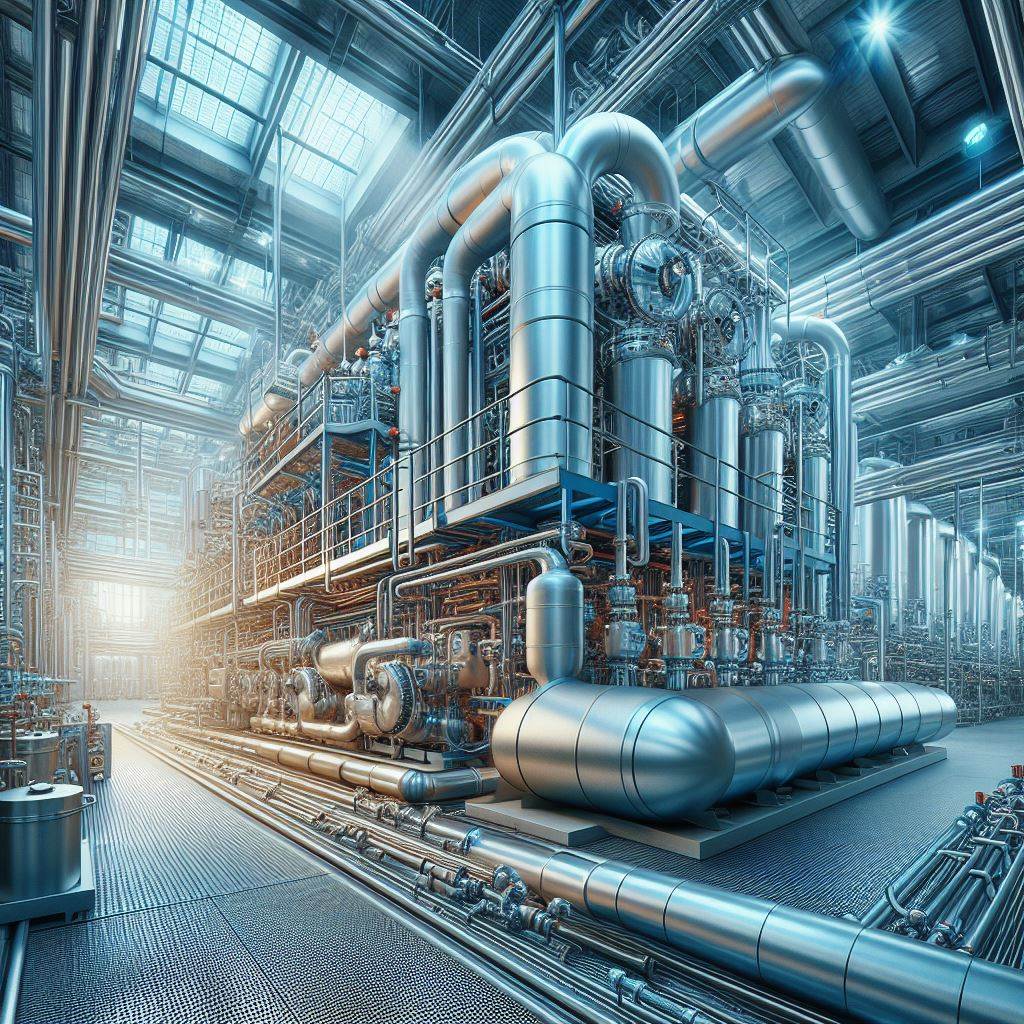
Les groupes froids industriels sont conçus pour fonctionner efficacement dans une plage de températures ambiantes spécifiques. Cependant, à des températures très élevées, comme pendant des périodes de canicule, les performances des groupes froids peuvent être compromises. Les caractéristiques des fluides frigorifiques utilisés déterminent ces limites de température. Par exemple, à des températures ambiantes très élevées, certains fluides peuvent être hors de leur plage de fonctionnement, entraînant la mise en sécurité du groupe froid.
1. Problèmes liés aux Températures Ambiantes Élevées
Effets sur les Fluides Frigorifiques :
- Dégradation des Performances : Les fluides frigorifiques peuvent perdre leur capacité de transfert de chaleur à des températures ambiantes élevées.
- Surchauffe : Les systèmes peuvent surchauffer, ce qui déclenche des mécanismes de sécurité pour éviter les dommages.
Mise en Sécurité :
- Les groupes froids disposent de capteurs et de contrôles pour surveiller les conditions de fonctionnement. Si les températures ambiantes dépassent les limites de sécurité, le système se met en sécurité pour prévenir les pannes ou les dommages.
2. Solutions pour Contourner les Limites de Température
Pour maintenir l’efficacité des groupes froids pendant des périodes de chaleur extrême, plusieurs solutions peuvent être mises en œuvre.
Refroidissement Surdimensionné du Condenseur :
- Condenseurs surdimensionnés : Utiliser des condenseurs de plus grande capacité pour améliorer le rejet de chaleur dans l’environnement, même à des températures ambiantes élevées.
- Augmentation de la Surface d’Échange : Plus de surface d’échange thermique permet une meilleure dissipation de la chaleur, aidant à maintenir les fluides frigorifiques dans leur plage de fonctionnement optimale.
Arrosage du Condenseur avec de l’Eau Fraîche :
- Refroidissement par Évaporation : L’arrosage du condenseur avec de l’eau fraîche peut aider à réduire la température du condenseur par évaporation de l’eau, augmentant ainsi l’efficacité du refroidissement.
- Précautions : Il est important de respecter les limites spécifiées par le constructeur pour éviter d’endommager le condenseur ou de créer des problèmes de corrosion et d’entartrage.
Exemple de Mise en Œuvre
Prenons un exemple où un groupe froid industriel est utilisé dans une région sujette à des vagues de chaleur, avec des températures pouvant atteindre 45°C.
Étapes :
- Évaluation des Besoins : Analyse des périodes de l’année où les températures ambiantes sont susceptibles de dépasser les limites de fonctionnement du fluide frigorifique.
- Dimensionnement du Condenseur : Installation d’un condenseur surdimensionné pour améliorer la capacité de rejet de chaleur.
- Système d’Arrosage : Mise en place d’un système d’arrosage du condenseur avec de l’eau fraîche, activé uniquement lorsque les températures ambiantes dépassent les seuils critiques.
- Contrôles et Sécurité : Implémentation de capteurs et de contrôles supplémentaires pour surveiller l’état du condenseur et prévenir tout risque de dommage dû à l’arrosage.
Bénéfices :
- Maintien des Performances : Le système de refroidissement reste efficace même pendant des périodes de chaleur extrême.
- Prévention des Pannes : Réduction des risques de mise en sécurité du groupe froid, assurant une continuité des opérations industrielles.
- Efficacité Énergétique : Optimisation de la consommation d’énergie grâce à un refroidissement plus efficace.
Les groupes froids industriels doivent fonctionner dans des plages de température définies par les caractéristiques des fluides frigorifiques. Pendant des périodes de canicule, les températures ambiantes élevées peuvent compromettre l’efficacité et la sécurité des systèmes de refroidissement. Utiliser des condenseurs surdimensionnés et mettre en place des systèmes d’arrosage avec de l’eau fraîche sont des solutions efficaces pour maintenir les performances des groupes froids en conditions extrêmes. Ces mesures permettent de prévenir les mises en sécurité des systèmes et d’assurer une régulation stable et efficace de la température, même pendant les vagues de chaleur.
En somme, l’ingénierie des fluides industriels est une discipline importante et diversifiée qui joue un rôle clé dans de nombreuses industries. Elle nécessite une expertise technique et une connaissance approfondie des systèmes de circulation des fluides, de la thermodynamique, de la mécanique des fluides, de la régulation et du contrôle des processus, ainsi que de la sécurité.
Notre blog est une ressource complète pour tout ce qui concerne les fluides industriels. Nous vous encourageons à explorer nos articles, nos guides pratiques et nos ressources de formation pour approfondir vos connaissances et améliorer vos performances énergétiques. N’hésitez pas à nous contacter pour bénéficier de nos services d’ingénierie personnalisés ou pour trouver les produits dont vous avez besoin via notre site de commerce en ligne. Ensemble, nous pouvons aller plus loin dans l’apprentissage et réaliser des économies d’énergie significatives. Contactez-nous dès aujourd’hui à l’adresse suivante :
Guide pour choisir un groupe froid industriel
- Installation optimale de groupes froids industriels : Pratiques essentielles et paramètres clés
- Guide : La mise en service initiale d’un groupe froid industriel
- Lien : Exemple de schémas d’installation
- Lien : Calcul de la puissance nécessaire et facteurs de corrections usuels
- Mesure de Débit d’Eau par Ultrasons : Optimisation des Process Industriels
Lien pour achats :