Auteur : BILLAUT Fabrice
Optimisation par Réglages Fins : Maximisez l’Efficacité de Votre Groupe Froid Industriel Sans Investissements Majeurs
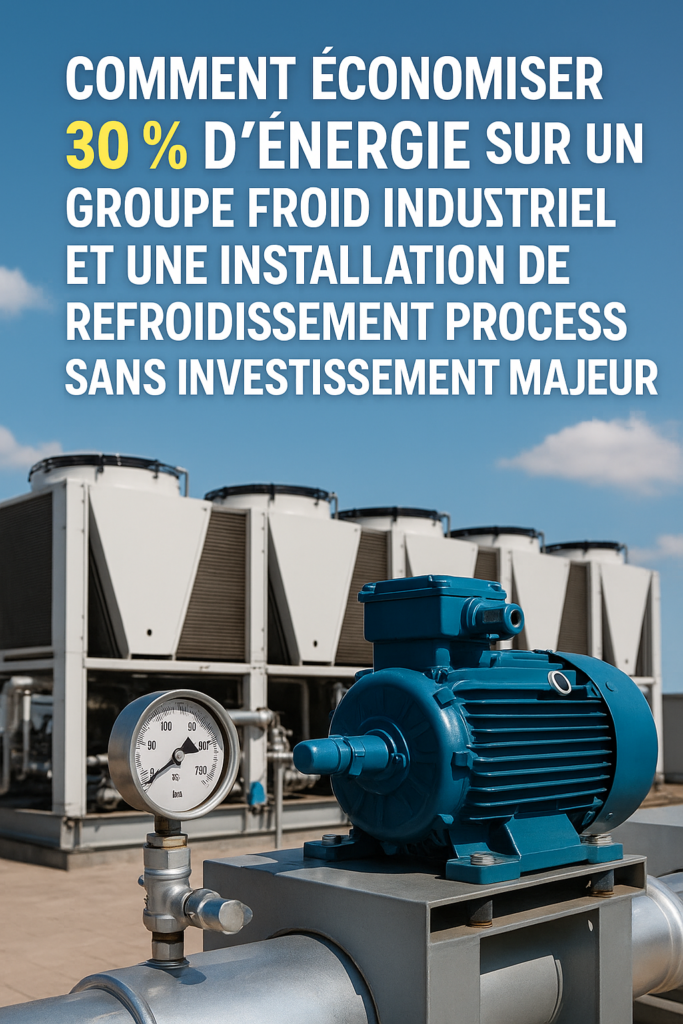
Dans un contexte où la maîtrise des coûts énergétiques est cruciale, optimiser l’efficacité des groupes froids industriels devient une priorité. Bonne nouvelle : des ajustements simples, sans investissements lourds, peuvent générer des économies significatives. Cet article explore trois leviers d’optimisation : la pression de condensation, la surchauffe et la pression d’évaporation.
1. Baisser la Pression de Condensation : La Clé des Économies Massives
Pourquoi c’est essentiel
La pression de condensation influence directement le travail du compresseur. Une pression élevée augmente la charge du compresseur, réduisant ainsi le Coefficient de Performance (COP) de l’installation. En abaissant cette pression, on diminue l’effort du compresseur, améliorant l’efficacité énergétique.
Astuce : Régler la Haute Pression en Fonction de la Température Ambiante
Mettre en place une régulation de la pression de condensation en fonction de la température extérieure permet d’ajuster automatiquement la pression à des niveaux optimaux. Ce système, appelé « haute pression flottante », adapte le fonctionnement du condenseur aux conditions ambiantes, réduisant ainsi la consommation énergétique.
Bon à Savoir : Limiter le Fonctionnement Continu des Ventilateurs
Les ventilateurs du condenseur consomment de l’énergie. En les régulant en fonction des besoins réels, on évite leur fonctionnement inutile, contribuant ainsi aux économies d’énergie.
2. Ajuster la Surchauffe au Plus Juste : Un Impact Direct sur le COP
Comprendre la Surchauffe
La surchauffe est la différence entre la température du fluide frigorigène en sortie de l’évaporateur et sa température de saturation. Une surchauffe adéquate garantit que seul du gaz entre dans le compresseur, évitant ainsi les risques de coups de liquide.
Effet sur le COP
Une surchauffe trop élevée réduit la capacité de l’évaporateur, tandis qu’une surchauffe trop faible peut endommager le compresseur. Un réglage précis de la surchauffe optimise le COP de l’installation.
Astuce : Contrôler et Ajuster la Surchauffe avec des Outils Simples
En utilisant un manomètre et un thermomètre, il est possible de mesurer la surchauffe et d’ajuster le détendeur en conséquence. Cette opération, bien que simple, nécessite une certaine expertise pour éviter les erreurs de réglage.
3. Abaisser Légèrement la Pression d’Évaporation : Un Gain Énergétique Substantiel
Le Principe
La pression d’évaporation détermine la température à laquelle le fluide frigorigène s’évapore dans l’évaporateur. En abaissant légèrement cette pression, on augmente la capacité de l’évaporateur, réduisant ainsi la charge du compresseur.
Attention aux Limites de Fonctionnement de l’Évaporateur
Une pression d’évaporation trop basse peut entraîner le gel de l’évaporateur, perturbant le fonctionnement de l’installation. Il est donc crucial de respecter les limites de fonctionnement spécifiées par le fabricant.
Optimiser un groupe froid industriel ne nécessite pas toujours des investissements importants. Des réglages fins, tels que l’ajustement de la pression de condensation, de la surchauffe et de la pression d’évaporation, peuvent améliorer significativement l’efficacité énergétique de l’installation. Ces actions, simples à mettre en œuvre, contribuent à réduire les coûts d’exploitation et à prolonger la durée de vie des équipements.
Note : Pour des recommandations spécifiques à votre installation, il est conseillé de consulter un professionnel qualifié.
En somme, l’ingénierie des fluides industriels est une discipline importante et diversifiée qui joue un rôle clé dans de nombreuses industries. Elle nécessite une expertise technique et une connaissance approfondie des systèmes de circulation des fluides, de la thermodynamique, de la mécanique des fluides, de la régulation et du contrôle des processus, ainsi que de la sécurité.
Notre blog est une ressource complète pour tout ce qui concerne les fluides industriels. Nous vous encourageons à explorer nos articles, nos guides pratiques et nos ressources de formation pour approfondir vos connaissances et améliorer vos performances énergétiques. N’hésitez pas à nous contacter pour bénéficier de nos services d’ingénierie personnalisés ou pour trouver les produits dont vous avez besoin via notre site de commerce en ligne. Ensemble, nous pouvons aller plus loin dans l’apprentissage et réaliser des économies d’énergie significatives. Contactez-nous dès aujourd’hui à l’adresse suivante :
- Guide pour choisir un groupe froid industriel
- Lien : Exemple de schémas d’installation
- Lien : Calcul de la puissance nécessaire et facteurs de corrections usuels
- Le Guide Ultime du Choix des Compresseurs Frigorifiques : Optimisation, Puissance et Régulation
- Installation optimale de groupes froids industriels : Pratiques essentielles et paramètres clés
- Guide : La mise en service initiale d’un groupe froid industriel
- Les Applications du Refroidissement Industriel dans Divers Secteurs
- Guide Pratique pour le Choix d’un Groupe Froid Industriel : Calculs, Installations, Méthodes, Besoins et Critères Essentiels
- Optimiser l’Efficacité Énergétique : Deux Méthodes Ingénieuses pour Récupérer la Chaleur d’un Groupe Froid Industriel
- Guide Pratique : Récupération de Chaleur sur Groupe Froid – Avantages et Mise en Œuvre
- Innovations et Stratégies Avancées dans le Refroidissement Industriel: Vers une Ère Durable et Efficace
- Optimisation Cruciale: Les Répercussions d’un Réseau Industriel Mal Équilibré sur la Performance et la Sécurité
- Optimisation du Dimensionnement des Tuyauteries : Préserver la Pression et Réduire les Pertes de Charge
- Calculs et dimensionnement, installation, optimisation et Maintenance des Groupes Froids Industriels : Guide Complet pour Calcul de Puissance, Facteurs de Correction, et Technologies de Contrôle
- La conception d’un système de refroidissement industriel (Industrial Cooling System)
- Révolutionner le Froid Industriel et le Refroidissement Process avec l’IoT et l’IA : Entre Solutions High Tech, Low Tech, et Approches Hybrides
- Optimiser le Refroidissement Process avec l’IoT et l’IA : Révolutions et Techniques pour les Groupes Froids et Groupes d’Eau Glacée Industriels
- Révolution Technologique des Groupes Froids Industriels et Groupes d’Eau Glacée : Quand l’IA et les IoT Façonnent l’Avenir du Refroidissement Industriel
- FAQ : Groupes Froids Industriels et au Refroidissement Process
- Questions / réponses fréquemment posées sur le thème du refroidissement de process, incluant l’eau glacée, le froid industriel, les groupes froids, et les groupes d’eau glacée
- Quelles sont les erreurs courantes à éviter lors du choix d’un groupe froid industriel pour le refroidissement de son process ?
- Refroidissement Industriel : L’Essentiel sur les Groupes Frigorifiques et les Groupes d’Eau Glacée
- Lien: Notions de base
- Lie0n : Fonctionnement des systèmes de réfrigération
- Lien : applications du froid industriel
- Lien : Avantages et inconvénients
- Lien : En conclusion, le froid industriel est un élément clé de nombreuses industries modernes
- Lien : mesure de débit ultrasonique
- Mesure de Débit d’Eau par Ultrasons : Optimisation des Process Industriels
- Lien : Vitesse des fluides dans les tuyauteries
- Pour réaliser des économies d’énergie avec les installations d’eau glacée (froid industriel)
- Lien : Retrouver la performance de vos échangeurs avec le peigne frigoriste (groupe froid industriel, sécheur air comprimé, …)
- Lien : Réfractomètre : Mesurez facilement la concentration en glycol essentielle pour assurer la sécurité et la performance des installations industrielles
- Lien : Analyse d’huile des équipements : Optimisez la maintenance industrielle (compresseur air comprimé, groupe froid industriel, …)
- Les avantages de la connectivité IoT et I.A. dans les groupes froids industriels : Comment tirer parti des données pour améliorer les performances
- Les tendances émergentes dans les groupes froids industriels : Les nouvelles technologies qui transforment l’industrie du refroidissement
- La sélection du groupe froid industriel adapté à vos besoins : Guide d’achat et recommandations pour une solution optimale
- La sécurité dans les groupes froids industriels : Conseils pour prévenir les accidents et assurer la conformité aux normes de sécurité
- Maximisez la fiabilité de votre groupe froid industriel : Les meilleures pratiques pour éviter les pannes et les temps d’arrêt coûteux
- La maintenance préventive des groupes froids industriels : Astuces pour prolonger la durée de vie de votre équipement
- Les solutions respectueuses de l’environnement pour les groupes froids industriels : Astuces pour réduire l’empreinte carbone de votre installation
- La gestion intelligente des groupes froids industriels : Comment utiliser les systèmes de contrôle avancés pour optimiser les performances
- Les dernières avancées en matière de groupes froids industriels : Les technologies innovantes qui améliorent les performances
- Groupe froid industriel : Optimisez les économies d’énergie en adaptant vos consignes de température
- Optimisez l’efficacité énergétique de votre groupe froid industriel : Astuces pratiques pour réduire la consommation d’énergie
- Maîtrisez la poussière : Astuces innovantes et simples pour protéger vos équipements avec des filtres d’air comprimé dans les environnements poussiéreu
Lien pour achats :
Comprendre les Bases du Fonctionnement Thermodynamique des Groupes Froids Industriels
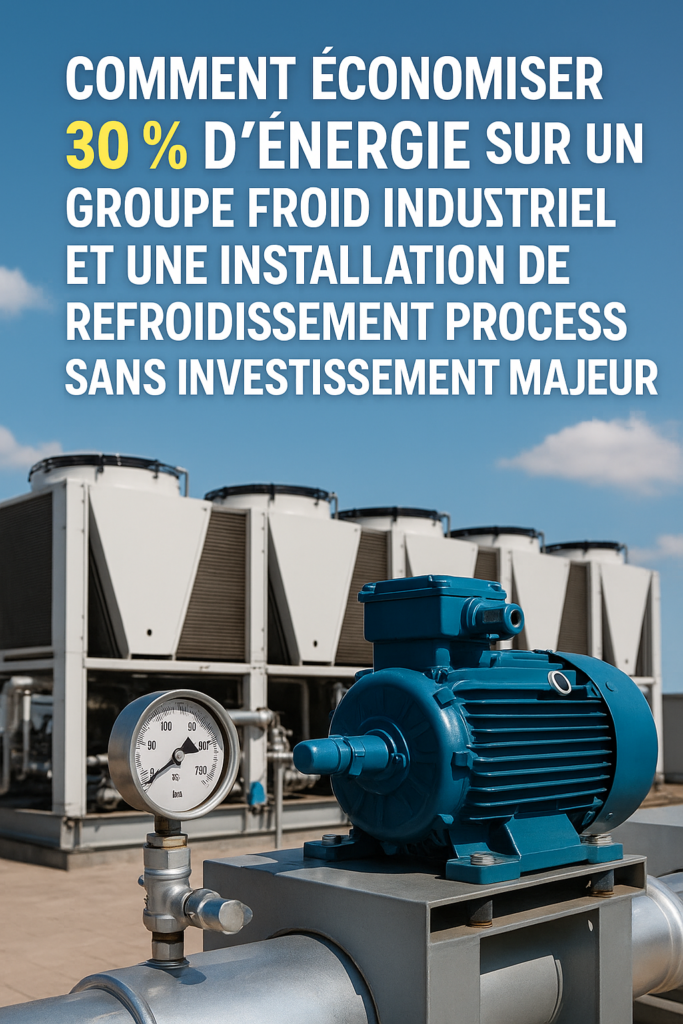
Dans le secteur industriel, la maîtrise du froid est essentielle pour garantir la qualité des produits, assurer la sécurité des processus et optimiser la consommation énergétique. Les groupes froids industriels, au cœur de cette maîtrise, fonctionnent selon des principes thermodynamiques précis. Comprendre ces principes permet non seulement d’améliorer l’efficacité énergétique, mais aussi de prévenir les surconsommations et les pannes coûteuses.
1. Le Cycle Thermodynamique du Groupe Froid Industriel
Un groupe froid industriel fonctionne selon un cycle thermodynamique en quatre étapes principales
1.1. Compression
Le fluide frigorigène, à l’état gazeux et à basse pression, est aspiré par le compresseur. Ce dernier augmente sa pression et sa température, le transformant en un gaz chaud et à haute pression.
1.2. Condensation
Le gaz chaud entre dans le condenseur, où il cède sa chaleur à un fluide caloporteur (air ou eau), se refroidissant ainsi et passant à l’état liquide.
1.3. Détente
Le liquide frigorigène traverse un détendeur, qui abaisse sa pression, provoquant une baisse de température
1.4. Évaporation
Le fluide à basse pression entre dans l’évaporateur, où il absorbe la chaleur du milieu à refroidir, s’évaporant ainsi et retournant à l’état gazeux. Le cycle recommence ensuite.
2. Le Coefficient de Performance (COP) : Un Indicateur Clé
Le Coefficient de Performance (COP) est un indicateur essentiel pour évaluer l’efficacité énergétique d’un groupe froid. Il se définit comme le rapport entre la puissance frigorifique produite et la puissance électrique consommée
COP = Puissance frigorifique / Puissance électrique consommée
Un COP élevé indique une meilleure efficacité énergétique. Par exemple, un COP de 4 signifie que pour chaque kilowattheure d’électricité consommée, le système produit 4 kilowattheures de froid.
3. Les Zones Critiques de Surconsommation
Certaines anomalies ou dysfonctionnements peuvent entraîner une surconsommation énergétique significative. Voici les principales zones critiques à surveiller :
3.1. Excès de Pression de Condensation
Une pression de condensation trop élevée peut résulter d’un encrassement du condenseur, d’une température ambiante élevée ou d’un débit d’air insuffisant. Cela augmente la charge du compresseur et réduit le COP.
3.2. Mauvaise Surchauffe ou Sous-refroidissement
Une surchauffe excessive peut indiquer un manque de fluide frigorigène ou un détendeur mal réglé, tandis qu’un sous-refroidissement insuffisant peut être le signe d’un condenseur encrassé. Ces conditions affectent l’efficacité du cycle frigorifique.
3.3. Encrassements Internes Invisibles
Des dépôts ou des obstructions internes dans les échangeurs ou les conduites peuvent réduire les échanges thermiques, augmentant ainsi la consommation énergétique. Un entretien régulier est essentiel pour prévenir ces problèmes.
4. Astuces pour Optimiser l’Efficacité Énergétique
- Entretien Régulier : Nettoyer les échangeurs, vérifier l’étanchéité du circuit et remplacer les filtres pour maintenir une performance optimale.
- Surveillance des Paramètres : Utiliser des instruments de mesure pour surveiller la pression, la température et le débit, permettant de détecter rapidement les anomalies.
- Formation du Personnel : Former les techniciens et opérateurs aux bonnes pratiques d’exploitation et de maintenance pour prévenir les dysfonctionnements.
- Utilisation de Technologies Avancées : Intégrer des systèmes de contrôle automatisés pour ajuster les paramètres en temps réel en fonction des besoins.
Comprendre le fonctionnement thermodynamique des groupes froids industriels est essentiel pour optimiser leur efficacité énergétique, réduire les coûts d’exploitation et prolonger la durée de vie des équipements. En surveillant les zones critiques de surconsommation et en adoptant des pratiques d’entretien rigoureuses, les entreprises peuvent réaliser des économies significatives tout en assurant la qualité et la sécurité de leurs processus industriels.
Note : Pour des recommandations spécifiques à votre installation, il est conseillé de consulter un professionnel qualifié.
En somme, l’ingénierie des fluides industriels est une discipline importante et diversifiée qui joue un rôle clé dans de nombreuses industries. Elle nécessite une expertise technique et une connaissance approfondie des systèmes de circulation des fluides, de la thermodynamique, de la mécanique des fluides, de la régulation et du contrôle des processus, ainsi que de la sécurité.
Notre blog est une ressource complète pour tout ce qui concerne les fluides industriels. Nous vous encourageons à explorer nos articles, nos guides pratiques et nos ressources de formation pour approfondir vos connaissances et améliorer vos performances énergétiques. N’hésitez pas à nous contacter pour bénéficier de nos services d’ingénierie personnalisés ou pour trouver les produits dont vous avez besoin via notre site de commerce en ligne. Ensemble, nous pouvons aller plus loin dans l’apprentissage et réaliser des économies d’énergie significatives. Contactez-nous dès aujourd’hui à l’adresse suivante :
- Guide pour choisir un groupe froid industriel
- Lien : Exemple de schémas d’installation
- Lien : Calcul de la puissance nécessaire et facteurs de corrections usuels
- Le Guide Ultime du Choix des Compresseurs Frigorifiques : Optimisation, Puissance et Régulation
- Installation optimale de groupes froids industriels : Pratiques essentielles et paramètres clés
- Guide : La mise en service initiale d’un groupe froid industriel
- Les Applications du Refroidissement Industriel dans Divers Secteurs
- Guide Pratique pour le Choix d’un Groupe Froid Industriel : Calculs, Installations, Méthodes, Besoins et Critères Essentiels
- Optimiser l’Efficacité Énergétique : Deux Méthodes Ingénieuses pour Récupérer la Chaleur d’un Groupe Froid Industriel
- Guide Pratique : Récupération de Chaleur sur Groupe Froid – Avantages et Mise en Œuvre
- Innovations et Stratégies Avancées dans le Refroidissement Industriel: Vers une Ère Durable et Efficace
- Optimisation Cruciale: Les Répercussions d’un Réseau Industriel Mal Équilibré sur la Performance et la Sécurité
- Optimisation du Dimensionnement des Tuyauteries : Préserver la Pression et Réduire les Pertes de Charge
- Calculs et dimensionnement, installation, optimisation et Maintenance des Groupes Froids Industriels : Guide Complet pour Calcul de Puissance, Facteurs de Correction, et Technologies de Contrôle
- La conception d’un système de refroidissement industriel (Industrial Cooling System)
- Révolutionner le Froid Industriel et le Refroidissement Process avec l’IoT et l’IA : Entre Solutions High Tech, Low Tech, et Approches Hybrides
- Optimiser le Refroidissement Process avec l’IoT et l’IA : Révolutions et Techniques pour les Groupes Froids et Groupes d’Eau Glacée Industriels
- Révolution Technologique des Groupes Froids Industriels et Groupes d’Eau Glacée : Quand l’IA et les IoT Façonnent l’Avenir du Refroidissement Industriel
- FAQ : Groupes Froids Industriels et au Refroidissement Process
- Questions / réponses fréquemment posées sur le thème du refroidissement de process, incluant l’eau glacée, le froid industriel, les groupes froids, et les groupes d’eau glacée
- Quelles sont les erreurs courantes à éviter lors du choix d’un groupe froid industriel pour le refroidissement de son process ?
- Refroidissement Industriel : L’Essentiel sur les Groupes Frigorifiques et les Groupes d’Eau Glacée
- Lien: Notions de base
- Lie0n : Fonctionnement des systèmes de réfrigération
- Lien : applications du froid industriel
- Lien : Avantages et inconvénients
- Lien : En conclusion, le froid industriel est un élément clé de nombreuses industries modernes
- Lien : mesure de débit ultrasonique
- Mesure de Débit d’Eau par Ultrasons : Optimisation des Process Industriels
- Lien : Vitesse des fluides dans les tuyauteries
- Pour réaliser des économies d’énergie avec les installations d’eau glacée (froid industriel)
- Lien : Retrouver la performance de vos échangeurs avec le peigne frigoriste (groupe froid industriel, sécheur air comprimé, …)
- Lien : Réfractomètre : Mesurez facilement la concentration en glycol essentielle pour assurer la sécurité et la performance des installations industrielles
- Lien : Analyse d’huile des équipements : Optimisez la maintenance industrielle (compresseur air comprimé, groupe froid industriel, …)
- Les avantages de la connectivité IoT et I.A. dans les groupes froids industriels : Comment tirer parti des données pour améliorer les performances
- Les tendances émergentes dans les groupes froids industriels : Les nouvelles technologies qui transforment l’industrie du refroidissement
- La sélection du groupe froid industriel adapté à vos besoins : Guide d’achat et recommandations pour une solution optimale
- La sécurité dans les groupes froids industriels : Conseils pour prévenir les accidents et assurer la conformité aux normes de sécurité
- Maximisez la fiabilité de votre groupe froid industriel : Les meilleures pratiques pour éviter les pannes et les temps d’arrêt coûteux
- La maintenance préventive des groupes froids industriels : Astuces pour prolonger la durée de vie de votre équipement
- Les solutions respectueuses de l’environnement pour les groupes froids industriels : Astuces pour réduire l’empreinte carbone de votre installation
- La gestion intelligente des groupes froids industriels : Comment utiliser les systèmes de contrôle avancés pour optimiser les performances
- Les dernières avancées en matière de groupes froids industriels : Les technologies innovantes qui améliorent les performances
- Groupe froid industriel : Optimisez les économies d’énergie en adaptant vos consignes de température
- Optimisez l’efficacité énergétique de votre groupe froid industriel : Astuces pratiques pour réduire la consommation d’énergie
- Maîtrisez la poussière : Astuces innovantes et simples pour protéger vos équipements avec des filtres d’air comprimé dans les environnements poussiéreu
Lien pour achats :
Pourquoi Chaque Kilowatt Compte ? L’Impact Direct du Coût Énergétique sur les Groupes Froids Industriels
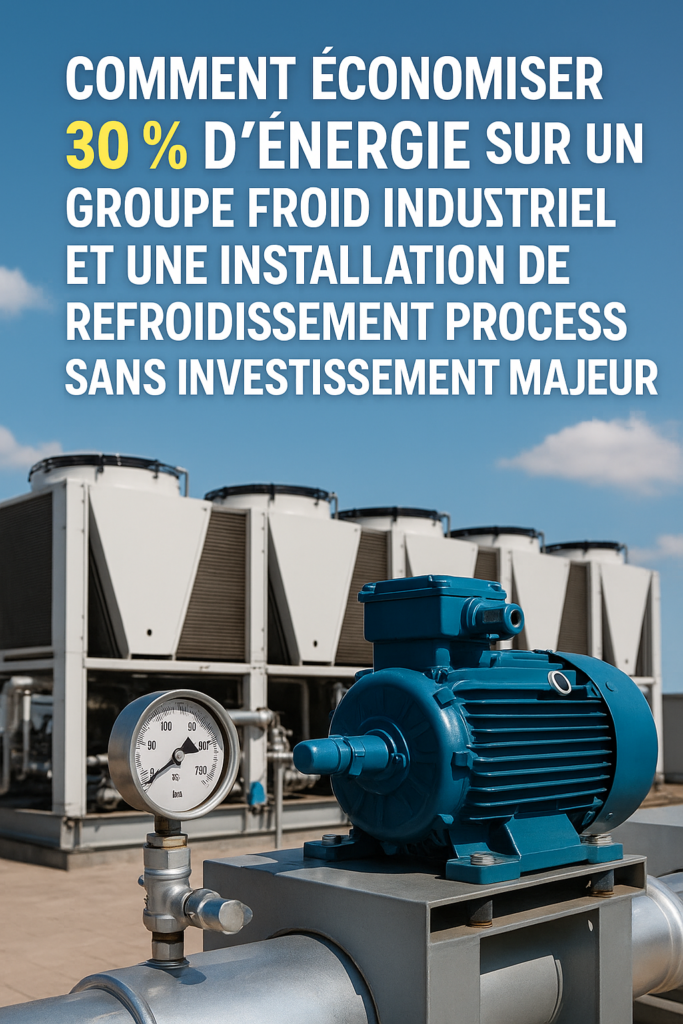
Dans un contexte où la maîtrise des coûts énergétiques et la réduction de l’empreinte carbone sont devenues des priorités, optimiser l’efficacité énergétique des groupes froids industriels est essentiel. Bonne nouvelle : il est possible d’obtenir des résultats significatifs sans investissements lourds. En agissant sur les réglages, la maintenance et en impliquant les équipes, des économies d’énergie allant jusqu’à 30 % peuvent être réalisées, tout en prolongeant la durée de vie des équipements.
1. Le Poids Énergétique du Froid Industriel
1.1. Une Consommation Énergétique Considérable
Le froid industriel représente une part significative de la consommation énergétique dans de nombreux secteurs industriels. Par exemple, dans l’industrie agroalimentaire, la production de froid peut représenter jusqu’à 50 % de la consommation électrique d’un site . Cette consommation élevée se traduit par des coûts énergétiques importants, impactant directement la rentabilité des entreprises.
1.2. Impact sur la Productivité
Un système de refroidissement efficace est essentiel pour maintenir la qualité des produits et assurer la continuité des processus de production. Des fluctuations de température ou des pannes peuvent entraîner des arrêts de production, des pertes de produits et des coûts supplémentaires. Ainsi, l’efficacité énergétique des groupes froids influence directement la productivité industrielle.
2. Objectif : 20 % à 30 % d’Économies Sans Changer Tout l’Équipement
2.1. Optimisation des Réglages
Ajuster les consignes de température, réguler la pression de condensation en fonction des conditions extérieures et optimiser la séquence des compresseurs sont des actions simples qui peuvent améliorer l’efficacité énergétique sans nécessiter de nouveaux investissements.
2.2. Maintenance Préventive
Un entretien régulier, incluant le nettoyage des échangeurs, la vérification de l’étanchéité et le contrôle des niveaux de fluide frigorigène, permet de maintenir les performances des équipements et d’éviter les surconsommations d’énergie.
2.3. Formation et Implication des Équipes
Former les techniciens et opérateurs aux bonnes pratiques d’exploitation et de maintenance favorise l’adoption de comportements éco-responsables et permet d’identifier rapidement les anomalies.
3. Astuces Techniques et Bonnes Pratiques
3.1. Utilisation de Ventilateurs à Vitesse Variable
Adapter la vitesse des ventilateurs en fonction des besoins permet de réduire la consommation énergétique et d’améliorer le confort thermique.
3.2. Récupération de Chaleur
Valoriser la chaleur fatale issue du processus de refroidissement pour d’autres usages, comme le chauffage de locaux ou la production d’eau chaude, contribue à réduire la consommation énergétique globale.
3.3. Surveillance des Températures de Refoulement
Des températures élevées peuvent indiquer la présence d’incondensables, affectant l’efficacité du système. Une surveillance régulière permet de détecter et de corriger ces anomalies.
4. Bon à Savoir
- Facture Énergétique : Une canalisation d’eau glacée non isolée de 10 mètres peut coûter jusqu’à 500 €/an en pertes thermiques.
- Impact Carbone : Chaque kilowattheure économisé réduit l’empreinte carbone de l’entreprise, contribuant à ses objectifs de développement durable.
- Aides Financières : Des dispositifs tels que les Certificats d’Économies d’Énergie (CEE) peuvent soutenir les projets d’amélioration de l’efficacité énergétique.
Optimiser l’efficacité énergétique des groupes froids industriels est une démarche rentable et accessible. En mettant en œuvre des actions simples et en impliquant les équipes, il est possible de réaliser des économies significatives, d’améliorer la productivité et de réduire l’empreinte carbone de l’entreprise. Chaque kilowatt compte, et les bénéfices sont multiples : pour l’entreprise, pour la planète et pour les générations futures.
Note : Pour des recommandations spécifiques à votre installation, il est conseillé de consulter un professionnel qualifié.
En somme, l’ingénierie des fluides industriels est une discipline importante et diversifiée qui joue un rôle clé dans de nombreuses industries. Elle nécessite une expertise technique et une connaissance approfondie des systèmes de circulation des fluides, de la thermodynamique, de la mécanique des fluides, de la régulation et du contrôle des processus, ainsi que de la sécurité.
Notre blog est une ressource complète pour tout ce qui concerne les fluides industriels. Nous vous encourageons à explorer nos articles, nos guides pratiques et nos ressources de formation pour approfondir vos connaissances et améliorer vos performances énergétiques. N’hésitez pas à nous contacter pour bénéficier de nos services d’ingénierie personnalisés ou pour trouver les produits dont vous avez besoin via notre site de commerce en ligne. Ensemble, nous pouvons aller plus loin dans l’apprentissage et réaliser des économies d’énergie significatives. Contactez-nous dès aujourd’hui à l’adresse suivante :
- Guide pour choisir un groupe froid industriel
- Lien : Exemple de schémas d’installation
- Lien : Calcul de la puissance nécessaire et facteurs de corrections usuels
- Le Guide Ultime du Choix des Compresseurs Frigorifiques : Optimisation, Puissance et Régulation
- Installation optimale de groupes froids industriels : Pratiques essentielles et paramètres clés
- Guide : La mise en service initiale d’un groupe froid industriel
- Les Applications du Refroidissement Industriel dans Divers Secteurs
- Guide Pratique pour le Choix d’un Groupe Froid Industriel : Calculs, Installations, Méthodes, Besoins et Critères Essentiels
- Optimiser l’Efficacité Énergétique : Deux Méthodes Ingénieuses pour Récupérer la Chaleur d’un Groupe Froid Industriel
- Guide Pratique : Récupération de Chaleur sur Groupe Froid – Avantages et Mise en Œuvre
- Innovations et Stratégies Avancées dans le Refroidissement Industriel: Vers une Ère Durable et Efficace
- Optimisation Cruciale: Les Répercussions d’un Réseau Industriel Mal Équilibré sur la Performance et la Sécurité
- Optimisation du Dimensionnement des Tuyauteries : Préserver la Pression et Réduire les Pertes de Charge
- Calculs et dimensionnement, installation, optimisation et Maintenance des Groupes Froids Industriels : Guide Complet pour Calcul de Puissance, Facteurs de Correction, et Technologies de Contrôle
- La conception d’un système de refroidissement industriel (Industrial Cooling System)
- Révolutionner le Froid Industriel et le Refroidissement Process avec l’IoT et l’IA : Entre Solutions High Tech, Low Tech, et Approches Hybrides
- Optimiser le Refroidissement Process avec l’IoT et l’IA : Révolutions et Techniques pour les Groupes Froids et Groupes d’Eau Glacée Industriels
- Révolution Technologique des Groupes Froids Industriels et Groupes d’Eau Glacée : Quand l’IA et les IoT Façonnent l’Avenir du Refroidissement Industriel
- FAQ : Groupes Froids Industriels et au Refroidissement Process
- Questions / réponses fréquemment posées sur le thème du refroidissement de process, incluant l’eau glacée, le froid industriel, les groupes froids, et les groupes d’eau glacée
- Quelles sont les erreurs courantes à éviter lors du choix d’un groupe froid industriel pour le refroidissement de son process ?
- Refroidissement Industriel : L’Essentiel sur les Groupes Frigorifiques et les Groupes d’Eau Glacée
- Lien: Notions de base
- Lie0n : Fonctionnement des systèmes de réfrigération
- Lien : applications du froid industriel
- Lien : Avantages et inconvénients
- Lien : En conclusion, le froid industriel est un élément clé de nombreuses industries modernes
- Lien : mesure de débit ultrasonique
- Mesure de Débit d’Eau par Ultrasons : Optimisation des Process Industriels
- Lien : Vitesse des fluides dans les tuyauteries
- Pour réaliser des économies d’énergie avec les installations d’eau glacée (froid industriel)
- Lien : Retrouver la performance de vos échangeurs avec le peigne frigoriste (groupe froid industriel, sécheur air comprimé, …)
- Lien : Réfractomètre : Mesurez facilement la concentration en glycol essentielle pour assurer la sécurité et la performance des installations industrielles
- Lien : Analyse d’huile des équipements : Optimisez la maintenance industrielle (compresseur air comprimé, groupe froid industriel, …)
- Les avantages de la connectivité IoT et I.A. dans les groupes froids industriels : Comment tirer parti des données pour améliorer les performances
- Les tendances émergentes dans les groupes froids industriels : Les nouvelles technologies qui transforment l’industrie du refroidissement
- La sélection du groupe froid industriel adapté à vos besoins : Guide d’achat et recommandations pour une solution optimale
- La sécurité dans les groupes froids industriels : Conseils pour prévenir les accidents et assurer la conformité aux normes de sécurité
- Maximisez la fiabilité de votre groupe froid industriel : Les meilleures pratiques pour éviter les pannes et les temps d’arrêt coûteux
- La maintenance préventive des groupes froids industriels : Astuces pour prolonger la durée de vie de votre équipement
- Les solutions respectueuses de l’environnement pour les groupes froids industriels : Astuces pour réduire l’empreinte carbone de votre installation
- La gestion intelligente des groupes froids industriels : Comment utiliser les systèmes de contrôle avancés pour optimiser les performances
- Les dernières avancées en matière de groupes froids industriels : Les technologies innovantes qui améliorent les performances
- Groupe froid industriel : Optimisez les économies d’énergie en adaptant vos consignes de température
- Optimisez l’efficacité énergétique de votre groupe froid industriel : Astuces pratiques pour réduire la consommation d’énergie
- Maîtrisez la poussière : Astuces innovantes et simples pour protéger vos équipements avec des filtres d’air comprimé dans les environnements poussiéreu
Lien pour achats :
Optimiser l’Efficacité Énergétique d’un Groupe Froid Industriel Sans Investissement Majeur : Astuces, Bonnes Pratiques et Gains Immédiats
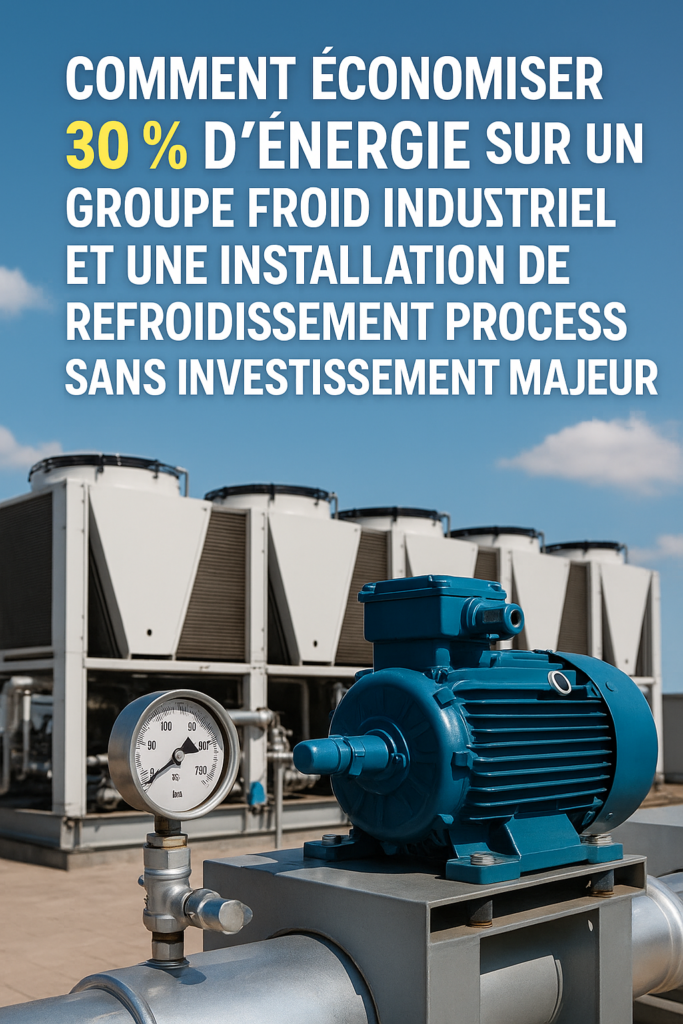
Dans un contexte où la maîtrise des coûts énergétiques et la réduction de l’empreinte carbone sont devenues des priorités, optimiser l’efficacité énergétique des groupes froids industriels est essentiel. Bonne nouvelle : il est possible d’obtenir des résultats significatifs sans investissements lourds. En agissant sur les réglages, la maintenance et en impliquant les équipes, des économies d’énergie allant jusqu’à 30 % peuvent être réalisées, tout en prolongeant la durée de vie des équipements.
1. Agir sur les Réglages et l’Entretien
1.1. Optimisation des Réglages
- Ajuster les consignes de température : Relever la consigne de température de quelques degrés peut réduire la charge sur le système frigorifique.
- Régulation de la pression flottante : Adapter la pression de condensation en fonction des conditions extérieures permet de diminuer la consommation énergétique.
1.2. Maintenance Préventive
- Nettoyage régulier des échangeurs : Des échangeurs propres assurent un transfert de chaleur optimal, réduisant ainsi la consommation d’énergie.
- Vérification de l’étanchéité : Détecter et réparer les fuites de fluide frigorigène est crucial pour maintenir l’efficacité du système.
2. Impliquer les Techniciens et Opérateurs
- Formation continue : Former les équipes aux bonnes pratiques d’exploitation et de maintenance permet d’identifier rapidement les anomalies et d’agir en conséquence.
- Sensibilisation à l’efficacité énergétique : Impliquer le personnel dans la démarche d’optimisation favorise l’adoption de comportements éco-responsables.
3. Suivre Régulièrement les Performances
- Mise en place d’indicateurs de performance : Suivre des indicateurs tels que le coefficient de performance (COP) ou la consommation énergétique spécifique permet d’évaluer l’efficacité du système.
- Utilisation d’outils de monitoring : Des outils simples, comme des enregistreurs de données ou des logiciels de supervision, facilitent le suivi en temps réel des performances.
4. Décider sur des Mesures Simples, Mesurables et Vérifiables
- Identification des actions prioritaires : Cibler les interventions ayant un retour sur investissement rapide, comme l’isolation des tuyauteries ou l’installation de vannes de régulation.
- Mise en œuvre progressive : Planifier les actions en fonction de leur impact et de leur faisabilité, en commençant par les plus simples à réaliser.
5. Astuces Techniques et Bonnes Pratiques
- Utilisation de ventilateurs à vitesse variable : Adapter la vitesse des ventilateurs en fonction des besoins permet de réduire la consommation énergétique.
- Récupération de chaleur : Valoriser la chaleur fatale issue du processus de refroidissement pour d’autres usages, comme le chauffage de locaux ou la production d’eau chaude.
- Surveillance des températures de refoulement : Des températures élevées peuvent indiquer la présence d’incondensables, affectant l’efficacité du système.
Optimiser l’efficacité énergétique d’un groupe froid industriel sans investissement majeur est non seulement possible, mais également rentable. En agissant sur les réglages, la maintenance, en impliquant les équipes et en suivant régulièrement les performances, des économies d’énergie significatives peuvent être réalisées. Ces actions contribuent également à la réduction de l’empreinte carbone et à la pérennité des installations.
Note : Pour des recommandations spécifiques à votre installation, il est conseillé de consulter un professionnel qualifié.
En somme, l’ingénierie des fluides industriels est une discipline importante et diversifiée qui joue un rôle clé dans de nombreuses industries. Elle nécessite une expertise technique et une connaissance approfondie des systèmes de circulation des fluides, de la thermodynamique, de la mécanique des fluides, de la régulation et du contrôle des processus, ainsi que de la sécurité.
Notre blog est une ressource complète pour tout ce qui concerne les fluides industriels. Nous vous encourageons à explorer nos articles, nos guides pratiques et nos ressources de formation pour approfondir vos connaissances et améliorer vos performances énergétiques. N’hésitez pas à nous contacter pour bénéficier de nos services d’ingénierie personnalisés ou pour trouver les produits dont vous avez besoin via notre site de commerce en ligne. Ensemble, nous pouvons aller plus loin dans l’apprentissage et réaliser des économies d’énergie significatives. Contactez-nous dès aujourd’hui à l’adresse suivante :
- Guide pour choisir un groupe froid industriel
- Lien : Exemple de schémas d’installation
- Lien : Calcul de la puissance nécessaire et facteurs de corrections usuels
- Le Guide Ultime du Choix des Compresseurs Frigorifiques : Optimisation, Puissance et Régulation
- Installation optimale de groupes froids industriels : Pratiques essentielles et paramètres clés
- Guide : La mise en service initiale d’un groupe froid industriel
- Les Applications du Refroidissement Industriel dans Divers Secteurs
- Guide Pratique pour le Choix d’un Groupe Froid Industriel : Calculs, Installations, Méthodes, Besoins et Critères Essentiels
- Optimiser l’Efficacité Énergétique : Deux Méthodes Ingénieuses pour Récupérer la Chaleur d’un Groupe Froid Industriel
- Guide Pratique : Récupération de Chaleur sur Groupe Froid – Avantages et Mise en Œuvre
- Innovations et Stratégies Avancées dans le Refroidissement Industriel: Vers une Ère Durable et Efficace
- Optimisation Cruciale: Les Répercussions d’un Réseau Industriel Mal Équilibré sur la Performance et la Sécurité
- Optimisation du Dimensionnement des Tuyauteries : Préserver la Pression et Réduire les Pertes de Charge
- Calculs et dimensionnement, installation, optimisation et Maintenance des Groupes Froids Industriels : Guide Complet pour Calcul de Puissance, Facteurs de Correction, et Technologies de Contrôle
- La conception d’un système de refroidissement industriel (Industrial Cooling System)
- Révolutionner le Froid Industriel et le Refroidissement Process avec l’IoT et l’IA : Entre Solutions High Tech, Low Tech, et Approches Hybrides
- Optimiser le Refroidissement Process avec l’IoT et l’IA : Révolutions et Techniques pour les Groupes Froids et Groupes d’Eau Glacée Industriels
- Révolution Technologique des Groupes Froids Industriels et Groupes d’Eau Glacée : Quand l’IA et les IoT Façonnent l’Avenir du Refroidissement Industriel
- FAQ : Groupes Froids Industriels et au Refroidissement Process
- Questions / réponses fréquemment posées sur le thème du refroidissement de process, incluant l’eau glacée, le froid industriel, les groupes froids, et les groupes d’eau glacée
- Quelles sont les erreurs courantes à éviter lors du choix d’un groupe froid industriel pour le refroidissement de son process ?
- Refroidissement Industriel : L’Essentiel sur les Groupes Frigorifiques et les Groupes d’Eau Glacée
- Lien: Notions de base
- Lie0n : Fonctionnement des systèmes de réfrigération
- Lien : applications du froid industriel
- Lien : Avantages et inconvénients
- Lien : En conclusion, le froid industriel est un élément clé de nombreuses industries modernes
- Lien : mesure de débit ultrasonique
- Mesure de Débit d’Eau par Ultrasons : Optimisation des Process Industriels
- Lien : Vitesse des fluides dans les tuyauteries
- Pour réaliser des économies d’énergie avec les installations d’eau glacée (froid industriel)
- Lien : Retrouver la performance de vos échangeurs avec le peigne frigoriste (groupe froid industriel, sécheur air comprimé, …)
- Lien : Réfractomètre : Mesurez facilement la concentration en glycol essentielle pour assurer la sécurité et la performance des installations industrielles
- Lien : Analyse d’huile des équipements : Optimisez la maintenance industrielle (compresseur air comprimé, groupe froid industriel, …)
- Les avantages de la connectivité IoT et I.A. dans les groupes froids industriels : Comment tirer parti des données pour améliorer les performances
- Les tendances émergentes dans les groupes froids industriels : Les nouvelles technologies qui transforment l’industrie du refroidissement
- La sélection du groupe froid industriel adapté à vos besoins : Guide d’achat et recommandations pour une solution optimale
- La sécurité dans les groupes froids industriels : Conseils pour prévenir les accidents et assurer la conformité aux normes de sécurité
- Maximisez la fiabilité de votre groupe froid industriel : Les meilleures pratiques pour éviter les pannes et les temps d’arrêt coûteux
- La maintenance préventive des groupes froids industriels : Astuces pour prolonger la durée de vie de votre équipement
- Les solutions respectueuses de l’environnement pour les groupes froids industriels : Astuces pour réduire l’empreinte carbone de votre installation
- La gestion intelligente des groupes froids industriels : Comment utiliser les systèmes de contrôle avancés pour optimiser les performances
- Les dernières avancées en matière de groupes froids industriels : Les technologies innovantes qui améliorent les performances
- Groupe froid industriel : Optimisez les économies d’énergie en adaptant vos consignes de température
- Optimisez l’efficacité énergétique de votre groupe froid industriel : Astuces pratiques pour réduire la consommation d’énergie
- Maîtrisez la poussière : Astuces innovantes et simples pour protéger vos équipements avec des filtres d’air comprimé dans les environnements poussiéreu
Lien pour achats :
Réduire son Impact Carbone : Comment les Économies d’Énergie Deviennent un Atout RSE Majeur
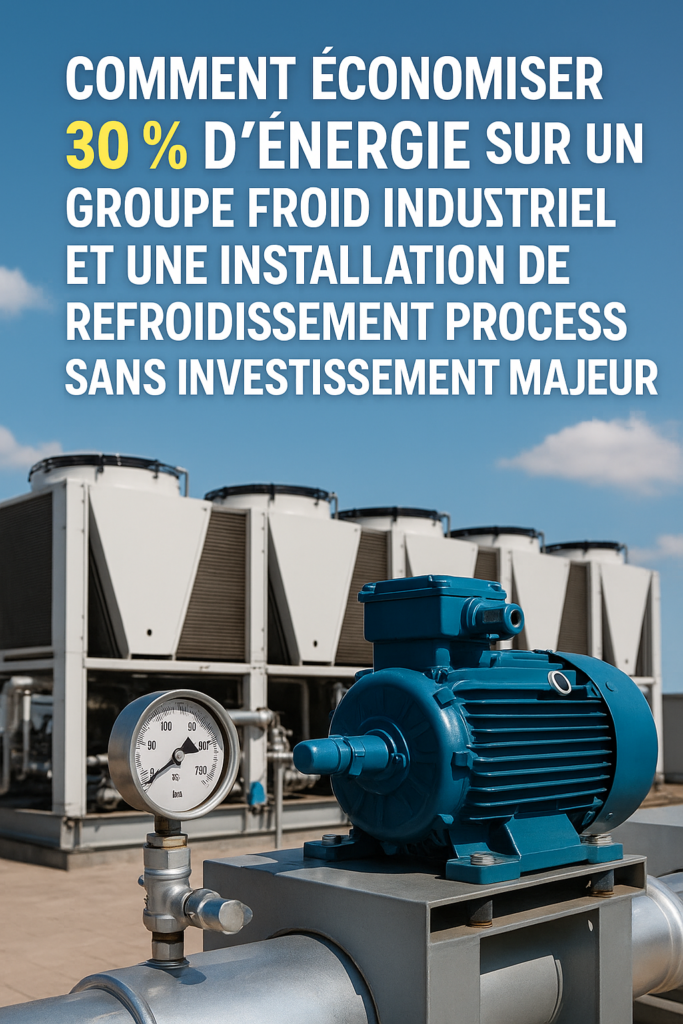
Dans un contexte où la transition énergétique est au cœur des préoccupations, réduire sa consommation d’énergie ne se limite plus à une simple question d’économie financière. C’est également un levier puissant pour diminuer son empreinte carbone et valoriser ses engagements en matière de Responsabilité Sociétale des Entreprises (RSE). Cet article explore comment chaque kilowattheure (kWh) économisé contribue à la lutte contre le changement climatique et renforce la position des entreprises dans leurs démarches environnementales.
1. Comprendre l’Impact Carbone de l’Électricité
1.1. Qu’est-ce que l’empreinte carbone de l’électricité ?
L’empreinte carbone de l’électricité correspond aux émissions de dioxyde de carbone (CO₂) générées lors de sa production. Elle varie en fonction du mix énergétique de chaque pays. Par exemple, en France, grâce à une production majoritairement nucléaire, l’intensité carbone est relativement faible, estimée à environ 32 gCO₂eq/kWh en 2023 .Analyses et Données de l’Électricité
1.2. Moyenne européenne
En Europe, la moyenne des émissions de CO₂ par kWh est plus élevée, atteignant environ 0,5 kg CO₂/kWh . Cette différence souligne l’importance de prendre en compte le contexte local lors de l’évaluation de l’impact carbone des économies d’énergie.Green IT
2. Calculer les Émissions de CO₂ Évitée
Chaque kWh économisé se traduit par une réduction des émissions de CO₂. En utilisant le facteur d’émission moyen européen de 0,5 kg CO₂/kWh, on peut estimer les économies d’émissions réalisées.
2.1. Exemple de calcul
- Économie d’énergie : 30 000 kWh/an
- Facteur d’émission : 0,5 kg CO₂/kWh
- Émissions évitées : 30 000 kWh × 0,5 kg CO₂/kWh = 15 tonnes de CO₂/an
Ainsi, une économie de 30 000 kWh par an permet d’éviter l’émission de 15 tonnes de CO₂, contribuant significativement à la réduction de l’empreinte carbone de l’entreprise.
3. Intégrer les Économies d’Énergie dans la Stratégie RSE
3.1. Valorisation dans les audits RSE
Les économies d’énergie et les réductions d’émissions de CO₂ sont des indicateurs clés dans les audits RSE. Ils démontrent l’engagement de l’entreprise en faveur du développement durable et peuvent améliorer sa notation dans les évaluations environnementales.
3.2. Certification ISO 14001
La norme ISO 14001 encourage les entreprises à identifier et à maîtriser les impacts environnementaux de leurs activités. Les économies d’énergie et la réduction des émissions de CO₂ sont des éléments essentiels pour obtenir et maintenir cette certification.
3.3. Communication auprès des parties prenantes
Mettre en avant les efforts réalisés en matière d’économies d’énergie et de réduction des émissions de CO₂ renforce la réputation de l’entreprise auprès de ses clients, partenaires et investisseurs. Cela peut également constituer un avantage concurrentiel sur le marché.
4. Bonnes Pratiques pour Réduire l’Impact Carbone
4.1. Audit énergétique
Réaliser un audit énergétique permet d’identifier les sources de consommation d’énergie et de mettre en place des actions ciblées pour les réduire.
4.2. Optimisation des équipements
Remplacer les équipements obsolètes par des modèles plus performants et économes en énergie contribue à diminuer la consommation et les émissions associées.
4.3. Sensibilisation des collaborateurs
Impliquer les employés dans la démarche de réduction de l’impact carbone favorise l’adoption de comportements éco-responsables au quotidien.
Réduire sa consommation d’énergie est une démarche gagnant-gagnant : elle permet de réaliser des économies financières tout en diminuant son empreinte carbone. Intégrer ces actions dans une stratégie RSE globale renforce l’engagement de l’entreprise en faveur du développement durable et améliore sa performance environnementale. Chaque kWh économisé compte, et les bénéfices sont multiples : pour l’entreprise, pour la planète et pour les générations futures.
Note : Pour des recommandations spécifiques à votre installation, il est conseillé de consulter un professionnel qualifié.
En somme, l’ingénierie des fluides industriels est une discipline importante et diversifiée qui joue un rôle clé dans de nombreuses industries. Elle nécessite une expertise technique et une connaissance approfondie des systèmes de circulation des fluides, de la thermodynamique, de la mécanique des fluides, de la régulation et du contrôle des processus, ainsi que de la sécurité.
Notre blog est une ressource complète pour tout ce qui concerne les fluides industriels. Nous vous encourageons à explorer nos articles, nos guides pratiques et nos ressources de formation pour approfondir vos connaissances et améliorer vos performances énergétiques. N’hésitez pas à nous contacter pour bénéficier de nos services d’ingénierie personnalisés ou pour trouver les produits dont vous avez besoin via notre site de commerce en ligne. Ensemble, nous pouvons aller plus loin dans l’apprentissage et réaliser des économies d’énergie significatives. Contactez-nous dès aujourd’hui à l’adresse suivante :
- Guide pour choisir un groupe froid industriel
- Lien : Exemple de schémas d’installation
- Lien : Calcul de la puissance nécessaire et facteurs de corrections usuels
- Le Guide Ultime du Choix des Compresseurs Frigorifiques : Optimisation, Puissance et Régulation
- Installation optimale de groupes froids industriels : Pratiques essentielles et paramètres clés
- Guide : La mise en service initiale d’un groupe froid industriel
- Les Applications du Refroidissement Industriel dans Divers Secteurs
- Guide Pratique pour le Choix d’un Groupe Froid Industriel : Calculs, Installations, Méthodes, Besoins et Critères Essentiels
- Optimiser l’Efficacité Énergétique : Deux Méthodes Ingénieuses pour Récupérer la Chaleur d’un Groupe Froid Industriel
- Guide Pratique : Récupération de Chaleur sur Groupe Froid – Avantages et Mise en Œuvre
- Innovations et Stratégies Avancées dans le Refroidissement Industriel: Vers une Ère Durable et Efficace
- Optimisation Cruciale: Les Répercussions d’un Réseau Industriel Mal Équilibré sur la Performance et la Sécurité
- Optimisation du Dimensionnement des Tuyauteries : Préserver la Pression et Réduire les Pertes de Charge
- Calculs et dimensionnement, installation, optimisation et Maintenance des Groupes Froids Industriels : Guide Complet pour Calcul de Puissance, Facteurs de Correction, et Technologies de Contrôle
- La conception d’un système de refroidissement industriel (Industrial Cooling System)
- Révolutionner le Froid Industriel et le Refroidissement Process avec l’IoT et l’IA : Entre Solutions High Tech, Low Tech, et Approches Hybrides
- Optimiser le Refroidissement Process avec l’IoT et l’IA : Révolutions et Techniques pour les Groupes Froids et Groupes d’Eau Glacée Industriels
- Révolution Technologique des Groupes Froids Industriels et Groupes d’Eau Glacée : Quand l’IA et les IoT Façonnent l’Avenir du Refroidissement Industriel
- FAQ : Groupes Froids Industriels et au Refroidissement Process
- Questions / réponses fréquemment posées sur le thème du refroidissement de process, incluant l’eau glacée, le froid industriel, les groupes froids, et les groupes d’eau glacée
- Quelles sont les erreurs courantes à éviter lors du choix d’un groupe froid industriel pour le refroidissement de son process ?
- Refroidissement Industriel : L’Essentiel sur les Groupes Frigorifiques et les Groupes d’Eau Glacée
- Lien: Notions de base
- Lie0n : Fonctionnement des systèmes de réfrigération
- Lien : applications du froid industriel
- Lien : Avantages et inconvénients
- Lien : En conclusion, le froid industriel est un élément clé de nombreuses industries modernes
- Lien : mesure de débit ultrasonique
- Mesure de Débit d’Eau par Ultrasons : Optimisation des Process Industriels
- Lien : Vitesse des fluides dans les tuyauteries
- Pour réaliser des économies d’énergie avec les installations d’eau glacée (froid industriel)
- Lien : Retrouver la performance de vos échangeurs avec le peigne frigoriste (groupe froid industriel, sécheur air comprimé, …)
- Lien : Réfractomètre : Mesurez facilement la concentration en glycol essentielle pour assurer la sécurité et la performance des installations industrielles
- Lien : Analyse d’huile des équipements : Optimisez la maintenance industrielle (compresseur air comprimé, groupe froid industriel, …)
- Les avantages de la connectivité IoT et I.A. dans les groupes froids industriels : Comment tirer parti des données pour améliorer les performances
- Les tendances émergentes dans les groupes froids industriels : Les nouvelles technologies qui transforment l’industrie du refroidissement
- La sélection du groupe froid industriel adapté à vos besoins : Guide d’achat et recommandations pour une solution optimale
- La sécurité dans les groupes froids industriels : Conseils pour prévenir les accidents et assurer la conformité aux normes de sécurité
- Maximisez la fiabilité de votre groupe froid industriel : Les meilleures pratiques pour éviter les pannes et les temps d’arrêt coûteux
- La maintenance préventive des groupes froids industriels : Astuces pour prolonger la durée de vie de votre équipement
- Les solutions respectueuses de l’environnement pour les groupes froids industriels : Astuces pour réduire l’empreinte carbone de votre installation
- La gestion intelligente des groupes froids industriels : Comment utiliser les systèmes de contrôle avancés pour optimiser les performances
- Les dernières avancées en matière de groupes froids industriels : Les technologies innovantes qui améliorent les performances
- Groupe froid industriel : Optimisez les économies d’énergie en adaptant vos consignes de température
- Optimisez l’efficacité énergétique de votre groupe froid industriel : Astuces pratiques pour réduire la consommation d’énergie
- Maîtrisez la poussière : Astuces innovantes et simples pour protéger vos équipements avec des filtres d’air comprimé dans les environnements poussiéreu
Lien pour achats :
Simulation d’Économie Réelle : Optimiser un Groupe Froid de 100 kW pour Réduire les Coûts Énergétiques
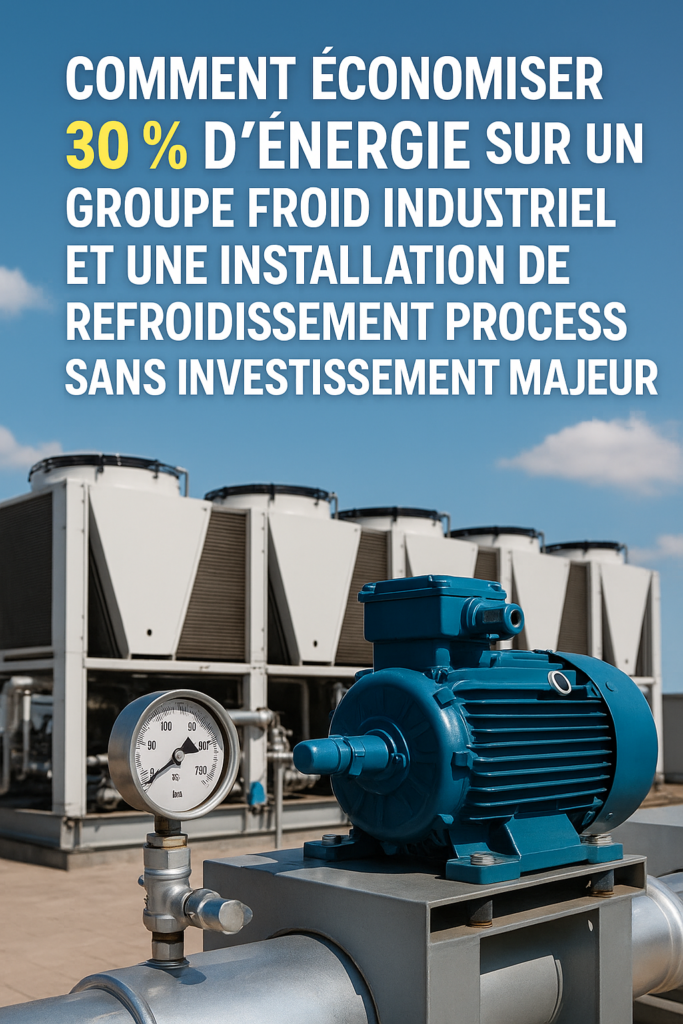
Dans un contexte où la maîtrise des coûts énergétiques est essentielle, l’optimisation des installations frigorifiques devient une priorité. Cet article présente une simulation concrète des économies réalisables sur un groupe froid de 100 kW électrique, en mettant en œuvre des actions simples et efficaces.
1. Contexte de l’Installation
Considérons une installation équipée d’un groupe froid d’une puissance électrique de 100 kW, fonctionnant 8 000 heures par an. Le coût de l’électricité est estimé à 0,11 €/kWh. L’objectif est de réduire la consommation énergétique sans compromettre les performances du système.
2. Actions d’Optimisation et Gains Estimés
Action | Gain Estimé | Réduction de Puissance |
---|---|---|
Remonter la consigne de température de +2°C | 5 % | -5 kW |
Nettoyage du condenseur | 8 % | -8 kW |
Optimisation de la séquence des compresseurs | 6 % | -6 kW |
Optimisation des ventilateurs | 3 % | -3 kW |
Isolation des tuyauteries | 5 % | -5 kW |
Coupure automatique des process non utilisés | 4 % | -4 kW |
Total | 30 % | -30 kW |
3. Détail des Actions
3.1 Remonter la Consigne de Température de +2°C
Augmenter la consigne de température de l’eau glacée de 2°C permet de réduire la charge sur le compresseur, diminuant ainsi la consommation énergétique.
3.2 Nettoyage du Condenseur
Un condenseur encrassé entraîne une surconsommation d’énergie. Un nettoyage régulier améliore l’efficacité thermique et réduit la consommation.
3.3 Optimisation de la Séquence des Compresseurs
Adapter la séquence de fonctionnement des compresseurs en fonction de la demande permet d’éviter les démarrages fréquents et d’optimiser la consommation.
3.4 Optimisation des Ventilateurs
L’utilisation de ventilateurs à vitesse variable et la régulation de leur fonctionnement en fonction des besoins réduisent la consommation énergétique.
3.5 Isolation des Tuyauteries
Une bonne isolation des tuyauteries limite les pertes thermiques, réduisant ainsi la charge sur le système frigorifique.
3.6 Coupure Automatique des Process Non Utilisés
Mettre en place des systèmes de détection et de coupure automatique pour les process non utilisés évite une consommation inutile.
4. Simulation des Économies Réalisées
En appliquant l’ensemble de ces actions, la puissance électrique nécessaire est réduite de 30 kW.
- Puissance Économisée : 30 kW
- Heures de Fonctionnement Annuelles : 8 000 hEnergie Plus Le Site+4Scribd+4aggreko.com+4
- Énergie Économisée : 30 kW × 8 000 h = 240 000 kWh
- Coût de l’Électricité : 0,11 €/kWh
- Économie Annuelle : 240 000 kWh × 0,11 €/kWh = 26 400 €
5. Retour sur Investissement
Les actions proposées nécessitent des investissements modérés, principalement en maintenance et en équipements de régulation. Le retour sur investissement est généralement inférieur à un an, rendant ces optimisations particulièrement attractives.
L’optimisation d’un groupe froid de 100 kW permet de réaliser des économies significatives, tant sur le plan énergétique que financier. En mettant en œuvre des actions simples et ciblées, il est possible de réduire la consommation de 30 %, soit une économie annuelle d’environ 26 400 €. Ces mesures contribuent également à la durabilité des installations et à la réduction de l’empreinte carbone.
Note : Pour des recommandations spécifiques à votre installation, il est conseillé de consulter un professionnel qualifié.
En somme, l’ingénierie des fluides industriels est une discipline importante et diversifiée qui joue un rôle clé dans de nombreuses industries. Elle nécessite une expertise technique et une connaissance approfondie des systèmes de circulation des fluides, de la thermodynamique, de la mécanique des fluides, de la régulation et du contrôle des processus, ainsi que de la sécurité.
Notre blog est une ressource complète pour tout ce qui concerne les fluides industriels. Nous vous encourageons à explorer nos articles, nos guides pratiques et nos ressources de formation pour approfondir vos connaissances et améliorer vos performances énergétiques. N’hésitez pas à nous contacter pour bénéficier de nos services d’ingénierie personnalisés ou pour trouver les produits dont vous avez besoin via notre site de commerce en ligne. Ensemble, nous pouvons aller plus loin dans l’apprentissage et réaliser des économies d’énergie significatives. Contactez-nous dès aujourd’hui à l’adresse suivante :
- Guide pour choisir un groupe froid industriel
- Lien : Exemple de schémas d’installation
- Lien : Calcul de la puissance nécessaire et facteurs de corrections usuels
- Le Guide Ultime du Choix des Compresseurs Frigorifiques : Optimisation, Puissance et Régulation
- Installation optimale de groupes froids industriels : Pratiques essentielles et paramètres clés
- Guide : La mise en service initiale d’un groupe froid industriel
- Les Applications du Refroidissement Industriel dans Divers Secteurs
- Guide Pratique pour le Choix d’un Groupe Froid Industriel : Calculs, Installations, Méthodes, Besoins et Critères Essentiels
- Optimiser l’Efficacité Énergétique : Deux Méthodes Ingénieuses pour Récupérer la Chaleur d’un Groupe Froid Industriel
- Guide Pratique : Récupération de Chaleur sur Groupe Froid – Avantages et Mise en Œuvre
- Innovations et Stratégies Avancées dans le Refroidissement Industriel: Vers une Ère Durable et Efficace
- Optimisation Cruciale: Les Répercussions d’un Réseau Industriel Mal Équilibré sur la Performance et la Sécurité
- Optimisation du Dimensionnement des Tuyauteries : Préserver la Pression et Réduire les Pertes de Charge
- Calculs et dimensionnement, installation, optimisation et Maintenance des Groupes Froids Industriels : Guide Complet pour Calcul de Puissance, Facteurs de Correction, et Technologies de Contrôle
- La conception d’un système de refroidissement industriel (Industrial Cooling System)
- Révolutionner le Froid Industriel et le Refroidissement Process avec l’IoT et l’IA : Entre Solutions High Tech, Low Tech, et Approches Hybrides
- Optimiser le Refroidissement Process avec l’IoT et l’IA : Révolutions et Techniques pour les Groupes Froids et Groupes d’Eau Glacée Industriels
- Révolution Technologique des Groupes Froids Industriels et Groupes d’Eau Glacée : Quand l’IA et les IoT Façonnent l’Avenir du Refroidissement Industriel
- FAQ : Groupes Froids Industriels et au Refroidissement Process
- Questions / réponses fréquemment posées sur le thème du refroidissement de process, incluant l’eau glacée, le froid industriel, les groupes froids, et les groupes d’eau glacée
- Quelles sont les erreurs courantes à éviter lors du choix d’un groupe froid industriel pour le refroidissement de son process ?
- Refroidissement Industriel : L’Essentiel sur les Groupes Frigorifiques et les Groupes d’Eau Glacée
- Lien: Notions de base
- Lie0n : Fonctionnement des systèmes de réfrigération
- Lien : applications du froid industriel
- Lien : Avantages et inconvénients
- Lien : En conclusion, le froid industriel est un élément clé de nombreuses industries modernes
- Lien : mesure de débit ultrasonique
- Mesure de Débit d’Eau par Ultrasons : Optimisation des Process Industriels
- Lien : Vitesse des fluides dans les tuyauteries
- Pour réaliser des économies d’énergie avec les installations d’eau glacée (froid industriel)
- Lien : Retrouver la performance de vos échangeurs avec le peigne frigoriste (groupe froid industriel, sécheur air comprimé, …)
- Lien : Réfractomètre : Mesurez facilement la concentration en glycol essentielle pour assurer la sécurité et la performance des installations industrielles
- Lien : Analyse d’huile des équipements : Optimisez la maintenance industrielle (compresseur air comprimé, groupe froid industriel, …)
- Les avantages de la connectivité IoT et I.A. dans les groupes froids industriels : Comment tirer parti des données pour améliorer les performances
- Les tendances émergentes dans les groupes froids industriels : Les nouvelles technologies qui transforment l’industrie du refroidissement
- La sélection du groupe froid industriel adapté à vos besoins : Guide d’achat et recommandations pour une solution optimale
- La sécurité dans les groupes froids industriels : Conseils pour prévenir les accidents et assurer la conformité aux normes de sécurité
- Maximisez la fiabilité de votre groupe froid industriel : Les meilleures pratiques pour éviter les pannes et les temps d’arrêt coûteux
- La maintenance préventive des groupes froids industriels : Astuces pour prolonger la durée de vie de votre équipement
- Les solutions respectueuses de l’environnement pour les groupes froids industriels : Astuces pour réduire l’empreinte carbone de votre installation
- La gestion intelligente des groupes froids industriels : Comment utiliser les systèmes de contrôle avancés pour optimiser les performances
- Les dernières avancées en matière de groupes froids industriels : Les technologies innovantes qui améliorent les performances
- Groupe froid industriel : Optimisez les économies d’énergie en adaptant vos consignes de température
- Optimisez l’efficacité énergétique de votre groupe froid industriel : Astuces pratiques pour réduire la consommation d’énergie
- Maîtrisez la poussière : Astuces innovantes et simples pour protéger vos équipements avec des filtres d’air comprimé dans les environnements poussiéreu
Lien pour achats :
Mesurer pour Mieux Piloter : Le Suivi Énergétique Accessible à Tous
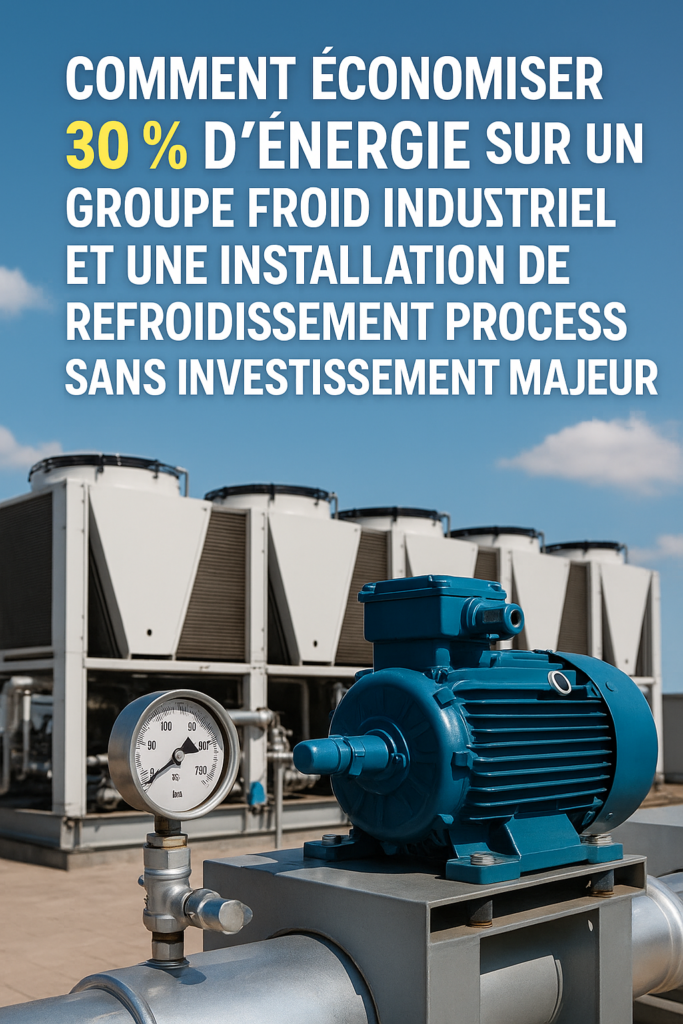
Dans un contexte où l’efficacité énergétique est devenue une priorité, la capacité à mesurer et à analyser sa consommation d’énergie est essentielle. Cependant, beaucoup pensent à tort que cela nécessite des systèmes coûteux comme le SCADA ou la GTC. En réalité, il est tout à fait possible de mettre en place un monitoring énergétique basique, efficace et économique.
1. Les Outils de Base pour un Suivi Énergétique Efficace
1.1 Manomètre Différentiel
Le manomètre différentiel est un outil simple permettant de mesurer la différence de pression entre deux points d’un système. Il est particulièrement utile pour suivre les pertes de charge dans les condenseurs et évaporateurs.
- Usage : Suivi des pertes dans les échangeurs thermiques.
- Coût : Environ 30 €.
- Effet : Diagnostic facile des encrassements et des dysfonctionnements.
1.2 Thermomètre Infrarouge
Le thermomètre infrarouge permet de mesurer la température de surface sans contact, ce qui est idéal pour contrôler les températures des échangeurs.
- Usage : Contrôle des températures des échangeurs.
- Coût : Environ 50 €.
- Effet : Détection rapide des anomalies thermiques.
1.3 Compteur kWh Clipsable
Le compteur kWh clipsable est un dispositif qui se fixe facilement sur les câbles électriques pour mesurer la consommation d’énergie.
- Usage : Suivi de la consommation électrique des équipements.
- Coût : Environ 80 €.
- Effet : Mesure directe des gains énergétiques.
2. Astuce Terrain : Le Tableau de Suivi Excel
Même sans logiciel spécialisé, un simple tableau Excel peut devenir un outil puissant pour le suivi énergétique.
2.1 Données à Collecter
- Consommations mensuelles (kWh).
- Consignes de température…
- Pressions relevées.
- Températures ambiantes.
2.2 Avantages
- Visualisation des tendances de consommation.
- Identification rapide des anomalies.
- Base de données pour des analyses futures.
3. Bonnes Pratiques pour un Suivi Énergétique Réussi
3.1 Régularité des Mesures
Effectuer des relevés réguliers (quotidiens, hebdomadaires ou mensuels) permet de détecter rapidement les dérives de consommation.
3.2 Implication du Personnel
Former et sensibiliser le personnel à l’importance du suivi énergétique favorise une culture d’économie d’énergie au sein de l’entreprise.
3.3 Analyse des Données
Analyser les données collectées pour identifier les opportunités d’amélioration et mettre en place des actions correctives.
Le suivi énergétique ne nécessite pas forcément des investissements lourds. Avec des outils simples et abordables, il est possible de mettre en place un système de monitoring efficace. L’essentiel est de commencer, même modestement, car chaque action compte dans la quête de l’efficacité énergétique.
Note : Pour des recommandations spécifiques à votre installation, il est conseillé de consulter un professionnel qualifié.
✅ Tableau de Synthèse : Outils de Suivi Énergétique à Bas Coût
Outil | Utilisation | Prix Indicatif | Avantage Clé |
---|---|---|---|
Manomètre différentiel | Suivi des pertes de charge sur échangeurs (évaporateurs/condenseurs) | ~30 € | Permet d’anticiper l’encrassement et de planifier le nettoyage |
Thermomètre infrarouge | Contrôle sans contact des températures des échangeurs | ~50 € | Rapide, simple et sans démontage |
Compteur kWh clipsable | Mesure directe de la consommation électrique | ~80 € | Visualisation immédiate des consommations spécifiques |
Tableau Excel personnalisé | Suivi mensuel des données clés (T°, pression, kWh, anomalies…) | Gratuit | Analyse des tendances et aide à la décision |
Horloge compteur/temps de marche | Connaître le temps de fonctionnement réel d’un équipement | ~25 € | Aide à détecter les surfonctionnements ou cycles trop longs |
📊 Exemple de Tableau de Suivi Énergétique (modèle Excel à créer)
Ce tableau peut être mis à jour chaque semaine ou chaque mois selon les besoins.
Date | Température consigne (°C) | Pression condenseur (bar) | Température ambiante (°C) | kWh consommés (groupe froid) | Observations / Anomalies |
---|---|---|---|---|---|
01/03/2025 | -6 | 13 | 21 | 1120 | RAS |
08/03/2025 | -6 | 14,5 | 24 | 1260 | Nettoyage condenseur à prévoir |
15/03/2025 | -5 | 12,5 | 22 | 1150 | Température consigne remontée de 1°C |
22/03/2025 | -5 | 12,2 | 21 | 1090 | Nettoyage condenseur effectué le 16/03 |
29/03/2025 | -5 | 12 | 20 | 1070 | RAS |
🧠 Bon à savoir :
- Une analyse graphique dans Excel (courbes d’évolution) peut mettre en évidence les corrélations entre pression, température et consommation électrique.
- Intégrer un indice de performance énergétique (kWh/tonne produite ou kWh/m³) est utile pour comparer l’efficacité au fil du temps.
- Ce type de suivi permet de justifier des investissements ou des ajustements techniques.
En somme, l’ingénierie des fluides industriels est une discipline importante et diversifiée qui joue un rôle clé dans de nombreuses industries. Elle nécessite une expertise technique et une connaissance approfondie des systèmes de circulation des fluides, de la thermodynamique, de la mécanique des fluides, de la régulation et du contrôle des processus, ainsi que de la sécurité.
Notre blog est une ressource complète pour tout ce qui concerne les fluides industriels. Nous vous encourageons à explorer nos articles, nos guides pratiques et nos ressources de formation pour approfondir vos connaissances et améliorer vos performances énergétiques. N’hésitez pas à nous contacter pour bénéficier de nos services d’ingénierie personnalisés ou pour trouver les produits dont vous avez besoin via notre site de commerce en ligne. Ensemble, nous pouvons aller plus loin dans l’apprentissage et réaliser des économies d’énergie significatives. Contactez-nous dès aujourd’hui à l’adresse suivante :
- Guide pour choisir un groupe froid industriel
- Lien : Exemple de schémas d’installation
- Lien : Calcul de la puissance nécessaire et facteurs de corrections usuels
- Le Guide Ultime du Choix des Compresseurs Frigorifiques : Optimisation, Puissance et Régulation
- Installation optimale de groupes froids industriels : Pratiques essentielles et paramètres clés
- Guide : La mise en service initiale d’un groupe froid industriel
- Les Applications du Refroidissement Industriel dans Divers Secteurs
- Guide Pratique pour le Choix d’un Groupe Froid Industriel : Calculs, Installations, Méthodes, Besoins et Critères Essentiels
- Optimiser l’Efficacité Énergétique : Deux Méthodes Ingénieuses pour Récupérer la Chaleur d’un Groupe Froid Industriel
- Guide Pratique : Récupération de Chaleur sur Groupe Froid – Avantages et Mise en Œuvre
- Innovations et Stratégies Avancées dans le Refroidissement Industriel: Vers une Ère Durable et Efficace
- Optimisation Cruciale: Les Répercussions d’un Réseau Industriel Mal Équilibré sur la Performance et la Sécurité
- Optimisation du Dimensionnement des Tuyauteries : Préserver la Pression et Réduire les Pertes de Charge
- Calculs et dimensionnement, installation, optimisation et Maintenance des Groupes Froids Industriels : Guide Complet pour Calcul de Puissance, Facteurs de Correction, et Technologies de Contrôle
- La conception d’un système de refroidissement industriel (Industrial Cooling System)
- Révolutionner le Froid Industriel et le Refroidissement Process avec l’IoT et l’IA : Entre Solutions High Tech, Low Tech, et Approches Hybrides
- Optimiser le Refroidissement Process avec l’IoT et l’IA : Révolutions et Techniques pour les Groupes Froids et Groupes d’Eau Glacée Industriels
- Révolution Technologique des Groupes Froids Industriels et Groupes d’Eau Glacée : Quand l’IA et les IoT Façonnent l’Avenir du Refroidissement Industriel
- FAQ : Groupes Froids Industriels et au Refroidissement Process
- Questions / réponses fréquemment posées sur le thème du refroidissement de process, incluant l’eau glacée, le froid industriel, les groupes froids, et les groupes d’eau glacée
- Quelles sont les erreurs courantes à éviter lors du choix d’un groupe froid industriel pour le refroidissement de son process ?
- Refroidissement Industriel : L’Essentiel sur les Groupes Frigorifiques et les Groupes d’Eau Glacée
- Lien: Notions de base
- Lie0n : Fonctionnement des systèmes de réfrigération
- Lien : applications du froid industriel
- Lien : Avantages et inconvénients
- Lien : En conclusion, le froid industriel est un élément clé de nombreuses industries modernes
- Lien : mesure de débit ultrasonique
- Mesure de Débit d’Eau par Ultrasons : Optimisation des Process Industriels
- Lien : Vitesse des fluides dans les tuyauteries
- Pour réaliser des économies d’énergie avec les installations d’eau glacée (froid industriel)
- Lien : Retrouver la performance de vos échangeurs avec le peigne frigoriste (groupe froid industriel, sécheur air comprimé, …)
- Lien : Réfractomètre : Mesurez facilement la concentration en glycol essentielle pour assurer la sécurité et la performance des installations industrielles
- Lien : Analyse d’huile des équipements : Optimisez la maintenance industrielle (compresseur air comprimé, groupe froid industriel, …)
- Les avantages de la connectivité IoT et I.A. dans les groupes froids industriels : Comment tirer parti des données pour améliorer les performances
- Les tendances émergentes dans les groupes froids industriels : Les nouvelles technologies qui transforment l’industrie du refroidissement
- La sélection du groupe froid industriel adapté à vos besoins : Guide d’achat et recommandations pour une solution optimale
- La sécurité dans les groupes froids industriels : Conseils pour prévenir les accidents et assurer la conformité aux normes de sécurité
- Maximisez la fiabilité de votre groupe froid industriel : Les meilleures pratiques pour éviter les pannes et les temps d’arrêt coûteux
- La maintenance préventive des groupes froids industriels : Astuces pour prolonger la durée de vie de votre équipement
- Les solutions respectueuses de l’environnement pour les groupes froids industriels : Astuces pour réduire l’empreinte carbone de votre installation
- La gestion intelligente des groupes froids industriels : Comment utiliser les systèmes de contrôle avancés pour optimiser les performances
- Les dernières avancées en matière de groupes froids industriels : Les technologies innovantes qui améliorent les performances
- Groupe froid industriel : Optimisez les économies d’énergie en adaptant vos consignes de température
- Optimisez l’efficacité énergétique de votre groupe froid industriel : Astuces pratiques pour réduire la consommation d’énergie
- Maîtrisez la poussière : Astuces innovantes et simples pour protéger vos équipements avec des filtres d’air comprimé dans les environnements poussiéreu
Lien pour achats :
Maîtriser et Ajuster les Débits d’Eau : Optimisez vos Systèmes pour des Économies d’Énergie Significatives
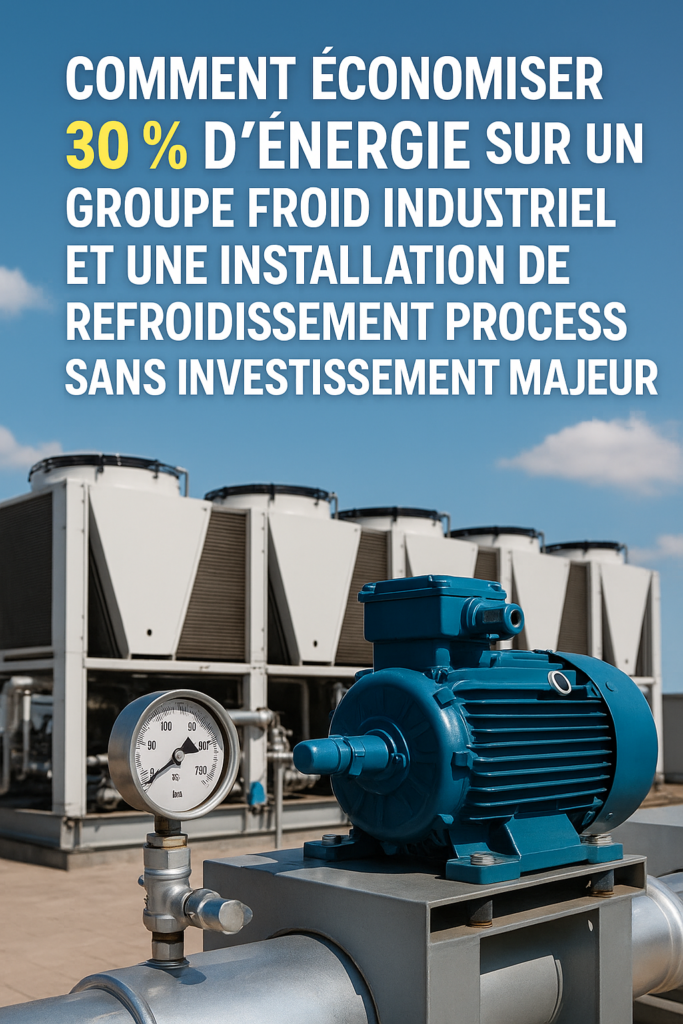
Dans les installations industrielles et tertiaires, un débit d’eau surdimensionné est une erreur fréquente qui entraîne une consommation énergétique excessive. Une gestion optimale des débits d’eau est essentielle pour améliorer l’efficacité énergétique, prolonger la durée de vie des équipements et réduire les coûts d’exploitation.
Cet article explore les causes des débits surdimensionnés, propose des solutions simples pour les corriger et présente des exemples concrets d’économies réalisées grâce à une gestion optimisée des débits d’eau.
1. Comprendre les Débits Surchargés
1.1 Causes Courantes
- Surdimensionnement des Pompes : L’installation de pompes trop puissantes par rapport aux besoins réels du système.
- Absence de Régulation : Manque de dispositifs de régulation adaptés pour ajuster le débit en fonction de la demande.
- Utilisation de Vannes de Régulation Inappropriées : L’utilisation de vannes qui ne permettent pas un contrôle précis du débit.
1.2 Conséquences
- Consommation Énergétique Accrue : Un débit excessif entraîne une consommation d’énergie inutile.
- Usure des Équipements : Les pompes et autres composants sont soumis à des contraintes supplémentaires, réduisant leur durée de vie.
- Instabilité du Système : Des débits inappropriés peuvent provoquer des déséquilibres hydrauliques, affectant la performance globale du système.
2. Solutions Simples pour Ajuster les Débits
2.1 Réduction des Débits sur Pompes Fixes
Pour les pompes à vitesse fixe, l’ajustement du débit peut être réalisé en utilisant des vannes de régulation ou des systèmes de bypass. Cela permet de contrôler le débit sans modifier la vitesse de la pompe.
2.2 Vérification des Régulations Automatiques
L’intégration de régulations automatiques, telles que des variateurs de fréquence, permet d’ajuster la vitesse des pompes en fonction de la demande réelle, optimisant ainsi la consommation d’énergie.
3. Bonnes Pratiques pour une Gestion Optimale des Débits
3.1 Réaliser un Audit Hydraulique
Un audit hydraulique permet d’identifier les points de surconsommation et de proposer des solutions adaptées pour améliorer l’efficacité énergétique des installations.
3.2 Former le Personnel
La sensibilisation et la formation du personnel à l’importance de la gestion des débits et aux bonnes pratiques de régulation sont essentielles pour maintenir des économies d’énergie sur le long terme.
3.3 Mettre en Place une Maintenance Préventive
Une maintenance régulière des équipements, y compris la vérification des vannes et des régulateurs, assure leur bon fonctionnement et prévient les dysfonctionnements pouvant entraîner des surconsommations.
4. Exemple Concret : Économie Réalisée grâce à l’Ajustement des Débits
Une entreprise a constaté une consommation énergétique excessive due à un débit d’eau surdimensionné dans son système de refroidissement. En installant des variateurs de fréquence sur les pompes et en ajustant les vannes de régulation, elle a réussi à réduire sa consommation d’énergie de 15 %, entraînant des économies significatives sur ses coûts d’exploitation.
Maîtriser et ajuster les débits d’eau dans les installations industrielles et tertiaires est une démarche essentielle pour améliorer l’efficacité énergétique et réduire les coûts d’exploitation. En identifiant les causes des débits surdimensionnés, en mettant en œuvre des solutions simples et en adoptant des bonnes pratiques de gestion, il est possible de réaliser des économies significatives tout en contribuant à la durabilité des installations.
En somme, l’ingénierie des fluides industriels est une discipline importante et diversifiée qui joue un rôle clé dans de nombreuses industries. Elle nécessite une expertise technique et une connaissance approfondie des systèmes de circulation des fluides, de la thermodynamique, de la mécanique des fluides, de la régulation et du contrôle des processus, ainsi que de la sécurité.
Notre blog est une ressource complète pour tout ce qui concerne les fluides industriels. Nous vous encourageons à explorer nos articles, nos guides pratiques et nos ressources de formation pour approfondir vos connaissances et améliorer vos performances énergétiques. N’hésitez pas à nous contacter pour bénéficier de nos services d’ingénierie personnalisés ou pour trouver les produits dont vous avez besoin via notre site de commerce en ligne. Ensemble, nous pouvons aller plus loin dans l’apprentissage et réaliser des économies d’énergie significatives. Contactez-nous dès aujourd’hui à l’adresse suivante :
- Guide pour choisir un groupe froid industriel
- Lien : Exemple de schémas d’installation
- Lien : Calcul de la puissance nécessaire et facteurs de corrections usuels
- Le Guide Ultime du Choix des Compresseurs Frigorifiques : Optimisation, Puissance et Régulation
- Installation optimale de groupes froids industriels : Pratiques essentielles et paramètres clés
- Guide : La mise en service initiale d’un groupe froid industriel
- Les Applications du Refroidissement Industriel dans Divers Secteurs
- Guide Pratique pour le Choix d’un Groupe Froid Industriel : Calculs, Installations, Méthodes, Besoins et Critères Essentiels
- Optimiser l’Efficacité Énergétique : Deux Méthodes Ingénieuses pour Récupérer la Chaleur d’un Groupe Froid Industriel
- Guide Pratique : Récupération de Chaleur sur Groupe Froid – Avantages et Mise en Œuvre
- Innovations et Stratégies Avancées dans le Refroidissement Industriel: Vers une Ère Durable et Efficace
- Optimisation Cruciale: Les Répercussions d’un Réseau Industriel Mal Équilibré sur la Performance et la Sécurité
- Optimisation du Dimensionnement des Tuyauteries : Préserver la Pression et Réduire les Pertes de Charge
- Calculs et dimensionnement, installation, optimisation et Maintenance des Groupes Froids Industriels : Guide Complet pour Calcul de Puissance, Facteurs de Correction, et Technologies de Contrôle
- La conception d’un système de refroidissement industriel (Industrial Cooling System)
- Révolutionner le Froid Industriel et le Refroidissement Process avec l’IoT et l’IA : Entre Solutions High Tech, Low Tech, et Approches Hybrides
- Optimiser le Refroidissement Process avec l’IoT et l’IA : Révolutions et Techniques pour les Groupes Froids et Groupes d’Eau Glacée Industriels
- Révolution Technologique des Groupes Froids Industriels et Groupes d’Eau Glacée : Quand l’IA et les IoT Façonnent l’Avenir du Refroidissement Industriel
- FAQ : Groupes Froids Industriels et au Refroidissement Process
- Questions / réponses fréquemment posées sur le thème du refroidissement de process, incluant l’eau glacée, le froid industriel, les groupes froids, et les groupes d’eau glacée
- Quelles sont les erreurs courantes à éviter lors du choix d’un groupe froid industriel pour le refroidissement de son process ?
- Refroidissement Industriel : L’Essentiel sur les Groupes Frigorifiques et les Groupes d’Eau Glacée
- Lien: Notions de base
- Lie0n : Fonctionnement des systèmes de réfrigération
- Lien : applications du froid industriel
- Lien : Avantages et inconvénients
- Lien : En conclusion, le froid industriel est un élément clé de nombreuses industries modernes
- Lien : mesure de débit ultrasonique
- Mesure de Débit d’Eau par Ultrasons : Optimisation des Process Industriels
- Lien : Vitesse des fluides dans les tuyauteries
- Pour réaliser des économies d’énergie avec les installations d’eau glacée (froid industriel)
- Lien : Retrouver la performance de vos échangeurs avec le peigne frigoriste (groupe froid industriel, sécheur air comprimé, …)
- Lien : Réfractomètre : Mesurez facilement la concentration en glycol essentielle pour assurer la sécurité et la performance des installations industrielles
- Lien : Analyse d’huile des équipements : Optimisez la maintenance industrielle (compresseur air comprimé, groupe froid industriel, …)
- Les avantages de la connectivité IoT et I.A. dans les groupes froids industriels : Comment tirer parti des données pour améliorer les performances
- Les tendances émergentes dans les groupes froids industriels : Les nouvelles technologies qui transforment l’industrie du refroidissement
- La sélection du groupe froid industriel adapté à vos besoins : Guide d’achat et recommandations pour une solution optimale
- La sécurité dans les groupes froids industriels : Conseils pour prévenir les accidents et assurer la conformité aux normes de sécurité
- Maximisez la fiabilité de votre groupe froid industriel : Les meilleures pratiques pour éviter les pannes et les temps d’arrêt coûteux
- La maintenance préventive des groupes froids industriels : Astuces pour prolonger la durée de vie de votre équipement
- Les solutions respectueuses de l’environnement pour les groupes froids industriels : Astuces pour réduire l’empreinte carbone de votre installation
- La gestion intelligente des groupes froids industriels : Comment utiliser les systèmes de contrôle avancés pour optimiser les performances
- Les dernières avancées en matière de groupes froids industriels : Les technologies innovantes qui améliorent les performances
- Groupe froid industriel : Optimisez les économies d’énergie en adaptant vos consignes de température
- Optimisez l’efficacité énergétique de votre groupe froid industriel : Astuces pratiques pour réduire la consommation d’énergie
- Maîtrisez la poussière : Astuces innovantes et simples pour protéger vos équipements avec des filtres d’air comprimé dans les environnements poussiéreu
Lien pour achats :
Améliorer l’Isolation Thermique : Réduisez vos Pertes Énergétiques et vos Coûts
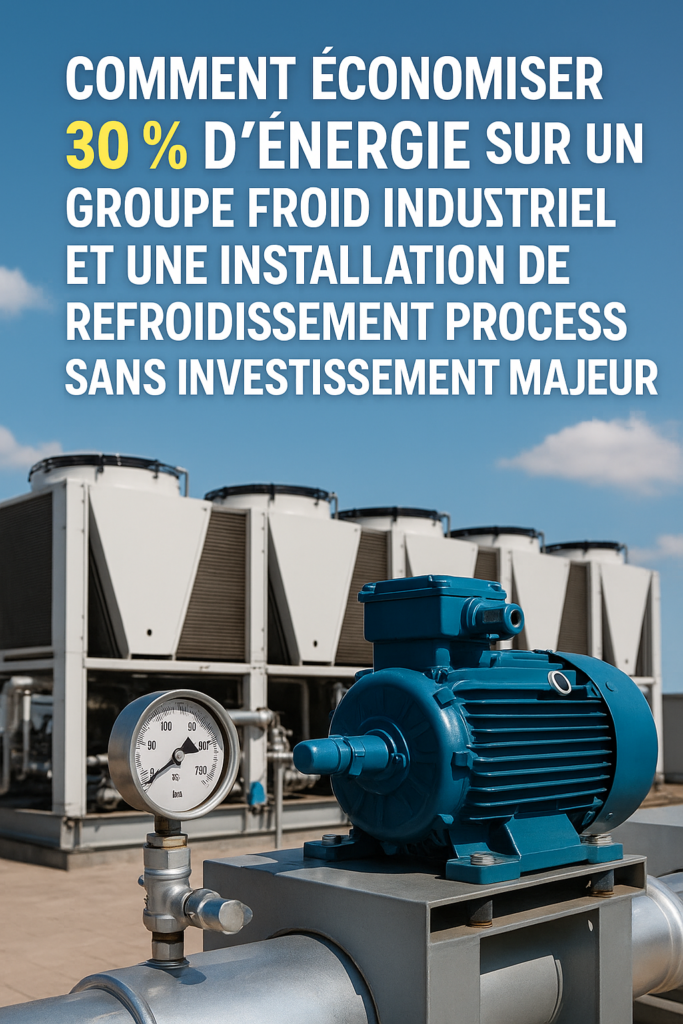
Dans les secteurs industriels et tertiaires, une isolation thermique efficace est essentielle pour minimiser les pertes d’énergie, optimiser les performances des systèmes de chauffage et de refroidissement, et réduire les coûts d’exploitation. Des zones telles que les réseaux d’eau glacée, les réservoirs tampons et les chambres froides sont particulièrement sensibles aux déperditions thermiques. Une isolation inadéquate ou dégradée peut entraîner des pertes énergétiques significatives, impactant la rentabilité et la durabilité des installations.
Cet article explore les zones prioritaires pour l’amélioration de l’isolation thermique, les matériaux et techniques recommandés, ainsi que les bonnes pratiques pour assurer une performance énergétique optimale.
1. Zones Prioritaires pour l’Isolation Thermique
1.1 Réseaux d’Eau Glacée
Les réseaux d’eau glacée sont utilisés pour le refroidissement dans de nombreux systèmes industriels et commerciaux. Une isolation efficace de ces réseaux est cruciale pour maintenir la température souhaitée et éviter les pertes d’énergie.
Bon à savoir : Une canalisation d’eau glacée non isolée de 10 mètres peut entraîner des pertes thermiques coûtant jusqu’à 500 € par an .
1.2 Réservoirs Tampons
Les réservoirs tampons stockent l’énergie thermique pour équilibrer les variations de demande. Une isolation adéquate de ces réservoirs est essentielle pour minimiser les pertes de chaleur et maintenir l’efficacité du système .
1.3 Chambres Froides
Les chambres froides nécessitent une isolation thermique de haute qualité pour maintenir des températures basses constantes. Une mauvaise isolation peut entraîner des fluctuations de température, une consommation énergétique accrue et des risques pour la conservation des produits .
2. Vérification et Réparation de l’Isolation
2.1 Inspection des Isolants
Il est essentiel de vérifier régulièrement l’état des matériaux isolants pour détecter les signes d’usure, d’humidité ou de dégradation. Les isolants endommagés ou manquants doivent être remplacés pour assurer une performance optimale.
2.2 Traitement de l’Humidité
L’humidité peut compromettre l’efficacité des matériaux isolants. Il est important de s’assurer que les isolants restent secs et de réparer toute fuite ou infiltration d’eau susceptible de les affecter.
3. Matériaux et Techniques d’Isolation Recommandés
3.1 Matériaux Isolants
- Mousse de polyuréthane (PUR) : Offre une excellente résistance thermique et est couramment utilisée pour l’isolation des réservoirs tampons .
- Laine de verre : Utilisée pour l’isolation des tuyauteries et des chambres froides, elle présente de bonnes propriétés thermiques et acoustiques.
- Polystyrène expansé (PSE) : Matériau léger et efficace pour l’isolation des chambres froides .
3.2 Techniques d’Isolation
- Calorifugeage : Consiste à envelopper les tuyauteries avec des matériaux isolants pour réduire les pertes de chaleur .
- Isolation continue : Assure une couverture complète sans interruption pour éviter les ponts thermiques.
- Utilisation de jaquettes démontables : Facilitent la maintenance tout en maintenant une isolation efficace .
4. Bonnes Pratiques pour une Isolation Thermique Optimale
4.1 Planification et Conception
Dès la phase de conception, intégrer des solutions d’isolation adaptées aux besoins spécifiques de l’installation permet d’optimiser l’efficacité énergétique.
4.2 Maintenance Régulière
Mettre en place un programme de maintenance préventive pour inspecter et entretenir les matériaux isolants assure leur performance sur le long terme.
4.3 Formation du Personnel
Former le personnel aux bonnes pratiques d’installation et de maintenance de l’isolation thermique contribue à prévenir les erreurs et à maintenir une efficacité optimale.
Améliorer l’isolation thermique des installations industrielles et tertiaires est une démarche essentielle pour réduire les pertes énergétiques, optimiser les performances des systèmes et diminuer les coûts d’exploitation. En ciblant les zones prioritaires telles que les réseaux d’eau glacée, les réservoirs tampons et les chambres froides, et en adoptant des matériaux et techniques d’isolation appropriés, il est possible de réaliser des économies significatives et de contribuer à la durabilité des installations.
En somme, l’ingénierie des fluides industriels est une discipline importante et diversifiée qui joue un rôle clé dans de nombreuses industries. Elle nécessite une expertise technique et une connaissance approfondie des systèmes de circulation des fluides, de la thermodynamique, de la mécanique des fluides, de la régulation et du contrôle des processus, ainsi que de la sécurité.
Notre blog est une ressource complète pour tout ce qui concerne les fluides industriels. Nous vous encourageons à explorer nos articles, nos guides pratiques et nos ressources de formation pour approfondir vos connaissances et améliorer vos performances énergétiques. N’hésitez pas à nous contacter pour bénéficier de nos services d’ingénierie personnalisés ou pour trouver les produits dont vous avez besoin via notre site de commerce en ligne. Ensemble, nous pouvons aller plus loin dans l’apprentissage et réaliser des économies d’énergie significatives. Contactez-nous dès aujourd’hui à l’adresse suivante :
- Guide pour choisir un groupe froid industriel
- Lien : Exemple de schémas d’installation
- Lien : Calcul de la puissance nécessaire et facteurs de corrections usuels
- Le Guide Ultime du Choix des Compresseurs Frigorifiques : Optimisation, Puissance et Régulation
- Installation optimale de groupes froids industriels : Pratiques essentielles et paramètres clés
- Guide : La mise en service initiale d’un groupe froid industriel
- Les Applications du Refroidissement Industriel dans Divers Secteurs
- Guide Pratique pour le Choix d’un Groupe Froid Industriel : Calculs, Installations, Méthodes, Besoins et Critères Essentiels
- Optimiser l’Efficacité Énergétique : Deux Méthodes Ingénieuses pour Récupérer la Chaleur d’un Groupe Froid Industriel
- Guide Pratique : Récupération de Chaleur sur Groupe Froid – Avantages et Mise en Œuvre
- Innovations et Stratégies Avancées dans le Refroidissement Industriel: Vers une Ère Durable et Efficace
- Optimisation Cruciale: Les Répercussions d’un Réseau Industriel Mal Équilibré sur la Performance et la Sécurité
- Optimisation du Dimensionnement des Tuyauteries : Préserver la Pression et Réduire les Pertes de Charge
- Calculs et dimensionnement, installation, optimisation et Maintenance des Groupes Froids Industriels : Guide Complet pour Calcul de Puissance, Facteurs de Correction, et Technologies de Contrôle
- La conception d’un système de refroidissement industriel (Industrial Cooling System)
- Révolutionner le Froid Industriel et le Refroidissement Process avec l’IoT et l’IA : Entre Solutions High Tech, Low Tech, et Approches Hybrides
- Optimiser le Refroidissement Process avec l’IoT et l’IA : Révolutions et Techniques pour les Groupes Froids et Groupes d’Eau Glacée Industriels
- Révolution Technologique des Groupes Froids Industriels et Groupes d’Eau Glacée : Quand l’IA et les IoT Façonnent l’Avenir du Refroidissement Industriel
- FAQ : Groupes Froids Industriels et au Refroidissement Process
- Questions / réponses fréquemment posées sur le thème du refroidissement de process, incluant l’eau glacée, le froid industriel, les groupes froids, et les groupes d’eau glacée
- Quelles sont les erreurs courantes à éviter lors du choix d’un groupe froid industriel pour le refroidissement de son process ?
- Refroidissement Industriel : L’Essentiel sur les Groupes Frigorifiques et les Groupes d’Eau Glacée
- Lien: Notions de base
- Lie0n : Fonctionnement des systèmes de réfrigération
- Lien : applications du froid industriel
- Lien : Avantages et inconvénients
- Lien : En conclusion, le froid industriel est un élément clé de nombreuses industries modernes
- Lien : mesure de débit ultrasonique
- Mesure de Débit d’Eau par Ultrasons : Optimisation des Process Industriels
- Lien : Vitesse des fluides dans les tuyauteries
- Pour réaliser des économies d’énergie avec les installations d’eau glacée (froid industriel)
- Lien : Retrouver la performance de vos échangeurs avec le peigne frigoriste (groupe froid industriel, sécheur air comprimé, …)
- Lien : Réfractomètre : Mesurez facilement la concentration en glycol essentielle pour assurer la sécurité et la performance des installations industrielles
- Lien : Analyse d’huile des équipements : Optimisez la maintenance industrielle (compresseur air comprimé, groupe froid industriel, …)
- Les avantages de la connectivité IoT et I.A. dans les groupes froids industriels : Comment tirer parti des données pour améliorer les performances
- Les tendances émergentes dans les groupes froids industriels : Les nouvelles technologies qui transforment l’industrie du refroidissement
- La sélection du groupe froid industriel adapté à vos besoins : Guide d’achat et recommandations pour une solution optimale
- La sécurité dans les groupes froids industriels : Conseils pour prévenir les accidents et assurer la conformité aux normes de sécurité
- Maximisez la fiabilité de votre groupe froid industriel : Les meilleures pratiques pour éviter les pannes et les temps d’arrêt coûteux
- La maintenance préventive des groupes froids industriels : Astuces pour prolonger la durée de vie de votre équipement
- Les solutions respectueuses de l’environnement pour les groupes froids industriels : Astuces pour réduire l’empreinte carbone de votre installation
- La gestion intelligente des groupes froids industriels : Comment utiliser les systèmes de contrôle avancés pour optimiser les performances
- Les dernières avancées en matière de groupes froids industriels : Les technologies innovantes qui améliorent les performances
- Groupe froid industriel : Optimisez les économies d’énergie en adaptant vos consignes de température
- Optimisez l’efficacité énergétique de votre groupe froid industriel : Astuces pratiques pour réduire la consommation d’énergie
- Maîtrisez la poussière : Astuces innovantes et simples pour protéger vos équipements avec des filtres d’air comprimé dans les environnements poussiéreu
Lien pour achats :
Supprimer les Surcharges Inutiles : Optimisez vos Installations pour des Économies d’Énergie Significatives
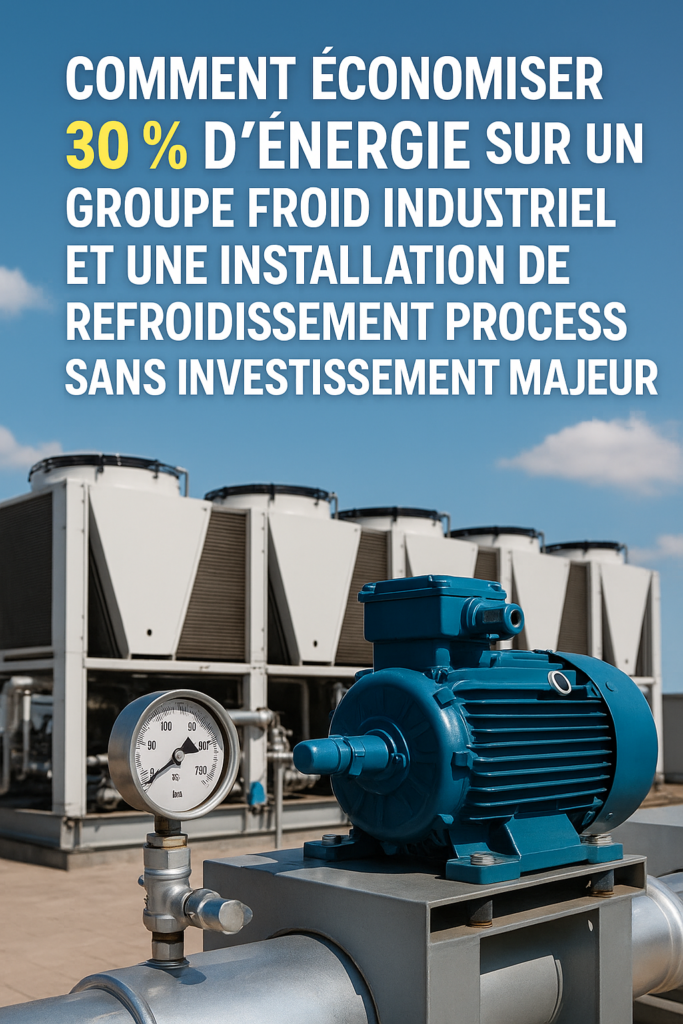
Dans les installations industrielles et tertiaires, des surcharges énergétiques inutiles peuvent survenir lorsque des équipements continuent de fonctionner sans nécessité, entraînant une consommation d’énergie superflue. Parmi les erreurs courantes figurent la circulation d’eau froide dans des équipements non utilisés et le refroidissement permanent de lignes de process arrêtées. Ces pratiques peuvent entraîner une surconsommation énergétique de 5 à 8 %, affectant la rentabilité et l’efficacité énergétique des installations.
Cet article explore les causes de ces surcharges, propose des actions concrètes pour les éliminer et présente des exemples concrets d’économies réalisées grâce à une gestion optimisée des systèmes.
Comprendre les Surcharges Inutiles
Circulation d’Eau Froide dans des Équipements Non Utilisés
Dans de nombreuses installations, l’eau froide continue de circuler dans des équipements ou des circuits qui ne sont pas en service. Cette circulation inutile maintient des pompes en fonctionnement et entraîne des pertes thermiques, augmentant la consommation d’énergie sans apporter de bénéfices opérationnels.
Refroidissement Permanent de Lignes de Process Arrêtées
Il est fréquent que des lignes de process, bien qu’arrêtées, continuent d’être refroidies en permanence. Cette pratique résulte souvent d’une absence de régulation adaptée ou d’un manque de détection de l’état des équipements, conduisant à une consommation énergétique inutile.
Actions Concrètes pour Éliminer les Surcharges Inutiles
Installer des Vannes Manuelles ou Électrovannes
L’installation de vannes manuelles ou d’électrovannes permet de contrôler efficacement la circulation des fluides dans les circuits. Les électrovannes, en particulier, offrent une automatisation du contrôle, s’ouvrant ou se fermant en fonction des besoins opérationnels, ce qui réduit les pertes énergétiques. Selon Tameson, les électrovannes sont utilisées pour fermer, ouvrir, doser, distribuer ou mélanger le flux de gaz ou de liquide dans une conduite .Tameson.fr
Ajouter un Pilotage Simple avec Détecteurs de Fonctionnement
L’intégration de détecteurs de fonctionnement permet de déterminer l’état des équipements (en marche ou à l’arrêt) et de piloter les vannes en conséquence. Cette automatisation assure que le refroidissement ou la circulation de fluides ne se produit que lorsque cela est nécessaire, évitant ainsi les surconsommations.
Exemple Concret : Économie Immédiate de 5 à 8 %
Prenons l’exemple d’une ligne de production qui, bien qu’à l’arrêt, continue de recevoir de l’eau froide pour son refroidissement. En installant une électrovanne pilotée par un détecteur de fonctionnement, le refroidissement est automatiquement interrompu lorsque la ligne est inactive. Cette simple modification peut entraîner une économie immédiate de 5 à 8 % sur la consommation énergétique liée au refroidissement.
Bonnes Pratiques pour une Gestion Énergétique Optimisée
Réaliser un Audit Énergétique
Un audit énergétique permet d’identifier les points de surconsommation et de proposer des solutions adaptées pour améliorer l’efficacité énergétique des installations.
Former le Personnel
La sensibilisation et la formation du personnel à l’importance de l’efficacité énergétique et aux bonnes pratiques de gestion des équipements sont essentielles pour maintenir des économies d’énergie sur le long terme.
Mettre en Place une Maintenance Préventive
Une maintenance régulière des équipements, y compris la vérification des vannes et des détecteurs, assure leur bon fonctionnement et prévient les dysfonctionnements pouvant entraîner des surconsommations.
La suppression des surcharges inutiles dans les installations industrielles et tertiaires est une démarche essentielle pour améliorer l’efficacité énergétique et réduire les coûts d’exploitation. En identifiant les sources de surconsommation, en installant des systèmes de régulation adaptés et en adoptant des bonnes pratiques de gestion, il est possible de réaliser des économies significatives tout en contribuant à la préservation de l’environnement.
En somme, l’ingénierie des fluides industriels est une discipline importante et diversifiée qui joue un rôle clé dans de nombreuses industries. Elle nécessite une expertise technique et une connaissance approfondie des systèmes de circulation des fluides, de la thermodynamique, de la mécanique des fluides, de la régulation et du contrôle des processus, ainsi que de la sécurité.
Notre blog est une ressource complète pour tout ce qui concerne les fluides industriels. Nous vous encourageons à explorer nos articles, nos guides pratiques et nos ressources de formation pour approfondir vos connaissances et améliorer vos performances énergétiques. N’hésitez pas à nous contacter pour bénéficier de nos services d’ingénierie personnalisés ou pour trouver les produits dont vous avez besoin via notre site de commerce en ligne. Ensemble, nous pouvons aller plus loin dans l’apprentissage et réaliser des économies d’énergie significatives. Contactez-nous dès aujourd’hui à l’adresse suivante :
- Guide pour choisir un groupe froid industriel
- Lien : Exemple de schémas d’installation
- Lien : Calcul de la puissance nécessaire et facteurs de corrections usuels
- Le Guide Ultime du Choix des Compresseurs Frigorifiques : Optimisation, Puissance et Régulation
- Installation optimale de groupes froids industriels : Pratiques essentielles et paramètres clés
- Guide : La mise en service initiale d’un groupe froid industriel
- Les Applications du Refroidissement Industriel dans Divers Secteurs
- Guide Pratique pour le Choix d’un Groupe Froid Industriel : Calculs, Installations, Méthodes, Besoins et Critères Essentiels
- Optimiser l’Efficacité Énergétique : Deux Méthodes Ingénieuses pour Récupérer la Chaleur d’un Groupe Froid Industriel
- Guide Pratique : Récupération de Chaleur sur Groupe Froid – Avantages et Mise en Œuvre
- Innovations et Stratégies Avancées dans le Refroidissement Industriel: Vers une Ère Durable et Efficace
- Optimisation Cruciale: Les Répercussions d’un Réseau Industriel Mal Équilibré sur la Performance et la Sécurité
- Optimisation du Dimensionnement des Tuyauteries : Préserver la Pression et Réduire les Pertes de Charge
- Calculs et dimensionnement, installation, optimisation et Maintenance des Groupes Froids Industriels : Guide Complet pour Calcul de Puissance, Facteurs de Correction, et Technologies de Contrôle
- La conception d’un système de refroidissement industriel (Industrial Cooling System)
- Révolutionner le Froid Industriel et le Refroidissement Process avec l’IoT et l’IA : Entre Solutions High Tech, Low Tech, et Approches Hybrides
- Optimiser le Refroidissement Process avec l’IoT et l’IA : Révolutions et Techniques pour les Groupes Froids et Groupes d’Eau Glacée Industriels
- Révolution Technologique des Groupes Froids Industriels et Groupes d’Eau Glacée : Quand l’IA et les IoT Façonnent l’Avenir du Refroidissement Industriel
- FAQ : Groupes Froids Industriels et au Refroidissement Process
- Questions / réponses fréquemment posées sur le thème du refroidissement de process, incluant l’eau glacée, le froid industriel, les groupes froids, et les groupes d’eau glacée
- Quelles sont les erreurs courantes à éviter lors du choix d’un groupe froid industriel pour le refroidissement de son process ?
- Refroidissement Industriel : L’Essentiel sur les Groupes Frigorifiques et les Groupes d’Eau Glacée
- Lien: Notions de base
- Lie0n : Fonctionnement des systèmes de réfrigération
- Lien : applications du froid industriel
- Lien : Avantages et inconvénients
- Lien : En conclusion, le froid industriel est un élément clé de nombreuses industries modernes
- Lien : mesure de débit ultrasonique
- Mesure de Débit d’Eau par Ultrasons : Optimisation des Process Industriels
- Lien : Vitesse des fluides dans les tuyauteries
- Pour réaliser des économies d’énergie avec les installations d’eau glacée (froid industriel)
- Lien : Retrouver la performance de vos échangeurs avec le peigne frigoriste (groupe froid industriel, sécheur air comprimé, …)
- Lien : Réfractomètre : Mesurez facilement la concentration en glycol essentielle pour assurer la sécurité et la performance des installations industrielles
- Lien : Analyse d’huile des équipements : Optimisez la maintenance industrielle (compresseur air comprimé, groupe froid industriel, …)
- Les avantages de la connectivité IoT et I.A. dans les groupes froids industriels : Comment tirer parti des données pour améliorer les performances
- Les tendances émergentes dans les groupes froids industriels : Les nouvelles technologies qui transforment l’industrie du refroidissement
- La sélection du groupe froid industriel adapté à vos besoins : Guide d’achat et recommandations pour une solution optimale
- La sécurité dans les groupes froids industriels : Conseils pour prévenir les accidents et assurer la conformité aux normes de sécurité
- Maximisez la fiabilité de votre groupe froid industriel : Les meilleures pratiques pour éviter les pannes et les temps d’arrêt coûteux
- La maintenance préventive des groupes froids industriels : Astuces pour prolonger la durée de vie de votre équipement
- Les solutions respectueuses de l’environnement pour les groupes froids industriels : Astuces pour réduire l’empreinte carbone de votre installation
- La gestion intelligente des groupes froids industriels : Comment utiliser les systèmes de contrôle avancés pour optimiser les performances
- Les dernières avancées en matière de groupes froids industriels : Les technologies innovantes qui améliorent les performances
- Groupe froid industriel : Optimisez les économies d’énergie en adaptant vos consignes de température
- Optimisez l’efficacité énergétique de votre groupe froid industriel : Astuces pratiques pour réduire la consommation d’énergie
- Maîtrisez la poussière : Astuces innovantes et simples pour protéger vos équipements avec des filtres d’air comprimé dans les environnements poussiéreu
Lien pour achats :
Réglage Optimal des Ventilateurs dans les Condenseurs Aérauliques : Économies d’Énergie et Performance Maximale
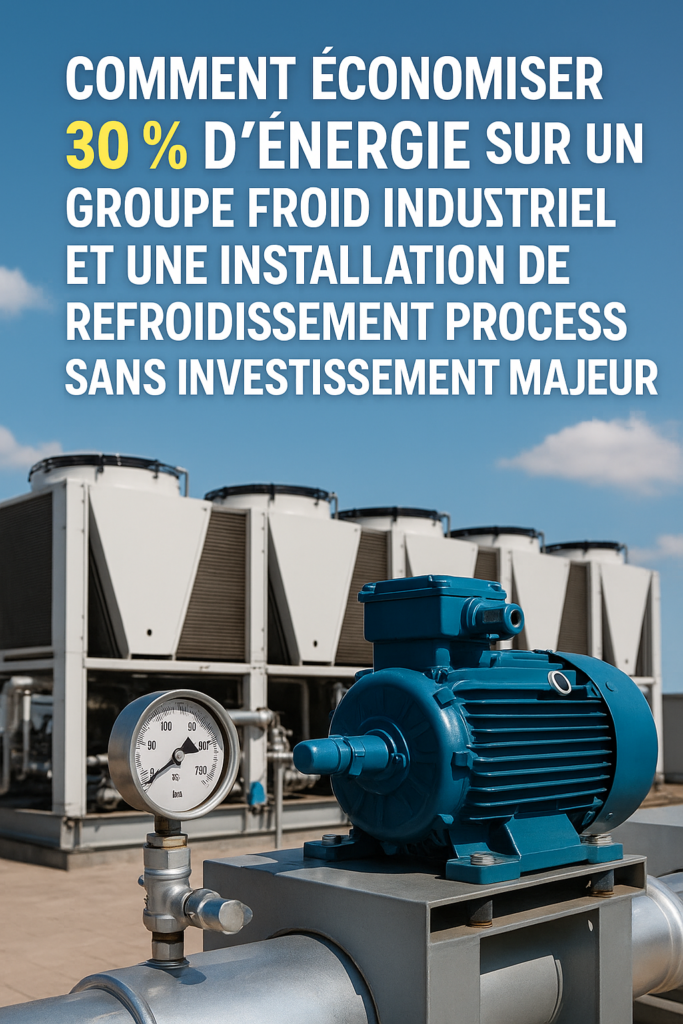
Dans les systèmes de réfrigération industrielle, les condenseurs aérauliques jouent un rôle crucial en dissipant la chaleur extraite des espaces refroidis. Leur efficacité dépend en grande partie du bon fonctionnement des ventilateurs qui les équipent. Un réglage optimal de ces ventilateurs peut conduire à des économies d’énergie significatives, améliorer la performance du système et prolonger la durée de vie des équipements.
Cet article explore les meilleures pratiques pour optimiser le réglage des ventilateurs dans les condenseurs aérauliques, en mettant l’accent sur l’utilisation de la vitesse variable, l’optimisation des seuils de déclenchement et la définition de rampes de modulation douces.
1. Comprendre le Fonctionnement des Ventilateurs dans les Condenseurs Aérauliques
Les condenseurs aérauliques utilisent des ventilateurs pour forcer l’air à travers les serpentins du condenseur, facilitant ainsi le transfert de chaleur du réfrigérant vers l’air ambiant. Le contrôle précis de la vitesse des ventilateurs est essentiel pour maintenir une pression de condensation optimale et assurer une performance énergétique efficace.
2. Utilisation de la Vitesse Variable
2.1. Avantages de la Vitesse Variable
L’intégration de variateurs de vitesse permet d’ajuster la vitesse des ventilateurs en fonction des besoins thermiques réels, plutôt que de fonctionner à pleine capacité en permanence. Cette approche offre plusieurs avantages :
- Économies d’énergie : Réduire la vitesse du ventilateur diminue la consommation d’énergie de manière exponentielle. Par exemple, réduire de moitié la vitesse d’un ventilateur peut diviser par huit la consommation électrique du moteur .Energie SPW
- Réduction du bruit : Une vitesse de fonctionnement plus basse entraîne une diminution du niveau sonore, améliorant ainsi le confort acoustique.
- Prolongation de la durée de vie des équipements : Moins de stress mécanique sur les composants prolonge leur durée de vie.
2.2. Mise en Œuvre
Pour tirer parti de la vitesse variable, il est essentiel d’utiliser des moteurs compatibles avec les variateurs de fréquence et de configurer correctement les paramètres de contrôle pour répondre aux besoins spécifiques de l’installation.
3. Optimisation des Seuils de Déclenchement
3.1. Importance des Seuils de Déclenchement
Les seuils de déclenchement déterminent à quelle température ou pression les ventilateurs commencent à fonctionner. Des seuils mal configurés peuvent entraîner un fonctionnement inutile des ventilateurs, augmentant ainsi la consommation d’énergie.
3.2. Meilleures Pratiques
- Analyse des besoins réels : Évaluer les conditions de fonctionnement pour déterminer les seuils optimaux.
- Utilisation de capteurs précis : Intégrer des capteurs de température et de pression fiables pour une détection précise des conditions de déclenchement.
- Réglage dynamique : Adapter les seuils en fonction des variations saisonnières ou des charges thermiques fluctuantes.
4. Définition de Rampes de Modulation Douces
4.1. Qu’est-ce qu’une Rampe de Modulation ?
Une rampe de modulation définit la manière dont la vitesse du ventilateur augmente ou diminue en réponse aux changements de température ou de pression. Des rampes trop abruptes peuvent entraîner des cycles de marche/arrêt fréquents, réduisant l’efficacité énergétique et augmentant l’usure des composants.
4.2. Mise en Place de Rampes Douces
- Paramétrage progressif : Configurer les variateurs de vitesse pour permettre des augmentations ou diminutions graduelles de la vitesse.
- Évitement des à-coups : Une modulation douce réduit les chocs mécaniques, prolongeant ainsi la durée de vie des ventilateurs.
- Amélioration de la stabilité thermique : Des transitions en douceur contribuent à maintenir des conditions thermiques stables dans l’installation.
5. Économies d’Énergie Potentielles
L’optimisation du réglage des ventilateurs peut conduire à des économies d’énergie significatives. Selon les études, chaque degré de réduction de la pression de condensation permet de gagner 1 à 2 % de consommation électrique . De plus, l’utilisation de la vitesse variable et de rampes de modulation douces peut entraîner jusqu’à 10 % d’économie supplémentaire sur le fonctionnement auxiliaire.
6. Astuces Pratiques et Bonnes Pratiques
6.1. Maintenance Régulière
Un entretien régulier des ventilateurs et des condenseurs est essentiel pour maintenir une performance optimale. Cela inclut le nettoyage des ailettes, la vérification des connexions électriques et l’inspection des composants mécaniques.
6.2. Surveillance Continue
Mettre en place un système de surveillance permet de détecter rapidement les anomalies et d’ajuster les paramètres de fonctionnement en temps réel.
6.3. Formation du Personnel
Assurer que le personnel d’exploitation est formé aux meilleures pratiques de réglage et de maintenance des ventilateurs contribue à une gestion efficace du système.
L’optimisation du réglage des ventilateurs dans les condenseurs aérauliques est une stratégie efficace pour améliorer la performance énergétique, réduire les coûts d’exploitation et prolonger la durée de vie des équipements. En mettant en œuvre des pratiques telles que l’utilisation de la vitesse variable, l’optimisation des seuils de déclenchement et la définition de rampes de modulation douces, les installations peuvent réaliser des économies d’énergie significatives tout en maintenant des conditions de fonctionnement optimales.
En somme, l’ingénierie des fluides industriels est une discipline importante et diversifiée qui joue un rôle clé dans de nombreuses industries. Elle nécessite une expertise technique et une connaissance approfondie des systèmes de circulation des fluides, de la thermodynamique, de la mécanique des fluides, de la régulation et du contrôle des processus, ainsi que de la sécurité.
Notre blog est une ressource complète pour tout ce qui concerne les fluides industriels. Nous vous encourageons à explorer nos articles, nos guides pratiques et nos ressources de formation pour approfondir vos connaissances et améliorer vos performances énergétiques. N’hésitez pas à nous contacter pour bénéficier de nos services d’ingénierie personnalisés ou pour trouver les produits dont vous avez besoin via notre site de commerce en ligne. Ensemble, nous pouvons aller plus loin dans l’apprentissage et réaliser des économies d’énergie significatives. Contactez-nous dès aujourd’hui à l’adresse suivante :
- Guide pour choisir un groupe froid industriel
- Lien : Exemple de schémas d’installation
- Lien : Calcul de la puissance nécessaire et facteurs de corrections usuels
- Le Guide Ultime du Choix des Compresseurs Frigorifiques : Optimisation, Puissance et Régulation
- Installation optimale de groupes froids industriels : Pratiques essentielles et paramètres clés
- Guide : La mise en service initiale d’un groupe froid industriel
- Les Applications du Refroidissement Industriel dans Divers Secteurs
- Guide Pratique pour le Choix d’un Groupe Froid Industriel : Calculs, Installations, Méthodes, Besoins et Critères Essentiels
- Optimiser l’Efficacité Énergétique : Deux Méthodes Ingénieuses pour Récupérer la Chaleur d’un Groupe Froid Industriel
- Guide Pratique : Récupération de Chaleur sur Groupe Froid – Avantages et Mise en Œuvre
- Innovations et Stratégies Avancées dans le Refroidissement Industriel: Vers une Ère Durable et Efficace
- Optimisation Cruciale: Les Répercussions d’un Réseau Industriel Mal Équilibré sur la Performance et la Sécurité
- Optimisation du Dimensionnement des Tuyauteries : Préserver la Pression et Réduire les Pertes de Charge
- Calculs et dimensionnement, installation, optimisation et Maintenance des Groupes Froids Industriels : Guide Complet pour Calcul de Puissance, Facteurs de Correction, et Technologies de Contrôle
- La conception d’un système de refroidissement industriel (Industrial Cooling System)
- Révolutionner le Froid Industriel et le Refroidissement Process avec l’IoT et l’IA : Entre Solutions High Tech, Low Tech, et Approches Hybrides
- Optimiser le Refroidissement Process avec l’IoT et l’IA : Révolutions et Techniques pour les Groupes Froids et Groupes d’Eau Glacée Industriels
- Révolution Technologique des Groupes Froids Industriels et Groupes d’Eau Glacée : Quand l’IA et les IoT Façonnent l’Avenir du Refroidissement Industriel
- FAQ : Groupes Froids Industriels et au Refroidissement Process
- Questions / réponses fréquemment posées sur le thème du refroidissement de process, incluant l’eau glacée, le froid industriel, les groupes froids, et les groupes d’eau glacée
- Quelles sont les erreurs courantes à éviter lors du choix d’un groupe froid industriel pour le refroidissement de son process ?
- Refroidissement Industriel : L’Essentiel sur les Groupes Frigorifiques et les Groupes d’Eau Glacée
- Lien: Notions de base
- Lie0n : Fonctionnement des systèmes de réfrigération
- Lien : applications du froid industriel
- Lien : Avantages et inconvénients
- Lien : En conclusion, le froid industriel est un élément clé de nombreuses industries modernes
- Lien : mesure de débit ultrasonique
- Mesure de Débit d’Eau par Ultrasons : Optimisation des Process Industriels
- Lien : Vitesse des fluides dans les tuyauteries
- Pour réaliser des économies d’énergie avec les installations d’eau glacée (froid industriel)
- Lien : Retrouver la performance de vos échangeurs avec le peigne frigoriste (groupe froid industriel, sécheur air comprimé, …)
- Lien : Réfractomètre : Mesurez facilement la concentration en glycol essentielle pour assurer la sécurité et la performance des installations industrielles
- Lien : Analyse d’huile des équipements : Optimisez la maintenance industrielle (compresseur air comprimé, groupe froid industriel, …)
- Les avantages de la connectivité IoT et I.A. dans les groupes froids industriels : Comment tirer parti des données pour améliorer les performances
- Les tendances émergentes dans les groupes froids industriels : Les nouvelles technologies qui transforment l’industrie du refroidissement
- La sélection du groupe froid industriel adapté à vos besoins : Guide d’achat et recommandations pour une solution optimale
- La sécurité dans les groupes froids industriels : Conseils pour prévenir les accidents et assurer la conformité aux normes de sécurité
- Maximisez la fiabilité de votre groupe froid industriel : Les meilleures pratiques pour éviter les pannes et les temps d’arrêt coûteux
- La maintenance préventive des groupes froids industriels : Astuces pour prolonger la durée de vie de votre équipement
- Les solutions respectueuses de l’environnement pour les groupes froids industriels : Astuces pour réduire l’empreinte carbone de votre installation
- La gestion intelligente des groupes froids industriels : Comment utiliser les systèmes de contrôle avancés pour optimiser les performances
- Les dernières avancées en matière de groupes froids industriels : Les technologies innovantes qui améliorent les performances
- Groupe froid industriel : Optimisez les économies d’énergie en adaptant vos consignes de température
- Optimisez l’efficacité énergétique de votre groupe froid industriel : Astuces pratiques pour réduire la consommation d’énergie
- Maîtrisez la poussière : Astuces innovantes et simples pour protéger vos équipements avec des filtres d’air comprimé dans les environnements poussiéreu
Lien pour achats :
Optimiser la Séquence des Compresseurs Frigorifiques : Performances, Économies et Fiabilité à la Clé
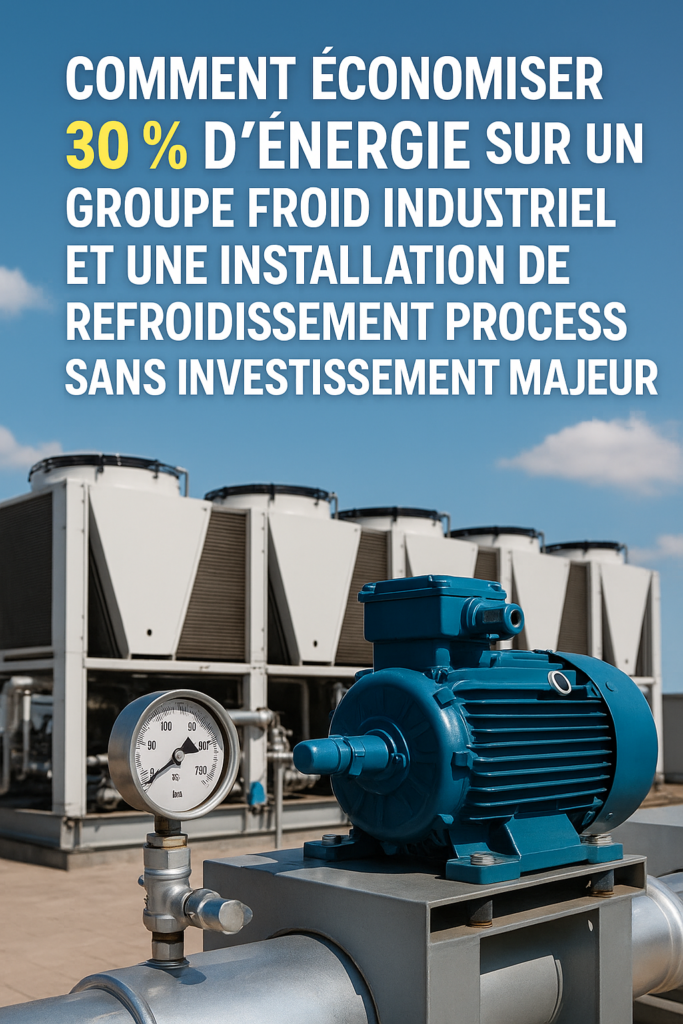
Dans les installations de production de froid industriel, le choix de l’ordre de fonctionnement des compresseurs frigorifiques peut faire toute la différence entre une usine performante… et une machine énergivore.
Quand plusieurs groupes frigorifiques sont en place — que ce soit pour des raisons de redondance, d’historique d’investissement ou d’évolutivité — il est crucial d’organiser leur mise en service selon des critères d’efficacité énergétique, de disponibilité et de logique de secours.
Dans cet article complet, découvrez comment optimiser la séquence de vos compresseurs frigorifiques, réduire vos coûts, limiter l’usure prématurée, et éviter les pièges courants dans la gestion multi-groupes.
1. Pourquoi optimiser la séquence des compresseurs frigorifiques ?
Dans une installation où plusieurs compresseurs frigorifiques coexistent, l’ordre de démarrage (ou de priorisation) de ces machines est tout sauf anodin.
En effet :
- Chaque machine a un rendement spécifique selon sa technologie et son âge.
- Leur fonctionnement parallèle peut entraîner des inefficacités énergétiques.
- Une mauvaise séquence peut entraîner une usure prématurée des compresseurs les moins performants.
- Le fait de faire fonctionner tous les groupes simultanément peut saturer l’alimentation électrique, augmenter les cycles de marche/arrêt, ou détériorer la stabilité thermique.
💡 Bon à savoir : Un mauvais ordonnancement des compresseurs frigorifiques peut engendrer jusqu’à 20 à 30 % de surconsommation d’énergie dans certaines configurations.
2. Comprendre la logique de séquençage principal/secondaire
La première règle fondamentale est simple :
Faire fonctionner en priorité le compresseur le plus efficace, et garder les autres en réserve (secours ou complément).
Cela suppose d’identifier clairement :
- Le compresseur le plus récent
- Le compresseur le plus performant énergétiquement
- Le compresseur ayant le coût d’entretien le plus bas par heure de fonctionnement
- Le compresseur conçu pour travailler en continu
Les autres compresseurs seront donc configurés pour :
- Prendre le relais en cas de défaillance
- Être appelés en complément uniquement en cas de pic de charge
3. Analyse énergétique : quel compresseur en priorité ?
Avant de séquencer quoi que ce soit, il faut mesurer. Voici quelques indicateurs à prendre en compte :
🔍 1. COP (Coefficient de performance)
Plus le COP est élevé, moins le compresseur consomme pour une puissance frigorifique donnée.
🔍 2. Âge et technologie
Un compresseur scroll ou à vis récent est souvent bien plus performant qu’un compresseur à piston des années 90.
🔍 3. Entretien et fiabilité
Un compresseur peu entretenu ou sujet à des arrêts fréquents doit être gardé en secours, non en usage courant.
🔍 4. Consommation spécifique (kWh/tonne de froid)
C’est un excellent indicateur pratique pour déterminer le coût réel d’exploitation de chaque compresseur.
⚠️ Astuce : N’utilisez jamais deux petits compresseurs peu efficaces en parallèle si un seul groupe plus grand et plus performant peut couvrir la charge.
4. Exemple de mauvaise configuration : cas concret à éviter
Voici un exemple classique :
Contexte :
- 1 compresseur récent de 100 kW frigorifiques (COP 4, technologie scroll)
- 2 compresseurs anciens de 50 kW chacun (COP 2, technologie à piston)
Erreur courante :
L’opérateur configure tous les compresseurs en fonctionnement alterné automatique, pour « répartir l’usure ».
Conséquences :
- En fonctionnement à charge partielle, les deux anciens compresseurs démarrent simultanément au lieu du nouveau.
- Surconsommation électrique importante.
- Augmentation de la fréquence de maintenance sur les machines anciennes.
- Mauvaise stabilisation thermique de l’installation.
✅ Bonne pratique : Prioriser le compresseur scroll de 100 kW en « maître », les deux autres en « esclaves », pour ne les activer qu’en cas de surcharge ou d’urgence.
5. Exemples d’optimisation en milieu industriel
🏭 Exemple 1 : Agroalimentaire
Dans une laiterie, un compresseur principal alimente en froid les cuves de stockage du lait. En cas de pic de demande (lavage NEP, pic de production), un compresseur secondaire démarre automatiquement pendant les heures de charge uniquement.
Résultat :
- Réduction de la facture énergétique de 12 %
- Amélioration de la stabilité thermique
- Moins d’arrêts imprévus
🏭 Exemple 2 : Logistique frigorifique
Dans un entrepôt de produits congelés :
- Deux compresseurs identiques sont utilisés en alternance hebdomadaire.
- En été, un compresseur à débit variable est mis en priorité pour absorber les fluctuations thermiques sans à-coups.
- L’ancienne machine tourne seulement la nuit ou en cas de dépassement de consigne.
Résultat :
- Réduction des redémarrages intempestifs
- Température plus stable dans les chambres
- Diminution des coûts d’entretien
6. Astuces pratiques pour une séquence intelligente
🔧 Installez un contrôleur de séquence automatique
Des automates programmables peuvent gérer l’ordre de démarrage selon la température ambiante, la consigne de froid, ou la charge horaire.
🔧 Programmez des plages horaires
Vous pouvez, par exemple :
- Activer le gros compresseur de jour
- Utiliser un petit compresseur silencieux de nuit
- Prévoir des relèves automatiques toutes les 48h en cas d’absence d’alarme
🔧 Adaptez à la saison
- En hiver : priorité aux groupes à air libre
- En été : bascule sur les groupes les mieux ventilés
💡 Bon à savoir : Un système de séquence dynamique permet d’adapter automatiquement le fonctionnement aux conditions climatiques et à la charge thermique réelle.
7. Pilotage automatique et séquence dynamique
Les séquenceurs intelligents modernes permettent :
- De comparer le rendement en temps réel de chaque compresseur
- De moduler la puissance en fonction de la demande
- De détecter une surchauffe, une surpression ou un dérèglement
- D’appliquer des priorités conditionnelles (température extérieure, consigne, planning de production)
Ces outils utilisent souvent des capteurs de température, de pression, de consommation électrique, et parfois l’IA embarquée pour apprendre les habitudes de l’installation.
8. Surveillance, capteurs et indicateurs clés
Pour bien piloter votre séquence, surveillez :
- Température de sortie d’évaporateur
- Pression de refoulement
- Puissance absorbée (en kW)
- COP en temps réel
- Heures de fonctionnement de chaque groupe
- Temps de réponse à une variation de consigne
Pensez à utiliser des solutions de supervision centralisée avec alertes mail/SMS pour anticiper les dérives.
9. Sécurité et redondance : garantir le secours sans excès
❗ Attention : Trop de redondance = consommation inutile. Trop peu = risque de panne globale.
La bonne approche consiste à :
- Toujours avoir au moins un groupe en secours automatique, prêt à démarrer sans délai
- Utiliser des vannes motorisées et sondes intelligentes pour commuter automatiquement
- Simuler des tests de bascule une fois par mois
- Prévoir des règles de priorités claires en cas de défaut (alarme, coupure de réseau, etc.)
10. Une logique de performance globale
L’optimisation de la séquence des compresseurs frigorifiques ne repose pas uniquement sur de la programmation. C’est un état d’esprit, une stratégie d’exploitation, et une façon de concevoir l’énergie comme un levier de performance industrielle.
Un bon séquençage :
- Réduit les coûts
- Améliore la disponibilité machine
- Prolonge la durée de vie des équipements
- Protège les installations de surcharge
- Renforce la régularité thermique
- Respecte les enjeux RSE en diminuant les émissions indirectes
🧠 Récapitulatif des points-clés
- Priorisez le compresseur le plus performant énergétiquement
- Gardez les autres en secours ou en appoint
- Ne jamais faire tourner en parallèle deux groupes inefficaces
- Utilisez la supervision et les capteurs pour ajuster en temps réel
- Intégrez les conditions climatiques, les horaires et la production dans la logique de séquence
- Testez vos bascules, évitez les redondances excessives
En somme, l’ingénierie des fluides industriels est une discipline importante et diversifiée qui joue un rôle clé dans de nombreuses industries. Elle nécessite une expertise technique et une connaissance approfondie des systèmes de circulation des fluides, de la thermodynamique, de la mécanique des fluides, de la régulation et du contrôle des processus, ainsi que de la sécurité.
Notre blog est une ressource complète pour tout ce qui concerne les fluides industriels. Nous vous encourageons à explorer nos articles, nos guides pratiques et nos ressources de formation pour approfondir vos connaissances et améliorer vos performances énergétiques. N’hésitez pas à nous contacter pour bénéficier de nos services d’ingénierie personnalisés ou pour trouver les produits dont vous avez besoin via notre site de commerce en ligne. Ensemble, nous pouvons aller plus loin dans l’apprentissage et réaliser des économies d’énergie significatives. Contactez-nous dès aujourd’hui à l’adresse suivante :
- Guide pour choisir un groupe froid industriel
- Lien : Exemple de schémas d’installation
- Lien : Calcul de la puissance nécessaire et facteurs de corrections usuels
- Le Guide Ultime du Choix des Compresseurs Frigorifiques : Optimisation, Puissance et Régulation
- Installation optimale de groupes froids industriels : Pratiques essentielles et paramètres clés
- Guide : La mise en service initiale d’un groupe froid industriel
- Les Applications du Refroidissement Industriel dans Divers Secteurs
- Guide Pratique pour le Choix d’un Groupe Froid Industriel : Calculs, Installations, Méthodes, Besoins et Critères Essentiels
- Optimiser l’Efficacité Énergétique : Deux Méthodes Ingénieuses pour Récupérer la Chaleur d’un Groupe Froid Industriel
- Guide Pratique : Récupération de Chaleur sur Groupe Froid – Avantages et Mise en Œuvre
- Innovations et Stratégies Avancées dans le Refroidissement Industriel: Vers une Ère Durable et Efficace
- Optimisation Cruciale: Les Répercussions d’un Réseau Industriel Mal Équilibré sur la Performance et la Sécurité
- Optimisation du Dimensionnement des Tuyauteries : Préserver la Pression et Réduire les Pertes de Charge
- Calculs et dimensionnement, installation, optimisation et Maintenance des Groupes Froids Industriels : Guide Complet pour Calcul de Puissance, Facteurs de Correction, et Technologies de Contrôle
- La conception d’un système de refroidissement industriel (Industrial Cooling System)
- Révolutionner le Froid Industriel et le Refroidissement Process avec l’IoT et l’IA : Entre Solutions High Tech, Low Tech, et Approches Hybrides
- Optimiser le Refroidissement Process avec l’IoT et l’IA : Révolutions et Techniques pour les Groupes Froids et Groupes d’Eau Glacée Industriels
- Révolution Technologique des Groupes Froids Industriels et Groupes d’Eau Glacée : Quand l’IA et les IoT Façonnent l’Avenir du Refroidissement Industriel
- FAQ : Groupes Froids Industriels et au Refroidissement Process
- Questions / réponses fréquemment posées sur le thème du refroidissement de process, incluant l’eau glacée, le froid industriel, les groupes froids, et les groupes d’eau glacée
- Quelles sont les erreurs courantes à éviter lors du choix d’un groupe froid industriel pour le refroidissement de son process ?
- Refroidissement Industriel : L’Essentiel sur les Groupes Frigorifiques et les Groupes d’Eau Glacée
- Lien: Notions de base
- Lie0n : Fonctionnement des systèmes de réfrigération
- Lien : applications du froid industriel
- Lien : Avantages et inconvénients
- Lien : En conclusion, le froid industriel est un élément clé de nombreuses industries modernes
- Lien : mesure de débit ultrasonique
- Mesure de Débit d’Eau par Ultrasons : Optimisation des Process Industriels
- Lien : Vitesse des fluides dans les tuyauteries
- Pour réaliser des économies d’énergie avec les installations d’eau glacée (froid industriel)
- Lien : Retrouver la performance de vos échangeurs avec le peigne frigoriste (groupe froid industriel, sécheur air comprimé, …)
- Lien : Réfractomètre : Mesurez facilement la concentration en glycol essentielle pour assurer la sécurité et la performance des installations industrielles
- Lien : Analyse d’huile des équipements : Optimisez la maintenance industrielle (compresseur air comprimé, groupe froid industriel, …)
- Les avantages de la connectivité IoT et I.A. dans les groupes froids industriels : Comment tirer parti des données pour améliorer les performances
- Les tendances émergentes dans les groupes froids industriels : Les nouvelles technologies qui transforment l’industrie du refroidissement
- La sélection du groupe froid industriel adapté à vos besoins : Guide d’achat et recommandations pour une solution optimale
- La sécurité dans les groupes froids industriels : Conseils pour prévenir les accidents et assurer la conformité aux normes de sécurité
- Maximisez la fiabilité de votre groupe froid industriel : Les meilleures pratiques pour éviter les pannes et les temps d’arrêt coûteux
- La maintenance préventive des groupes froids industriels : Astuces pour prolonger la durée de vie de votre équipement
- Les solutions respectueuses de l’environnement pour les groupes froids industriels : Astuces pour réduire l’empreinte carbone de votre installation
- La gestion intelligente des groupes froids industriels : Comment utiliser les systèmes de contrôle avancés pour optimiser les performances
- Les dernières avancées en matière de groupes froids industriels : Les technologies innovantes qui améliorent les performances
- Groupe froid industriel : Optimisez les économies d’énergie en adaptant vos consignes de température
- Optimisez l’efficacité énergétique de votre groupe froid industriel : Astuces pratiques pour réduire la consommation d’énergie
- Maîtrisez la poussière : Astuces innovantes et simples pour protéger vos équipements avec des filtres d’air comprimé dans les environnements poussiéreu
Lien pour achats :
Assurer un Bon Entretien des Échangeurs Thermiques : Le Guide Ultime pour Éviter la Surchauffe et Réduire les Coûts Énergétiques
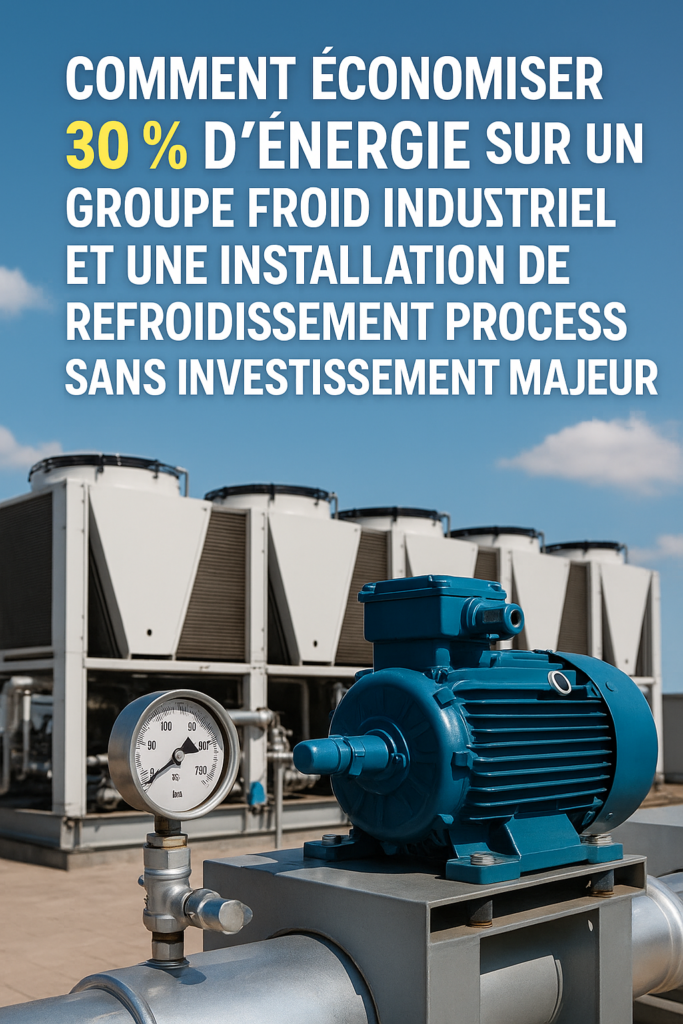
L’entretien régulier des échangeurs thermiques est une étape cruciale dans la performance énergétique des installations industrielles, qu’il s’agisse de groupes froids, de compresseurs d’air ou de systèmes HVAC. Trop souvent négligée, cette opération peut pourtant éviter bien des déconvenues : pannes coûteuses, surconsommation électrique, baisse de rendement, voire arrêt brutal des équipements.
Un condenseur encrassé de seulement 2 mm de tartre peut suffire à provoquer une surchauffe du compresseur de 10 % ! C’est dire l’impact concret de cette problématique.
Dans cet article complet, nous allons passer en revue les meilleures pratiques, les erreurs à éviter, les bons réflexes à adopter pour garantir un entretien efficace et durable de vos échangeurs thermiques.
1. Comprendre le rôle des échangeurs thermiques
Les échangeurs thermiques sont les organes de transfert de chaleur entre deux fluides de nature différente. Dans les installations industrielles, on retrouve principalement :
- Les condenseurs aérauliques : échange chaleur/air
- Les condenseurs hydrauliques : échange chaleur/eau
- Les évaporateurs
- Les échangeurs à plaques, tubulaires, coaxiaux
Ils permettent d’optimiser les cycles thermodynamiques (compression-détente), et donc de réduire la consommation énergétique globale. Un bon rendement d’échange thermique est synonyme de performances stables et de longévité accrue des machines.
2. Les conséquences d’un encrassement
Un échangeur encrassé, c’est :
- Une résistance accrue au transfert thermique
- Une augmentation de la pression de condensation ou une baisse de la capacité frigorifique
- Une surcharge du compresseur
- Une consommation électrique augmentée
- Une usure prématurée des composants
- Des pannes en cascade, surtout en période estivale
💡 Bon à savoir : Une perte d’efficacité de 10 à 20 % est rapidement atteinte si l’échangeur n’est pas entretenu régulièrement. Cela se traduit par des centaines voire des milliers d’euros de pertes annuelles.
3. Checklist complète pour un entretien efficace
Voici une checklist professionnelle pour assurer un bon entretien de vos échangeurs :
🔹 1. Nettoyage des condenseurs aérauliques
- Utiliser un nettoyeur haute pression adapté à basse puissance
- Ne pas détériorer les ailettes (pas de jet trop proche)
- Nettoyer les ventilateurs et grilles d’aspiration
- Éliminer les dépôts de poussière, pollen, insectes, graisses
🔹 2. Nettoyage des condenseurs hydrauliques
- Nettoyage chimique ou mécanique (brossage ou circulation de produits antitartre)
- Rinçage soigneux après traitement
- Vérification des joints et des plaques
🔹 3. Vérification des pertes de charge
- Comparer les valeurs de perte de charge actuelles avec celles initialement mesurées à l’installation
- Une perte de charge élevée est souvent le signe d’un encrassement interne
🔹 4. Traitement préventif du circuit d’eau
- Analyse de la dureté de l’eau
- Ajout de traitements anticalcaire, anticorrosion
- Filtration adaptée pour éviter l’introduction d’impuretés
🔹 5. Inspection visuelle
- Recherche de traces de fuites, d’oxydation, de corrosion
- Vérification des raccords et brides
4. Astuces de pro pour un nettoyage réussi
✅ Choisir le bon moment
Effectuez le nettoyage avant la période de forte sollicitation thermique, généralement au printemps, pour éviter les surchauffes estivales.
✅ Utiliser les bons produits
Évitez les détergents acides agressifs non compatibles avec les matériaux des échangeurs (aluminium, inox). Préférez des produits dégraissants neutres ou faiblement alcalins, compatibles CVC/R.
✅ Optimiser l’accessibilité
Pensez à prévoir dès l’installation des accès faciles aux condenseurs pour simplifier les futures opérations d’entretien.
💡 Bon à savoir : Un échangeur mal accessible sera rarement bien nettoyé. C’est une erreur de conception fréquente !
5. Entretien des condenseurs : spécificités selon les types
🌬️ Condenseurs aérauliques
- Sensibles à la poussière et à la pollution urbaine
- À nettoyer tous les 6 mois minimum, voire tous les 3 mois en environnement poussiéreux
- Attention à l’alignement des ailettes après nettoyage
💧 Condenseurs hydrauliques (à eau)
- Sensibles au tartre, boues, algues
- Nettoyage au moins une fois par an, parfois plus dans les régions à eau dure
- Nécessitent des traitements préventifs
6. Traitement préventif : lutter contre le tartre et la corrosion
L’eau utilisée dans les circuits hydrauliques doit être traitée. Sans cela, vous augmentez fortement le risque d’encrassement par le tartre ou la corrosion, ce qui compromet l’échange thermique.
🔹 Antitartre
- Additifs chimiques pour eau calcaire
- Adoucisseurs ou osmoseurs en amont de l’installation
🔹 Anticorrosion
- Inhibiteurs spécifiques en circuit fermé
- Surveillance régulière du pH, TH, conductivité
💡 Bon à savoir : 2 mm de tartre sur un échangeur = jusqu’à 30 % de perte d’efficacité thermique.
7. Surveillance continue : mesurer pour anticiper
L’entretien ne doit pas être uniquement curatif. Il devient intelligent lorsqu’il est prédictif, grâce à des capteurs et des outils de suivi.
📈 Mesures à surveiller :
- Pression de condensation
- Température entrée/sortie
- Pertes de charge
- Écarts de température anormaux
Utilisez un système de supervision (IoT) pour anticiper les dérives et intervenir avant qu’un problème ne devienne critique.
8. Bonnes pratiques organisationnelles en industrie
Une bonne organisation interne garantit un entretien régulier et efficace :
- Tenir un carnet d’entretien (papier ou digital)
- Planifier les interventions selon un planning semestriel ou annuel
- Former les techniciens aux bons gestes de nettoyage
- Externaliser à des prestataires spécialisés si besoin
- Impliquer le service QHSE pour évaluer les risques liés aux produits de nettoyage
9. Écogestes et maintenance durable
🌱 Réduire l’impact environnemental :
- Utiliser des produits écologiques certifiés
- Réduire la consommation d’eau pendant les nettoyages
- Optimiser la fréquence des nettoyages : ni trop peu, ni trop souvent
♻️ Bonnes pratiques écoresponsables :
- Recycler les eaux usées de nettoyage si possible
- Former à l’éco-conduite des équipements
- Éviter les dégazages intempestifs ou les fuites de réfrigérants
💡 Bon à savoir : Un échangeur bien entretenu = moins de consommation d’énergie = empreinte carbone réduite !
10. Penser efficacité globale et rentabilité
L’entretien des échangeurs n’est pas un poste de dépense inutile. C’est au contraire un levier de performance énergétique, de durabilité des équipements, et de rentabilité industrielle.
En intégrant un programme de maintenance rigoureux, en s’équipant d’outils de suivi, et en agissant préventivement, vous prolongez la durée de vie de vos machines tout en réduisant la facture énergétique de manière significative.
🚀 Résumé : les points-clés à retenir
- Un encrassement mineur peut provoquer une perte énergétique majeure
- Nettoyage régulier = gain de performance de 10 à 30 %
- Surveillez les pertes de charge et les écarts de température
- Anticipez avec des capteurs IoT et une maintenance préventive
- Formez vos équipes, tenez des registres, et utilisez les bons produits
En somme, l’ingénierie des fluides industriels est une discipline importante et diversifiée qui joue un rôle clé dans de nombreuses industries. Elle nécessite une expertise technique et une connaissance approfondie des systèmes de circulation des fluides, de la thermodynamique, de la mécanique des fluides, de la régulation et du contrôle des processus, ainsi que de la sécurité.
Notre blog est une ressource complète pour tout ce qui concerne les fluides industriels. Nous vous encourageons à explorer nos articles, nos guides pratiques et nos ressources de formation pour approfondir vos connaissances et améliorer vos performances énergétiques. N’hésitez pas à nous contacter pour bénéficier de nos services d’ingénierie personnalisés ou pour trouver les produits dont vous avez besoin via notre site de commerce en ligne. Ensemble, nous pouvons aller plus loin dans l’apprentissage et réaliser des économies d’énergie significatives. Contactez-nous dès aujourd’hui à l’adresse suivante :
- Guide pour choisir un groupe froid industriel
- Lien : Exemple de schémas d’installation
- Lien : Calcul de la puissance nécessaire et facteurs de corrections usuels
- Le Guide Ultime du Choix des Compresseurs Frigorifiques : Optimisation, Puissance et Régulation
- Installation optimale de groupes froids industriels : Pratiques essentielles et paramètres clés
- Guide : La mise en service initiale d’un groupe froid industriel
- Les Applications du Refroidissement Industriel dans Divers Secteurs
- Guide Pratique pour le Choix d’un Groupe Froid Industriel : Calculs, Installations, Méthodes, Besoins et Critères Essentiels
- Optimiser l’Efficacité Énergétique : Deux Méthodes Ingénieuses pour Récupérer la Chaleur d’un Groupe Froid Industriel
- Guide Pratique : Récupération de Chaleur sur Groupe Froid – Avantages et Mise en Œuvre
- Innovations et Stratégies Avancées dans le Refroidissement Industriel: Vers une Ère Durable et Efficace
- Optimisation Cruciale: Les Répercussions d’un Réseau Industriel Mal Équilibré sur la Performance et la Sécurité
- Optimisation du Dimensionnement des Tuyauteries : Préserver la Pression et Réduire les Pertes de Charge
- Calculs et dimensionnement, installation, optimisation et Maintenance des Groupes Froids Industriels : Guide Complet pour Calcul de Puissance, Facteurs de Correction, et Technologies de Contrôle
- La conception d’un système de refroidissement industriel (Industrial Cooling System)
- Révolutionner le Froid Industriel et le Refroidissement Process avec l’IoT et l’IA : Entre Solutions High Tech, Low Tech, et Approches Hybrides
- Optimiser le Refroidissement Process avec l’IoT et l’IA : Révolutions et Techniques pour les Groupes Froids et Groupes d’Eau Glacée Industriels
- Révolution Technologique des Groupes Froids Industriels et Groupes d’Eau Glacée : Quand l’IA et les IoT Façonnent l’Avenir du Refroidissement Industriel
- FAQ : Groupes Froids Industriels et au Refroidissement Process
- Questions / réponses fréquemment posées sur le thème du refroidissement de process, incluant l’eau glacée, le froid industriel, les groupes froids, et les groupes d’eau glacée
- Quelles sont les erreurs courantes à éviter lors du choix d’un groupe froid industriel pour le refroidissement de son process ?
- Refroidissement Industriel : L’Essentiel sur les Groupes Frigorifiques et les Groupes d’Eau Glacée
- Lien: Notions de base
- Lie0n : Fonctionnement des systèmes de réfrigération
- Lien : applications du froid industriel
- Lien : Avantages et inconvénients
- Lien : En conclusion, le froid industriel est un élément clé de nombreuses industries modernes
- Lien : mesure de débit ultrasonique
- Mesure de Débit d’Eau par Ultrasons : Optimisation des Process Industriels
- Lien : Vitesse des fluides dans les tuyauteries
- Pour réaliser des économies d’énergie avec les installations d’eau glacée (froid industriel)
- Lien : Retrouver la performance de vos échangeurs avec le peigne frigoriste (groupe froid industriel, sécheur air comprimé, …)
- Lien : Réfractomètre : Mesurez facilement la concentration en glycol essentielle pour assurer la sécurité et la performance des installations industrielles
- Lien : Analyse d’huile des équipements : Optimisez la maintenance industrielle (compresseur air comprimé, groupe froid industriel, …)
- Les avantages de la connectivité IoT et I.A. dans les groupes froids industriels : Comment tirer parti des données pour améliorer les performances
- Les tendances émergentes dans les groupes froids industriels : Les nouvelles technologies qui transforment l’industrie du refroidissement
- La sélection du groupe froid industriel adapté à vos besoins : Guide d’achat et recommandations pour une solution optimale
- La sécurité dans les groupes froids industriels : Conseils pour prévenir les accidents et assurer la conformité aux normes de sécurité
- Maximisez la fiabilité de votre groupe froid industriel : Les meilleures pratiques pour éviter les pannes et les temps d’arrêt coûteux
- La maintenance préventive des groupes froids industriels : Astuces pour prolonger la durée de vie de votre équipement
- Les solutions respectueuses de l’environnement pour les groupes froids industriels : Astuces pour réduire l’empreinte carbone de votre installation
- La gestion intelligente des groupes froids industriels : Comment utiliser les systèmes de contrôle avancés pour optimiser les performances
- Les dernières avancées en matière de groupes froids industriels : Les technologies innovantes qui améliorent les performances
- Groupe froid industriel : Optimisez les économies d’énergie en adaptant vos consignes de température
- Optimisez l’efficacité énergétique de votre groupe froid industriel : Astuces pratiques pour réduire la consommation d’énergie
- Maîtrisez la poussière : Astuces innovantes et simples pour protéger vos équipements avec des filtres d’air comprimé dans les environnements poussiéreu
Lien pour achats :
Optimiser la Température et la Pression de Condensation : Levier Clé pour Réduire Votre Consommation Énergétique
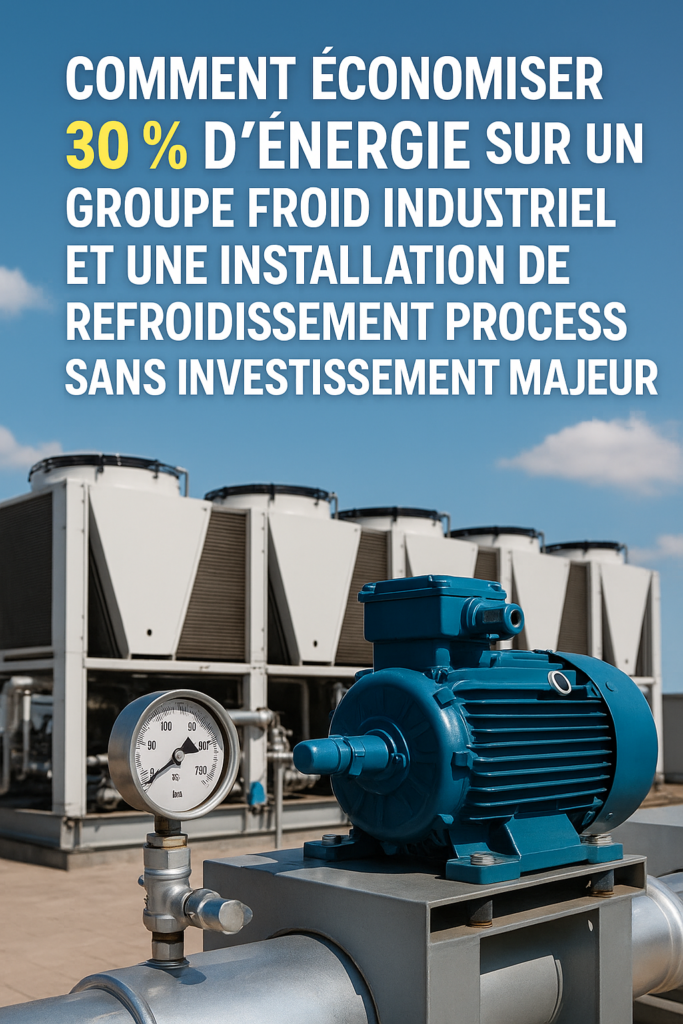
Dans le monde de la réfrigération industrielle et du froid process, l’optimisation énergétique est devenue une priorité. La performance des installations thermiques repose en grande partie sur le bon fonctionnement de l’étape de condensation, qui transforme le fluide frigorigène gazeux en liquide. Une condensation mal maîtrisée entraîne des pertes d’efficacité majeures, une consommation d’énergie excessive, et une usure prématurée du système.
Vous avez peut-être déjà entendu cette règle d’or : « Chaque degré de réduction de la pression de condensation permet d’économiser entre 1 et 2 % d’électricité. » Pourtant, dans de nombreuses installations, les condenseurs fonctionnent bien au-dessus des températures idéales – souvent à 45°C, voire plus, alors qu’un fonctionnement à 35°C est possible avec un peu de maintenance et d’ajustements.
Dans cet article, nous allons vous expliquer pourquoi et comment optimiser la température et la pression de condensation, avec des exemples concrets, des astuces techniques, des actions clés, et des bonnes pratiques faciles à mettre en œuvre.
🌡 Pourquoi la condensation est-elle si cruciale ?
La condensation est une étape fondamentale dans un cycle frigorifique. Elle a lieu dans le condenseur, lorsque le fluide frigorigène gazeux, encore chaud, est refroidi pour redevenir liquide. Cette étape libère de la chaleur, qui doit être évacuée efficacement vers l’extérieur (généralement via l’air ou l’eau).
Or, plus la température de condensation est élevée, plus le compresseur doit fournir d’effort pour compresser le fluide. Ce surtravail se traduit directement par :
- Une consommation électrique plus élevée
- Une usure mécanique accélérée
- Des performances frigorifiques amoindries
- Une augmentation du coût global d’exploitation
⚠️ Exemple chiffré : l’impact de 10°C de trop
Prenons un cas concret : une installation frigorifique fonctionnant avec un condenseur à 45°C, alors que 35°C suffiraient.
👉 Conséquence directe :
- Le compresseur va consommer 10 à 20 % d’énergie en plus
- Le coefficient de performance (COP) du système chute, avec un rendement global détérioré
C’est pourquoi il est essentiel de maintenir la température et la pression de condensation aussi basses que possible, dans le respect des contraintes techniques et climatiques.
🛠️ Actions clés pour optimiser la condensation
1. ✅ Vérifier l’état des échangeurs (condenseurs)
Les échangeurs thermiques sont le cœur de la dissipation de chaleur. Avec le temps, ils peuvent se couvrir de poussière, de graisses, de tartre, ou encore subir des dégradations mécaniques.
- Condenseurs à air : poussières, feuilles, pollens obstruent les ailettes
- Condenseurs à eau : calcaire, corrosion, biofilm réduisent le transfert thermique
🧼 Astuce pratique : Planifiez un nettoyage régulier (mensuel à trimestriel selon l’environnement), avec des produits adaptés (détartrants, nettoyants spécifiques). N’oubliez pas de vérifier la pression différentielle en entrée/sortie pour détecter une obstruction.
2. ✅ Nettoyer les ailettes / tubes
Un condenseur propre est un condenseur efficace. Même 1 mm de poussière sur des ailettes peut diminuer l’échange thermique de 10 à 15 % !
- Utilisez un jet d’air comprimé, une brosse douce ou un nettoyeur basse pression (pas trop puissant pour ne pas abîmer les ailettes).
- Sur les condenseurs à eau, utilisez des produits détartrants en circuit fermé, sous supervision technique.
🧽 Bon à savoir : le nettoyage améliore également la durée de vie du compresseur et la stabilité des températures de consigne.
3. ⚙️ Ajuster la régulation des ventilateurs
Les ventilateurs du condenseur doivent adapter leur vitesse en fonction de la température extérieure. Une régulation en mode tout ou rien (marche/arrêt) est peu efficace et énergivore.
🔄 Solution recommandée : passer à une régulation flottante de la pression de condensation. Cela consiste à :
- Diminuer la vitesse des ventilateurs quand les températures extérieures le permettent
- Éviter de maintenir une pression fixe inutilement élevée
💡 Astuce bonus : installez des variateurs de fréquence (VFD) sur les moteurs de ventilateurs pour ajuster la vitesse de rotation de manière progressive.
4. ✅ Activer l’option de flottement de pression de condensation (si disponible)
De nombreux systèmes modernes disposent d’une fonction de flottement de pression de condensation. Elle permet au système de laisser descendre automatiquement la pression de condensation, lorsque la température ambiante le permet, sans impact négatif sur la distribution de liquide.
📉 Avantage :
- Moins de travail pour le compresseur
- Moins de bruit
- Moins de consommation d’électricité
⚠️ Attention : toutes les installations ne sont pas compatibles avec cette option. Elle nécessite parfois une adaptation de la vanne de détente et du récepteur de liquide.
📊 Résultats attendus : économies concrètes
Action mise en œuvre | Économie énergétique estimée |
---|---|
Nettoyage complet des condenseurs | 5 à 15 % |
Réduction de 5°C de la température de condensation | 5 à 10 % |
Régulation flottante avec VFD | 5 à 8 % |
Activation du flottement de pression | 3 à 7 % |
🏁 Total cumulé possible : jusqu’à 30 % d’économies sur la facture électrique !
🚨 Contraintes à respecter
1. ⚖️ Équilibre entre efficacité et sécurité
Attention à ne pas descendre trop bas en pression de condensation, au risque de :
- Perturber le fonctionnement de la vanne de détente (risque de manque de liquide)
- Provoquer des surchauffes au niveau de l’évaporateur
- Créer des défauts de régulation ou des alarmes
📌 Conseil : travaillez toujours en collaboration avec votre frigoriste, surtout pour les systèmes complexes ou multi-évaporateurs.
2. 🧊 Respect des normes et exigences process
Dans certains secteurs (industrie pharmaceutique, agroalimentaire, production de froid négatif), les températures doivent rester stables et sous contrôle précis. Optimiser la pression ne doit jamais compromettre la qualité du produit final.
- Suivre les préconisations des fabricants
- Respecter les normes ISO, les protocoles de sécurité alimentaire (HACCP)
- Surveiller la température du fluide secondaire (glycol, eau glacée…)
💼 Cas d’usage réel : une brasserie artisanale
Une brasserie artisanale équipée d’un groupe froid de 60 kW pour refroidir ses cuves de fermentation avait un condenseur encrassé qui condensait à 47°C en plein été.
Après :
- Un nettoyage complet des échangeurs
- L’ajout de variateurs de fréquence sur les ventilateurs
- L’activation du mode de régulation flottante
➡️ Résultat :
- Température de condensation stabilisée à 37°C
- Économie de 15 % sur la facture électrique mensuelle
- Retour sur investissement en moins de 12 mois
🧠 Bonnes pratiques à retenir
- 🌬️ Ventilez efficacement : évitez toute obstruction autour du condenseur (buissons, murs proches, débris)
- 🛠️ Entretenez régulièrement : mettez en place un plan de maintenance préventive
- 📉 Suivez vos indicateurs : température de condensation, intensité absorbée, pression HP
- 📊 Mettez en place une supervision énergétique pour identifier les dérives
🧩 Vers une automatisation intelligente
Les systèmes modernes s’appuient de plus en plus sur des capteurs IoT et des algorithmes intelligents pour :
- Adapter la régulation automatiquement
- Optimiser la température de condensation en temps réel
- Anticiper les encrassements ou surchauffes
🤖 Bon à savoir : associer intelligence artificielle + IoT permet une maintenance prédictive, réduisant les arrêts non planifiés tout en optimisant la performance énergétique.
L’optimisation de la température et de la pression de condensation est un levier accessible, rentable et peu complexe pour réduire rapidement votre consommation d’énergie. Trop souvent négligée, cette action offre des gains significatifs, immédiats et mesurables, avec peu d’investissement si vous êtes déjà équipé de matériel moderne.
✅ À retenir :
- Réduire la pression de condensation = moins d’énergie, moins de stress mécanique
- Nettoyez, régulez, surveillez
- Investissez dans l’automatisation si possible
💬 Vous souhaitez un audit de votre installation, un accompagnement technique ou une étude de rétrofit ? Contactez nous pour valoriser votre système de froid au maximum de son efficacité.
En somme, l’ingénierie des fluides industriels est une discipline importante et diversifiée qui joue un rôle clé dans de nombreuses industries. Elle nécessite une expertise technique et une connaissance approfondie des systèmes de circulation des fluides, de la thermodynamique, de la mécanique des fluides, de la régulation et du contrôle des processus, ainsi que de la sécurité.
Notre blog est une ressource complète pour tout ce qui concerne les fluides industriels. Nous vous encourageons à explorer nos articles, nos guides pratiques et nos ressources de formation pour approfondir vos connaissances et améliorer vos performances énergétiques. N’hésitez pas à nous contacter pour bénéficier de nos services d’ingénierie personnalisés ou pour trouver les produits dont vous avez besoin via notre site de commerce en ligne. Ensemble, nous pouvons aller plus loin dans l’apprentissage et réaliser des économies d’énergie significatives. Contactez-nous dès aujourd’hui à l’adresse suivante :
- Guide pour choisir un groupe froid industriel
- Lien : Exemple de schémas d’installation
- Lien : Calcul de la puissance nécessaire et facteurs de corrections usuels
- Le Guide Ultime du Choix des Compresseurs Frigorifiques : Optimisation, Puissance et Régulation
- Installation optimale de groupes froids industriels : Pratiques essentielles et paramètres clés
- Guide : La mise en service initiale d’un groupe froid industriel
- Les Applications du Refroidissement Industriel dans Divers Secteurs
- Guide Pratique pour le Choix d’un Groupe Froid Industriel : Calculs, Installations, Méthodes, Besoins et Critères Essentiels
- Optimiser l’Efficacité Énergétique : Deux Méthodes Ingénieuses pour Récupérer la Chaleur d’un Groupe Froid Industriel
- Guide Pratique : Récupération de Chaleur sur Groupe Froid – Avantages et Mise en Œuvre
- Innovations et Stratégies Avancées dans le Refroidissement Industriel: Vers une Ère Durable et Efficace
- Optimisation Cruciale: Les Répercussions d’un Réseau Industriel Mal Équilibré sur la Performance et la Sécurité
- Optimisation du Dimensionnement des Tuyauteries : Préserver la Pression et Réduire les Pertes de Charge
- Calculs et dimensionnement, installation, optimisation et Maintenance des Groupes Froids Industriels : Guide Complet pour Calcul de Puissance, Facteurs de Correction, et Technologies de Contrôle
- La conception d’un système de refroidissement industriel (Industrial Cooling System)
- Révolutionner le Froid Industriel et le Refroidissement Process avec l’IoT et l’IA : Entre Solutions High Tech, Low Tech, et Approches Hybrides
- Optimiser le Refroidissement Process avec l’IoT et l’IA : Révolutions et Techniques pour les Groupes Froids et Groupes d’Eau Glacée Industriels
- Révolution Technologique des Groupes Froids Industriels et Groupes d’Eau Glacée : Quand l’IA et les IoT Façonnent l’Avenir du Refroidissement Industriel
- FAQ : Groupes Froids Industriels et au Refroidissement Process
- Questions / réponses fréquemment posées sur le thème du refroidissement de process, incluant l’eau glacée, le froid industriel, les groupes froids, et les groupes d’eau glacée
- Quelles sont les erreurs courantes à éviter lors du choix d’un groupe froid industriel pour le refroidissement de son process ?
- Refroidissement Industriel : L’Essentiel sur les Groupes Frigorifiques et les Groupes d’Eau Glacée
- Lien: Notions de base
- Lie0n : Fonctionnement des systèmes de réfrigération
- Lien : applications du froid industriel
- Lien : Avantages et inconvénients
- Lien : En conclusion, le froid industriel est un élément clé de nombreuses industries modernes
- Lien : mesure de débit ultrasonique
- Mesure de Débit d’Eau par Ultrasons : Optimisation des Process Industriels
- Lien : Vitesse des fluides dans les tuyauteries
- Pour réaliser des économies d’énergie avec les installations d’eau glacée (froid industriel)
- Lien : Retrouver la performance de vos échangeurs avec le peigne frigoriste (groupe froid industriel, sécheur air comprimé, …)
- Lien : Réfractomètre : Mesurez facilement la concentration en glycol essentielle pour assurer la sécurité et la performance des installations industrielles
- Lien : Analyse d’huile des équipements : Optimisez la maintenance industrielle (compresseur air comprimé, groupe froid industriel, …)
- Les avantages de la connectivité IoT et I.A. dans les groupes froids industriels : Comment tirer parti des données pour améliorer les performances
- Les tendances émergentes dans les groupes froids industriels : Les nouvelles technologies qui transforment l’industrie du refroidissement
- La sélection du groupe froid industriel adapté à vos besoins : Guide d’achat et recommandations pour une solution optimale
- La sécurité dans les groupes froids industriels : Conseils pour prévenir les accidents et assurer la conformité aux normes de sécurité
- Maximisez la fiabilité de votre groupe froid industriel : Les meilleures pratiques pour éviter les pannes et les temps d’arrêt coûteux
- La maintenance préventive des groupes froids industriels : Astuces pour prolonger la durée de vie de votre équipement
- Les solutions respectueuses de l’environnement pour les groupes froids industriels : Astuces pour réduire l’empreinte carbone de votre installation
- La gestion intelligente des groupes froids industriels : Comment utiliser les systèmes de contrôle avancés pour optimiser les performances
- Les dernières avancées en matière de groupes froids industriels : Les technologies innovantes qui améliorent les performances
- Groupe froid industriel : Optimisez les économies d’énergie en adaptant vos consignes de température
- Optimisez l’efficacité énergétique de votre groupe froid industriel : Astuces pratiques pour réduire la consommation d’énergie
- Maîtrisez la poussière : Astuces innovantes et simples pour protéger vos équipements avec des filtres d’air comprimé dans les environnements poussiéreu
Lien pour achats :
Relever la consigne de température : une stratégie simple pour réduire vos coûts énergétiques sans compromettre la qualité
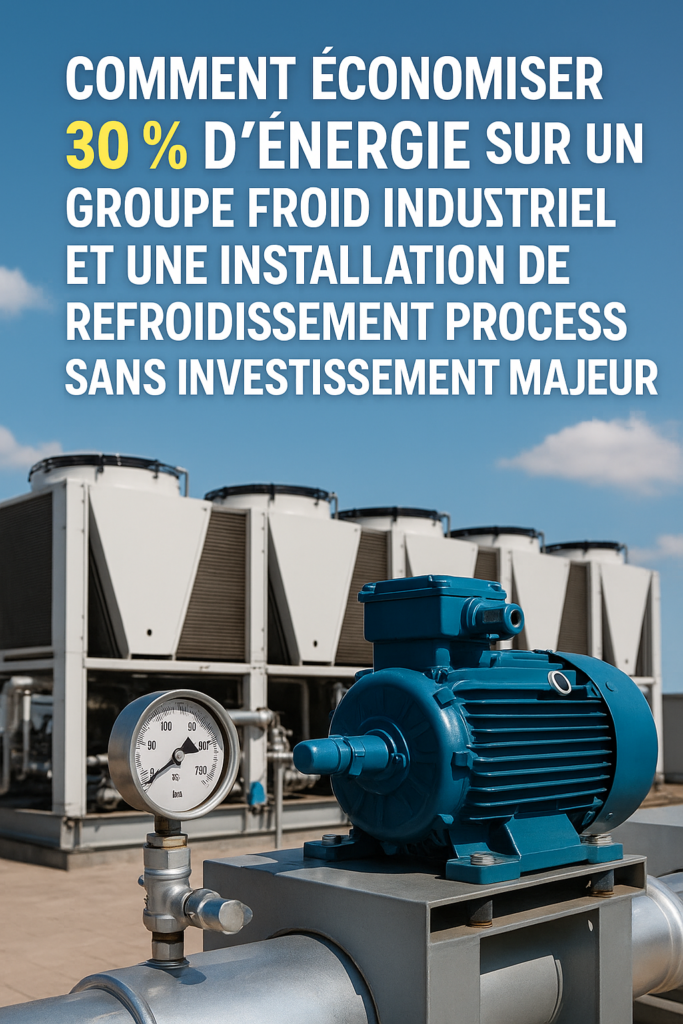
Dans un contexte de hausse continue du prix de l’énergie et de transition vers des pratiques industrielles plus durables, chaque degré compte. Si l’on parle souvent d’investissements lourds pour améliorer l’efficacité énergétique, il existe aussi des leviers simples, peu coûteux, mais extrêmement efficaces. L’un des plus puissants : relever légèrement la température de consigne de vos installations thermiques ou frigorifiques.
Ce geste apparemment anodin peut, à lui seul, générer 4 à 6 % d’économies d’énergie, tout en maintenant la qualité et la sécurité de vos processus industriels. Encore faut-il le faire intelligemment, en tenant compte des réalités terrain, des contraintes techniques et normatives. Cet article vous guide pas à pas pour comprendre, évaluer et mettre en œuvre cette optimisation.
🌡️ Comprendre ce qu’est la température de consigne
La température de consigne est la valeur cible que vos équipements de régulation thermique ou de réfrigération doivent maintenir. C’est un paramètre clé qui conditionne à la fois le niveau de confort, la qualité produit, et surtout, la consommation énergétique de vos systèmes.
👉 En production industrielle, on la retrouve sur :
- Les groupes froid pour le process (agroalimentaire, pharmaceutique…)
- Les climatiseurs industriels
- Les centrales de traitement d’air
- Les chaudières et PAC (pompes à chaleur)
- Les systèmes de refroidissement ou d’eau glacée
⚠️ Pourquoi les consignes sont souvent plus basses que nécessaire ?
Dans bien des cas, les températures de consigne sont fixées de manière empirique ou excessive, souvent « pour être sûr ». Résultat :
- Le système travaille plus dur pour atteindre une température inutilement basse
- Les compresseurs consomment davantage
- Les usures mécaniques augmentent
- Et surtout : l’énergie est gaspillée sans valeur ajoutée pour le process
📌 Bon à savoir :
Baisser la consigne de 1°C équivaut souvent à une augmentation de la consommation énergétique de 2 à 4 % !
À l’inverse, la relever de 1 à 3°C permet une économie similaire sans impact sur la qualité, si cela reste dans les limites acceptables.
🔧 Astuce pratique : remonter la température de consigne en toute sécurité
Voici une démarche simple et méthodique pour adapter la température de consigne à vos besoins réels :
1. 📊 Analyser les besoins réels du process
Commencez par évaluer objectivement la température nécessaire pour assurer la qualité de vos produits ou le confort requis. Posez-vous ces questions :
- Quelle est la température réellement nécessaire pour maintenir mes produits ?
- Existe-t-il une marge de sécurité aujourd’hui sur la consigne ?
- Puis-je moduler la consigne en fonction des heures, jours ou saisons ?
💡 Exemple concret :
Une entreprise agroalimentaire conservait ses produits à -7°C « par habitude », alors qu’une analyse a montré qu’un stockage à -5°C suffisait parfaitement aux normes de conservation.
Gain énergétique estimé : 5 % sur la facture annuelle du groupe froid !
2. 🧪 Tester progressivement
Ne modifiez jamais brutalement la consigne de température. Procédez par ajustements progressifs, en respectant les conditions suivantes :
- Montez la consigne par paliers de 1°C maximum
- Surveillez étroitement les impacts sur la qualité produit
- Utilisez des capteurs de température précis, idéalement reliés à un système de supervision
- Documentez les résultats et validez la stabilité du process
⚠️ Attention aux contraintes critiques :
- Température de consigne imposée par des normes ISO, IFS, BRC…
- Process pharmaceutiques avec traçabilité réglementaire
- Sécurité alimentaire ou maintien de la chaîne du froid
En cas de doute, validez les changements avec un responsable qualité ou un bureau d’études process.
3. 🔄 Optimiser en continu avec les données
L’approche data-driven est la clé pour pérenniser les gains :
- Connectez vos équipements à un système de supervision (IoT, SCADA, GTC…)
- Analysez les courbes de température et les variations de consommation
- Identifiez les zones d’inefficience ou de sur-refroidissement ponctuel
- Intégrez ces données dans vos revues de performance énergétique
📊 Astuce technique :
Installer un capteur de température intelligent avec transmission sans fil permet de monitorer des points critiques oubliés, à moindre coût.
💡 Bonnes pratiques à connaître
Voici une série de conseils applicables dès aujourd’hui pour booster l’efficacité énergétique via la gestion des consignes de température :
✅ Faites la chasse aux consignes « historiques »
Certaines valeurs ont été fixées il y a des années sans remise en question. Interrogez systématiquement les consignes en place.
✅ Adaptez la consigne à l’usage
- En horaire de nuit ou week-end : possibilité de remonter légèrement la consigne
- En période creuse : mode éco ou « veille énergétique »
✅ Soyez cohérent entre chauffage et refroidissement
Une consigne de chauffage à 20°C et une consigne de clim à 19°C créent un conflit absurde et énergivore.
✅ Formez vos équipes
Les opérateurs ou techniciens doivent comprendre l’impact d’1 seul degré sur la facture énergétique et l’usure du matériel.
📉 Résultats mesurés : études de cas
🧊 Cas 1 – Industrie agroalimentaire
Situation : entrepôt frigorifique à -22°C
Action : consigne relevée à -20°C après validation qualité
Résultat : économie de 6,3 % sur la consommation du groupe froid
🧪 Cas 2 – Laboratoire pharmaceutique
Situation : chambre climatique à 5°C
Action : montée progressive de la consigne à 7°C
Résultat : baisse de 4,1 % de la consommation énergétique, sans altération du processus
🏭 Cas 3 – Usine de production industrielle
Situation : circuit d’eau glacée avec consigne à 6°C
Action : test à 8°C sur 3 semaines avec supervision continue
Résultat : -4,7 % sur les factures électriques, aucun retour client négatif
📌 Zoom sur le retour sur investissement (ROI)
Remonter la consigne est une action à coût quasi nul : aucun investissement lourd, juste de l’analyse, des tests et un peu de rigueur.
💰 Exemple chiffré :
Installation frigorifique de 150 kW
Consommation annuelle : 500 000 kWh
Tarif énergie : 0,12 €/kWh
➡ Gain de 5 % = 25 000 kWh = 3 000 €/an d’économie
Sur 10 ans : 30 000 € économisés sans changement matériel.
🧠 Ce que vous gagnez en plus de l’énergie
Relever la consigne de température, c’est aussi :
- ✅ Moins d’usure des compresseurs et équipements
- ✅ Moins de cycles marche/arrêt
- ✅ Moins de variations thermiques internes
- ✅ Moins de maintenance et de pannes
- ✅ Une meilleure maîtrise du process
🔍 Et si vous alliez plus loin ?
Relever la consigne est un levier simple, mais ce n’est qu’un élément d’une démarche globale d’optimisation énergétique. Associez-le à d’autres actions comme :
- Le désembouage et nettoyage des échangeurs
- La gestion intelligente des séquences de compresseurs
- La détection des fuites d’air comprimé
- L’isolation des réseaux frigorifiques ou calorifuges
- L’ajout de variateurs de vitesse
Chaque % gagné compte, surtout dans une industrie où l’énergie est un poste de coût critique.
🚀 En résumé : relevez vos consignes intelligemment
Étape | Objectif | Impact potentiel |
---|---|---|
Analyse des besoins | Identifier les marges de sécurité inutiles | 2 à 6 % d’économie |
Test progressif | Monter la consigne sans impact process | 1°C à la fois |
Validation normative | Respecter les normes (ISO, IFS, pharma…) | Zéro risque |
Suivi continu | Supervision des données | Maintien des gains |
Formation des équipes | Sensibiliser aux enjeux d’1°C | Efficacité durable |
✅ À retenir
🎯 Relever une consigne de 1 à 3°C peut réduire la consommation énergétique de 4 à 6 % sans compromis sur la qualité.
✔️ Action rapide, gratuite, mesurable
✔️ Respect impératif des normes process
✔️ Intégration facile dans un plan de performance énergétique
✔️ Gains durables et effet positif sur la maintenance
En somme, l’ingénierie des fluides industriels est une discipline importante et diversifiée qui joue un rôle clé dans de nombreuses industries. Elle nécessite une expertise technique et une connaissance approfondie des systèmes de circulation des fluides, de la thermodynamique, de la mécanique des fluides, de la régulation et du contrôle des processus, ainsi que de la sécurité.
Notre blog est une ressource complète pour tout ce qui concerne les fluides industriels. Nous vous encourageons à explorer nos articles, nos guides pratiques et nos ressources de formation pour approfondir vos connaissances et améliorer vos performances énergétiques. N’hésitez pas à nous contacter pour bénéficier de nos services d’ingénierie personnalisés ou pour trouver les produits dont vous avez besoin via notre site de commerce en ligne. Ensemble, nous pouvons aller plus loin dans l’apprentissage et réaliser des économies d’énergie significatives. Contactez-nous dès aujourd’hui à l’adresse suivante :
- Guide pour choisir un groupe froid industriel
- Lien : Exemple de schémas d’installation
- Lien : Calcul de la puissance nécessaire et facteurs de corrections usuels
- Le Guide Ultime du Choix des Compresseurs Frigorifiques : Optimisation, Puissance et Régulation
- Installation optimale de groupes froids industriels : Pratiques essentielles et paramètres clés
- Guide : La mise en service initiale d’un groupe froid industriel
- Les Applications du Refroidissement Industriel dans Divers Secteurs
- Guide Pratique pour le Choix d’un Groupe Froid Industriel : Calculs, Installations, Méthodes, Besoins et Critères Essentiels
- Optimiser l’Efficacité Énergétique : Deux Méthodes Ingénieuses pour Récupérer la Chaleur d’un Groupe Froid Industriel
- Guide Pratique : Récupération de Chaleur sur Groupe Froid – Avantages et Mise en Œuvre
- Innovations et Stratégies Avancées dans le Refroidissement Industriel: Vers une Ère Durable et Efficace
- Optimisation Cruciale: Les Répercussions d’un Réseau Industriel Mal Équilibré sur la Performance et la Sécurité
- Optimisation du Dimensionnement des Tuyauteries : Préserver la Pression et Réduire les Pertes de Charge
- Calculs et dimensionnement, installation, optimisation et Maintenance des Groupes Froids Industriels : Guide Complet pour Calcul de Puissance, Facteurs de Correction, et Technologies de Contrôle
- La conception d’un système de refroidissement industriel (Industrial Cooling System)
- Révolutionner le Froid Industriel et le Refroidissement Process avec l’IoT et l’IA : Entre Solutions High Tech, Low Tech, et Approches Hybrides
- Optimiser le Refroidissement Process avec l’IoT et l’IA : Révolutions et Techniques pour les Groupes Froids et Groupes d’Eau Glacée Industriels
- Révolution Technologique des Groupes Froids Industriels et Groupes d’Eau Glacée : Quand l’IA et les IoT Façonnent l’Avenir du Refroidissement Industriel
- FAQ : Groupes Froids Industriels et au Refroidissement Process
- Questions / réponses fréquemment posées sur le thème du refroidissement de process, incluant l’eau glacée, le froid industriel, les groupes froids, et les groupes d’eau glacée
- Quelles sont les erreurs courantes à éviter lors du choix d’un groupe froid industriel pour le refroidissement de son process ?
- Refroidissement Industriel : L’Essentiel sur les Groupes Frigorifiques et les Groupes d’Eau Glacée
- Lien: Notions de base
- Lie0n : Fonctionnement des systèmes de réfrigération
- Lien : applications du froid industriel
- Lien : Avantages et inconvénients
- Lien : En conclusion, le froid industriel est un élément clé de nombreuses industries modernes
- Lien : mesure de débit ultrasonique
- Mesure de Débit d’Eau par Ultrasons : Optimisation des Process Industriels
- Lien : Vitesse des fluides dans les tuyauteries
- Pour réaliser des économies d’énergie avec les installations d’eau glacée (froid industriel)
- Lien : Retrouver la performance de vos échangeurs avec le peigne frigoriste (groupe froid industriel, sécheur air comprimé, …)
- Lien : Réfractomètre : Mesurez facilement la concentration en glycol essentielle pour assurer la sécurité et la performance des installations industrielles
- Lien : Analyse d’huile des équipements : Optimisez la maintenance industrielle (compresseur air comprimé, groupe froid industriel, …)
- Les avantages de la connectivité IoT et I.A. dans les groupes froids industriels : Comment tirer parti des données pour améliorer les performances
- Les tendances émergentes dans les groupes froids industriels : Les nouvelles technologies qui transforment l’industrie du refroidissement
- La sélection du groupe froid industriel adapté à vos besoins : Guide d’achat et recommandations pour une solution optimale
- La sécurité dans les groupes froids industriels : Conseils pour prévenir les accidents et assurer la conformité aux normes de sécurité
- Maximisez la fiabilité de votre groupe froid industriel : Les meilleures pratiques pour éviter les pannes et les temps d’arrêt coûteux
- La maintenance préventive des groupes froids industriels : Astuces pour prolonger la durée de vie de votre équipement
- Les solutions respectueuses de l’environnement pour les groupes froids industriels : Astuces pour réduire l’empreinte carbone de votre installation
- La gestion intelligente des groupes froids industriels : Comment utiliser les systèmes de contrôle avancés pour optimiser les performances
- Les dernières avancées en matière de groupes froids industriels : Les technologies innovantes qui améliorent les performances
- Groupe froid industriel : Optimisez les économies d’énergie en adaptant vos consignes de température
- Optimisez l’efficacité énergétique de votre groupe froid industriel : Astuces pratiques pour réduire la consommation d’énergie
- Maîtrisez la poussière : Astuces innovantes et simples pour protéger vos équipements avec des filtres d’air comprimé dans les environnements poussiéreu
Lien pour achats :
Comprendre où l’énergie est gaspillée dans une installation de froid industriel : Le préalable indispensable à toute optimisation
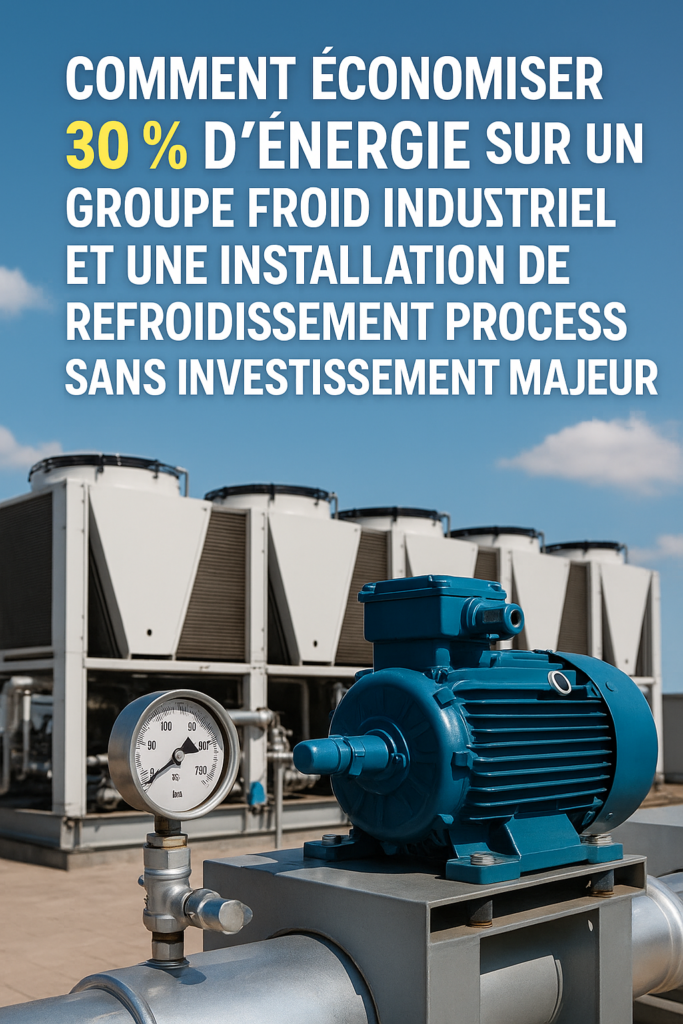
L’efficacité énergétique commence par la connaissance des pertes
Dans le secteur industriel, les installations de froid consomment une part significative de l’électricité totale, notamment dans l’agroalimentaire, la plasturgie, la chimie, ou encore la pharmacie. Pourtant, dans nombre de cas, jusqu’à 30 % de l’énergie consommée peut être gaspillée sans qu’aucune alarme ne soit déclenchée.
Avant de penser à investir dans un nouveau groupe froid, des variateurs de vitesse, ou des systèmes de supervision coûteux, il est impératif de comprendre où se trouvent les pertes d’énergie. Cet article fait le point de manière ultra technique et pédagogique sur les postes les plus courants de gaspillage, les méthodes simples pour les identifier, et les gains potentiels associés.
1. Températures de consigne excessivement basses : une erreur fréquente et coûteuse
1.1 Le mythe du “plus froid = mieux”
Beaucoup d’exploitants pensent que plus la température de consigne est basse, meilleure sera la qualité ou la sécurité du process. En réalité, chaque degré de froid en plus a un coût énergétique exponentiel.
🔧 Bon à savoir :
1°C de réduction de consigne = +2 à 4 % de consommation électrique !
1.2 Exemple pratique
Si une cuve de process fonctionne à -6°C au lieu de -3°C, c’est environ 9 à 12 % d’énergie gaspillée inutilement 24h/24.
✅ Astuce :
- Vérifier les besoins réels du process : une cartographie température/process peut montrer que 1 ou 2°C peuvent être récupérés sans impact sur la qualité.
- Mettre en place une alerte sur la régulation dès que la température descend sous la valeur cible – cela évite les dérives.
2. Pressions de condensation trop élevées : surcharge inutile des compresseurs
2.1 Le principe
Une pression de condensation trop haute oblige le compresseur à travailler contre une contre-pression excessive. Cela augmente l’effort mécanique et donc la consommation électrique.
2.2 Pourquoi cela arrive ?
- Mauvais réglage des ventilateurs de condenseurs.
- Encrassement des échangeurs.
- Températures extérieures mal exploitées (pas de “floating head pressure”).
🔧 Bon à savoir :
Chaque réduction de 1 bar en condensation = 7 à 8 % de consommation en moins sur le compresseur.
✅ Astuce :
- Utiliser des régulations flottantes de la pression de condensation en fonction de la température ambiante.
- Nettoyage régulier des condenseurs à air (minimum 2 fois par an en environnement poussiéreux).
- Ajouter des sondes extérieures couplées à une carte de régulation pour adapter la pression automatiquement.
3. Surcharges thermiques inutiles : attention aux apports parasites
3.1 Qu’est-ce qu’une surcharge thermique inutile ?
Ce sont des apports de chaleur au circuit frigorifique non nécessaires :
- Portes de chambres froides laissées ouvertes trop longtemps.
- Isolations dégradées ou absentes.
- Apports solaires non maîtrisés.
3.2 Impacts
Le groupe froid doit compenser des calories qui ne devraient pas exister, ce qui augmente fortement la consommation électrique.
🔧 Bon à savoir :
Un simple joint de porte défectueux peut représenter plusieurs centaines d’euros par an de surconsommation.
✅ Astuce :
- Mettre en place un checklist visuel mensuel sur les isolations, portes, stores, clapets anti-retour, etc.
- Installer des rideaux d’air ou portes rapides en zones de passage intensif.
4. Encrassement des échangeurs : perte de rendement thermique garantie
4.1 Un problème invisible mais fréquent
L’encrassement (dépôts, tartre, poussière) des échangeurs baisse l’efficacité des transferts de chaleur, obligeant le groupe froid à travailler plus longtemps et plus fort.
4.2 Symptômes typiques
- Temps de cycle plus longs.
- Moins bon maintien des consignes.
- Évaporation à pression plus basse = plus de travail pour le compresseur.
🔧 Bon à savoir :
Une perte d’échange thermique de 15 % équivaut à environ 5 à 10 % d’énergie en plus selon la configuration.
✅ Astuce :
- Purger les échangeurs à plaques tous les 6 mois, ou installer des filtres anti-boues.
- Planifier le détartrage chimique annuel des condenseurs à eau.
- Installer des manomètres différentiels pour surveiller les pertes de charge croissantes.
5. Pertes d’eau et fuites d’air sur les circuits auxiliaires
5.1 Des pertes invisibles mais coûteuses
Beaucoup d’installations utilisent des circuits secondaires : eau glacée, air comprimé, glycol. Toute fuite ou micro-perte représente une charge thermique ou mécanique permanente.
5.2 Exemples fréquents
- Une fuite d’eau de 1 litre/min = 525 000 litres/an à refroidir inutilement.
- Un soufflage d’air comprimé permanent = jusqu’à 1 000 €/an par point de perte.
🔧 Bon à savoir :
L’eau de process coûte en double : à refroidir et à traiter (chloration, adoucissement…).
✅ Astuce :
- Mettre en place des journées de chasse aux fuites avec détection par ultrasons.
- Vérifier régulièrement les vannes de vidange automatique (souvent bloquées ouvertes).
- Installer des compteurs d’eau et débitmètres différentiel pour alerter en cas d’anomalie.
6. Arrêts/redémarrages fréquents : des cycles énergivores
6.1 L’inertie thermique a un coût
Chaque redémarrage d’un groupe froid implique :
- Des pics de consommation.
- Une montée en pression et en température.
- Des pertes dues à l’absence d’inertie.
Cela augmente les cycles courts, diminue la durée de vie des composants, et multiplie les consommations cachées.
6.2 Cas typique
Un petit groupe de 15 kW redémarrant toutes les 10 minutes pendant la journée gaspille 5 à 8 % d’énergie sur les cycles seuls.
🔧 Bon à savoir :
Certains compresseurs à vis peuvent perdre en rendement dès que la charge est inférieure à 30 %.
✅ Astuce :
- Adapter la taille du groupe froid à la charge réelle → éviter les surdimensionnements.
- Installer des ballons tampons ou modules d’inertie.
- Travailler avec une plage de régulation plus large pour limiter les ON/OFF.
7. Régulation non optimisée des compresseurs
7.1 Pourquoi c’est important ?
Des compresseurs mal régulés ou mal séquencés peuvent :
- Fonctionner à vide inutilement.
- Se chevaucher.
- Être sollicités alors qu’un seul suffirait.
🔧 Bon à savoir :
Un compresseur de 75 kW fonctionnant à vide pendant 20 % du temps = 15 kW/h gaspillés.
✅ Astuce :
- Installer une carte maître/esclave entre compresseurs.
- Réviser les stratégies de séquençage : prioritaire/secours, alternance hebdomadaire.
- Étendre la plage de régulation sans mettre en danger la qualité du process.
8. Synthèse : Visualiser les pertes pour mieux agir
Poste de gaspillage | Impact potentiel | Solution rapide | Gain estimé |
---|---|---|---|
Température trop basse | +2 à 4 % par °C | Revoir les besoins réels | Jusqu’à 12 % |
Condensation élevée | +7 % par bar | Régulation flottante | 10 à 15 % |
Échangeur encrassé | -15 % rendement | Nettoyage/entretien | 5 à 10 % |
Fuites eau/air | Permanent | Chasse aux fuites | 3 à 5 % |
Cycles courts | Pics énergie | Inertie/régulation | 5 à 8 % |
Mauvais séquençage | Groupe à vide | Carte de régulation | 5 à 10 % |
Identifier avant d’investir
Optimiser la consommation énergétique d’un groupe froid ou d’une installation de refroidissement process ne commence pas par des investissements, mais par une phase de diagnostic approfondi des causes de gaspillage.
Agir avec méthode, c’est souvent 30 % d’économies réalisables en quelques semaines, avec un retour immédiat sur effort. Un simple écart de consigne, une vanne oubliée, ou un condenseur encrassé peut faire la différence entre une exploitation performante ou énergivore.
En somme, l’ingénierie des fluides industriels est une discipline importante et diversifiée qui joue un rôle clé dans de nombreuses industries. Elle nécessite une expertise technique et une connaissance approfondie des systèmes de circulation des fluides, de la thermodynamique, de la mécanique des fluides, de la régulation et du contrôle des processus, ainsi que de la sécurité.
Notre blog est une ressource complète pour tout ce qui concerne les fluides industriels. Nous vous encourageons à explorer nos articles, nos guides pratiques et nos ressources de formation pour approfondir vos connaissances et améliorer vos performances énergétiques. N’hésitez pas à nous contacter pour bénéficier de nos services d’ingénierie personnalisés ou pour trouver les produits dont vous avez besoin via notre site de commerce en ligne. Ensemble, nous pouvons aller plus loin dans l’apprentissage et réaliser des économies d’énergie significatives. Contactez-nous dès aujourd’hui à l’adresse suivante :
- Guide pour choisir un groupe froid industriel
- Lien : Exemple de schémas d’installation
- Lien : Calcul de la puissance nécessaire et facteurs de corrections usuels
- Le Guide Ultime du Choix des Compresseurs Frigorifiques : Optimisation, Puissance et Régulation
- Installation optimale de groupes froids industriels : Pratiques essentielles et paramètres clés
- Guide : La mise en service initiale d’un groupe froid industriel
- Les Applications du Refroidissement Industriel dans Divers Secteurs
- Guide Pratique pour le Choix d’un Groupe Froid Industriel : Calculs, Installations, Méthodes, Besoins et Critères Essentiels
- Optimiser l’Efficacité Énergétique : Deux Méthodes Ingénieuses pour Récupérer la Chaleur d’un Groupe Froid Industriel
- Guide Pratique : Récupération de Chaleur sur Groupe Froid – Avantages et Mise en Œuvre
- Innovations et Stratégies Avancées dans le Refroidissement Industriel: Vers une Ère Durable et Efficace
- Optimisation Cruciale: Les Répercussions d’un Réseau Industriel Mal Équilibré sur la Performance et la Sécurité
- Optimisation du Dimensionnement des Tuyauteries : Préserver la Pression et Réduire les Pertes de Charge
- Calculs et dimensionnement, installation, optimisation et Maintenance des Groupes Froids Industriels : Guide Complet pour Calcul de Puissance, Facteurs de Correction, et Technologies de Contrôle
- La conception d’un système de refroidissement industriel (Industrial Cooling System)
- Révolutionner le Froid Industriel et le Refroidissement Process avec l’IoT et l’IA : Entre Solutions High Tech, Low Tech, et Approches Hybrides
- Optimiser le Refroidissement Process avec l’IoT et l’IA : Révolutions et Techniques pour les Groupes Froids et Groupes d’Eau Glacée Industriels
- Révolution Technologique des Groupes Froids Industriels et Groupes d’Eau Glacée : Quand l’IA et les IoT Façonnent l’Avenir du Refroidissement Industriel
- FAQ : Groupes Froids Industriels et au Refroidissement Process
- Questions / réponses fréquemment posées sur le thème du refroidissement de process, incluant l’eau glacée, le froid industriel, les groupes froids, et les groupes d’eau glacée
- Quelles sont les erreurs courantes à éviter lors du choix d’un groupe froid industriel pour le refroidissement de son process ?
- Refroidissement Industriel : L’Essentiel sur les Groupes Frigorifiques et les Groupes d’Eau Glacée
- Lien: Notions de base
- Lie0n : Fonctionnement des systèmes de réfrigération
- Lien : applications du froid industriel
- Lien : Avantages et inconvénients
- Lien : En conclusion, le froid industriel est un élément clé de nombreuses industries modernes
- Lien : mesure de débit ultrasonique
- Mesure de Débit d’Eau par Ultrasons : Optimisation des Process Industriels
- Lien : Vitesse des fluides dans les tuyauteries
- Pour réaliser des économies d’énergie avec les installations d’eau glacée (froid industriel)
- Lien : Retrouver la performance de vos échangeurs avec le peigne frigoriste (groupe froid industriel, sécheur air comprimé, …)
- Lien : Réfractomètre : Mesurez facilement la concentration en glycol essentielle pour assurer la sécurité et la performance des installations industrielles
- Lien : Analyse d’huile des équipements : Optimisez la maintenance industrielle (compresseur air comprimé, groupe froid industriel, …)
- Les avantages de la connectivité IoT et I.A. dans les groupes froids industriels : Comment tirer parti des données pour améliorer les performances
- Les tendances émergentes dans les groupes froids industriels : Les nouvelles technologies qui transforment l’industrie du refroidissement
- La sélection du groupe froid industriel adapté à vos besoins : Guide d’achat et recommandations pour une solution optimale
- La sécurité dans les groupes froids industriels : Conseils pour prévenir les accidents et assurer la conformité aux normes de sécurité
- Maximisez la fiabilité de votre groupe froid industriel : Les meilleures pratiques pour éviter les pannes et les temps d’arrêt coûteux
- La maintenance préventive des groupes froids industriels : Astuces pour prolonger la durée de vie de votre équipement
- Les solutions respectueuses de l’environnement pour les groupes froids industriels : Astuces pour réduire l’empreinte carbone de votre installation
- La gestion intelligente des groupes froids industriels : Comment utiliser les systèmes de contrôle avancés pour optimiser les performances
- Les dernières avancées en matière de groupes froids industriels : Les technologies innovantes qui améliorent les performances
- Groupe froid industriel : Optimisez les économies d’énergie en adaptant vos consignes de température
- Optimisez l’efficacité énergétique de votre groupe froid industriel : Astuces pratiques pour réduire la consommation d’énergie
- Maîtrisez la poussière : Astuces innovantes et simples pour protéger vos équipements avec des filtres d’air comprimé dans les environnements poussiéreu
Lien pour achats :
Comment Économiser Jusqu’à 30 % d’Énergie sur un Groupe Froid Industriel et un Système de Refroidissement Process Sans Investissement Majeur
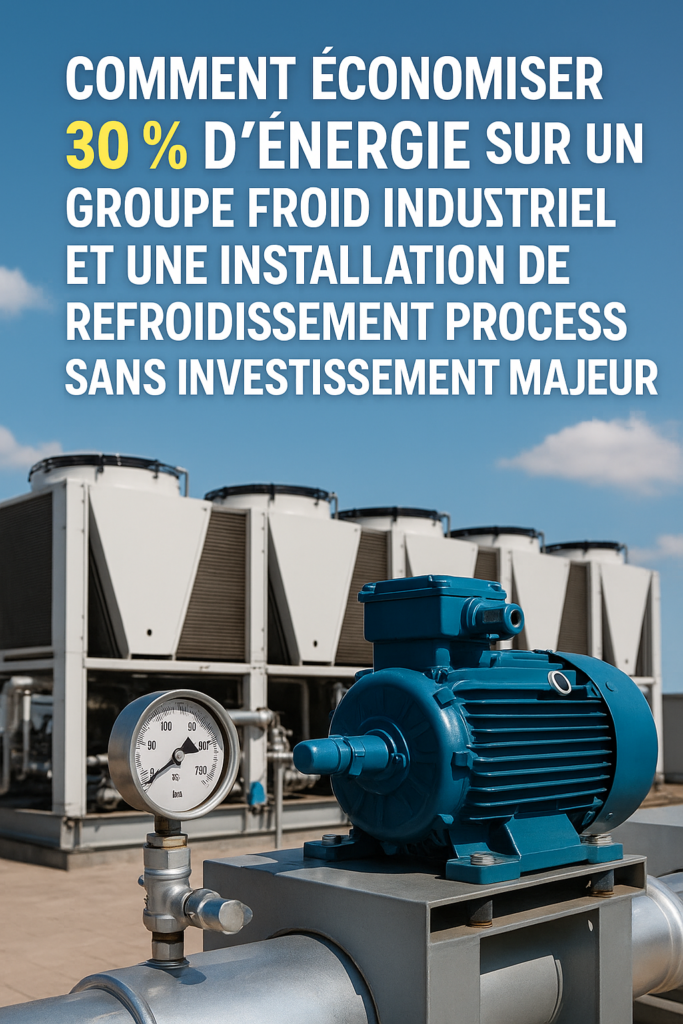
Dans l’industrie, le fonctionnement d’un groupe froid et d’une installation de refroidissement process représente souvent 20 à 40 % de la facture énergétique d’un site. Pourtant, sans engager de lourds investissements, il est possible de réaliser jusqu’à 30 % d’économies simplement en optimisant l’existant.
Cet article ultra-technique, riche en trucs et astuces, vous guide étape par étape vers une performance énergétique améliorée, en agissant avec bon sens, méthode, et pragmatisme.
1. 🧠 Comprendre d’abord où l’énergie est gaspillée
Avant toute action, il est essentiel d’identifier les sources majeures de pertes :
- Températures de consigne excessivement basses → Surconsommation électrique inutile.
- Pressions de condensation élevées → Plus d’effort pour les compresseurs.
- Surcharges thermiques inutiles → Mauvaise utilisation de l’équipement.
- Encrassement des échangeurs → Baisse des rendements thermiques.
- Pertes d’eau / fuites d’air sur les circuits auxiliaires.
- Arrêts/redémarrages fréquents → Moins bon rendement.
- Séquences de compresseurs non optimisées.
Bon à savoir :
Un simple écart de 1°C en consigne peut représenter 2 à 4 % d’économie d’énergie !
2. 🎯 Actions immédiates sur les groupes froids pour des gains rapides
2.1 Relever la consigne de température
🔧 Astuce pratique :
- Analyser précisément les besoins process réels.
- Remonter la température de consigne de 1°C à 3°C si possible.
Exemple : Passer de -7°C à -5°C peut déjà réduire la consommation de 4 à 6 % sans impacter la qualité produit.
Attention : Respecter les contraintes process critiques (sécurité alimentaire, normes ISO…).
2.2 Optimiser la pression de condensation
Un condenseur qui condense à 45°C au lieu de 35°C entraîne une surconsommation importante.
🔧 Actions clés :
- Vérifier l’état des échangeurs (condenseurs).
- Nettoyer les ailettes / tubes (poussières, calcaire, graisse…).
- Ajuster la régulation des ventilateurs (mode flottant conseillé).
- Activer l’option de flottement de pression de condensation si disponible.
Bon à savoir :
Chaque degré de réduction de la pression de condensation permet de gagner 1 à 2 % de consommation électrique.
2.3 Assurer un bon entretien des échangeurs
🔧 Checklist rapide :
- Nettoyage des condenseurs aérauliques ou hydrauliques (décrassage haute pression adaptée).
- Vérification de la perte de charge initiale vs actuelle.
- Traitement anticalcaire éventuel sur circuit d’eau de refroidissement.
Bon à savoir :
Un condenseur encrassé de 2 mm de tartre peut entraîner une surchauffe de 10 % du compresseur.
2.4 Optimiser la séquence des compresseurs frigorifiques
Si plusieurs groupes sont en place :
- Mettre un groupe principal en priorité (le plus récent ou le plus performant).
- Garder les autres en secours automatique.
Astuce :
Utiliser des séquences principal/secondaire basées sur l’efficacité énergétique de chaque machine.
Exemple concret :
Ne pas faire tourner en parallèle deux petits groupes inefficaces si un seul gros groupe peut suffire temporairement.
2.5 Réglage optimal des ventilateurs
Dans les condenseurs aérauliques :
- Utiliser la vitesse variable si disponible.
- Optimiser le seuil de déclenchement.
- Définir des rampes de modulation douces.
Effet : Jusqu’à 10 % d’économie supplémentaire sur le fonctionnement auxiliaire.
3. 📏 Côté installation process : interventions faciles et efficaces
3.1 Supprimer les surcharges inutiles
Erreurs classiques :
- Circulation d’eau froide dans des équipements non utilisés.
- Refroidissement « permanent » de lignes process arrêtées.
🔧 Actions :
- Installer des vannes manuelles / électrovannes.
- Ajouter un pilotage simple avec détecteurs de fonctionnement.
Exemple concret :
Couper le refroidissement d’un process à l’arrêt = économie immédiate de 5 à 8 %.
3.2 Améliorer l’isolation thermique
🔧 Zones prioritaires :
- Réseaux d’eau glacée.
- Réservoirs tampon.
- Chambres froides.
Vérifier et réparer :
- Isolants endommagés, manquants, humides.
Bon à savoir :
Une canalisation d’eau glacée non isolée de 10 mètres peut coûter jusqu’à 500 €/an en pertes thermiques.
3.3 Contrôler et ajuster les débits d’eau
Défaut fréquent :
Débit d’eau surdimensionné → énergie pompée inutilement.
🔧 Solutions simples :
- Réduction des débits sur pompes fixes (bypass, réglage vannes).
- Vérification des régulations automatiques.
4. 📈 Mesurer pour mieux piloter : le suivi énergétique
Même sans système SCADA ou GTC coûteux, il est possible d’assurer un monitoring énergétique basique :
Outil | Usage | Coût | Effet |
---|---|---|---|
Manomètre différentiel | Suivre pertes condenseurs/évaporateurs | 30 € | Diagnostic facile |
Thermomètre infrarouge | Contrôler températures échangeurs | 50 € | Détecter anomalies rapidement |
Compteur kWh clipsable | Suivi de la consommation électrique du groupe | 80 € | Mesure directe de gains |
Astuce terrain :
Créer un tableau Excel pour relever consommations mensuelles, consignes de température, pressions, et températures ambiantes.
5. 📊 Simulation d’économie réelle
Exemple type : Groupe froid de 100 kW électrique installé.
Action | Gain estimé | Impact |
---|---|---|
Remonter consigne de +2°C | 5 % | -5 kW |
Nettoyage condenseur | 8 % | -8 kW |
Optimisation séquence compresseurs | 6 % | -6 kW |
Optimisation ventilateurs | 3 % | -3 kW |
Isolation des tuyauteries | 5 % | -5 kW |
Coupure automatique de process non utilisés | 4 % | -4 kW |
Total :
30 % de réduction soit 30 kW économisés → ~26 000 € économisés/an sur une base de 8000 heures de fonctionnement et un prix de 0,11 €/kWh.
6. ♻️ Bonus : Impact carbone des économies
Réduction d’empreinte carbone associée :
- 1 kWh économisé = 0,08 kg de CO2 évité (moyenne européenne).
- 30 000 kWh/an économisés = 2,4 tonnes de CO2/an évitées.
Un double gain : Économie financière + réduction des émissions = valeur ajoutée pour vos audits RSE, ISO 14001, ou pour valoriser vos démarches clients.
🏆 En résumé
Optimiser l’efficacité énergétique d’un groupe froid industriel sans investissement majeur, c’est possible, rapide et rentable.
Les clés du succès :
- Agir sur les réglages et l’entretien plutôt que de remplacer immédiatement.
- Former et impliquer les techniciens et opérateurs.
- Suivre régulièrement les performances.
- Décider sur des mesures simples, mesurables et vérifiables.
En appliquant rigoureusement ces bonnes pratiques, vous pourrez atteindre jusqu’à 30 % d’économies d’énergie, voire davantage, tout en prolongeant la durée de vie de vos équipements !
🔧 Astuces techniques, bonnes pratiques, réglages intelligents et maintenance préventive pour booster l’efficacité énergétique immédiatement.
1. Pourquoi Chaque Kilowatt Compte ?
- Impact direct du coût énergétique sur les groupes froids industriels
- Lien entre refroidissement process et productivité industrielle
- Objectif : 20 % à 30 % d’économie sans changer tout l’équipement
2. Comprendre les Bases du Fonctionnement Thermodynamique
2.1 Petit rappel : comment fonctionne un groupe froid industriel
- Détente – évaporation – compression – condensation
- COP (Coefficient de Performance) : votre indicateur clé
2.2 Les zones critiques de surconsommation
- Excès de pression de condensation
- Mauvaise surchauffe ou sous-refroidissement
- Encrassements internes invisibles mais dévastateurs
3. Optimisation par Réglages Fins (sans gros investissement)
3.1 Baisser la pression de condensation
- Pourquoi c’est la clé N°1 d’économies massives
- Astuce : comment régler correctement la haute pression selon la température ambiante
- Bon à savoir : limiter le fonctionnement continu des ventilateurs
3.2 Ajuster la surchauffe au plus juste
- Effet direct sur le COP
- Comment contrôler et ajuster la surchauffe avec un simple mano et thermomètre
3.3 Abaisser légèrement la pression d’évaporation
- Comment gagner 5 à 10 % d’énergie avec un simple réglage
- Attention aux limites de fonctionnement de l’évaporateur
4. Maintenance et Nettoyage : Un Gisement Caché d’Économies
4.1 Nettoyer régulièrement les échangeurs (condenseur + évaporateur)
- Pourquoi 1 mm de saleté = +15 % de consommation
- Astuce : fréquence de nettoyage recommandée selon l’environnement industriel
4.2 Vérifier et entretenir les ventilateurs et pompes
- Équilibrage, alignement, nettoyage : des gains rapides
- Signes qui montrent qu’un ventilateur “fatigue” et surconsomme
4.3 Contrôler les niveaux de fluide frigorigène
- Manque ou excès = baisse drastique du rendement
- Test simple pour détecter une fuite lente sans station complexe
5. Piloter l’Installation Plus Intelligemment
5.1 Mettre en place des consignes de température plus réalistes
- Pourquoi on sur-refroidit souvent pour rien
- Comment gagner 3 % à 5 % d’énergie par degré de consigne ajusté
5.2 Prioriser la coupure automatique des équipements
- Asservir la production de froid à la vraie demande
- Astuce : installer des minuteries ou des relais simples pour éviter la marche “à vide”
5.3 Surveillance continue « low tech » avec quelques capteurs
- Températures d’eau de process
- Pressions d’évaporation/condensation
- Enregistrer simplement sur Excel pour détecter les dérives
6. Optimiser la Distribution d’Eau de Refroidissement
6.1 Supprimer les pertes de charge inutiles
- Vérifier les vannes, tuyaux, échangeurs encrassés
- Astuce : comment détecter une perte de charge anormale sans débitmètre
6.2 Ajuster la vitesse des pompes de circulation
- Pourquoi parfois ralentir un peu = énorme économie
- Techniques simples de réglage manuel
6.3 Isolation thermique des réseaux
- Même sur quelques mètres : jusqu’à 5 % d’économie
- Matériaux simples et retour sur investissement ultra-rapide
7. Et si l’air extérieur devenait votre meilleur allié ?
7.1 Utiliser le free-cooling dès que possible
- Abaisser naturellement la température de l’eau sans consommer plus
- Astuce : clapets ou by-pass manuels à bas coût
7.2 Optimiser les échangeurs air/eau
- Nettoyage + bonne orientation = moins de charge frigorifique nécessaire
- Exemple pratique : gain de 7 % sur une installation industrielle existante
8. Focus sur le Comportement des Opérateurs
8.1 Former à la “culture de l’énergie”
- Pourquoi expliquer aux utilisateurs l’intérêt de la consigne correcte
- Astuce : tableau d’affichage simple des gains mensuels
8.2 Éviter les manipulations inutiles
- Mauvais réglages = surconsommation chronique
- Procédures simples pour maintenir les réglages d’origine
9. Résultats Attendus : Simulation de Gains
9.1 Exemples de gains sur installation existante 100 kW frigorifique
- Avant : 0,85 COP / Après : 1,15 COP
- Réduction de 25 à 30 % de la consommation annuelle
- Estimation du gain financier brut annuel
9.2 Lien direct avec le Bilan Carbone
- Réduction des kWh = Réduction des émissions CO₂
- Impact positif sur l’empreinte environnementale
10. Passer à l’Action Dès Maintenant
- Prioriser les actions à “0 €” ou faibles coûts
- Mesurer > Ajuster > Maintenir
- L’énergie la moins chère est celle que vous n’avez pas consommée
📋 Tableau Synthèse – Optimiser un Groupe Froid Industriel et un Refroidissement Process sans Gros Investissement
Action | Effet attendu | Coût | Commentaire technique |
---|---|---|---|
1. Baisser la pression de condensation | Gain de 5 à 10 % d’énergie | 0 € | Ajustement simple des régulations ou thermostat |
2. Ajuster la surchauffe au plus juste | Amélioration du COP de 2 à 5 % | 0 € | Réglage détendeur manuel ou électronique |
3. Nettoyer condenseurs/évaporateurs | Gain de 10 à 15 % d’énergie | Faible (nettoyant spécifique ou eau sous pression) | Récurrence : 2 à 4 fois/an selon environnement |
4. Vérifier/entretenir ventilateurs et pompes | Gain de 2 à 4 % | 0 € à très faible (maintenance interne) | Contrôle équilibrage et alignement, graissage éventuel |
5. Corriger les niveaux de fluide frigorigène | Gain de 5 à 8 % | Faible (contrôle + appoint éventuel) | Evite les surconsommations et usures prématurées |
6. Ajuster les consignes de température process | Gain de 3 à 5 % par °C | 0 € | Souvent sur-refroidissement inutile en production |
7. Asservir fonctionnement ventilateurs/pompes à la demande | Gain de 5 à 10 % | Très faible (relais ou minuterie) | Limite le fonctionnement à vide |
8. Installer quelques capteurs basse technologie (pression/température/débit) | Surveillance + détection précoce de dérives | Faible coût (100-500 €) | Permet un pilotage très efficace sans gros SCADA |
9. Supprimer les pertes de charge dans les circuits d’eau | Gain de 3 à 6 % | Faible (reprise de tuyauteries ou nettoyage) | Vérifier filtres, vannes partiellement fermées |
10. Optimiser l’isolation des réseaux d’eau | Gain de 2 à 5 % | Faible (matériau isolant) | Priorité aux points sensibles (sortie de groupe, vannes, brides) |
11. Exploiter le free-cooling extérieur | Jusqu’à 15 % d’économie saisonnière | Faible (by-pass manuel ou clapets) | Fonctionne idéalement en mi-saison/hiver |
12. Sensibiliser et former les opérateurs | Gain global de 5 à 10 % par bonnes pratiques | 0 € (interne) | Culture de la consigne juste et de l’arrêt intelligent |
13. Mettre en place un tableau de suivi simple (Excel) | Suivi des dérives = économies pérennes | 0 € | Mesurer pour piloter ! |
📈 En résumé :
- Effet cumulatif potentiel : 20 à 35 % d’économie d’énergie selon l’état initial de l’installation.
- Coût global estimé : quasiment nul à quelques centaines d’euros maximum.
- Retour sur investissement : immédiat (dès les premières factures d’électricité).
Modèle de tableau de suivi énergétique mensuel avant/après optimisation, pensé de manière pratique et professionnelle pour :
- Suivre la consommation énergétique réelle.
- Comparer avant et après les actions d’optimisation.
- Calculer automatiquement les gains en énergie, en euros, et éventuellement en CO₂ évité.
📋 Modèle de Tableau de Suivi Énergétique Mensuel (Avant / Après Optimisation)
Mois | Énergie Consommée Avant (kWh) | Énergie Consommée Après (kWh) | Économie (kWh) | % Économie | Coût Énergie Avant (€) | Coût Énergie Après (€) | Économie (€) | Émissions CO₂ Évitée (kg) | Commentaires |
---|---|---|---|---|---|---|---|---|---|
Janvier | |||||||||
Février | |||||||||
Mars | |||||||||
Avril | |||||||||
Mai | |||||||||
Juin | |||||||||
Juillet | |||||||||
Août | |||||||||
Septembre | |||||||||
Octobre | |||||||||
Novembre | |||||||||
Décembre |
🛠️ Explication rapide de chaque colonne :
Colonne | Utilité |
---|---|
Énergie Consommée Avant (kWh) | Mesures ou factures avant optimisations. |
Énergie Consommée Après (kWh) | Mesures après mise en œuvre des actions d’économie. |
Économie (kWh) | Différence entre Avant et Après. (formule = Avant – Après) |
% Économie | Pourcentage de gain d’énergie. (formule = (Économie / Avant) × 100) |
Coût Énergie Avant (€) | Coût basé sur prix du kWh (ex. 0,12 €/kWh) |
Coût Énergie Après (€) | Idem mais après actions. |
Économie (€) | Gain financier mensuel. (Avant € – Après €) |
Émissions CO₂ Évitée (kg) | Conversion standard : 0,084 kg CO₂/kWh électrique (valeur moyenne France) |
Commentaires | Anomalies, événements spéciaux (canicule, travaux, etc.) |
🎯 Objectif final :
- Visualiser très vite l’impact des optimisations.
- Communiquer facilement avec la direction / responsables techniques.
- Détecter rapidement les mois atypiques pour corriger.
Checklist action rapide, conçue spécifiquement pour les techniciens de maintenance industrielle, frigoristes, ou intervenants sur groupes froids et installations de refroidissement process.
Elle est sous forme de tableau imprimable, claire, pratique, et directement actionnable en intervention :
📋 Checklist Action Rapide – Optimisation Énergétique Groupes Froids et Installations de Refroidissement
N° | Action | Détail / Astuce | Fréquence conseillée | Coche ✅ |
---|---|---|---|---|
1 | Vérifier les filtres à air d’admission | Nettoyer ou remplacer si colmatage (>350 mbar de perte) | Mensuel | ⬜ |
2 | Contrôler et nettoyer les échangeurs thermiques (condenseurs, évaporateurs) | Détartrer, dépoussiérer pour maintenir efficacité | Mensuel / Trimestriel | ⬜ |
3 | Mesurer la pression d’évaporation et de condensation | Surveiller les dérives, ajuster si besoin | Mensuel | ⬜ |
4 | Vérifier la consigne de température | Ajuster au plus haut tolérable pour le process | Semestriel | ⬜ |
5 | Surveiller les ventilateurs | Nettoyage des pales, contrôle vibrations | Trimestriel | ⬜ |
6 | Inspecter les purgeurs d’eau et les drains automatiques | Remplacer si défaillants pour éviter perte d’efficacité | Trimestriel | ⬜ |
7 | Vérifier l’isolation des tuyauteries et équipements froids | Réparer si endommagée ou manquante | Semestriel | ⬜ |
8 | Contrôler les pressostats et thermostats de régulation | Réglage fin pour éviter surconsommation | Annuel | ⬜ |
9 | Rechercher les fuites de fluide frigorigène | Utiliser détecteur spécifique / Visite annuelle obligatoire | Annuel | ⬜ |
10 | Mesurer la consommation électrique globale | Comparer aux historiques / détecter surconsommation | Mensuel | ⬜ |
11 | Contrôler les réglages de séquence des compresseurs | Prioriser un compresseur efficace + secours auto | Semestriel | ⬜ |
12 | Installer ou vérifier présence de manomètres différentiels | Lecture rapide des pertes de charge | À l’installation / Remplacement si HS | ⬜ |
13 | Ajuster la plage de régulation de pression | Éviter les plages trop courtes générant surconsommation | Annuel | ⬜ |
14 | Installer un suivi simple (compteur kWh / enregistreur) | Facilite détection immédiate des dérives énergétiques | Dès que possible | ⬜ |
15 | Sensibiliser les opérateurs au bon usage des équipements | Petits gestes = grandes économies (portes fermées, pas d’obstructions) | Annuel / Affichage permanent | ⬜ |
🔧 Conseils pratiques pour l’utilisation de cette checklist :
- Imprimer et plastifier pour un usage terrain durable.
- Utiliser en routine préventive, mais aussi après toute intervention corrective.
- Former rapidement les nouveaux techniciens à son usage.
- Archiver chaque checklist remplie pour constituer une traçabilité énergétique.
- Analyser les points récurrents pour planifier les investissements si besoin.
En somme, l’ingénierie des fluides industriels est une discipline importante et diversifiée qui joue un rôle clé dans de nombreuses industries. Elle nécessite une expertise technique et une connaissance approfondie des systèmes de circulation des fluides, de la thermodynamique, de la mécanique des fluides, de la régulation et du contrôle des processus, ainsi que de la sécurité.
Notre blog est une ressource complète pour tout ce qui concerne les fluides industriels. Nous vous encourageons à explorer nos articles, nos guides pratiques et nos ressources de formation pour approfondir vos connaissances et améliorer vos performances énergétiques. N’hésitez pas à nous contacter pour bénéficier de nos services d’ingénierie personnalisés ou pour trouver les produits dont vous avez besoin via notre site de commerce en ligne. Ensemble, nous pouvons aller plus loin dans l’apprentissage et réaliser des économies d’énergie significatives. Contactez-nous dès aujourd’hui à l’adresse suivante :
- Guide pour choisir un groupe froid industriel
- Lien : Exemple de schémas d’installation
- Lien : Calcul de la puissance nécessaire et facteurs de corrections usuels
- Le Guide Ultime du Choix des Compresseurs Frigorifiques : Optimisation, Puissance et Régulation
- Installation optimale de groupes froids industriels : Pratiques essentielles et paramètres clés
- Guide : La mise en service initiale d’un groupe froid industriel
- Les Applications du Refroidissement Industriel dans Divers Secteurs
- Guide Pratique pour le Choix d’un Groupe Froid Industriel : Calculs, Installations, Méthodes, Besoins et Critères Essentiels
- Optimiser l’Efficacité Énergétique : Deux Méthodes Ingénieuses pour Récupérer la Chaleur d’un Groupe Froid Industriel
- Guide Pratique : Récupération de Chaleur sur Groupe Froid – Avantages et Mise en Œuvre
- Innovations et Stratégies Avancées dans le Refroidissement Industriel: Vers une Ère Durable et Efficace
- Optimisation Cruciale: Les Répercussions d’un Réseau Industriel Mal Équilibré sur la Performance et la Sécurité
- Optimisation du Dimensionnement des Tuyauteries : Préserver la Pression et Réduire les Pertes de Charge
- Calculs et dimensionnement, installation, optimisation et Maintenance des Groupes Froids Industriels : Guide Complet pour Calcul de Puissance, Facteurs de Correction, et Technologies de Contrôle
- La conception d’un système de refroidissement industriel (Industrial Cooling System)
- Révolutionner le Froid Industriel et le Refroidissement Process avec l’IoT et l’IA : Entre Solutions High Tech, Low Tech, et Approches Hybrides
- Optimiser le Refroidissement Process avec l’IoT et l’IA : Révolutions et Techniques pour les Groupes Froids et Groupes d’Eau Glacée Industriels
- Révolution Technologique des Groupes Froids Industriels et Groupes d’Eau Glacée : Quand l’IA et les IoT Façonnent l’Avenir du Refroidissement Industriel
- FAQ : Groupes Froids Industriels et au Refroidissement Process
- Questions / réponses fréquemment posées sur le thème du refroidissement de process, incluant l’eau glacée, le froid industriel, les groupes froids, et les groupes d’eau glacée
- Quelles sont les erreurs courantes à éviter lors du choix d’un groupe froid industriel pour le refroidissement de son process ?
- Refroidissement Industriel : L’Essentiel sur les Groupes Frigorifiques et les Groupes d’Eau Glacée
- Lien: Notions de base
- Lie0n : Fonctionnement des systèmes de réfrigération
- Lien : applications du froid industriel
- Lien : Avantages et inconvénients
- Lien : En conclusion, le froid industriel est un élément clé de nombreuses industries modernes
- Lien : mesure de débit ultrasonique
- Mesure de Débit d’Eau par Ultrasons : Optimisation des Process Industriels
- Lien : Vitesse des fluides dans les tuyauteries
- Pour réaliser des économies d’énergie avec les installations d’eau glacée (froid industriel)
- Lien : Retrouver la performance de vos échangeurs avec le peigne frigoriste (groupe froid industriel, sécheur air comprimé, …)
- Lien : Réfractomètre : Mesurez facilement la concentration en glycol essentielle pour assurer la sécurité et la performance des installations industrielles
- Lien : Analyse d’huile des équipements : Optimisez la maintenance industrielle (compresseur air comprimé, groupe froid industriel, …)
- Les avantages de la connectivité IoT et I.A. dans les groupes froids industriels : Comment tirer parti des données pour améliorer les performances
- Les tendances émergentes dans les groupes froids industriels : Les nouvelles technologies qui transforment l’industrie du refroidissement
- La sélection du groupe froid industriel adapté à vos besoins : Guide d’achat et recommandations pour une solution optimale
- La sécurité dans les groupes froids industriels : Conseils pour prévenir les accidents et assurer la conformité aux normes de sécurité
- Maximisez la fiabilité de votre groupe froid industriel : Les meilleures pratiques pour éviter les pannes et les temps d’arrêt coûteux
- La maintenance préventive des groupes froids industriels : Astuces pour prolonger la durée de vie de votre équipement
- Les solutions respectueuses de l’environnement pour les groupes froids industriels : Astuces pour réduire l’empreinte carbone de votre installation
- La gestion intelligente des groupes froids industriels : Comment utiliser les systèmes de contrôle avancés pour optimiser les performances
- Les dernières avancées en matière de groupes froids industriels : Les technologies innovantes qui améliorent les performances
- Groupe froid industriel : Optimisez les économies d’énergie en adaptant vos consignes de température
- Optimisez l’efficacité énergétique de votre groupe froid industriel : Astuces pratiques pour réduire la consommation d’énergie
- Maîtrisez la poussière : Astuces innovantes et simples pour protéger vos équipements avec des filtres d’air comprimé dans les environnements poussiéreu
Lien pour achats :
Air Comprimé : 12 Actions Immédiates pour Réduire Votre Consommation Sans Investissement Majeur
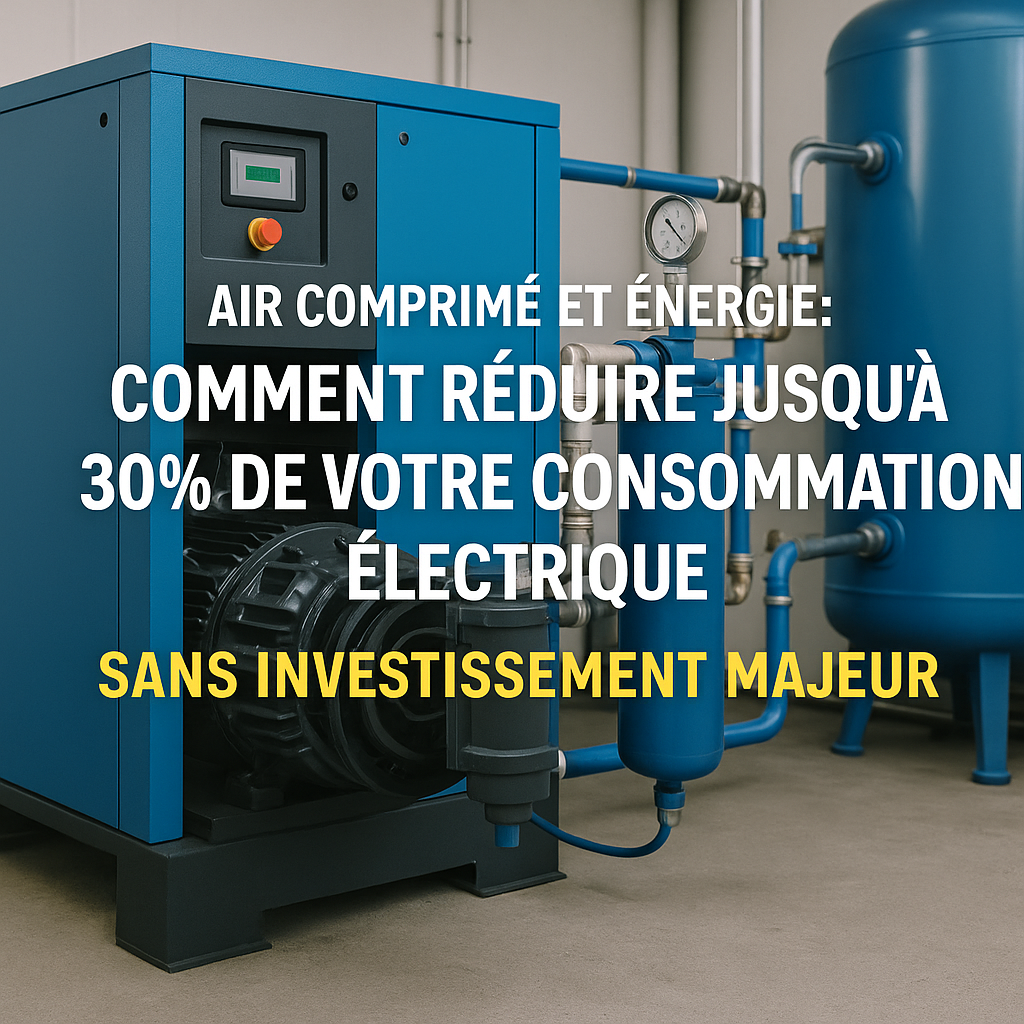
Jusqu’à 30% d’économie d’énergie réalisables sans budget lourd, juste avec du bon sens, des réglages et un peu de méthode
🔍 L’air comprimé, énergie chère… mais optimisable
L’air comprimé est l’une des sources d’énergie les plus utilisées en industrie. C’est aussi l’une des plus coûteuses. On estime que 70 à 90 % de l’énergie électrique consommée par les compresseurs est perdue en chaleur, fuites, surpression ou mauvaise utilisation.
Mais la bonne nouvelle ? Des économies substantielles sont possibles, sans investir dans un nouveau compresseur. Il suffit de corriger les mauvaises pratiques, d’ajuster les réglages, et de mettre en place une routine de suivi simple.
✅ 1. Réduire la pression générale du réseau
🎓 Loi physique : 1 bar de moins = 7% d’économie
Chaque bar supplémentaire demande un effort énergétique exponentiel. Si vous travaillez à 8 bar alors que 6,5 suffiraient, vous gaspillez de l’électricité.
⚙️ Comment faire ?
- Testez une baisse progressive de 0,2 bar par semaine, jusqu’à la pression minimale acceptable par les équipements.
- Surveillez les points sensibles : les postes les plus éloignés, les machines exigeantes.
💡 Astuce :
Un simple changement de consigne dans le pressostat ou la régulation centrale peut économiser plusieurs milliers d’euros par an.
✅ 2. Chasser et réparer les fuites
📊 Les chiffres parlent :
Une fuite de 3 mm à 7 bar = 2 600 €/an de gaspillage. Or 20 à 40 % de l’air produit s’échappe par des fuites.
🔎 Comment agir ?
- Audit visuel régulier des tuyaux, flexibles, raccords.
- Utilisation d’un détecteur ultrason pour les zones bruitées.
- Organisation de journées “chasse aux fuites” participatives.
✅ Bon à savoir :
Réparez immédiatement ou étiquetez les fuites pour action différée, mais ne les ignorez jamais.
✅ 3. Supprimer les soufflages inutiles
💸 Le coût caché d’un pistolet soufflant
Un pistolet soufflant laissé ouvert 1h par jour coûte 300 à 400 €/an.
🔁 Solutions de remplacement :
- Buses économes type “air amplifié”.
- Aspirateurs venturi pour l’évacuation de poussière.
🛠️ Astuce :
Installez des vannes temporisées ou pistolets à gâchette avec retour automatique.
✅ 4. Programmer l’arrêt des compresseurs hors production
🕐 Un compresseur qui tourne la nuit, c’est du gaspillage
Même sans production, les compresseurs consomment pour compenser les fuites.
📆 Solutions simples :
- Programmation horaire des compresseurs.
- Vannes motorisées temporisées ou électromagnétiques.
- Analyse de la courbe de charge sur 7 jours.
🔁 Astuce :
Programmez un arrêt automatique 30 minutes après la dernière baisse de charge, avec relance manuelle.
✅ 5. Optimiser les purges automatiques
⏱️ Les purges à minuterie gaspillent de l’air
Elles s’ouvrent même sans eau à évacuer !
💧 Solution :
- Utiliser des purges sensibles à la condensation (niveau ou conductivité).
- Nettoyer régulièrement les purgeurs pour éviter le blocage en position ouverte.
✅ 6. Nettoyer et changer les filtres colmatés
📉 Impact direct :
Un filtre colmaté = perte de charge = compresseur qui travaille plus = surconsommation électrique.
🧪 Comment contrôler ?
- Lire les pressostats différentiels : au-delà de 350 mbar de perte = remplacement immédiat.
- Anticiper les remplacements selon les courbes de colmatage du fabricant.
✅ 7. Réglage des surcharges de compresseur
⚠️ Danger : réglages par défaut souvent trop élevés
Cela impose une pression plus haute qu’utile, et augmente les cycles de charge.
🔧 Astuce :
Adaptez le réglage à la pression minimale nécessaire aux équipements les plus sensibles.
✅ 8. Améliorer la régulation des compresseurs
🔄 Intervalles de pression trop serrés = compresseurs qui démarrent trop souvent
🔍 Que faire ?
- Élargir la plage de régulation dans la limite des tolérances process.
- Régler finement les pressostats ou les cartes électroniques de régulation.
✅ 9. Répartition optimisée des compresseurs
📊 Le piège du “tout en marche” :
Un compresseur de secours qui tourne à vide est un gouffre énergétique.
🎯 Bonne stratégie :
- Un compresseur principal régulé finement.
- Un ou deux compresseurs en secours ou en soutien automatisé par séquenceur intelligent.
✅ 10. Former et sensibiliser les opérateurs
🧠 Les petits gestes font les grandes économies
Soufflage permanent, ouverture inutile de vannes, non signalement des fuites…
📘 Actions concrètes :
- Fiches réflexes près des postes.
- Formations courtes de 15 minutes avec photos avant/après.
- Challenge “économie d’air” par atelier.
✅ 11. Mesurer, suivre, piloter
📏 Sans mesure, pas de pilotage
Installez des outils simples :
- Manomètres différentiels sur les filtres.
- Débitmètres portatifs à prêter atelier par atelier.
- Compteur d’énergie électrique dédié aux compresseurs.
📊 Bonus :
Créez un tableau Excel de suivi mensuel pour visualiser les effets des actions.
✅ 12. Penser maintenance et écoconception
🛠️ Entretenir, c’est économiser
- Vérifier l’état des tuyauteries.
- Remplacer les joints usés.
- Éviter les coudes inutiles dans les tuyaux : chaque coude = perte de charge !
💬 De petites actions pour de grandes économies
La clé est simple : vous pouvez économiser 15 à 30 % de votre consommation électrique liée à l’air comprimé sans investissement lourd.
- Pas besoin d’acheter un nouveau compresseur.
- Pas besoin de refaire tout le réseau.
Juste un peu de méthode, un peu de rigueur, et beaucoup de bon sens.
🛠️ Plan d’action en 5 étapes
- Faites un diagnostic visuel de vos installations (fuites, soufflages, pression).
- Réglez la pression réseau et les pressostats.
- Formez les opérateurs aux bons gestes.
- Installez des indicateurs simples pour suivre l’évolution.
- Mettez en place une routine mensuelle de vérification.
🚀 Passez à l’action maintenant !
Chaque jour qui passe sans optimisation coûte de l’argent. Vous avez désormais toutes les clés pour lancer une démarche pragmatique, efficace, et surtout rentable.
Pas à pas. Action par action. Résultat par résultat.
« Air Comprimé : 12 Actions Immédiates pour Réduire Votre Consommation Sans Investissement Majeur » — parfait pour un usage opérationnel, une réunion technique, une fiche mémo atelier … :
🧩 Tableau de Synthèse – 12 Actions Immédiates pour Optimiser l’Air Comprimé Sans Investissement Majeur
N° | Action | Objectif | Résultat Attendu | Trucs & Astuces |
---|---|---|---|---|
1️⃣ | Réduction de la pression réseau | Diminuer la charge compresseur | -7% conso par bar réduit | Baisser progressivement par pas de 0,2 bar |
2️⃣ | Réparation des fuites | Supprimer le gaspillage | Jusqu’à 40% de pertes évitées | Audit + détection ultrason + étiquetage |
3️⃣ | Suppression soufflages inutiles | Stopper les pertes continues | 300–400 €/poste/an | Remplacer par buses air amplifié |
4️⃣ | Arrêt auto des compresseurs hors production | Éviter fonctionnement à vide | Gains nocturnes/week-end importants | Programmation horaire + électrovanne |
5️⃣ | Optimisation des purgeurs | Éviter les déclenchements inutiles | Économie d’air inutilement purgé | Privilégier purgeurs à niveau de condensat |
6️⃣ | Entretien des filtres | Réduire pertes de charge | Moins de surpression inutile | Remplacement dès +350 mbar de ΔP |
7️⃣ | Réglage des pressostats | Éviter surrégime inutile | Réduction de la pression globale | Adapter aux besoins réels des machines |
8️⃣ | Amélioration régulation compresseurs | Limiter les cycles courts | Meilleure efficacité | Élargir les plages de consigne intelligemment |
9️⃣ | Répartition intelligente des compresseurs | Optimiser le parc existant | Réduction marche à vide | Séquenceur ou programmation horaire |
🔟 | Sensibilisation des opérateurs | Limiter les mauvaises pratiques | Meilleure discipline terrain | Mini formations, affichage, challenges |
1️⃣1️⃣ | Suivi & mesure des consommations | Piloter par les données | Mesure = réduction ciblée | Débitmètre, compteur élec, manomètre ΔP |
1️⃣2️⃣ | Maintenance des réseaux & composants | Éviter les surpertes par design | Meilleur rendement global | Supprimer coudes, vérifier diamètre adapté |
✅ Bonus
- Économie potentielle sans investissement lourd : 15 à 30 %
- Retour sur investissement : Immédiat dans la majorité des cas
- Outils requis : Clés plates, manomètre, détecteur de fuite, Excel
- Méthodologie recommandée : 1 action/semaine, pilotage par indicateurs simples
En somme, l’ingénierie des fluides industriels est une discipline importante et diversifiée qui joue un rôle clé dans de nombreuses industries. Elle nécessite une expertise technique et une connaissance approfondie des systèmes de circulation des fluides, de la thermodynamique, de la mécanique des fluides, de la régulation et du contrôle des processus, ainsi que de la sécurité.
Notre blog est une ressource complète pour tout ce qui concerne les fluides industriels. Nous vous encourageons à explorer nos articles, nos guides pratiques et nos ressources de formation pour approfondir vos connaissances et améliorer vos performances énergétiques. N’hésitez pas à nous contacter pour bénéficier de nos services d’ingénierie personnalisés ou pour trouver les produits dont vous avez besoin via notre site de commerce en ligne. Ensemble, nous pouvons aller plus loin dans l’apprentissage et réaliser des économies d’énergie significatives. Contactez-nous dès aujourd’hui à l’adresse suivante :
- Guide Ultime pour Choisir le Compresseur d’Air Comprimé Idéal
- Guide Pratique pour la Mise en Service des Compresseurs d’Air Comprimé : Astuces et Bonnes Pratiques
- FAQ sur l’Air Comprimé : Optimisez Votre Énergie, Votre Fiabilité et Votre Productivité
- FAQ : foire aux questions spécifiques sur les cuves d’air comprimé
- FAQ : Sécheurs d’Air Comprimé à Détente Directe
- FAQ : Sécheurs d’Air Comprimé à Masse Thermique
- FAQ : Sécheurs d’Air Comprimé par Adsorption
- Configurations de Montage pour Compresseurs d’Air Comprimé : Optimisation, Performance et Intégration
- Guide Complet : Pourquoi de l’Eau Apparaît Lors de l’Utilisation de l’Air Comprimé et Comment Résoudre Ce Problème
- Guide complet pour choisir et dimensionner un compresseur comprimé : Méthodes, Besoins et Critères Essentiels (piston-s, vis, palettes, centifuge, )
- Guide complet pour choisir et dimensionner un sécheur d’air comprimé : Méthodes, Besoins et Critères Essentiels
- Guide Avancé pour la Sélection des Filtres d’Air Comprimé : Approche Technique, Scientifique et Pédagogique
- Guide Pratique pour le Choix d’une Cuve d’Air Comprimé : Matériau, Pression, Durée de Vie et Capacité
- Guide de Choix pour Purgeurs d’Air Comprimé : Économie d’Énergie et Gestion des Fuites
- Guide Complet pour Choisir et Dimensionner un Réseau d’Air Comprimé : Méthodes, Besoins et Critères Essentiels
- Optimiser l’Énergie : Deux Approches Innovantes pour Récupérer la Chaleur d’un Compresseur d’Air Comprimé
- Optimisation du Réseau d’Air Comprimé : Les Clés d’un Dimensionnement Stratégique
- Choisir le Diamètre Idéal pour Votre Tuyau d’Air Comprimé selon pression : Un Guide Technique Approfondi
- L’Impact des Fuites d’Air Comprimé sur le Débit : Guide Pratique
- Traitement air comprimé / Optimisation de la Qualité de l’Air Comprimé : Guide Complet
- Pourquoi l’eau peut être un problème dans un réseau air comprimé ?
- Traitement écologique et la gestion des condensats d’air comprimé
- Maîtrisez l’Air Comprimé : 10 Astuces pour Optimiser son Utilisation et Réduire les Coûts dans Votre Entreprise
- Comment Réduire les Pertes d’Énergie dans Votre Système de Distribution d’Air Comprimé
- Guide pour Choisir le Sécheur d’Air Comprimé Idéal pour Votre Entreprise
- Sécurité de l’Air Comprimé : Risques, Prévention et Protection
- Guide Essentiel de l’Air Comprimé : Questions Clés Répondues
- Les causes courantes de panne des sécheurs d’air comprimé?
- Mesurer le point de rosée sous pression dans votre système d’air comprimé est crucial pour garantir la qualité de l’air et prévenir les problèmes liés à l’humidité
- Guide ultime pour réparer votre compresseur d’air : Défauts courants, remèdes efficaces et conseils de maintenance
- La sélection du bon raccord rapide air comprimé
- Optimisation Cruciale: Les Répercussions d’un Réseau Industriel Mal Équilibré sur la Performance et la Sécurité
- L’Air Comprimé : Le Pouvoir Invisible au Cœur des Technologies Avancées et des Applications Insolites
- Révolutionner l’Air Comprimé avec l’IoT et l’IA : Entre Solutions High Tech, Low Tech, et Approches Hybrides
- Les Applications et Innovations des Systèmes d’Air Comprimé dans l’Industrie : Guide Complet
- L’Azote en Industrie : Production, Purification et Avantages
- Optimisation des Systèmes d’Air Comprimé : Techniques et Technologies pour Améliorer l’Efficacité Énergétique et Réduire les Coûts Opérationnels
- Lien : Cuves d’Air Comprimé : Déclaration, Vérification et Requalification pour la Sécurité Opérationnelle
- Lien : Exemples d’applications courantes pour des compresseurs d’air comprimé à différentes pressions
- Lien : . Comprendre l’air comprimé
- Lien : Comprendre les équipements d’air comprimé
- Lien : Sélection d’équipements d’air comprimé
- Lien: Les avantages de l’utilisation d’équipements d’air comprimé
- Lien : Maintenance et entretien des équipements d’air comprimé
- Il est important de noter que la conversion entre Nm3/h et m3/h est sensible aux variations de température et de pression, et une conversion précise nécessite des valeurs exactes pour ces paramètres
- FAQ sur l’Air Comprimé : Optimisez Votre Énergie, Votre Fiabilité et Votre Productivité
- Quels sont les matériaux couramment utilisés pour les tuyauteries d’air comprimé ?
- Air Comprimé et Écologie : Vers une Industrie Plus Verte et économie d’énergies
- Les Dangers de l’Air Comprimé et Comment les Éviter
- Maîtrisez la Filtration de l’Air Comprimé : Guide Approfondi sur le Changement et l’Entretien des Éléments Filtrants
- Optimisation de la Pulvérisation : Techniques Avancées pour l’Application de Peinture Automobile
- Régulateurs de Débit et de Pression pour Air Comprimé : Guide Technique et Scientifique
- Optimisation des Systèmes d’Air Comprimé : Techniques et Technologies pour Améliorer l’Efficacité Énergétique et Réduire les Coûts Opérationnels
- Régulation de Température de l’Air Comprimé en Industrie
- Innovations dans l’air comprimé : De la production à l’utilisation
- La conception d’un système d’air comprimé est une tâche complexe
Lien pour achats :
L’Avenir de l’Air Comprimé : Vers une Gestion Prédictive Low Tech & High Tech pour des Économies Durables
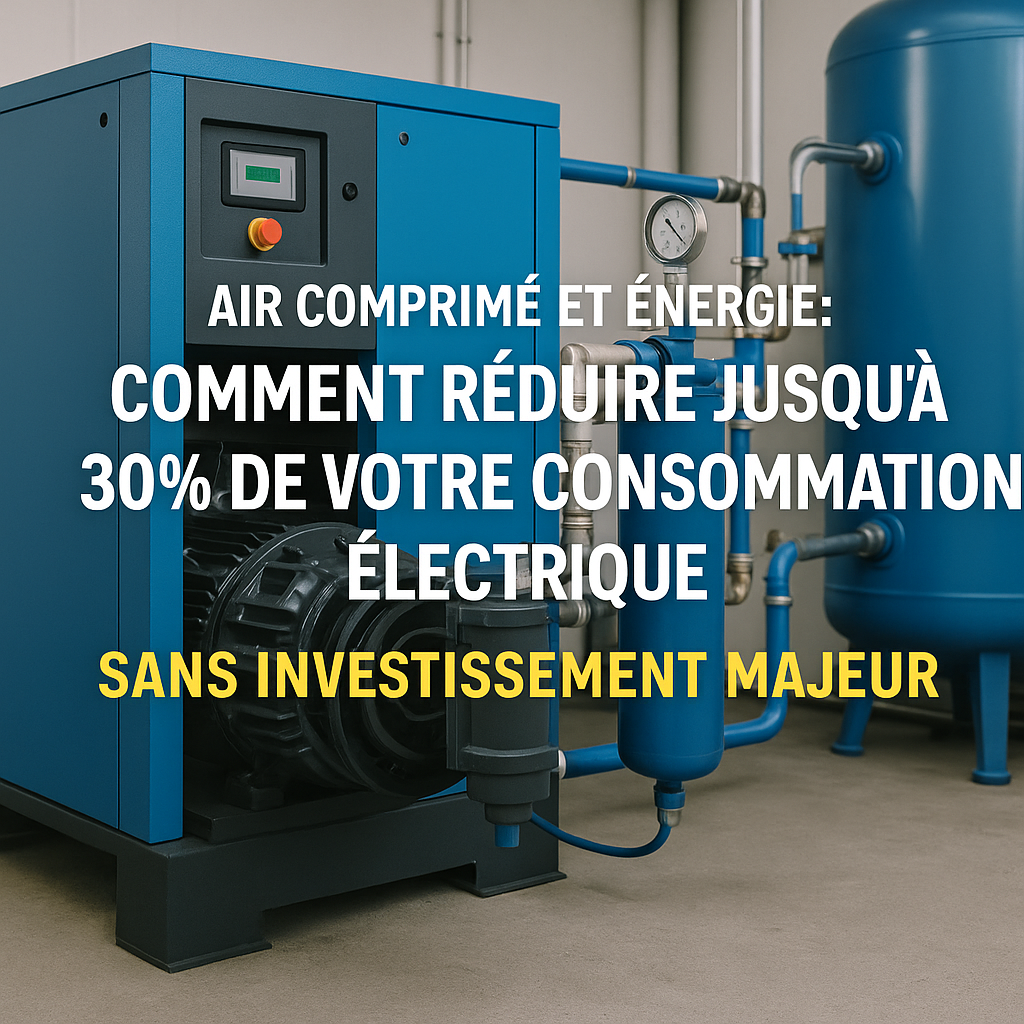
Dans un contexte industriel où la maîtrise des coûts énergétiques et la recherche de performance durable deviennent des objectifs stratégiques, la gestion des réseaux d’air comprimé entre dans une nouvelle ère. Fini le pilotage à l’aveugle, place à la gestion prédictive, à mi-chemin entre solutions low tech pragmatiques et innovations high tech accessibles. Cet article vise à présenter une vision technique, pédagogique et orientée terrain pour mettre en œuvre des outils de supervision intelligents, sans basculer dans l’usine 4.0 inaccessible.
1. Monitoring simple mais efficace : les capteurs connectés à l’essentiel
1.1 Capteurs de pression et de débit différentiel : Installer des capteurs au bon endroit permet de collecter les données vitales : pression en entrée et sortie de filtres, pression réseau, débit total et partiel. Ces mesures suffisent à identifier les pertes de charge, les colmatages, les dérives de fonctionnement, les chutes de pression critiques.
1.2 Outils plug-and-play : De nombreux fabricants proposent aujourd’hui des kits simples d’installation : capteur autonome + boitier de transmission LoRa ou WiFi + application mobile. Coût moyen : 200 à 600 € par point.
1.3 Bon à savoir : Privilégier les capteurs avec enregistrement local + cloud pour conserver les données en cas de coupure.
2. Plateformes de supervision accessibles et scalables
2.1 Outils open source ou SAAS : Il existe aujourd’hui des plateformes de supervision très abordables (Grafana, Ubidots, ThingsBoard, etc.) qui permettent de visualiser les données sur PC, tablette ou smartphone. Elles intègrent des alertes mail/SMS en cas de dérives.
2.2 Visualisation utile pour les opérateurs : L’idée n’est pas de faire du Big Data, mais de créer un tableau de bord clair : pression moyenne, consommation instantanée, alarmes, historique. Même un simple Raspberry Pi peut suffire pour héberger l’interface.
2.3 Astuce : Un code couleur clair (vert = OK, orange = à surveiller, rouge = alarme) permet à n’importe quel technicien de comprendre en un coup d’œil l’état du réseau.
3. L’IoT comme assistant de maintenance prédictive
3.1 Anticiper les défaillances : Un capteur de pression qui chute doucement, un filtre qui sature lentement, une température de sécheur qui grimpe… ces dérives annoncent une panne. L’IoT permet de créer des seuils d’alerte avant incident.
3.2 Maintenance conditionnelle : Plutôt que de changer les filtres tous les 6 mois, on les change quand le delta P dépasse 350 mbar. Résultat : moins de coûts, moins d’arrêts non prévus, et une maintenance ciblée.
3.3 Exemple concret : Sur une ligne avec 3 filtres en cascade, l’installation de pressostats différentiels a permis de décaler le remplacement des cartouches de 2 mois, soit 400 € économisés.
4. Vers une régulation intelligente assistée par l’IA
4.1 Algorithmes adaptatifs : En analysant en continu les profils de consommation, l’IA peut adapter la consigne de pression ou activer/désactiver certains compresseurs selon la demande réelle.
4.2 Apprentissage automatique : Les plateformes cloud dotées de machine learning peuvent détecter des comportements anormaux (fuites, surconsommation) sans avoir à tout programmer.
4.3 Limites à maîtriser : L’IA reste un outil. Une mauvaise configuration peut induire des cycles parasites ou des dérives si les données de base sont erronées.
4.4 Bon à savoir : Toujours prévoir une supervision humaine à intervalle régulier pour valider les algorithmes.
Vers une intelligence pragmatique de l’air comprimé
Passer au digital ne veut pas dire s’engouffrer dans la complexité ou des investissements lourds. Entre les capteurs intelligents bon marché, les plateformes de monitoring simples, les alertes conditionnelles et l’analyse des données, l’industrie dispose d’une boîte à outils redoutablement efficace pour faire de l’air comprimé une énergie optimisée, pilotée, et économe. L’avenir est à ceux qui anticipent… avec bon sens et technologie combinés.
En somme, l’ingénierie des fluides industriels est une discipline importante et diversifiée qui joue un rôle clé dans de nombreuses industries. Elle nécessite une expertise technique et une connaissance approfondie des systèmes de circulation des fluides, de la thermodynamique, de la mécanique des fluides, de la régulation et du contrôle des processus, ainsi que de la sécurité.
Notre blog est une ressource complète pour tout ce qui concerne les fluides industriels. Nous vous encourageons à explorer nos articles, nos guides pratiques et nos ressources de formation pour approfondir vos connaissances et améliorer vos performances énergétiques. N’hésitez pas à nous contacter pour bénéficier de nos services d’ingénierie personnalisés ou pour trouver les produits dont vous avez besoin via notre site de commerce en ligne. Ensemble, nous pouvons aller plus loin dans l’apprentissage et réaliser des économies d’énergie significatives. Contactez-nous dès aujourd’hui à l’adresse suivante :
- Guide Ultime pour Choisir le Compresseur d’Air Comprimé Idéal
- Guide Pratique pour la Mise en Service des Compresseurs d’Air Comprimé : Astuces et Bonnes Pratiques
- FAQ sur l’Air Comprimé : Optimisez Votre Énergie, Votre Fiabilité et Votre Productivité
- FAQ : foire aux questions spécifiques sur les cuves d’air comprimé
- FAQ : Sécheurs d’Air Comprimé à Détente Directe
- FAQ : Sécheurs d’Air Comprimé à Masse Thermique
- FAQ : Sécheurs d’Air Comprimé par Adsorption
- Configurations de Montage pour Compresseurs d’Air Comprimé : Optimisation, Performance et Intégration
- Guide Complet : Pourquoi de l’Eau Apparaît Lors de l’Utilisation de l’Air Comprimé et Comment Résoudre Ce Problème
- Guide complet pour choisir et dimensionner un compresseur comprimé : Méthodes, Besoins et Critères Essentiels (piston-s, vis, palettes, centifuge, )
- Guide complet pour choisir et dimensionner un sécheur d’air comprimé : Méthodes, Besoins et Critères Essentiels
- Guide Avancé pour la Sélection des Filtres d’Air Comprimé : Approche Technique, Scientifique et Pédagogique
- Guide Pratique pour le Choix d’une Cuve d’Air Comprimé : Matériau, Pression, Durée de Vie et Capacité
- Guide de Choix pour Purgeurs d’Air Comprimé : Économie d’Énergie et Gestion des Fuites
- Guide Complet pour Choisir et Dimensionner un Réseau d’Air Comprimé : Méthodes, Besoins et Critères Essentiels
- Optimiser l’Énergie : Deux Approches Innovantes pour Récupérer la Chaleur d’un Compresseur d’Air Comprimé
- Optimisation du Réseau d’Air Comprimé : Les Clés d’un Dimensionnement Stratégique
- Choisir le Diamètre Idéal pour Votre Tuyau d’Air Comprimé selon pression : Un Guide Technique Approfondi
- L’Impact des Fuites d’Air Comprimé sur le Débit : Guide Pratique
- Traitement air comprimé / Optimisation de la Qualité de l’Air Comprimé : Guide Complet
- Pourquoi l’eau peut être un problème dans un réseau air comprimé ?
- Traitement écologique et la gestion des condensats d’air comprimé
- Maîtrisez l’Air Comprimé : 10 Astuces pour Optimiser son Utilisation et Réduire les Coûts dans Votre Entreprise
- Comment Réduire les Pertes d’Énergie dans Votre Système de Distribution d’Air Comprimé
- Guide pour Choisir le Sécheur d’Air Comprimé Idéal pour Votre Entreprise
- Sécurité de l’Air Comprimé : Risques, Prévention et Protection
- Guide Essentiel de l’Air Comprimé : Questions Clés Répondues
- Les causes courantes de panne des sécheurs d’air comprimé?
- Mesurer le point de rosée sous pression dans votre système d’air comprimé est crucial pour garantir la qualité de l’air et prévenir les problèmes liés à l’humidité
- Guide ultime pour réparer votre compresseur d’air : Défauts courants, remèdes efficaces et conseils de maintenance
- La sélection du bon raccord rapide air comprimé
- Optimisation Cruciale: Les Répercussions d’un Réseau Industriel Mal Équilibré sur la Performance et la Sécurité
- L’Air Comprimé : Le Pouvoir Invisible au Cœur des Technologies Avancées et des Applications Insolites
- Révolutionner l’Air Comprimé avec l’IoT et l’IA : Entre Solutions High Tech, Low Tech, et Approches Hybrides
- Les Applications et Innovations des Systèmes d’Air Comprimé dans l’Industrie : Guide Complet
- L’Azote en Industrie : Production, Purification et Avantages
- Optimisation des Systèmes d’Air Comprimé : Techniques et Technologies pour Améliorer l’Efficacité Énergétique et Réduire les Coûts Opérationnels
- Lien : Cuves d’Air Comprimé : Déclaration, Vérification et Requalification pour la Sécurité Opérationnelle
- Lien : Exemples d’applications courantes pour des compresseurs d’air comprimé à différentes pressions
- Lien : . Comprendre l’air comprimé
- Lien : Comprendre les équipements d’air comprimé
- Lien : Sélection d’équipements d’air comprimé
- Lien: Les avantages de l’utilisation d’équipements d’air comprimé
- Lien : Maintenance et entretien des équipements d’air comprimé
- Il est important de noter que la conversion entre Nm3/h et m3/h est sensible aux variations de température et de pression, et une conversion précise nécessite des valeurs exactes pour ces paramètres
- FAQ sur l’Air Comprimé : Optimisez Votre Énergie, Votre Fiabilité et Votre Productivité
- Quels sont les matériaux couramment utilisés pour les tuyauteries d’air comprimé ?
- Air Comprimé et Écologie : Vers une Industrie Plus Verte et économie d’énergies
- Les Dangers de l’Air Comprimé et Comment les Éviter
- Maîtrisez la Filtration de l’Air Comprimé : Guide Approfondi sur le Changement et l’Entretien des Éléments Filtrants
- Optimisation de la Pulvérisation : Techniques Avancées pour l’Application de Peinture Automobile
- Régulateurs de Débit et de Pression pour Air Comprimé : Guide Technique et Scientifique
- Optimisation des Systèmes d’Air Comprimé : Techniques et Technologies pour Améliorer l’Efficacité Énergétique et Réduire les Coûts Opérationnels
- Régulation de Température de l’Air Comprimé en Industrie
- Innovations dans l’air comprimé : De la production à l’utilisation
- La conception d’un système d’air comprimé est une tâche complexe
Lien pour achats :
Écoconception et Bon Sens Industriel : Réduire la Consommation d’Énergie grâce à une Approche Globale du Système d’Air Comprimé
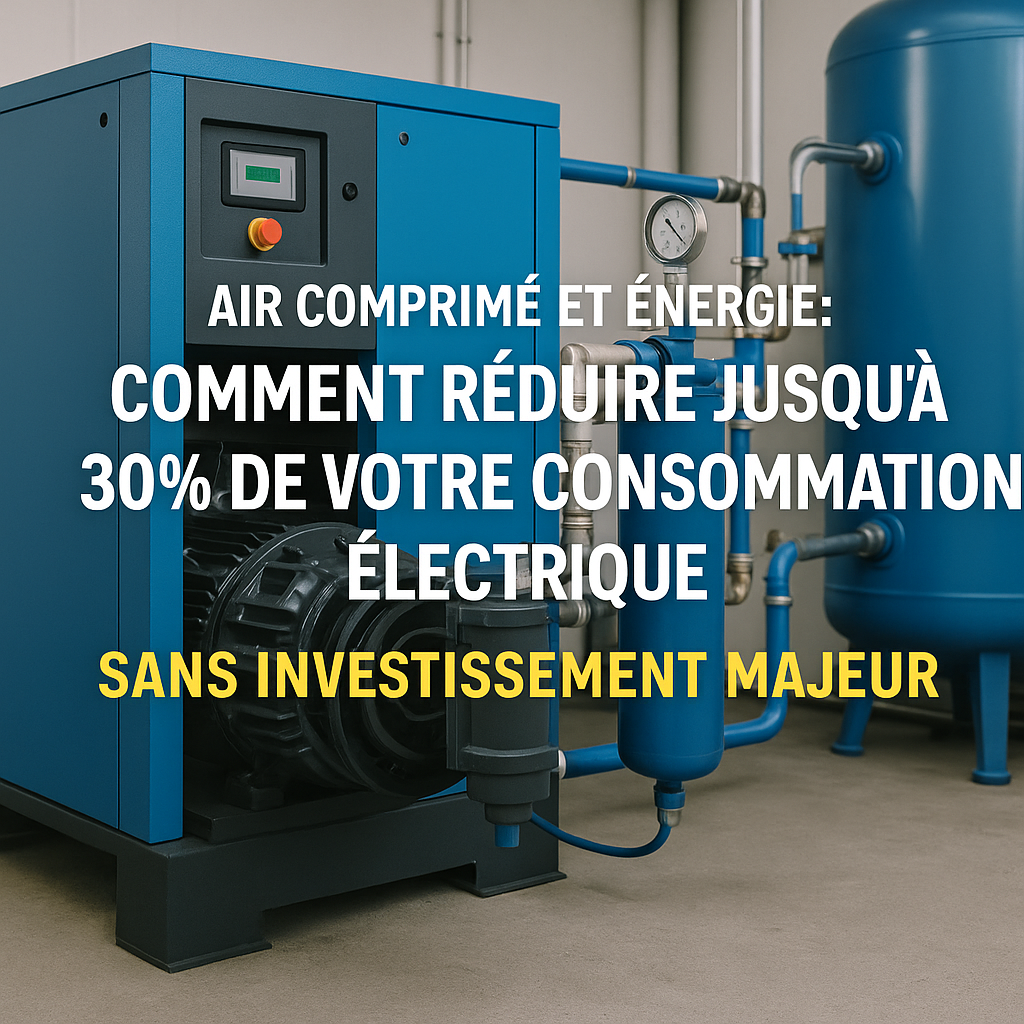
Dans un contexte industriel où la performance énergétique est devenue un levier de compétitivité, l’écoconception appliquée à l’air comprimé offre un formidable potentiel d’optimisation. Souvent perçu comme un poste de coûts fixes, le système d’air comprimé cache pourtant une marge importante d’amélioration sans investissements lourds, simplement par une meilleure conception, un entretien rigoureux et une gestion intelligente.
1. Faire durer les machines : éviter la surconsommation par l’entretien préventif
Bon à savoir : un compresseur mal entretenu peut consommer jusqu’à 15% d’énergie supplémentaire.
L’écoconception ne s’arrête pas au choix du matériel. Elle commence par un objectif simple : assurer une durée de vie optimale aux équipements. Car un compresseur ou un sécheur vieillissant, mal lubrifié, ou aux filtres obstrués, perd en efficacité, génère de la chaleur inutile, et demande plus d’énergie pour produire la même quantité d’air.
Astuces et conseils :
- Respecter le plan de maintenance constructeur.
- Prévoir un suivi par heures de fonctionnement et non par périodicité calendaire.
- Surveiller les jeux mécaniques et les vibrations via capteurs.
- Utiliser de l’huile de qualité et la changer régulièrement.
Un compresseur bien entretenu tourne à son point de fonctionnement optimal, avec une surchauffe limitée, moins de pertes et une durée de vie prolongée.
2. Filtres, sécheurs, purgeurs : entretenir pour économiser
Bon à savoir : 1 bar de perte de charge équivaut à 7% de consommation électrique supplémentaire.
Les éléments de traitement de l’air comprimé jouent un rôle clé dans le rendement global du système. Mais leur efficacité se dégrade avec le temps si l’entretien n’est pas rigoureux.
Filtres :
Un filtre colmaté augmente la perte de charge, ce qui oblige le compresseur à produire plus de pression, donc à consommer plus d’énergie. Le remplacement précoce des éléments filtrants est souvent plus rentable que leur prolongation excessive.
Astuce : installer des pressostats différentiels pour suivre l’évolution de la perte de charge en temps réel.
Sécheurs :
Un sécheur mal dimensionné ou non entretenu dégrade la qualité de l’air, favorisant la corrosion des réseaux et la perte de rendement des outils pneumatiques.
Astuce : vérifier le point de rosée et ajuster le débit traité à la consommation réelle.
Purgeurs :
Les purgeurs automatiques permettent d’éliminer les condensats sans pertes d’air. Mais un purgeur bloqué peut devenir une fuite permanente.
Astuce : préférer les purgeurs capacitifs à déclenchement par niveau de liquide plutôt que les modèles à minuterie.
3. Design des lignes d’air comprimé : optimiser le réseau
Bon à savoir : les pertes de charge sur le réseau peuvent représenter jusqu’à 20% de l’énergie consommée.
L’efficacité du système repose sur un réseau bien pensé. Trop souvent, les canalisations sont installées sans considération pour les débits réels, les pertes de charge ou l’accès à l’entretien.
Règles d’écoconception du réseau :
- Éviter les coudes à 90° qui créent des turbulences et augmentent les pertes.
- Utiliser des diamètres de tuyauterie adaptés aux débits pour réduire la vitesse de l’air.
- Favoriser les réseaux en boucle pour une distribution homogène.
- Installer des points de purge en bas de réseau pour évacuer les condensats.
Astuce : cartographier le réseau avec des mesures de débit et de pression pour identifier les goulots d’étranglement.
L’écoconception, c’est du bon sens appliqué
Optimiser l’air comprimé sans investissement majeur repose avant tout sur une approche systémique et rigoureuse. Entretenir les composants, concevoir un réseau intelligent, ajuster la pression et sensibiliser les opérateurs sont des leviers concrets, mesurables et écologiques. L’industrie de demain sera sobre, non par contrainte, mais par efficacité. Et l’air comprimé, trop longtemps négligé, peut devenir un atout dans cette stratégie.
En somme, l’ingénierie des fluides industriels est une discipline importante et diversifiée qui joue un rôle clé dans de nombreuses industries. Elle nécessite une expertise technique et une connaissance approfondie des systèmes de circulation des fluides, de la thermodynamique, de la mécanique des fluides, de la régulation et du contrôle des processus, ainsi que de la sécurité.
Notre blog est une ressource complète pour tout ce qui concerne les fluides industriels. Nous vous encourageons à explorer nos articles, nos guides pratiques et nos ressources de formation pour approfondir vos connaissances et améliorer vos performances énergétiques. N’hésitez pas à nous contacter pour bénéficier de nos services d’ingénierie personnalisés ou pour trouver les produits dont vous avez besoin via notre site de commerce en ligne. Ensemble, nous pouvons aller plus loin dans l’apprentissage et réaliser des économies d’énergie significatives. Contactez-nous dès aujourd’hui à l’adresse suivante :
- Guide Ultime pour Choisir le Compresseur d’Air Comprimé Idéal
- Guide Pratique pour la Mise en Service des Compresseurs d’Air Comprimé : Astuces et Bonnes Pratiques
- FAQ sur l’Air Comprimé : Optimisez Votre Énergie, Votre Fiabilité et Votre Productivité
- FAQ : foire aux questions spécifiques sur les cuves d’air comprimé
- FAQ : Sécheurs d’Air Comprimé à Détente Directe
- FAQ : Sécheurs d’Air Comprimé à Masse Thermique
- FAQ : Sécheurs d’Air Comprimé par Adsorption
- Configurations de Montage pour Compresseurs d’Air Comprimé : Optimisation, Performance et Intégration
- Guide Complet : Pourquoi de l’Eau Apparaît Lors de l’Utilisation de l’Air Comprimé et Comment Résoudre Ce Problème
- Guide complet pour choisir et dimensionner un compresseur comprimé : Méthodes, Besoins et Critères Essentiels (piston-s, vis, palettes, centifuge, )
- Guide complet pour choisir et dimensionner un sécheur d’air comprimé : Méthodes, Besoins et Critères Essentiels
- Guide Avancé pour la Sélection des Filtres d’Air Comprimé : Approche Technique, Scientifique et Pédagogique
- Guide Pratique pour le Choix d’une Cuve d’Air Comprimé : Matériau, Pression, Durée de Vie et Capacité
- Guide de Choix pour Purgeurs d’Air Comprimé : Économie d’Énergie et Gestion des Fuites
- Guide Complet pour Choisir et Dimensionner un Réseau d’Air Comprimé : Méthodes, Besoins et Critères Essentiels
- Optimiser l’Énergie : Deux Approches Innovantes pour Récupérer la Chaleur d’un Compresseur d’Air Comprimé
- Optimisation du Réseau d’Air Comprimé : Les Clés d’un Dimensionnement Stratégique
- Choisir le Diamètre Idéal pour Votre Tuyau d’Air Comprimé selon pression : Un Guide Technique Approfondi
- L’Impact des Fuites d’Air Comprimé sur le Débit : Guide Pratique
- Traitement air comprimé / Optimisation de la Qualité de l’Air Comprimé : Guide Complet
- Pourquoi l’eau peut être un problème dans un réseau air comprimé ?
- Traitement écologique et la gestion des condensats d’air comprimé
- Maîtrisez l’Air Comprimé : 10 Astuces pour Optimiser son Utilisation et Réduire les Coûts dans Votre Entreprise
- Comment Réduire les Pertes d’Énergie dans Votre Système de Distribution d’Air Comprimé
- Guide pour Choisir le Sécheur d’Air Comprimé Idéal pour Votre Entreprise
- Sécurité de l’Air Comprimé : Risques, Prévention et Protection
- Guide Essentiel de l’Air Comprimé : Questions Clés Répondues
- Les causes courantes de panne des sécheurs d’air comprimé?
- Mesurer le point de rosée sous pression dans votre système d’air comprimé est crucial pour garantir la qualité de l’air et prévenir les problèmes liés à l’humidité
- Guide ultime pour réparer votre compresseur d’air : Défauts courants, remèdes efficaces et conseils de maintenance
- La sélection du bon raccord rapide air comprimé
- Optimisation Cruciale: Les Répercussions d’un Réseau Industriel Mal Équilibré sur la Performance et la Sécurité
- L’Air Comprimé : Le Pouvoir Invisible au Cœur des Technologies Avancées et des Applications Insolites
- Révolutionner l’Air Comprimé avec l’IoT et l’IA : Entre Solutions High Tech, Low Tech, et Approches Hybrides
- Les Applications et Innovations des Systèmes d’Air Comprimé dans l’Industrie : Guide Complet
- L’Azote en Industrie : Production, Purification et Avantages
- Optimisation des Systèmes d’Air Comprimé : Techniques et Technologies pour Améliorer l’Efficacité Énergétique et Réduire les Coûts Opérationnels
- Lien : Cuves d’Air Comprimé : Déclaration, Vérification et Requalification pour la Sécurité Opérationnelle
- Lien : Exemples d’applications courantes pour des compresseurs d’air comprimé à différentes pressions
- Lien : . Comprendre l’air comprimé
- Lien : Comprendre les équipements d’air comprimé
- Lien : Sélection d’équipements d’air comprimé
- Lien: Les avantages de l’utilisation d’équipements d’air comprimé
- Lien : Maintenance et entretien des équipements d’air comprimé
- Il est important de noter que la conversion entre Nm3/h et m3/h est sensible aux variations de température et de pression, et une conversion précise nécessite des valeurs exactes pour ces paramètres
- FAQ sur l’Air Comprimé : Optimisez Votre Énergie, Votre Fiabilité et Votre Productivité
- Quels sont les matériaux couramment utilisés pour les tuyauteries d’air comprimé ?
- Air Comprimé et Écologie : Vers une Industrie Plus Verte et économie d’énergies
- Les Dangers de l’Air Comprimé et Comment les Éviter
- Maîtrisez la Filtration de l’Air Comprimé : Guide Approfondi sur le Changement et l’Entretien des Éléments Filtrants
- Optimisation de la Pulvérisation : Techniques Avancées pour l’Application de Peinture Automobile
- Régulateurs de Débit et de Pression pour Air Comprimé : Guide Technique et Scientifique
- Optimisation des Systèmes d’Air Comprimé : Techniques et Technologies pour Améliorer l’Efficacité Énergétique et Réduire les Coûts Opérationnels
- Régulation de Température de l’Air Comprimé en Industrie
- Innovations dans l’air comprimé : De la production à l’utilisation
- La conception d’un système d’air comprimé est une tâche complexe
Lien pour achats :
Ce Que Vous Pouvez Économiser : Chiffres Clés pour Optimiser Votre Réseau d’Air Comprimé
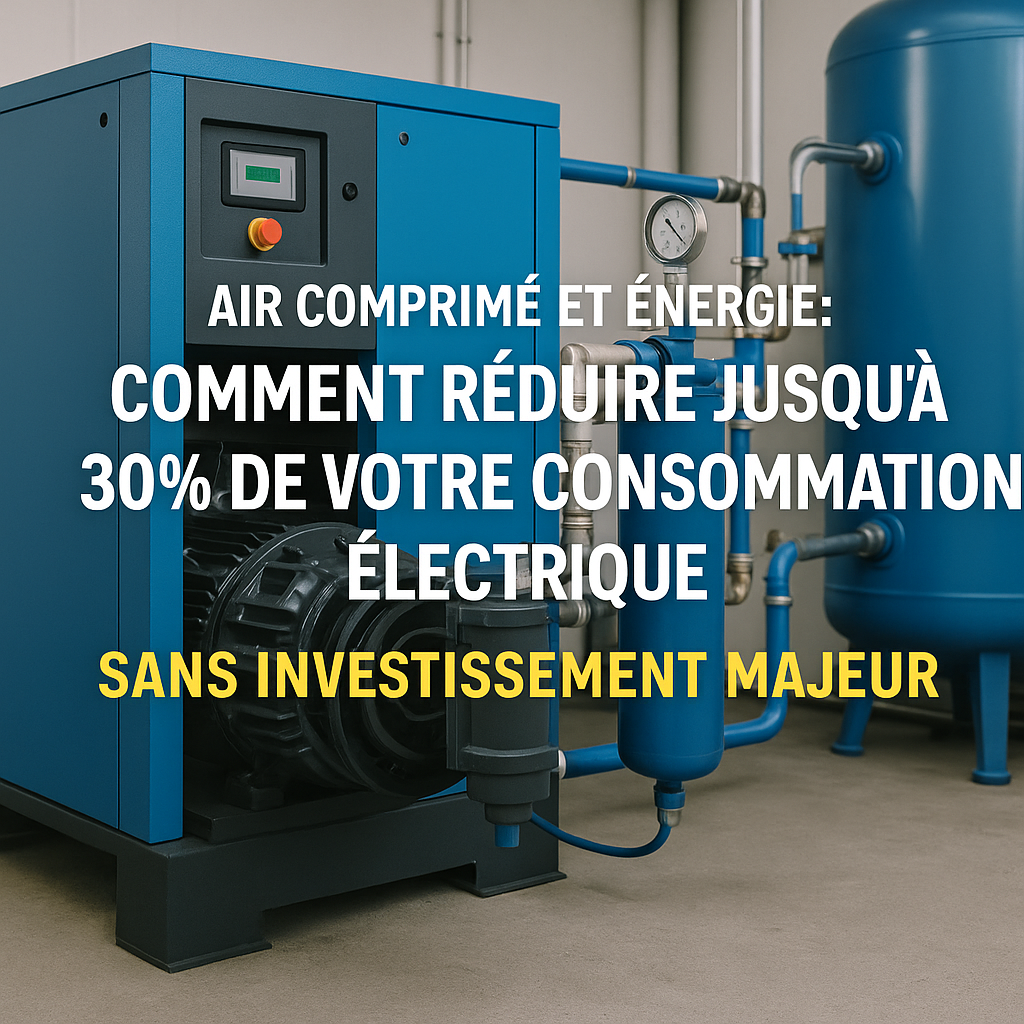
L’air comprimé, un fluide coûteux sous-estimé
L’air comprimé représente généralement 8 à 12 % de la facture énergétique globale d’un site industriel. Malgré cela, il est souvent considéré comme un coût fixe, inévitable. Pourtant, les possibilités d’économie sont réelles, immédiates et mesurables. Dans cet article, nous allons analyser les chiffres clés à connaître, illustrés par des cas concrets, et démontrer comment des actions simples peuvent conduire à des retours sur investissement ultra-rapides.
5.1 🏋️♂️ Exemple de Consommation : Installation de 100 kW
Prenons une installation type :
- Puissance installée : 100 kW
- Fonctionnement : 4 000 h/an (production 1×8 ou 2×8)
- Coût électrique moyen : 0,14 €/kWh
Consommation annuelle :
Coût annuel :
Bon à savoir : Un compresseur de 100 kW produit environ 12 à 16 m³/min d’air à 7 bar. Chaque m³ d’air a donc un coût énergétique d’environ 0,02 € à 0,04 €, selon les pertes.
5.2 📅 Simulation de Gains : Avec et Sans Optimisation
Scénario 1 : Aucune action d’amélioration
- Fuites estimées à 20 %
- Filtres colmatés, perte de charge > 600 mbar
- Pression de régulation à 8 bar (au lieu de 6,5 bar)
Surcoût annuel estimé :
- Fuites : 20 % de 56 000 € = 11 200 €
- Perte de charge : +5 % = 2 800 €
- Surpression : +10 % = 5 600 €
Total surcoût : 19 600 €/an
Scénario 2 : Optimisation ciblée
- Réduction des fuites à 5 %
- Changement de filtres
- Réglage pression à 6,5 bar
Gain potentiel :
- Fuites : 8 400 €
- Pression : 5 600 €
- Filtres : 2 800 €
Économie totale : 16 800 €/an
Astuce : Installez un compteur de débit pour vérifier les gains réels après chaque action !
5.3 🧹 Retour sur Investissement Immédiat : Preuve par les Chiffres
Coûts d’optimisation (approximatifs)
- Filtres neufs : 400 €
- Réglage pression : 0 € (simple intervention)
- Réparation fuites : 1 000 € (main d’œuvre + accessoires)
Total investissement : 1 400 €
Gain la première année : 16 800 €
ROI = 1 mois !
Bon à savoir : Certaines aides CEE permettent de subventionner jusqu’à 50 % des coûts d’audit ou d’équipement.
Formule clé :
5.4 🌍 Bonus : Économie d’Air Comprimé = Réduction du Bilan Carbone
1 kWh électrique = 0,084 kg éq. CO₂ (France – média EDF mix réel 2023)
Réduction énergétique : 120 000 kWh/an économisés
Bon à savoir : Une voiture thermique moyenne émet environ 2 tonnes CO₂/an.
Impact équivalent : Retirer 5 voitures de la circulation chaque année !
Vers la certification ISO 50001
Intégrer des actions d’optimisation sur l’air comprimé renforce la démarche de performance énergétique. Les économies deviennent des arguments environnementaux et stratégiques.
L’air comprimé, levier de performance sous-exploité
Avec un minimum d’analyse et de méthodologie, les gains sur le poste air comprimé sont non seulement significatifs mais aussi immédiats. Cet exemple concret sur une installation de 100 kW est duplicable à toutes tailles d’usines. Mesurez, optimisez, économisez.
Vous voulez aller plus loin ? Pensez audit énergétique, supervision IoT, compresseurs à vitesse variable, ou encore récupération de chaleur !
Un euro investi dans la maîtrise de l’air comprimé, c’est souvent 10 euros gagnés.
En somme, l’ingénierie des fluides industriels est une discipline importante et diversifiée qui joue un rôle clé dans de nombreuses industries. Elle nécessite une expertise technique et une connaissance approfondie des systèmes de circulation des fluides, de la thermodynamique, de la mécanique des fluides, de la régulation et du contrôle des processus, ainsi que de la sécurité.
Notre blog est une ressource complète pour tout ce qui concerne les fluides industriels. Nous vous encourageons à explorer nos articles, nos guides pratiques et nos ressources de formation pour approfondir vos connaissances et améliorer vos performances énergétiques. N’hésitez pas à nous contacter pour bénéficier de nos services d’ingénierie personnalisés ou pour trouver les produits dont vous avez besoin via notre site de commerce en ligne. Ensemble, nous pouvons aller plus loin dans l’apprentissage et réaliser des économies d’énergie significatives. Contactez-nous dès aujourd’hui à l’adresse suivante :
- Guide Ultime pour Choisir le Compresseur d’Air Comprimé Idéal
- Guide Pratique pour la Mise en Service des Compresseurs d’Air Comprimé : Astuces et Bonnes Pratiques
- FAQ sur l’Air Comprimé : Optimisez Votre Énergie, Votre Fiabilité et Votre Productivité
- FAQ : foire aux questions spécifiques sur les cuves d’air comprimé
- FAQ : Sécheurs d’Air Comprimé à Détente Directe
- FAQ : Sécheurs d’Air Comprimé à Masse Thermique
- FAQ : Sécheurs d’Air Comprimé par Adsorption
- Configurations de Montage pour Compresseurs d’Air Comprimé : Optimisation, Performance et Intégration
- Guide Complet : Pourquoi de l’Eau Apparaît Lors de l’Utilisation de l’Air Comprimé et Comment Résoudre Ce Problème
- Guide complet pour choisir et dimensionner un compresseur comprimé : Méthodes, Besoins et Critères Essentiels (piston-s, vis, palettes, centifuge, )
- Guide complet pour choisir et dimensionner un sécheur d’air comprimé : Méthodes, Besoins et Critères Essentiels
- Guide Avancé pour la Sélection des Filtres d’Air Comprimé : Approche Technique, Scientifique et Pédagogique
- Guide Pratique pour le Choix d’une Cuve d’Air Comprimé : Matériau, Pression, Durée de Vie et Capacité
- Guide de Choix pour Purgeurs d’Air Comprimé : Économie d’Énergie et Gestion des Fuites
- Guide Complet pour Choisir et Dimensionner un Réseau d’Air Comprimé : Méthodes, Besoins et Critères Essentiels
- Optimiser l’Énergie : Deux Approches Innovantes pour Récupérer la Chaleur d’un Compresseur d’Air Comprimé
- Optimisation du Réseau d’Air Comprimé : Les Clés d’un Dimensionnement Stratégique
- Choisir le Diamètre Idéal pour Votre Tuyau d’Air Comprimé selon pression : Un Guide Technique Approfondi
- L’Impact des Fuites d’Air Comprimé sur le Débit : Guide Pratique
- Traitement air comprimé / Optimisation de la Qualité de l’Air Comprimé : Guide Complet
- Pourquoi l’eau peut être un problème dans un réseau air comprimé ?
- Traitement écologique et la gestion des condensats d’air comprimé
- Maîtrisez l’Air Comprimé : 10 Astuces pour Optimiser son Utilisation et Réduire les Coûts dans Votre Entreprise
- Comment Réduire les Pertes d’Énergie dans Votre Système de Distribution d’Air Comprimé
- Guide pour Choisir le Sécheur d’Air Comprimé Idéal pour Votre Entreprise
- Sécurité de l’Air Comprimé : Risques, Prévention et Protection
- Guide Essentiel de l’Air Comprimé : Questions Clés Répondues
- Les causes courantes de panne des sécheurs d’air comprimé?
- Mesurer le point de rosée sous pression dans votre système d’air comprimé est crucial pour garantir la qualité de l’air et prévenir les problèmes liés à l’humidité
- Guide ultime pour réparer votre compresseur d’air : Défauts courants, remèdes efficaces et conseils de maintenance
- La sélection du bon raccord rapide air comprimé
- Optimisation Cruciale: Les Répercussions d’un Réseau Industriel Mal Équilibré sur la Performance et la Sécurité
- L’Air Comprimé : Le Pouvoir Invisible au Cœur des Technologies Avancées et des Applications Insolites
- Révolutionner l’Air Comprimé avec l’IoT et l’IA : Entre Solutions High Tech, Low Tech, et Approches Hybrides
- Les Applications et Innovations des Systèmes d’Air Comprimé dans l’Industrie : Guide Complet
- L’Azote en Industrie : Production, Purification et Avantages
- Optimisation des Systèmes d’Air Comprimé : Techniques et Technologies pour Améliorer l’Efficacité Énergétique et Réduire les Coûts Opérationnels
- Lien : Cuves d’Air Comprimé : Déclaration, Vérification et Requalification pour la Sécurité Opérationnelle
- Lien : Exemples d’applications courantes pour des compresseurs d’air comprimé à différentes pressions
- Lien : . Comprendre l’air comprimé
- Lien : Comprendre les équipements d’air comprimé
- Lien : Sélection d’équipements d’air comprimé
- Lien: Les avantages de l’utilisation d’équipements d’air comprimé
- Lien : Maintenance et entretien des équipements d’air comprimé
- Il est important de noter que la conversion entre Nm3/h et m3/h est sensible aux variations de température et de pression, et une conversion précise nécessite des valeurs exactes pour ces paramètres
- FAQ sur l’Air Comprimé : Optimisez Votre Énergie, Votre Fiabilité et Votre Productivité
- Quels sont les matériaux couramment utilisés pour les tuyauteries d’air comprimé ?
- Air Comprimé et Écologie : Vers une Industrie Plus Verte et économie d’énergies
- Les Dangers de l’Air Comprimé et Comment les Éviter
- Maîtrisez la Filtration de l’Air Comprimé : Guide Approfondi sur le Changement et l’Entretien des Éléments Filtrants
- Optimisation de la Pulvérisation : Techniques Avancées pour l’Application de Peinture Automobile
- Régulateurs de Débit et de Pression pour Air Comprimé : Guide Technique et Scientifique
- Optimisation des Systèmes d’Air Comprimé : Techniques et Technologies pour Améliorer l’Efficacité Énergétique et Réduire les Coûts Opérationnels
- Régulation de Température de l’Air Comprimé en Industrie
- Innovations dans l’air comprimé : De la production à l’utilisation
- La conception d’un système d’air comprimé est une tâche complexe
Lien pour achats :
Mesurer pour Piloter : Les Outils de Diagnostic à Faible Coût pour l’Optimisation des Réseaux d’Air Comprimé
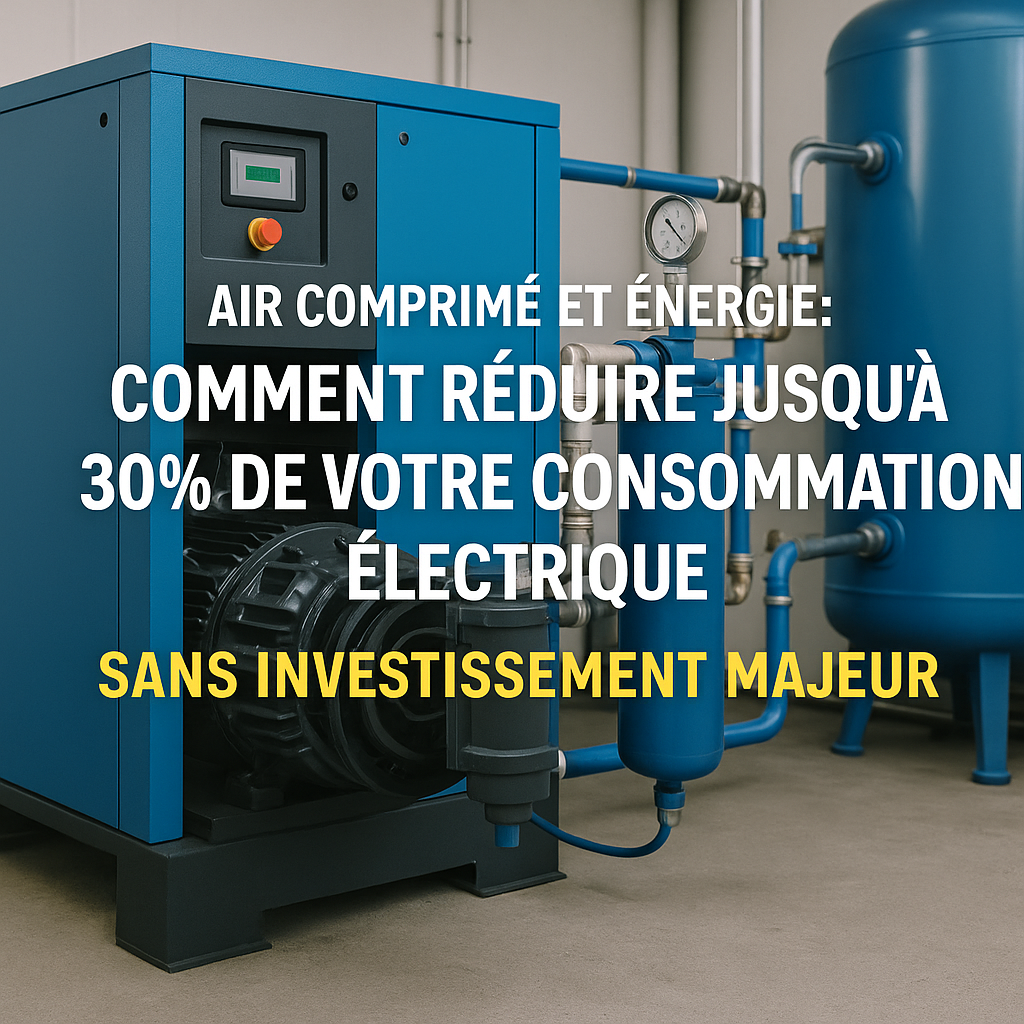
Pourquoi mesurer, et pourquoi maintenant ?
Dans un contexte industriel où la pression énergétique et économique s’intensifie, l’air comprimé reste l’un des fluides les plus coûteux à produire. Mal utilisé, mal mesuré, il devient un gouffre énergétique. Pour autant, optimiser un réseau ne commence ni par l’achat d’un nouveau compresseur, ni par la mise en place d’une IA avancée, mais bien par un geste simple : mesurer.
Cet article propose un tour d’horizon des outils de diagnostic à faible coût, accessibles à toutes les équipes de maintenance et de production. Des solutions simples, concrètes, éprouvées sur le terrain, avec pour objectif : réduire la consommation électrique, améliorer la performance des équipements, et piloter son réseau avec intelligence.
4.1 🎯 Manomètres différentiels : Où les installer, et comment les lire ?
📌 À quoi sert un manomètre différentiel ?
Il permet de mesurer la perte de charge (ou ΔP) entre l’entrée et la sortie d’un composant du réseau (filtre, sécheur, séparateur…). C’est l’outil de base pour diagnostiquer un filtre colmaté, un réseau sous-dimensionné ou une dérive progressive de pression.
Bon à savoir : Une perte de charge de 1 bar sur le réseau augmente la consommation électrique d’environ 7 à 10 % !
✅ Où installer les manomètres différentiels ?
Emplacement | Objectif | Périodicité de contrôle |
---|---|---|
🔘 En amont et aval des filtres | Suivre l’encrassement | Hebdomadaire |
🔘 En entrée et sortie du sécheur | Vérifier les dérives internes | Mensuel |
🔘 Sur collecteurs | Identifier les sections sous-dimensionnées | Trimestriel |
Astuce terrain : Utilisez des raccords rapides ou des vannes quart-de-tour pour installer des manomètres temporaires et diagnostiquer plusieurs zones avec le même appareil.
🧠 Comment bien interpréter les mesures ?
- ΔP neuf < 250 mbar = fonctionnement normal.
- ΔP entre 300 et 500 mbar = filtre à surveiller.
- ΔP > 600 mbar = filtre à remplacer d’urgence : surcoût énergétique immédiat.
4.2 🌀 Débitmètres portatifs : Pourquoi et comment les utiliser ?
🎯 Pourquoi utiliser un débitmètre portatif ?
Les débitmètres permettent de :
- Identifier les débits réels utilisés par atelier ou machine.
- Détecter des fuites (en comparant débit en charge et à vide).
- Évaluer l’efficacité de la régulation du compresseur (modulation, arrêt/démarrage, vitesse variable).
⚙️ Quels modèles choisir ?
Type de débitmètre | Avantages | Inconvénients | Prix indicatif |
---|---|---|---|
🎯 Ultrasonique clamp-on | Pas besoin de couper le réseau, mesure en continu | Moins précis sur petits diamètres | ~1500 à 3000€ |
🎯 Vortex ou turbine portatif | Bonne précision sur circuits bien dimensionnés | Intrusif, nécessite une section de tuyau adaptée | ~500 à 2000€ |
Bon à savoir : Certains fournisseurs proposent la location à la semaine de débitmètres (200 à 300€/semaine), idéal pour les audits ponctuels.
📊 Cas d’usage : Détection de fuite sur ligne inutilisée
- Mesure à vide : débit affiché = 0 ? Parfait.
- Débit résiduel ? → Fuite probable.
- Fermez les vannes de sections → localisez progressivement la fuite.
Astuce : Enregistrez les mesures avec un simple smartphone ou un petit enregistreur pour constituer une base de données d’historique.
4.3 ⚡ Suivi de la consommation électrique via compteur dédié
⚙️ Pourquoi mesurer l’électricité consommée ?
Parce que l’air comprimé est en réalité… de l’électricité transformée ! Et l’électricité, elle, se paie cash. Connaître la consommation précise des compresseurs permet de :
- Calculer le rendement énergétique (kWh/m³ produit).
- Identifier les dérives de performance (compresseur encrassé, régulation inadaptée).
- Justifier des investissements d’optimisation.
🔌 Quels types de compteurs choisir ?
Type | Avantages | Exemple d’usage |
---|---|---|
🧮 Compteur d’énergie monophasé ou triphasé modbus | Intégrable à un automate ou supervision | Suivi continu |
🧮 Prise wattmètre mobile | Mesures ponctuelles simples | Comparatif avant/après intervention |
🧮 Enregistreur autonome (data logger) | Suivi sur 1 à 7 jours | Diagnostic de dérive, charge machine |
Bon à savoir : Un compresseur bien régulé consomme en moyenne 0,12 à 0,20 kWh par m³ produit. Si vous êtes au-delà de 0,25 → optimisations possibles !
🎓 Astuce : croisez les données électriques et de débit
En comparant les kWh consommés et les m³ réellement produits sur une période donnée, vous obtenez le rendement énergétique global, un indicateur clé souvent négligé.
4.4 📈 Suivi via un tableau Excel de consommation mensuelle
🧰 Pourquoi suivre les consommations dans un tableau ?
Parce que ce qui ne se mesure pas… ne se maîtrise pas ! Un simple tableau Excel vous permet de :
- Visualiser les dérives.
- Suivre les résultats des actions d’optimisation.
- Justifier vos investissements auprès de la direction.
📊 Exemple de tableau mensuel
Mois | m³ Produits | kWh consommés | Rendement (kWh/m³) | Observations |
---|---|---|---|---|
Janvier | 190 000 | 25 000 | 0,131 | Filtre neuf posé |
Février | 182 000 | 24 500 | 0,134 | Sécheur colmaté (ΔP = 750 mbar) |
Mars | 185 000 | 22 000 | 0,118 | Réglage pression -0,5 bar |
Astuce terrain :
- Ajoutez une colonne « Coût mensuel en € » selon votre tarif kWh (ex. 0,14 €/kWh).
- Utilisez des codes couleur pour les rendements (vert < 0,15 ; orange entre 0,15 et 0,20 ; rouge > 0,20).
Bon à savoir : En visualisant un pic de consommation sans augmentation de débit, vous détectez une anomalie ou une fuite avant même qu’elle ne soit visible.
🎯 L’action commence par la mesure
Investir dans des outils de mesure simples mais efficaces est la meilleure porte d’entrée vers une maintenance proactive, une baisse des coûts, et une production durable. Chaque mbar perdu, chaque kWh gaspillé a un coût réel. Grâce à ces outils de diagnostic à faible coût, vous devenez acteur de votre performance énergétique.
✅ En résumé : les indispensables à avoir dans sa boîte à outils
Outil | Utilité principale | Budget |
---|---|---|
Manomètre différentiel | Suivi des filtres | < 100 € |
Débitmètre portable | Audit local, détection de fuite | ~ 1000 € (ou location) |
Wattmètre ou enregistreur | Suivi énergétique | 100 à 500 € |
Tableau Excel mensuel | Visualisation des tendances | Gratuit |
En somme, l’ingénierie des fluides industriels est une discipline importante et diversifiée qui joue un rôle clé dans de nombreuses industries. Elle nécessite une expertise technique et une connaissance approfondie des systèmes de circulation des fluides, de la thermodynamique, de la mécanique des fluides, de la régulation et du contrôle des processus, ainsi que de la sécurité.
Notre blog est une ressource complète pour tout ce qui concerne les fluides industriels. Nous vous encourageons à explorer nos articles, nos guides pratiques et nos ressources de formation pour approfondir vos connaissances et améliorer vos performances énergétiques. N’hésitez pas à nous contacter pour bénéficier de nos services d’ingénierie personnalisés ou pour trouver les produits dont vous avez besoin via notre site de commerce en ligne. Ensemble, nous pouvons aller plus loin dans l’apprentissage et réaliser des économies d’énergie significatives. Contactez-nous dès aujourd’hui à l’adresse suivante :
- Guide Ultime pour Choisir le Compresseur d’Air Comprimé Idéal
- Guide Pratique pour la Mise en Service des Compresseurs d’Air Comprimé : Astuces et Bonnes Pratiques
- FAQ sur l’Air Comprimé : Optimisez Votre Énergie, Votre Fiabilité et Votre Productivité
- FAQ : foire aux questions spécifiques sur les cuves d’air comprimé
- FAQ : Sécheurs d’Air Comprimé à Détente Directe
- FAQ : Sécheurs d’Air Comprimé à Masse Thermique
- FAQ : Sécheurs d’Air Comprimé par Adsorption
- Configurations de Montage pour Compresseurs d’Air Comprimé : Optimisation, Performance et Intégration
- Guide Complet : Pourquoi de l’Eau Apparaît Lors de l’Utilisation de l’Air Comprimé et Comment Résoudre Ce Problème
- Guide complet pour choisir et dimensionner un compresseur comprimé : Méthodes, Besoins et Critères Essentiels (piston-s, vis, palettes, centifuge, )
- Guide complet pour choisir et dimensionner un sécheur d’air comprimé : Méthodes, Besoins et Critères Essentiels
- Guide Avancé pour la Sélection des Filtres d’Air Comprimé : Approche Technique, Scientifique et Pédagogique
- Guide Pratique pour le Choix d’une Cuve d’Air Comprimé : Matériau, Pression, Durée de Vie et Capacité
- Guide de Choix pour Purgeurs d’Air Comprimé : Économie d’Énergie et Gestion des Fuites
- Guide Complet pour Choisir et Dimensionner un Réseau d’Air Comprimé : Méthodes, Besoins et Critères Essentiels
- Optimiser l’Énergie : Deux Approches Innovantes pour Récupérer la Chaleur d’un Compresseur d’Air Comprimé
- Optimisation du Réseau d’Air Comprimé : Les Clés d’un Dimensionnement Stratégique
- Choisir le Diamètre Idéal pour Votre Tuyau d’Air Comprimé selon pression : Un Guide Technique Approfondi
- L’Impact des Fuites d’Air Comprimé sur le Débit : Guide Pratique
- Traitement air comprimé / Optimisation de la Qualité de l’Air Comprimé : Guide Complet
- Pourquoi l’eau peut être un problème dans un réseau air comprimé ?
- Traitement écologique et la gestion des condensats d’air comprimé
- Maîtrisez l’Air Comprimé : 10 Astuces pour Optimiser son Utilisation et Réduire les Coûts dans Votre Entreprise
- Comment Réduire les Pertes d’Énergie dans Votre Système de Distribution d’Air Comprimé
- Guide pour Choisir le Sécheur d’Air Comprimé Idéal pour Votre Entreprise
- Sécurité de l’Air Comprimé : Risques, Prévention et Protection
- Guide Essentiel de l’Air Comprimé : Questions Clés Répondues
- Les causes courantes de panne des sécheurs d’air comprimé?
- Mesurer le point de rosée sous pression dans votre système d’air comprimé est crucial pour garantir la qualité de l’air et prévenir les problèmes liés à l’humidité
- Guide ultime pour réparer votre compresseur d’air : Défauts courants, remèdes efficaces et conseils de maintenance
- La sélection du bon raccord rapide air comprimé
- Optimisation Cruciale: Les Répercussions d’un Réseau Industriel Mal Équilibré sur la Performance et la Sécurité
- L’Air Comprimé : Le Pouvoir Invisible au Cœur des Technologies Avancées et des Applications Insolites
- Révolutionner l’Air Comprimé avec l’IoT et l’IA : Entre Solutions High Tech, Low Tech, et Approches Hybrides
- Les Applications et Innovations des Systèmes d’Air Comprimé dans l’Industrie : Guide Complet
- L’Azote en Industrie : Production, Purification et Avantages
- Optimisation des Systèmes d’Air Comprimé : Techniques et Technologies pour Améliorer l’Efficacité Énergétique et Réduire les Coûts Opérationnels
- Lien : Cuves d’Air Comprimé : Déclaration, Vérification et Requalification pour la Sécurité Opérationnelle
- Lien : Exemples d’applications courantes pour des compresseurs d’air comprimé à différentes pressions
- Lien : . Comprendre l’air comprimé
- Lien : Comprendre les équipements d’air comprimé
- Lien : Sélection d’équipements d’air comprimé
- Lien: Les avantages de l’utilisation d’équipements d’air comprimé
- Lien : Maintenance et entretien des équipements d’air comprimé
- Il est important de noter que la conversion entre Nm3/h et m3/h est sensible aux variations de température et de pression, et une conversion précise nécessite des valeurs exactes pour ces paramètres
- FAQ sur l’Air Comprimé : Optimisez Votre Énergie, Votre Fiabilité et Votre Productivité
- Quels sont les matériaux couramment utilisés pour les tuyauteries d’air comprimé ?
- Air Comprimé et Écologie : Vers une Industrie Plus Verte et économie d’énergies
- Les Dangers de l’Air Comprimé et Comment les Éviter
- Maîtrisez la Filtration de l’Air Comprimé : Guide Approfondi sur le Changement et l’Entretien des Éléments Filtrants
- Optimisation de la Pulvérisation : Techniques Avancées pour l’Application de Peinture Automobile
- Régulateurs de Débit et de Pression pour Air Comprimé : Guide Technique et Scientifique
- Optimisation des Systèmes d’Air Comprimé : Techniques et Technologies pour Améliorer l’Efficacité Énergétique et Réduire les Coûts Opérationnels
- Régulation de Température de l’Air Comprimé en Industrie
- Innovations dans l’air comprimé : De la production à l’utilisation
- La conception d’un système d’air comprimé est une tâche complexe
Lien pour achats :
Focus Technique : Lien entre Perte de Charge et Consommation Électrique dans un Réseau d’Air Comprimé
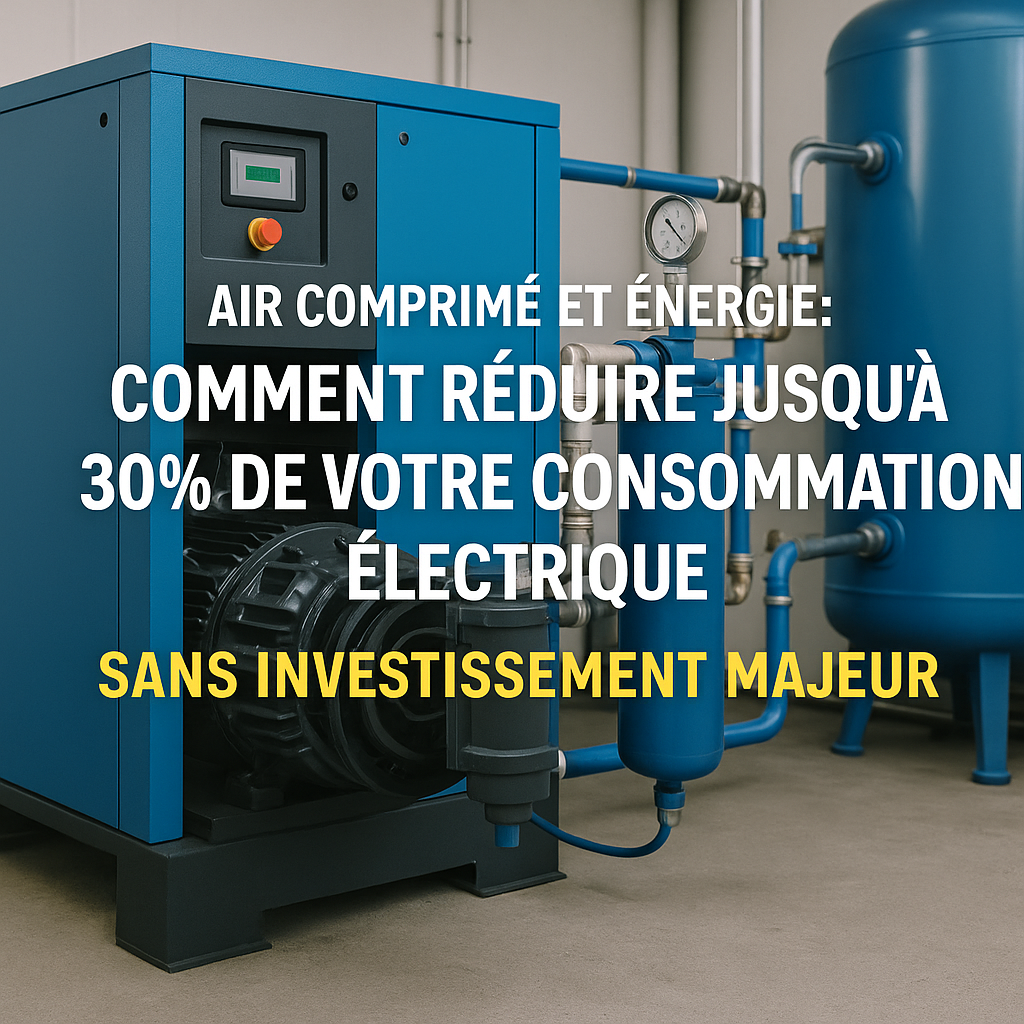
L’air comprimé est un des plus grands consommateurs d’énergie dans l’industrie, et pourtant, beaucoup d’entreprises ignorent les liens cruciaux entre la perte de charge et la consommation électrique. Lorsque la perte de charge augmente, il faut davantage d’énergie pour faire circuler l’air comprimé à travers le système, entraînant ainsi des coûts opérationnels plus élevés. Cet article se concentre sur les aspects techniques de cette relation, explore les lois physiques qui la régissent, fournit un tableau comparatif entre un filtre colmaté et un filtre neuf, et présente une étude de cas sur l’impact réel d’un entretien optimisé.
1. Comprendre la Perte de Charge et son Impact sur la Consommation Électrique
1.1 Qu’est-ce que la Perte de Charge ?
La perte de charge dans un réseau d’air comprimé fait référence à la baisse de pression observée à mesure que l’air se déplace à travers les différents éléments du système : compresseur, tuyaux, filtres, vannes, et autres composants. Cette perte est due à la résistance au flux d’air exercée par ces composants, et son impact direct est une augmentation de la consommation d’énergie.
1.2 La Loi de Darcy : Comprendre la Relation avec la Perte de Charge
La loi de Darcy est une relation mathématique qui modélise le flux de fluides dans des milieux poreux et est applicable dans le cas des réseaux d’air comprimé. Elle est formulée ainsi :
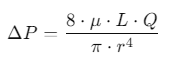
Où :
- ΔP : perte de charge (en Pa)
- μ\muμ : viscosité dynamique de l’air (en Pa.s)
- L : longueur du tuyau (en m)
- Q : débit volumétrique (en m³/s)
- r : rayon du tuyau (en m)
Cette formule montre que la perte de charge est proportionnelle au débit, à la longueur du tuyau, et à la viscosité de l’air, tout en étant inversement proportionnelle au rayon du tuyau. Ainsi, plus le débit est important, plus la perte de charge augmente, ce qui entraîne une augmentation de la consommation d’énergie pour compenser cette résistance.
Astuce technique : Lorsque vous effectuez un entretien du réseau, vérifiez également l’état des tuyaux et des raccords. Une usure ou une accumulation de résidus dans les conduits peut significativement augmenter la perte de charge.
2. L’Impact des Filtres sur la Perte de Charge et la Consommation Électrique
2.1 Filtre Neuf vs. Filtre Colmaté
Les filtres sont un composant clé dans un réseau d’air comprimé. Leur rôle est de purifier l’air et d’empêcher que des contaminants n’atteignent les équipements en aval. Cependant, les filtres ont une résistance naturelle au passage de l’air, et lorsque le filtre se colmate (avec de la poussière, de l’huile ou de l’eau), la perte de charge augmente de manière significative.
📊 Tableau comparatif : Filtre Colmaté vs. Filtre Neuf
Critère | Filtre Neuf | Filtre Colmaté |
---|---|---|
Perte de charge (Pa) | 30 à 50 Pa | 150 à 200 Pa |
Coût énergétique annuel (€/an) | 50 € | 200 € |
Débit d’air (m³/h) | 1000 m³/h | 850 m³/h |
Maintenance (Fréquence) | Tous les 6 mois | Tous les 3 mois |
Impact sur la performance | Efficacité optimale | Baisse d’efficacité |
Explication : Un filtre colmaté peut entraîner une perte de charge beaucoup plus importante, ce qui oblige le compresseur à consommer beaucoup plus d’énergie pour maintenir le même débit d’air. Le coût énergétique annuel peut être multiplié par quatre dans des conditions extrêmes de colmatage.
3. Étude de Cas : Impact d’un Entretien Optimisé
3.1 Contexte de l’Installation
Prenons l’exemple d’une usine qui utilise un réseau d’air comprimé avec plusieurs compresseurs pour alimenter des outils pneumatiques. Le système est équipé de filtres qui n’ont pas été changés depuis plusieurs années. Une analyse de la consommation énergétique révèle une surconsommation de 15% par rapport à un réseau similaire, avec un colmatage des filtres visible dans plusieurs zones du réseau.
3.2 Intervention : Remplacement des Filtres et Réglage de la Pression
Afin d’optimiser la consommation, les filtres ont été remplacés par des filtres neufs et la pression de fonctionnement a été ajustée. Initialement, la pression de l’air comprimé était réglée à 8 bars, mais un test a été effectué en réduisant la pression à 7 bars sans compromettre la qualité de l’air.
Résultats de l’optimisation :
- Réduction de la consommation énergétique de 15% en un mois.
- La perte de charge est tombée de 200 Pa à 50 Pa.
- Le débit d’air est resté stable, et les performances des équipements en aval sont restées optimales.
- L’usure des compresseurs a été réduite de 10%, ce qui a conduit à une réduction des coûts de maintenance.
Astuce pratique : L’optimisation de la pression est l’un des leviers les plus puissants pour économiser de l’énergie, tant que les besoins en pression des équipements en aval sont respectés.
4. Calcul du Coût Réel de la Consommation d’Air Comprimé : Un Outil Pratique
4.1 Coût de l’air comprimé par m³
Pour évaluer l’impact de la perte de charge et de la consommation énergétique, il est utile de calculer le coût réel de l’air comprimé. Voici une méthode simple pour obtenir cette valeur :
Coût annuel de l’air comprimé = (Puissance consommée en kW×Heures de fonctionnement par an × Coût de l’électricité
Exemple : Si votre compresseur consomme 15 kW, fonctionne 4000 heures par an, et que le coût de l’électricité est de 0,12 €/kWh : Coût annuel de l’air comprimé = 15 × 4000 × 0,12= 7200€
En réduisant la perte de charge de 150 Pa à 50 Pa, vous pourriez réduire votre consommation énergétique de 15%, ce qui représente 1 080 € d’économies par an.
5. L’Optimisation Continue : Comment Mesurer et Ajuster
5.1 Outils de Supervision de la Consommation
Pour garantir une optimisation continue, il est conseillé d’installer des systèmes de surveillance IoT pour suivre en temps réel les pertes de charge et la consommation d’énergie. Ces outils permettent de détecter immédiatement les anomalies dans le système, comme des fuites ou des fluctuations de pression.
Bon à savoir : Un compteur d’air comprimé connecté peut fournir des données en temps réel sur la pression, la consommation énergétique, et le rendement du système. Ces données peuvent être utilisées pour ajuster les paramètres de régulation et planifier les maintenances de manière plus proactive.
5.2 Planification des Entretiens et Remplacements de Filtres
Les filtres doivent être changés régulièrement, même si la perte de charge ne semble pas importante. Le remplacement doit être effectué avant que la perte de charge n’atteigne 200 Pa. Ce remplacement, associé à un ajustement de la pression, peut entraîner des économies substantielles sur le long terme.
Optimiser la Perte de Charge, C’est Optimiser les Coûts Énergétiques
La perte de charge dans un réseau d’air comprimé est l’un des facteurs les plus influents sur la consommation d’énergie. En appliquant des stratégies de maintenance et de régulation, comme le remplacement des filtres colmatés, l’optimisation de la pression et l’utilisation de systèmes de supervision pour suivre en temps réel les performances du réseau, il est possible de réaliser des économies d’énergie importantes.
Une analyse régulière de la perte de charge, des ajustements de la pression et des remplacements planifiés des filtres permettent de réduire la consommation énergétique de manière mesurable, tout en préservant les performances et la durée de vie des équipements.
En somme, l’ingénierie des fluides industriels est une discipline importante et diversifiée qui joue un rôle clé dans de nombreuses industries. Elle nécessite une expertise technique et une connaissance approfondie des systèmes de circulation des fluides, de la thermodynamique, de la mécanique des fluides, de la régulation et du contrôle des processus, ainsi que de la sécurité.
Notre blog est une ressource complète pour tout ce qui concerne les fluides industriels. Nous vous encourageons à explorer nos articles, nos guides pratiques et nos ressources de formation pour approfondir vos connaissances et améliorer vos performances énergétiques. N’hésitez pas à nous contacter pour bénéficier de nos services d’ingénierie personnalisés ou pour trouver les produits dont vous avez besoin via notre site de commerce en ligne. Ensemble, nous pouvons aller plus loin dans l’apprentissage et réaliser des économies d’énergie significatives. Contactez-nous dès aujourd’hui à l’adresse suivante :
- Guide Ultime pour Choisir le Compresseur d’Air Comprimé Idéal
- Guide Pratique pour la Mise en Service des Compresseurs d’Air Comprimé : Astuces et Bonnes Pratiques
- FAQ sur l’Air Comprimé : Optimisez Votre Énergie, Votre Fiabilité et Votre Productivité
- FAQ : foire aux questions spécifiques sur les cuves d’air comprimé
- FAQ : Sécheurs d’Air Comprimé à Détente Directe
- FAQ : Sécheurs d’Air Comprimé à Masse Thermique
- FAQ : Sécheurs d’Air Comprimé par Adsorption
- Configurations de Montage pour Compresseurs d’Air Comprimé : Optimisation, Performance et Intégration
- Guide Complet : Pourquoi de l’Eau Apparaît Lors de l’Utilisation de l’Air Comprimé et Comment Résoudre Ce Problème
- Guide complet pour choisir et dimensionner un compresseur comprimé : Méthodes, Besoins et Critères Essentiels (piston-s, vis, palettes, centifuge, )
- Guide complet pour choisir et dimensionner un sécheur d’air comprimé : Méthodes, Besoins et Critères Essentiels
- Guide Avancé pour la Sélection des Filtres d’Air Comprimé : Approche Technique, Scientifique et Pédagogique
- Guide Pratique pour le Choix d’une Cuve d’Air Comprimé : Matériau, Pression, Durée de Vie et Capacité
- Guide de Choix pour Purgeurs d’Air Comprimé : Économie d’Énergie et Gestion des Fuites
- Guide Complet pour Choisir et Dimensionner un Réseau d’Air Comprimé : Méthodes, Besoins et Critères Essentiels
- Optimiser l’Énergie : Deux Approches Innovantes pour Récupérer la Chaleur d’un Compresseur d’Air Comprimé
- Optimisation du Réseau d’Air Comprimé : Les Clés d’un Dimensionnement Stratégique
- Choisir le Diamètre Idéal pour Votre Tuyau d’Air Comprimé selon pression : Un Guide Technique Approfondi
- L’Impact des Fuites d’Air Comprimé sur le Débit : Guide Pratique
- Traitement air comprimé / Optimisation de la Qualité de l’Air Comprimé : Guide Complet
- Pourquoi l’eau peut être un problème dans un réseau air comprimé ?
- Traitement écologique et la gestion des condensats d’air comprimé
- Maîtrisez l’Air Comprimé : 10 Astuces pour Optimiser son Utilisation et Réduire les Coûts dans Votre Entreprise
- Comment Réduire les Pertes d’Énergie dans Votre Système de Distribution d’Air Comprimé
- Guide pour Choisir le Sécheur d’Air Comprimé Idéal pour Votre Entreprise
- Sécurité de l’Air Comprimé : Risques, Prévention et Protection
- Guide Essentiel de l’Air Comprimé : Questions Clés Répondues
- Les causes courantes de panne des sécheurs d’air comprimé?
- Mesurer le point de rosée sous pression dans votre système d’air comprimé est crucial pour garantir la qualité de l’air et prévenir les problèmes liés à l’humidité
- Guide ultime pour réparer votre compresseur d’air : Défauts courants, remèdes efficaces et conseils de maintenance
- La sélection du bon raccord rapide air comprimé
- Optimisation Cruciale: Les Répercussions d’un Réseau Industriel Mal Équilibré sur la Performance et la Sécurité
- L’Air Comprimé : Le Pouvoir Invisible au Cœur des Technologies Avancées et des Applications Insolites
- Révolutionner l’Air Comprimé avec l’IoT et l’IA : Entre Solutions High Tech, Low Tech, et Approches Hybrides
- Les Applications et Innovations des Systèmes d’Air Comprimé dans l’Industrie : Guide Complet
- L’Azote en Industrie : Production, Purification et Avantages
- Optimisation des Systèmes d’Air Comprimé : Techniques et Technologies pour Améliorer l’Efficacité Énergétique et Réduire les Coûts Opérationnels
- Lien : Cuves d’Air Comprimé : Déclaration, Vérification et Requalification pour la Sécurité Opérationnelle
- Lien : Exemples d’applications courantes pour des compresseurs d’air comprimé à différentes pressions
- Lien : . Comprendre l’air comprimé
- Lien : Comprendre les équipements d’air comprimé
- Lien : Sélection d’équipements d’air comprimé
- Lien: Les avantages de l’utilisation d’équipements d’air comprimé
- Lien : Maintenance et entretien des équipements d’air comprimé
- Il est important de noter que la conversion entre Nm3/h et m3/h est sensible aux variations de température et de pression, et une conversion précise nécessite des valeurs exactes pour ces paramètres
- FAQ sur l’Air Comprimé : Optimisez Votre Énergie, Votre Fiabilité et Votre Productivité
- Quels sont les matériaux couramment utilisés pour les tuyauteries d’air comprimé ?
- Air Comprimé et Écologie : Vers une Industrie Plus Verte et économie d’énergies
- Les Dangers de l’Air Comprimé et Comment les Éviter
- Maîtrisez la Filtration de l’Air Comprimé : Guide Approfondi sur le Changement et l’Entretien des Éléments Filtrants
- Optimisation de la Pulvérisation : Techniques Avancées pour l’Application de Peinture Automobile
- Régulateurs de Débit et de Pression pour Air Comprimé : Guide Technique et Scientifique
- Optimisation des Systèmes d’Air Comprimé : Techniques et Technologies pour Améliorer l’Efficacité Énergétique et Réduire les Coûts Opérationnels
- Régulation de Température de l’Air Comprimé en Industrie
- Innovations dans l’air comprimé : De la production à l’utilisation
- La conception d’un système d’air comprimé est une tâche complexe
Lien pour achats :
Formation et Sensibilisation des Opérateurs : Petits Gestes, Grandes Économies en Air Comprimé
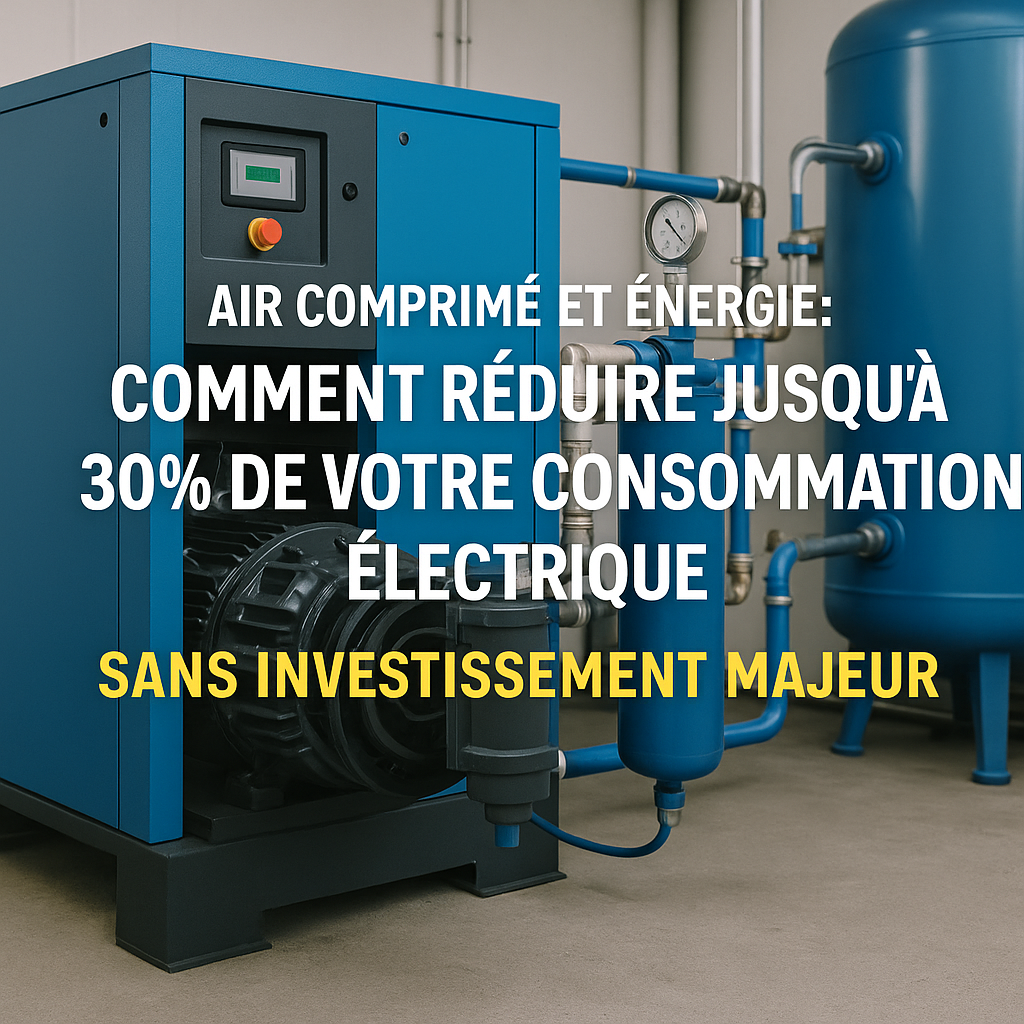
Dans les systèmes industriels, l’air comprimé est souvent considéré comme un « quatrième fluide » vital, au même titre que l’eau, l’électricité ou le gaz. Pourtant, il reste l’un des plus coûteux à produire. Une partie importante de ce coût ne vient pas des équipements, mais du comportement des utilisateurs. La formation et la sensibilisation des opérateurs représentent donc un levier majeur pour réduire les pertes et optimiser la performance énergétique. Dans cet article, nous allons détailler comment de simples gestes, bien appliqués par les opérateurs, peuvent se traduire par des économies substantielles.
1. Pourquoi impliquer les opérateurs ?
1.1 L’opérateur : chaînon clé de la consommation d’air
Un réseau d’air comprimé peut être parfaitement conçu, mais si l’utilisateur final laisse des purges ouvertes, ne ferme pas les arrivées d’air sur des machines à l’arrêt, ou utilise des soufflages inappropriés, alors toute la stratégie d’efficacité s’effondre.
1.2 Rôle des opérateurs dans la détection précoce
Les fuites d’air, les bruits anormaux, les chutes de pression ou les comportements inhabituels peuvent être détectés rapidement par les opérateurs formés. Ils deviennent alors de véritables capteurs humains de performance.
2. Les petits gestes qui changent tout
2.1 Fermer les vannes en fin de poste
Astuce : Installer des vannes quart de tour avec poignées visibles. Les opérateurs peuvent couper l’air facilement et vérifier l’état d’ouverture d’un simple coup d’œil.
2.2 Surveiller et signaler les fuites
Bon à savoir : Une fuite de 1 mm à 7 bars coûte environ 1000 €/an en énergie ! Des campagnes d’écoute acoustique peuvent être organisées avec les opérateurs.
2.3 Réduire l’usage des soufflages
Conseil : Remplacer les buses ouvertes par des buses réglementées (type OSHA), ou mieux, par des racleurs mécaniques, des aspirateurs Venturi, ou des balais industriels.
2.4 Purges automatiques intelligentes
Inutile de purger manuellement à chaque poste. Des purgeurs automatiques peuvent être installés sur les réservoirs. L’opérateur n’a plus besoin de déclencher à la main, mais il peut surveiller leur bon fonctionnement.
2.5 Utilisation à la bonne pression
Truc de pro : Chaque bar supplémentaire augmente la consommation d’environ 7 %. Adapter la pression aux besoins réels évite la surconsommation.
3. Créer des Fiches Réflexes
3.1 Format court, visuel, pratique
Chaque poste de travail peut avoir sa fiche « réflexe » avec 3 à 5 consignes illustrées :
- Vanne à fermer
- Bruit à signaler
- Appareil à vérifier
3.2 Rappel des bons gestes
Des pictogrammes simples (check vert / croix rouge) permettent une mémorisation rapide. Ces supports doivent être réactualisés à chaque modification de ligne ou procédé.
3.3 Exemples d’affichages utiles
- « Pensez à fermer l’air en fin de poste »
- « Un bruit suspect ? Prévenez la maintenance »
- « Chaque fuite = des euros qui s’envolent »
4. Formation : outil clé pour responsabiliser
4.1 Modules courts mais réguliers
Plutôt que de longs cours théoriques, il vaut mieux organiser des sessions de 15-30 minutes sur le terrain, avec explications concrètes sur les postes.
4.2 Intégration dans les formations sécurité
Profitez des formations obligatoires (SST, HACCP, ATEX…) pour intégrer un module « air comprimé : bon usage et économie d’énergie ».
4.3 Jeu de rôle ou audits participatifs
Faites intervenir les opérateurs dans des audits internes : à eux de trouver les fuites ou les mauvaises pratiques, sous forme de challenge.
5. Mettre en place une culture de la performance
5.1 Tableaux de bord visuels
Un panneau dans l’atelier affichant :
- le nombre de fuites détectées/réparées
- la consommation d’air par semaine
- les économies réalisées
5.2 Valoriser les bons comportements
Créez un système de récompense symbolique : « Top éco du mois », « meilleure alerte maintenance », etc.
5.3 Inclure les opérateurs dans les réunions techniques
Le retour du terrain est précieux : bruit inhabituel, consommation anormale, baisse de rendement, tout cela peut être capté par les opérateurs avant même que les capteurs n’alertent.
Sensibiliser les opérateurs à l’utilisation de l’air comprimé n’est pas un luxe : c’est une stratégie d’efficacité énergétique. En multipliant les actions simples et visibles (fiches réflexes, affichages, formations ciblées), vous pouvez transformer chaque opérateur en acteur de la performance. Le gain est double : économique, mais aussi humain. Car un opérateur qui comprend ce qu’il fait, et pourquoi il le fait, travaille mieux.
Et surtout, n’oublions pas : chaque bar, chaque mètre cube d’air économisé, c’est de l’argent que l’on ne brûle pas pour rien.
En somme, l’ingénierie des fluides industriels est une discipline importante et diversifiée qui joue un rôle clé dans de nombreuses industries. Elle nécessite une expertise technique et une connaissance approfondie des systèmes de circulation des fluides, de la thermodynamique, de la mécanique des fluides, de la régulation et du contrôle des processus, ainsi que de la sécurité.
Notre blog est une ressource complète pour tout ce qui concerne les fluides industriels. Nous vous encourageons à explorer nos articles, nos guides pratiques et nos ressources de formation pour approfondir vos connaissances et améliorer vos performances énergétiques. N’hésitez pas à nous contacter pour bénéficier de nos services d’ingénierie personnalisés ou pour trouver les produits dont vous avez besoin via notre site de commerce en ligne. Ensemble, nous pouvons aller plus loin dans l’apprentissage et réaliser des économies d’énergie significatives. Contactez-nous dès aujourd’hui à l’adresse suivante :
- Guide Ultime pour Choisir le Compresseur d’Air Comprimé Idéal
- Guide Pratique pour la Mise en Service des Compresseurs d’Air Comprimé : Astuces et Bonnes Pratiques
- FAQ sur l’Air Comprimé : Optimisez Votre Énergie, Votre Fiabilité et Votre Productivité
- FAQ : foire aux questions spécifiques sur les cuves d’air comprimé
- FAQ : Sécheurs d’Air Comprimé à Détente Directe
- FAQ : Sécheurs d’Air Comprimé à Masse Thermique
- FAQ : Sécheurs d’Air Comprimé par Adsorption
- Configurations de Montage pour Compresseurs d’Air Comprimé : Optimisation, Performance et Intégration
- Guide Complet : Pourquoi de l’Eau Apparaît Lors de l’Utilisation de l’Air Comprimé et Comment Résoudre Ce Problème
- Guide complet pour choisir et dimensionner un compresseur comprimé : Méthodes, Besoins et Critères Essentiels (piston-s, vis, palettes, centifuge, )
- Guide complet pour choisir et dimensionner un sécheur d’air comprimé : Méthodes, Besoins et Critères Essentiels
- Guide Avancé pour la Sélection des Filtres d’Air Comprimé : Approche Technique, Scientifique et Pédagogique
- Guide Pratique pour le Choix d’une Cuve d’Air Comprimé : Matériau, Pression, Durée de Vie et Capacité
- Guide de Choix pour Purgeurs d’Air Comprimé : Économie d’Énergie et Gestion des Fuites
- Guide Complet pour Choisir et Dimensionner un Réseau d’Air Comprimé : Méthodes, Besoins et Critères Essentiels
- Optimiser l’Énergie : Deux Approches Innovantes pour Récupérer la Chaleur d’un Compresseur d’Air Comprimé
- Optimisation du Réseau d’Air Comprimé : Les Clés d’un Dimensionnement Stratégique
- Choisir le Diamètre Idéal pour Votre Tuyau d’Air Comprimé selon pression : Un Guide Technique Approfondi
- L’Impact des Fuites d’Air Comprimé sur le Débit : Guide Pratique
- Traitement air comprimé / Optimisation de la Qualité de l’Air Comprimé : Guide Complet
- Pourquoi l’eau peut être un problème dans un réseau air comprimé ?
- Traitement écologique et la gestion des condensats d’air comprimé
- Maîtrisez l’Air Comprimé : 10 Astuces pour Optimiser son Utilisation et Réduire les Coûts dans Votre Entreprise
- Comment Réduire les Pertes d’Énergie dans Votre Système de Distribution d’Air Comprimé
- Guide pour Choisir le Sécheur d’Air Comprimé Idéal pour Votre Entreprise
- Sécurité de l’Air Comprimé : Risques, Prévention et Protection
- Guide Essentiel de l’Air Comprimé : Questions Clés Répondues
- Les causes courantes de panne des sécheurs d’air comprimé?
- Mesurer le point de rosée sous pression dans votre système d’air comprimé est crucial pour garantir la qualité de l’air et prévenir les problèmes liés à l’humidité
- Guide ultime pour réparer votre compresseur d’air : Défauts courants, remèdes efficaces et conseils de maintenance
- La sélection du bon raccord rapide air comprimé
- Optimisation Cruciale: Les Répercussions d’un Réseau Industriel Mal Équilibré sur la Performance et la Sécurité
- L’Air Comprimé : Le Pouvoir Invisible au Cœur des Technologies Avancées et des Applications Insolites
- Révolutionner l’Air Comprimé avec l’IoT et l’IA : Entre Solutions High Tech, Low Tech, et Approches Hybrides
- Les Applications et Innovations des Systèmes d’Air Comprimé dans l’Industrie : Guide Complet
- L’Azote en Industrie : Production, Purification et Avantages
- Optimisation des Systèmes d’Air Comprimé : Techniques et Technologies pour Améliorer l’Efficacité Énergétique et Réduire les Coûts Opérationnels
- Lien : Cuves d’Air Comprimé : Déclaration, Vérification et Requalification pour la Sécurité Opérationnelle
- Lien : Exemples d’applications courantes pour des compresseurs d’air comprimé à différentes pressions
- Lien : . Comprendre l’air comprimé
- Lien : Comprendre les équipements d’air comprimé
- Lien : Sélection d’équipements d’air comprimé
- Lien: Les avantages de l’utilisation d’équipements d’air comprimé
- Lien : Maintenance et entretien des équipements d’air comprimé
- Il est important de noter que la conversion entre Nm3/h et m3/h est sensible aux variations de température et de pression, et une conversion précise nécessite des valeurs exactes pour ces paramètres
- FAQ sur l’Air Comprimé : Optimisez Votre Énergie, Votre Fiabilité et Votre Productivité
- Quels sont les matériaux couramment utilisés pour les tuyauteries d’air comprimé ?
- Air Comprimé et Écologie : Vers une Industrie Plus Verte et économie d’énergies
- Les Dangers de l’Air Comprimé et Comment les Éviter
- Maîtrisez la Filtration de l’Air Comprimé : Guide Approfondi sur le Changement et l’Entretien des Éléments Filtrants
- Optimisation de la Pulvérisation : Techniques Avancées pour l’Application de Peinture Automobile
- Régulateurs de Débit et de Pression pour Air Comprimé : Guide Technique et Scientifique
- Optimisation des Systèmes d’Air Comprimé : Techniques et Technologies pour Améliorer l’Efficacité Énergétique et Réduire les Coûts Opérationnels
- Régulation de Température de l’Air Comprimé en Industrie
- Innovations dans l’air comprimé : De la production à l’utilisation
- La conception d’un système d’air comprimé est une tâche complexe
Lien pour achats :