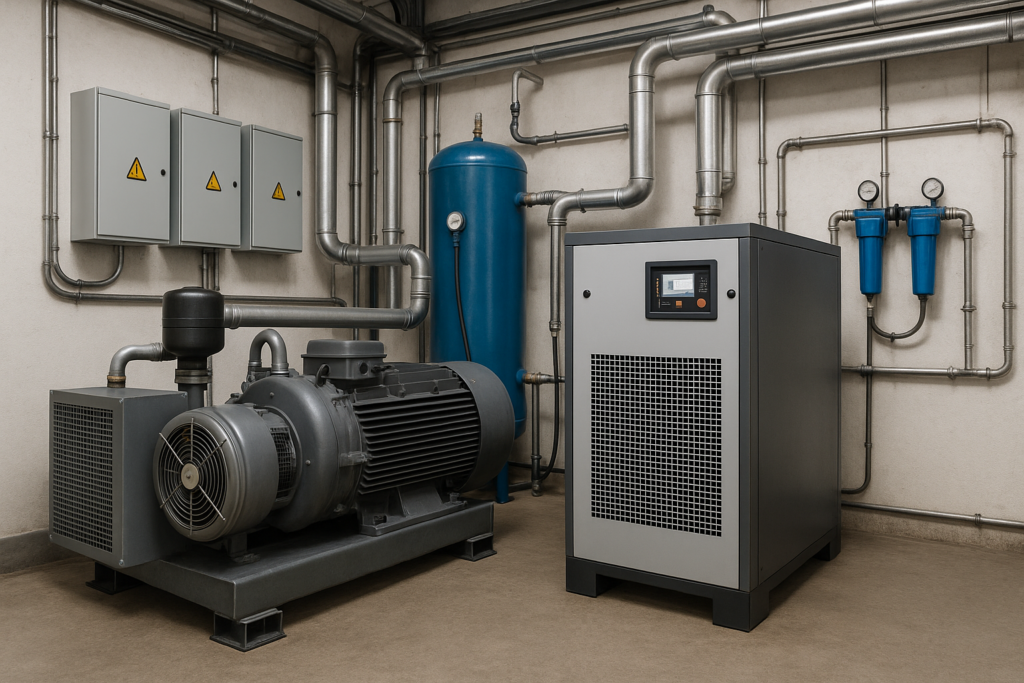
L’air comprimé est souvent qualifié de quatrième fluide industriel, au même titre que l’électricité, l’eau ou la vapeur. Mais contrairement aux apparences, cet air n’est jamais « sec » à la sortie du compresseur : il contient de l’eau sous forme de vapeur, voire sous forme liquide. Or, l’humidité dans un réseau d’air comprimé est une ennemie silencieuse : corrosion des tuyaux, perturbation des équipements pneumatiques, dégradation des instruments de mesure, pollution des produits finis…
C’est pourquoi l’usage d’un sécheur d’air comprimé est indispensable dans la majorité des applications industrielles. Mais attention : un sécheur mal dimensionné peut être aussi néfaste qu’un sécheur absent. Il en résulte une usure prématurée, une consommation énergétique excessive, une inefficacité de traitement, et des pertes de performance globales.
Cet article vous propose une analyse complète sur le bon dimensionnement des sécheurs d’air comprimé, en fonction des plages de charge (<70 %, 90 %, 100 %, 120 %, 150 %+), du type de technologie (réfrigération ou adsorption), de la température ambiante, de l’hygrométrie, et de l’adaptation à la dynamique de production.
1. Pourquoi sécher l’air comprimé ?
L’air atmosphérique contient entre 1 et 40 g/m³ d’eau, selon la température et l’humidité relative. Lorsqu’il est comprimé, la vapeur d’eau contenue dans l’air se condense. Si elle n’est pas éliminée :
- Elle crée de la rouille dans les tuyauteries métalliques
- Elle colmate les filtres
- Elle endommage les vérins et vannes pneumatiques
- Elle est incompatible avec les procédés alimentaires, électroniques, pharmaceutiques…
🎯 Objectif : réduire le point de rosée de l’air comprimé (par exemple à +3 °C pour un sécheur frigorifique, ou à -40 °C pour un sécheur par adsorption).
2. Les types de sécheurs d’air comprimé
🔹 Sécheurs à réfrigération
- Refroidissent l’air comprimé à env. 3 °C pour faire condenser l’eau
- Moins coûteux
- Point de rosée +3 °C (classe 4 selon ISO 8573-1)
- Consommation électrique modérée
❗ À éviter dans les environnements trop froids (risque de givre) ou avec des exigences de point de rosée très bas.
🔹 Sécheurs à adsorption
- Utilisent un matériau déshydratant (zéolite, alumine) pour capturer la vapeur d’eau
- Point de rosée jusqu’à -40 °C ou -70 °C (classe 2 à 1)
- Plus énergivores (chauffage ou purge d’air pour régénération)
- Indispensables pour les industries sensibles
3. Dimensionnement : quels paramètres à considérer ?
Le dimensionnement d’un sécheur dépend :
- Du débit maximal d’air comprimé (m³/h ou l/min)
- De la pression de service (bar)
- De la température d’entrée d’air
- De la température ambiante
- Du point de rosée souhaité
- De la technologie utilisée
- De la variabilité de la demande
- Du taux de charge sur 24h
💡 Astuce : toujours prendre une température d’entrée de l’air > température ambiante + 10 °C, pour compenser les pics de chaleur en été.
4. Conséquences d’un sous-dimensionnement (< 70 à 90 %)
🔴 Usure prématurée du sécheur
- Fonctionnement en surcharge thermique
- Le fluide frigorigène ou le matériau déshydratant sature plus rapidement
- Augmentation de la fréquence des cycles → vieillissement accéléré
🔴 Séchage inefficace
- Point de rosée non atteint
- Humidité résiduelle dans le réseau
- Contamination des équipements sensibles
🔴 Pannes en chaîne
- Formation d’eau dans les tuyauteries
- Colmatage des filtres
- Dysfonctionnements aléatoires sur les machines
- Multiplication des arrêts non planifiés
⚠️ Même un écart de 10 % sur le débit peut dégrader l’efficacité de séchage de plus de 20 %.
5. Dimensionnement idéal (100 % à 110 %)
✅ Rendement optimal
- Le sécheur travaille à son point de fonctionnement nominal
- Le COP (coefficient de performance) est maximisé
- La régulation thermique est fluide
✅ Durée de vie allongée
- Moins de cycles
- Moins de sollicitations mécaniques et thermiques
- Moins de maintenance curative
✅ Efficacité constante
- Point de rosée stable
- Adaptation possible aux petits pics de charge
- Faible risque de dérive même en été
✅ Recommandation ingénieur : dimensionner pour 100 à 110 % de la charge nominale + marge climatique, avec une réserve de sécurité intelligente.
6. Surdimensionnement (120 % à 150 % et plus) : erreurs fréquentes
🟡 Surchauffe en charge faible
Les sécheurs, notamment à réfrigération, n’aiment pas fonctionner à vide :
- Cycles de marche/arrêt fréquents
- Condensation dans les échangeurs
- Mauvaise stabilisation du point de rosée
🟡 Consommation électrique inutile
Un sécheur surdimensionné consomme plus d’électricité :
- Plus de fluide à pomper ou chauffer
- Inertie thermique accrue
- Usure prématurée des composants de régulation
🟡 Coût d’investissement injustifié
- Appareil plus cher (jusqu’à +50 %)
- Surface au sol plus grande
- Temps d’amortissement allongé
❌ Trop de marge = moins de performance, contrairement aux idées reçues.
7. En cas de pics momentanés de production
⚡ Mauvaise stratégie : surdimensionner en permanence
Vous risquez :
- Un fonctionnement inefficace la majorité du temps
- Une régulation instable
- Des arrêts intempestifs
✅ Bonne stratégie : ajouter une inertie tampon
- Ballon de stockage d’air comprimé après séchage
- Sécheur en mode adaptatif ou dual mode
- Ou deux sécheurs en parallèle (avec alternance en cascade)
8. Effets du climat : canicule, hygrométrie
☀️ Haute température ambiante (> 35 °C)
- Réduction des performances des sécheurs frigorifiques
- Risque de surpression du circuit de réfrigération
- Baisse de rendement : jusqu’à -20 %
💧 Hygrométrie forte (> 75 %)
- Entrée d’air plus saturée → plus de condensation
- Le sécheur doit travailler plus fort pour atteindre le même point de rosée
- Saturation rapide du média adsorbant ou du séparateur
⚠️ Toujours vérifier les correction factors fournis par le fabricant pour adapter la puissance à la température d’entrée et l’humidité.
9. Impacts électriques et mécaniques
🔌 Pics d’intensité au redémarrage
Un sécheur à réfrigération qui fonctionne par cycles courts :
- Subit des appels de courant fréquents
- Augmente la puissance réactive
- Use les relais, contacteurs, compresseurs de froid
🔧 Usure des composants internes
- Vannes, purgeurs, échangeurs, sondes, régulateurs… sont dimensionnés pour un régime nominal
- Trop de cycles → dégradation prématurée
- Maintenance anticipée
10. Astuces et bonnes pratiques pour un bon dimensionnement
✅ Analyser la charge réelle sur 7 à 30 jours
Via capteurs IoT ou superviseur, pour capter la variabilité de la demande
✅ Prévoir une régulation intelligente
Sécheurs à modulation de débit, à pilotage externe ou hybride froid/adsorption
✅ Intégrer les conditions extrêmes
Été / hiver, salle fermée ou ventilée, air pollué ou huileux
✅ Adapter le réseau en aval
Une mauvaise pente ou des tuyaux non purgés peuvent ruiner l’efficacité du sécheur
✅ Maintenance régulière et prédictive
Remplacement périodique du média adsorbant ou du fluide, test du point de rosée
✅ Respecter les classes ISO 8573-1
Classe 4 ou 5 pour applications générales, classe 2 pour machines sensibles, classe 1 pour industries critiques
Le bon séchage commence par un bon dimensionnement
Le sécheur d’air comprimé, trop souvent perçu comme un simple « accessoire », est en réalité un organe vital du réseau de fluides industriels. Son bon dimensionnement permet :
- D’éviter des pannes en cascade
- D’assurer la qualité de l’air comprimé
- De réduire la consommation énergétique
- D’allonger la durée de vie du compresseur et des équipements en aval
Un sécheur bien dimensionné, c’est un sécheur qui travaille efficacement, silencieusement, et sans surprise, été comme hiver.
Bien Dimensionner un Sécheur d’Air Comprimé : Clé de Performance, d’Économie et de Fiabilité Industrielle
🧭
- L’air comprimé : un fluide stratégique mais naturellement humide
- L’humidité, ennemie silencieuse de la performance industrielle
- Pourquoi un sécheur mal dimensionné est plus risqué qu’un sécheur absent
- Objectif du guide : maîtriser le dimensionnement, éviter les surcoûts, garantir la fiabilité
🔍 I. COMPRENDRE LE RÔLE DU SÉCHEUR D’AIR COMPRIMÉ
- Objectif : abaisser le point de rosée de l’air comprimé
- Effets de l’humidité non traitée sur :
- Réseaux de tuyauterie (corrosion)
- Outils pneumatiques (grippage)
- Process sensibles (alimentation, électronique, pharmacie…)
- Typologies de sécheurs :
- À réfrigération : simple, efficace, pour point de rosée +3 °C
- À adsorption : pour exigences sévères, -40 °C à -70 °C
- Norme ISO 8573-1 : comprendre les classes de pureté (eau)
⚙️ II. VARIABLES CLÉS POUR LE DIMENSIONNEMENT
- Débit d’air comprimé (m³/h ou l/min) à traiter
- Pression de service (effet sur volume et température)
- Température d’entrée de l’air (en sortie de compresseur)
- Température ambiante (locale technique ou extérieure)
- Humidité relative ambiante (hygrométrie saisonnière)
- Point de rosée requis selon l’application
- Facteurs de correction fabricant à intégrer (T°, HR, pression)
- Marge de sécurité : comment la définir intelligemment
📉 III. DIMENSIONNEMENT INSUFFISANT (< 70 %)
- Sécheur toujours en surcharge → fonctionnement instable
- Point de rosée non atteint → humidité résiduelle
- Saturation des échangeurs ou du dessicant
- Risques sur l’ensemble du réseau : corrosion, fuites, contamination
- Accélération de l’usure interne : compresseur, filtres, purges
- Surconsommation d’électricité (système à fond sans rendement)
- Arrêts imprévus ou défauts thermiques fréquents
- Impossibilité de réagir aux pics ou à la chaleur estivale
⚠️ IV. DIMENSIONNEMENT LÉGÈREMENT INSUFFISANT (≈ 90 %)
- Le système fonctionne… mais sans aucune marge
- Point de rosée instable selon la saison ou la charge
- Moins de fiabilité en cas de montée en température extérieure
- Usure accélérée par cycles courts / longues durées sous stress
- Inadapté aux environnements critiques (pharma, électronique)
✅ V. DIMENSIONNEMENT OPTIMAL (100 à 110 %)
- Meilleur rendement global du sécheur
- Fonctionnement à charge nominale = efficacité énergétique maximale
- Longévité des composants assurée (détendeur, échangeur, média déshydratant)
- Régulation stable = point de rosée maîtrisé
- Capacité à absorber des variations de débit modérées
- Moins de cycles de régulation → meilleure stabilité thermique
- Baisse du coût d’exploitation par m³ d’air sec
🟡 VI. SURDIMENSIONNEMENT MODÉRÉ (110 à 120 %)
- Risques de fonctionnement à vide ou sous-régime
- Comportement erratique : cycles courts, oscillations du point de rosée
- Augmentation du nombre de démarrages → usure électrique
- Réduction de la performance thermique globale
- Coût d’achat et d’installation inutilement plus élevé
- Perturbation de la régulation aval (purges, capteurs de T°/HR)
🔴 VII. SURDIMENSIONNEMENT EXCESSIF (≥ 150 %)
- Rendement énergétique dégradé (COP chuter drastiquement)
- Cycles de fonctionnement courts, incessants → stress thermique
- Risque de condensation interne (débit trop faible, pas assez chaud)
- Usure prématurée des éléments de régulation
- Problèmes de démarrage : pics d’intensité / redémarrages multiples
- Coût d’investissement surdimensionné + ROI défavorable
- Mauvaise compatibilité avec les sécheurs à adsorption (régénération excessive)
🔧 VIII. FONCTIONNEMENT EN MODE MARCHE/ARRÊT TROP FRÉQUENT
- Sécheur réfrigéré : compresseur frigorifique mis à rude épreuve
- Sécheur à adsorption : cycles de régénération accélérés
- Augmentation des appels de courant → surcharge tableau
- Usure mécanique des composants : contacteurs, ventilateurs, purgeurs
- Impact sur la stabilité du point de rosée
- Nuisances sonores accrues
⚡ IX. RÉPONSE AUX PICS MOMENTANÉS DE CONSOMMATION D’AIR
- Pourquoi une solution figée ne suffit jamais
- Limites du sécheur seul : inertie thermique et capacité instantanée
- Solutions techniques :
- Ballon d’air comprimé (tampon)
- Sécheur modulaire ou dual flow
- Groupes en parallèle avec pilotage séquentiel
- Régulation adaptative (via automates / capteurs)
- Anticiper les périodes critiques (redémarrage usine, montées en cadence)
🌡️ X. IMPACT DU CLIMAT SUR LES PERFORMANCES
A. Température ambiante élevée (canicule, locaux non ventilés)
- Chute du rendement de l’échangeur frigorifique
- Risque de surchauffe, déclenchements haute pression
- Moins de condensation → humidité résiduelle accrue
B. Hygrométrie forte
- Plus de vapeur à traiter = surcharge du sécheur
- Point de rosée plus difficile à atteindre
- Condensats en excès dans le réseau
C. Altitude ou locaux confinés
- Refroidissement difficile → besoin de surdimensionnement intelligent
- Altitude = baisse de densité de l’air → moins d’échange thermique
🔌 XI. CONSÉQUENCES ÉLECTRIQUES DU MAUVAIS DIMENSIONNEMENT
- Appels de courant élevés au démarrage
- Fonctionnement en surcharge → puissance active et réactive élevées
- Déséquilibre phase / neutre si mauvais câblage ou compresseur usé
- Détérioration de la qualité d’énergie dans l’atelier
- Influence sur les variateurs / onduleurs de la ligne
🧠 XII. ASTUCES, BONNES PRATIQUES ET CONSEILS D’INGÉNIEUR
- Analyser le profil réel de consommation d’air sur plusieurs jours
- Appliquer les facteurs de correction climatiques du fabricant
- Intégrer un ballon de stockage pour lisser les pics
- Toujours prévoir un préfiltrage efficace pour préserver le sécheur
- Prévoir de la maintenance préventive régulière (média, sondes, purgeurs)
- Choisir une régulation intelligente ou à variation de débit
- Penser à la modularité pour évoluer avec le besoin
- Vérifier le dimensionnement conjoint du compresseur + sécheur + filtration
📊 XIII. CAS PRATIQUES ET EXEMPLES CONCRETS
- Atelier mécanique sous-dimensionné en été
- Usine agroalimentaire avec exigences point de rosée -40 °C
- Ligne de production cyclique avec pics horaires
- Comparatif réel entre sécheur sous-dimensionné, bien dimensionné et surdimensionné
- Analyse énergétique sur 1 an
🏁
- Le sécheur d’air est un élément technique critique, pas un accessoire
- Bien dimensionner, c’est gagner en performance, en fiabilité et en énergie
- Ni trop petit, ni trop grand : la juste puissance pour un air comprimé toujours sec
- Anticiper les variations, les climats, les cycles, c’est penser industriel
- Le bon dimensionnement est le fruit de la mesure, de la méthode et de l’expérience
L’ingénierie au service de la sobriété et de la performance
Le dimensionnement des utilités de fluides process n’est pas un simple calcul de puissance. C’est une discipline d’ingénierie à part entière, où se croisent analyse de la demande, anticipation des aléas, maîtrise énergétique et choix techniques pertinents.
Il faut éviter deux pièges : l’économie court-termiste (sous-dimensionnement) et la surenchère sécuritaire (surdimensionnement coûteux). La justesse technique est la meilleure alliée de la performance économique, écologique et opérationnelle.
En somme, l’ingénierie des fluides industriels est une discipline importante et diversifiée qui joue un rôle clé dans de nombreuses industries. Elle nécessite une expertise technique et une connaissance approfondie des systèmes de circulation des fluides, de la thermodynamique, de la mécanique des fluides, de la régulation et du contrôle des processus, ainsi que de la sécurité.
Notre blog est une ressource complète pour tout ce qui concerne les fluides industriels. Nous vous encourageons à explorer nos articles, nos guides pratiques et nos ressources de formation pour approfondir vos connaissances et améliorer vos performances énergétiques. N’hésitez pas à nous contacter pour bénéficier de nos services d’ingénierie personnalisés ou pour trouver les produits dont vous avez besoin via notre site de commerce en ligne. Ensemble, nous pouvons aller plus loin dans l’apprentissage et réaliser des économies d’énergie significatives. Contactez-nous dès aujourd’hui à l’adresse suivante :
Lien : Tuyauteries et Flexibles
Lien : Electricité et électricité industrielle
Lien: Robinetterie et tuyauterie
Lien : Échangeurs et transferts thermiques
Lien : Eau surchauffe (industrie et génie climatique)
Lien : Hydraulique et Graissage
Lien :Mesures Physique et appareils de mesures
Lien : Les sondes de mesure de température
Lien : outils de mesures (thermomètre, manomètres,…)
Lien : Matériaux en industrie (galva, acier, inox …)
Lien : Eau – filtration et traitement
Lien : Gazs réfrigérants (frigorifiques)
Lien : Filetages et taraudages
Lien : Unités de mesure et conversion
Lien: R.I.A. (Réseau Incendie Armé)
Lien : ATEX (Atmosphères Explosibles)
Lien : Agitation dans les Fluides Industriels
Lien : Le Chauffage Industriel : Un Processus Complexifié
Lien : L’Eau Glacée en Génie Climatique
Lien : Réaliser un Bilan Thermique en Génie Climatique
Lien : L’Isolation en Génie Climatique
Lien : Les Méthodes de Soudure et de Brasage : Comment Faire le Bon Choix »
Lien : Fixations Industrielles : La Clé de la Solidité et de la Sécurité
Lien : Les E.P.I. (Equipements de Protections Individuels)
0ien : Les E.P.C. (Equipements de Protection Collectifs)
Lien : Principaux de transfert thermique : la conduction, la convection et le rayonnement
Lien : Le Cercle Vertueux en Industrie : L’Écologie au Cœur des Fluides Industriels
Lien : Courroies Trapézoïdales en Industrie : L’Art de Transmettre la Puissance avec Précision
Lien : Optimisation de la Stabilité Industrielle : Lutte Efficace Contre les Vibrations des Machines
- La Gestion des Pièces Détachées en Industrie : Obsolescence, Durée de Vie et Stockage
- L’Impact de la Nature de la Surface et de la Couleur : Bilan Thermique et Transfert de Chaleur
- Comprendre les Classes de Protection IP : Un Guide Technique
- L’Art de l’Ingénierie en Mesures Physiques Industrielles : Optimisation, Contrôle et Dimentionnement des Fluides Industriels
- Innovation et Durabilité : L’Ingénierie des Fluides Industriels au Service de l’Économie Verte
- L’Énigme des Fluides Industriels : Explorons l’Inclassable
- Optimisation Énergétique dans l’Industrie : Réduire les Coûts liés aux Fluides Industriels
- Solutions Sur Mesure en Électrovannes pour Projets Spécifiques : Une Expertise Unique
- Vannes Motorisées: Standard ou Sur Mesure, Trouvez la Solution Adaptée pour Votre Application
- Guide Complet des Vannes Pneumatiques : Personnalisation, Qualité et Expertise
- Découvrez la Révolution Pneumatique : Les Vérins Sur Mesure
- Optimisation Pneumatique : Explorez Notre Gamme de Moteurs Pneumatiques
- Comment choisir le bon matériau pour vos équipements industriels : Une approche personnalisée
- Optimisation Cruciale: Les Répercussions d’un Réseau Industriel Mal Équilibré sur la Performance et la Sécurité
- Démystification des Moteurs Électriques: Un Guide Complet des Types, Avantages et Inconvénients
- Comprendre les éléments constitutifs des machines spéciales : Un guide technique pour les ingénieurs et techniciens de maintenance
- Impact Environnemental des Fluides Industriels et des Méthodes de Production
- L’évolution des systèmes de maintenance et la gestion des équipements industriels
- L’Évolution des Technologies dans les Systèmes Industriels : Air Comprimé, Groupes Froids et au-delà
- L’Importance de la Formation Continue pour les Techniciens des Fluides Industriels
- Tolérances de Côtes et Rugosité en Mécanique : Précision et Qualité en Ingénierie
- Méthodes Statistiques et Échantillonnage : L’Art d’Anticiper les Dérives Industrielles (SPC, …)
- Maîtriser l’Art du Filtrage Industriel : Comment Choisir, Lire et Entretenir les Filtres pour Optimiser Performance, Énergie et Durabilité
Lien pour achats :