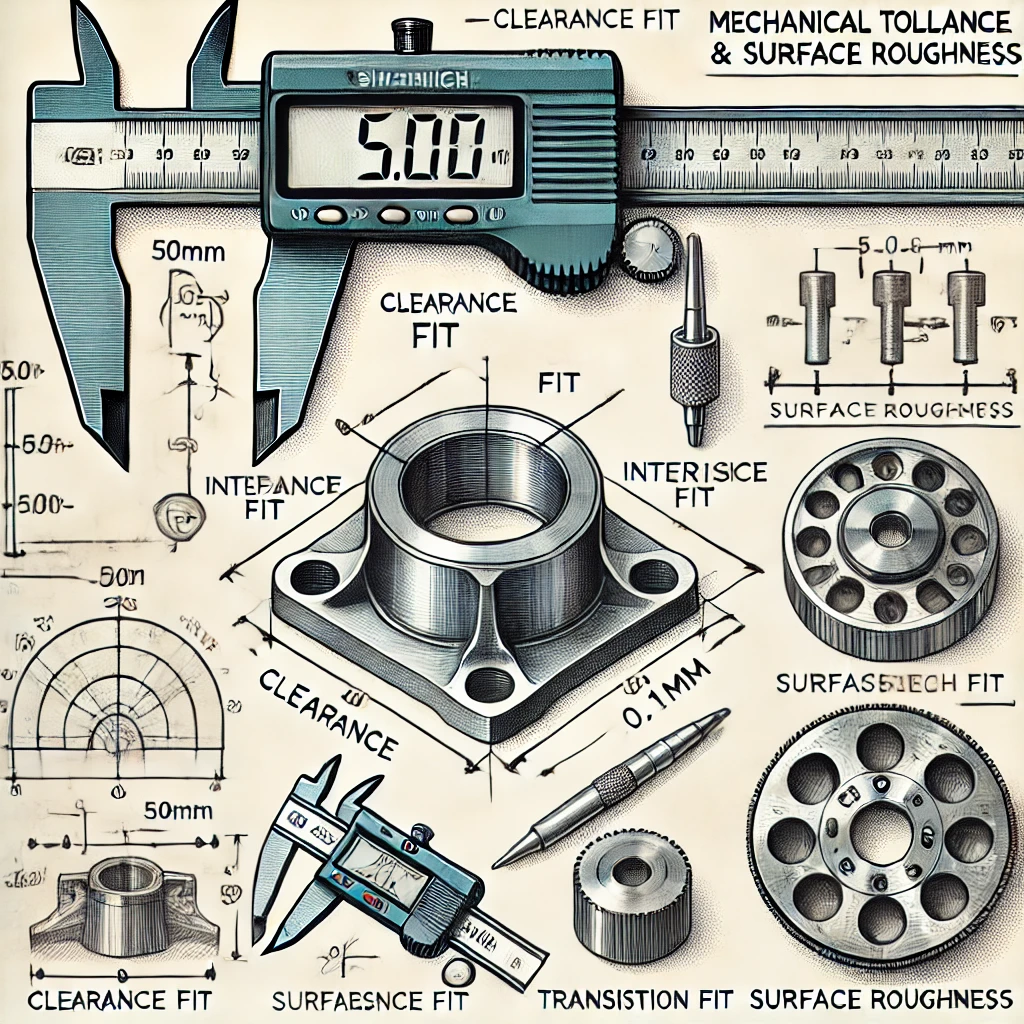
Les outils de coupe jouent un rôle essentiel dans l’usinage et la fabrication industrielle. Leur sélection et leur entretien influencent directement la précision des pièces usinées, la durée de vie des équipements et la rentabilité des opérations. Un bon choix de matériaux, de revêtements protecteurs et de stratégies d’affûtage peut améliorer considérablement les performances d’usinage. De plus, l’automatisation et la programmation adaptative des paramètres de coupe permettent d’optimiser la production tout en réduisant les coûts de maintenance.
Dans cet article, nous explorerons les critères de choix des outils de coupe, les techniques d’affûtage et les stratégies adaptatives permettant d’améliorer la productivité.
1. Matériaux des outils de coupe et revêtement protecteurs
a) Les principaux matériaux d’outils de coupe
Le choix du matériau influe sur la résistance à l’usure, la précision de coupe et la longévité de l’outil. Voici les matériaux les plus couramment utilisés :
- Acier rapide (HSS) : Bonne résistance à la chaleur et à l’usure, idéal pour des applications de coupe générale.
- Carbure de tungstène : Très dur et résistant aux températures élevées, utilisé pour des coupes rapides et précises.
- Céramiques : Résistantes à l’usure et aux hautes températures, idéales pour l’usinage des superalliages.
- Nitrure de bore cubique (CBN) : Excellente résistance à l’usure, utilisé pour l’usinage des aciers trempés.
- Diamant polycristallin (PCD) : Extrêmement dur et durable, parfait pour l’usinage des matériaux composites et non ferreux.
b) Revêtements protecteurs et leur impact sur la performance
Les revêtements permettent d’augmenter la durée de vie des outils et d’améliorer la qualité de coupe. Voici les plus courants :
- Nitrure de titane (TiN) : Augmente la résistance à l’usure et réduit le frottement.
- Carbonitrure de titane (TiCN) : Meilleure résistance à l’abrasion que le TiN, recommandé pour les aciers alliés.
- Aluminium-Titane-Nitrure (AlTiN) : Excellente résistance aux températures élevées, idéal pour les applications de coupe à grande vitesse.
- Revêtement diamant : Idéal pour l’usinage des matériaux très abrasifs comme les composites et l’aluminium chargé de silicium.
Astuce : L’utilisation d’un revêtement adapté permet d’augmenter la durée de vie des outils de 30 % à 300 % selon l’application.
2. Fréquence et techniques d’affûtage des outils de coupe
a) Signes indiquant un besoin d’affûtage
Un outil de coupe doit être affûter lorsqu’il présente les symptômes suivants :
- Augmentation des forces de coupe et vibration excessive.
- Diminution de la précision dimensionnelle des pièces usinées.
- Apparition de bavures ou échauffement excessif.
b) Techniques d’affûtage des outils
Différentes méthodes permettent d’affûter un outil :
- Affûtage manuel : Adapté pour les petits outils (forets, fraises, burins).
- Affûtage automatique : Utilisé dans les ateliers de production pour garantir une répétabilité optimale.
- Rectification CNC : Méthode précise pour les outils complexes (plaquettes carbure, fraises profilées).
Bon à savoir : Un affûtage régulier prolonge la durée de vie des outils de 50 % et réduit les coûts de remplacement.
3. Programmation adaptative des paramètres de coupe
a) Principe de la programmation adaptative
La programmation adaptative ajuste en temps réel les paramètres de coupe (vitesse, avance, profondeur) en fonction de l’usure de l’outil et des conditions de coupe.
b) Avantages de l’automatisation des paramètres
- Amélioration de la qualité : Meilleure précision dimensionnelle et réduction des écarts.
- Augmentation de la durée de vie des outils : Réduction des chocs thermiques et mécaniques.
- Optimisation des coûts de production : Réduction du gaspillage et amélioration de la productivité.
c) Intégration des capteurs et de l’IA pour un pilotage intelligent
- Capteurs de force et de vibrations : Surveillent l’usure de l’outil en temps réel.
- Systèmes de vision : Détectent les anomalies sur les arêtes de coupe.
- Intelligence artificielle : Prédit l’usure et optimise automatiquement les paramètres.
Astuce : L’utilisation de systèmes intelligents peut augmenter l’efficacité de production de 20 % à 40 %.
La sélection et l’entretien des outils de coupe sont essentiels pour garantir une production de qualité et optimiser les coûts. Le choix des matériaux et des revêtements, l’affûtage régulier et l’adoption de technologies avancées permettent d’améliorer la précision, la durée de vie des outils et la performance globale des processus d’usinage. L’intégration de capteurs et d’intelligence artificielle représente l’avenir de l’usinage adaptatif, rendant les ateliers de plus en plus autonomes et performants.
En optimisant chaque aspect du processus, les entreprises peuvent non seulement améliorer leur rentabilité, mais aussi réduire leur impact environnemental en limitant le gaspillage d’outils et de matières premières.
En intégrant ces notions à votre expertise technique, vous pourrez améliorer la précision, la qualité et la rentabilité de vos projets mécaniques.
Notre blog est une ressource complète pour tout ce qui concerne les fluides industriels. Nous vous encourageons à explorer nos articles, nos guides pratiques et nos ressources de formation pour approfondir vos connaissances et améliorer vos performances énergétiques. N’hésitez pas à nous contacter pour bénéficier de nos services d’ingénierie personnalisés ou pour trouver les produits dont vous avez besoin via notre site de commerce en ligne. Ensemble, nous pouvons aller plus loin dans l’apprentissage et réaliser des économies d’énergie significatives. Contactez-nous dès aujourd’hui à l’adresse suivante :
- Variation progressive des cotes, tolérances et rugosités en fabrication industrielle
- Tolérances en Mécanique : Comprendre les Différents Types et Leurs Applications
- Tolérances de Côtes et Rugosité en Mécanique : Maîtriser la Précision pour des Assemblages Fiables
- Tolérances de Côtes et Rugosité en Mécanique : Précision et Qualité en Ingénierie
- La Rugosité en Mécanique et en Mécanique de Précision : Guide Complet
- Tolérances en Mécanique et en Mécanique de Précision : Guide Complet
Lien pour achats :