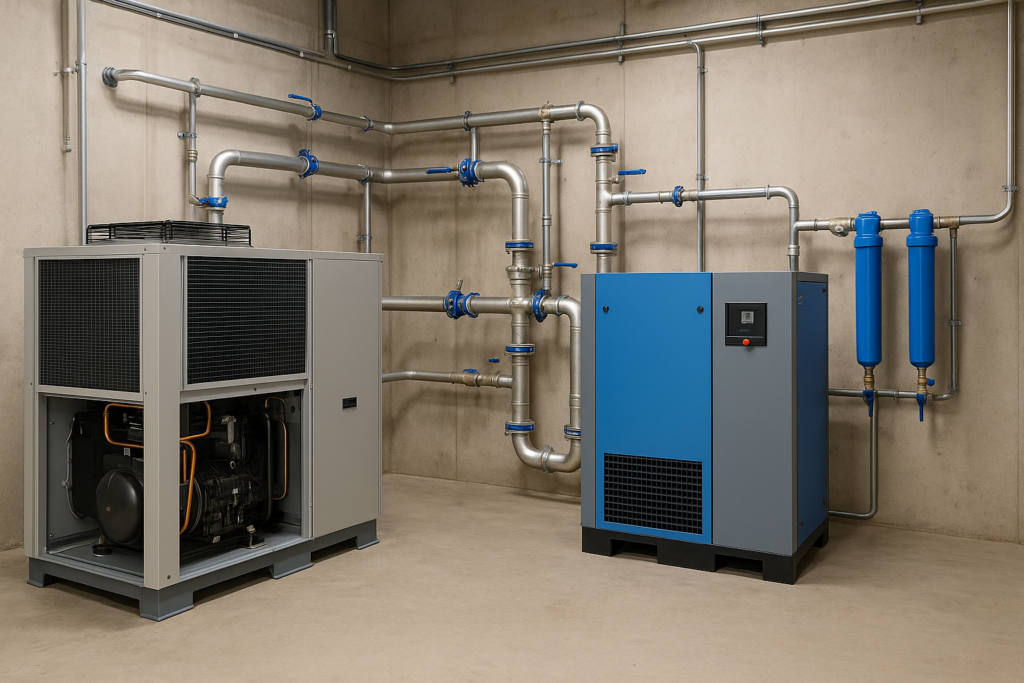
Le dimensionnement des utilités industrielles (air comprimé, eau glacée, vapeur, vide…) ne peut plus se limiter à un simple calcul de puissance. Aujourd’hui, il exige une approche globale et stratégique qui conjugue performance, fiabilité, efficacité énergétique et durabilité.
Dans un contexte industriel en pleine mutation – numérisation, volatilité des demandes, impératifs environnementaux – l’ingénieur doit viser juste. Ce n’est ni le plus gros équipement, ni le plus cher, qui garantit la performance, mais le système le mieux pensé, régulé, accessible et maintenable.
Dans cet article, nous détaillons les meilleures pratiques pour dimensionner intelligemment vos installations, en vous appuyant sur l’analyse de données, la modularité, l’efficacité énergétique et la simplicité opérationnelle.
I. Utiliser les données historiques de consommation : la base de toute ingénierie fiable
1. Pourquoi l’analyse de la demande réelle est indispensable
- Trop d’installations sont dimensionnées sur des hypothèses arbitraires ou sur des “pics théoriques” jamais atteints.
- Résultat : surdimensionnement coûteux, ou sous-calibrage risqué.
2. Exploiter les outils modernes
- IoT, capteurs intelligents, supervision SCADA ou GTC
- Enregistrement des débits, pressions, températures, hygrométrie, profils horaires
- Historique sur 6 à 12 mois recommandé
3. Analyse statistique des données
- Identifier les charges moyennes, maximales, les pics exceptionnels
- Déduire un profil de charge typique et ses variations saisonnières ou journalières
4. Cas pratique : air comprimé
- Enregistrement via débitmètre massique + enregistreur de pression
- Résultat : le compresseur ne fonctionnait à 100 % que 5 % du temps
- Réduction de 30 % de la puissance installée après re-calibrage
II. Prévoir une régulation à vitesse variable : l’arme ultime de l’agilité
1. Les limites du tout ou rien
- Équipements tout-ou-rien (on/off) = démarrages fréquents, consommation en pics, faible adaptabilité
- Usure accrue, bruit, pertes thermiques
2. Atouts du moteur à vitesse variable (VSD, VFD)
- Adapte la puissance en temps réel au besoin réel
- Réduction de la consommation électrique jusqu’à 35 %
- Allongement de la durée de vie des composants
3. Applications principales
- Compresseurs d’air : ajustement précis à la pression demandée
- Pompes de circulation d’eau glacée : contrôle du débit selon les besoins thermiques
- Ventilateurs : limitation du bruit et de la consommation en période basse
4. Astuce : combiner vitesse fixe + variable
- Base assurée par un équipement fixe
- Pointe absorbée par une machine VSD
III. Installer des by-pass et des redondances : fiabilité sans surdimensionner
1. Continuité de service = productivité assurée
- Un équipement à l’arrêt ne doit pas bloquer l’ensemble de la production
- Les by-pass permettent de contourner un équipement en panne ou en maintenance
2. Redondance intelligente
- Doubler les équipements critiques : 2×50 % ou 3×33 % plutôt que 1×100 %
- Permet de fonctionner à charge partielle, en rotation (allongement durée de vie)
3. Scénarios types
- Compresseur d’air principal + compresseur d’appoint prêt à prendre le relais
- Sécheur en stand-by enclenché automatiquement selon le point de rosée
4. Bénéfices
- Éviter les arrêts de ligne coûteux
- Réduire le stress sur les machines en service
- Maintenance facilitée sans interrompre la production
IV. Dimensionner les réseaux pour un débit optimal : ni trop, ni trop peu
1. L’enjeu du bon dimensionnement
- Trop faible : pertes de charge, surconsommation, surchauffe
- Trop grand : coût excessif, manque de balayage, condensation stagnante
2. Critères de conception
- Vitesse idéale de l’air : 6 à 8 m/s (réseau principal), 10-12 m/s (réseau secondaire)
- Vitesse de l’eau glacée : 0,8 à 1,5 m/s
3. Éviter les turbulences et le bruit
- Coudes optimisés, rayons larges
- Tubes anti-vibrations, fixations amorties
4. Prévoir des purges et des points hauts
- Évacuation de l’eau et des condensats facilitée
- Meilleure fiabilité dans le temps
V. Isoler thermiquement et acoustiquement les équipements
1. Pourquoi l’isolation est stratégique
- Réduire les pertes thermiques (surtout sur eau chaude ou eau glacée)
- Réduire les nuisances sonores, notamment en environnement semi-ouvert
2. Types d’isolation
- Calorifugeage des tuyauteries : gaines en mousse PE, coquilles en laine minérale
- Enceinte phonique pour compresseur ou pompe bruyante
3. Avantages
- Amélioration du rendement global du système
- Confort acoustique pour les opérateurs
- Diminution des pertes énergétiques indirectes
VI. Penser maintenance et accessibilité dès la conception
1. Le piège des locaux surchargés
- Trop souvent, les locaux techniques sont dimensionnés pour le matériel, sans prévoir les dégagements nécessaires à la maintenance
- Résultat : coûts indirects, risques d’accident, mauvaise gestion des pannes
2. Bonnes pratiques
- 1 m de dégagement minimum devant les armoires, filtres, organes d’accès
- Racks amovibles, rails pour échange standard
- Éclairage, ventilation et chemins de câble bien organisés
3. Anticiper les opérations de maintenance courante
- Changement de cartouche, nettoyage des condenseurs, resserrage des bornes
- Accès aux vannes, purges, instruments de mesure
VII. L’ingénierie au service de la sobriété et de la performance
1. Une science d’équilibre
- Trop petit : surcharge, pannes, pertes
- Trop gros : coût, inertie, instabilité
2. Le bon dimensionnement est une démarche structurée
- Analyse de la demande réelle
- Intégration des aléas climatiques
- Régulation dynamique
- Modularité et redondance
3. L’optimum = technique + économique + environnemental
- Moins de consommation d’énergie
- Moins d’entretien
- Moins de matière première et d’espace utilisé
4. Éviter les pièges classiques
- Économie court-termiste : mauvais retour sur investissement
- Surenchère sécuritaire : installation surdimensionnée, inefficace et coûteuse
5. Les clés du succès
- Travailler avec des outils de simulation (logiciels thermiques, hydrauliques, de charge)
- Impliquer les équipes de maintenance et d’exploitation dès l’avant-projet
- Planifier la maintenance préventive dans la phase de conception
Le dimensionnement d’une installation industrielle ne se résume pas à appliquer une formule. C’est une démarche d’ingénierie complète, qui fait appel à l’analyse, la modélisation, la projection, la régulation, l’ergonomie et la maintenance.
Chaque choix technique a un impact global : énergétique, économique, opérationnel. En intégrant les bonnes pratiques détaillées dans cet article, vous donnez à vos installations les meilleures chances de durer, de consommer moins, et de s’adapter au futur.
🎯 L’objectif final ? Concevoir des systèmes agiles, sobres, fiables… et intelligents.
En somme, l’ingénierie des fluides industriels est une discipline importante et diversifiée qui joue un rôle clé dans de nombreuses industries. Elle nécessite une expertise technique et une connaissance approfondie des systèmes de circulation des fluides, de la thermodynamique, de la mécanique des fluides, de la régulation et du contrôle des processus, ainsi que de la sécurité.
Notre blog est une ressource complète pour tout ce qui concerne les fluides industriels. Nous vous encourageons à explorer nos articles, nos guides pratiques et nos ressources de formation pour approfondir vos connaissances et améliorer vos performances énergétiques. N’hésitez pas à nous contacter pour bénéficier de nos services d’ingénierie personnalisés ou pour trouver les produits dont vous avez besoin via notre site de commerce en ligne. Ensemble, nous pouvons aller plus loin dans l’apprentissage et réaliser des économies d’énergie significatives. Contactez-nous dès aujourd’hui à l’adresse suivante :
Lien : Tuyauteries et Flexibles
Lien : Electricité et électricité industrielle
Lien: Robinetterie et tuyauterie
Lien : Échangeurs et transferts thermiques
Lien : Eau surchauffe (industrie et génie climatique)
Lien : Hydraulique et Graissage
Lien :Mesures Physique et appareils de mesures
Lien : Les sondes de mesure de température
Lien : outils de mesures (thermomètre, manomètres,…)
Lien : Matériaux en industrie (galva, acier, inox …)
Lien : Eau – filtration et traitement
Lien : Gazs réfrigérants (frigorifiques)
Lien : Filetages et taraudages
Lien : Unités de mesure et conversion
Lien: R.I.A. (Réseau Incendie Armé)
Lien : ATEX (Atmosphères Explosibles)
Lien : Agitation dans les Fluides Industriels
Lien : Le Chauffage Industriel : Un Processus Complexifié
Lien : L’Eau Glacée en Génie Climatique
Lien : Réaliser un Bilan Thermique en Génie Climatique
Lien : L’Isolation en Génie Climatique
Lien : Les Méthodes de Soudure et de Brasage : Comment Faire le Bon Choix »
Lien : Fixations Industrielles : La Clé de la Solidité et de la Sécurité
Lien : Les E.P.I. (Equipements de Protections Individuels)
0ien : Les E.P.C. (Equipements de Protection Collectifs)
Lien : Principaux de transfert thermique : la conduction, la convection et le rayonnement
Lien : Le Cercle Vertueux en Industrie : L’Écologie au Cœur des Fluides Industriels
Lien : Courroies Trapézoïdales en Industrie : L’Art de Transmettre la Puissance avec Précision
Lien : Optimisation de la Stabilité Industrielle : Lutte Efficace Contre les Vibrations des Machines
- La Gestion des Pièces Détachées en Industrie : Obsolescence, Durée de Vie et Stockage
- L’Impact de la Nature de la Surface et de la Couleur : Bilan Thermique et Transfert de Chaleur
- Comprendre les Classes de Protection IP : Un Guide Technique
- L’Art de l’Ingénierie en Mesures Physiques Industrielles : Optimisation, Contrôle et Dimentionnement des Fluides Industriels
- Innovation et Durabilité : L’Ingénierie des Fluides Industriels au Service de l’Économie Verte
- L’Énigme des Fluides Industriels : Explorons l’Inclassable
- Optimisation Énergétique dans l’Industrie : Réduire les Coûts liés aux Fluides Industriels
- Solutions Sur Mesure en Électrovannes pour Projets Spécifiques : Une Expertise Unique
- Vannes Motorisées: Standard ou Sur Mesure, Trouvez la Solution Adaptée pour Votre Application
- Guide Complet des Vannes Pneumatiques : Personnalisation, Qualité et Expertise
- Découvrez la Révolution Pneumatique : Les Vérins Sur Mesure
- Optimisation Pneumatique : Explorez Notre Gamme de Moteurs Pneumatiques
- Comment choisir le bon matériau pour vos équipements industriels : Une approche personnalisée
- Optimisation Cruciale: Les Répercussions d’un Réseau Industriel Mal Équilibré sur la Performance et la Sécurité
- Démystification des Moteurs Électriques: Un Guide Complet des Types, Avantages et Inconvénients
- Comprendre les éléments constitutifs des machines spéciales : Un guide technique pour les ingénieurs et techniciens de maintenance
- Impact Environnemental des Fluides Industriels et des Méthodes de Production
- L’évolution des systèmes de maintenance et la gestion des équipements industriels
- L’Évolution des Technologies dans les Systèmes Industriels : Air Comprimé, Groupes Froids et au-delà
- L’Importance de la Formation Continue pour les Techniciens des Fluides Industriels
- Tolérances de Côtes et Rugosité en Mécanique : Précision et Qualité en Ingénierie
- Méthodes Statistiques et Échantillonnage : L’Art d’Anticiper les Dérives Industrielles (SPC, …)
- Maîtriser l’Art du Filtrage Industriel : Comment Choisir, Lire et Entretenir les Filtres pour Optimiser Performance, Énergie et Durabilité
Lien pour achats :