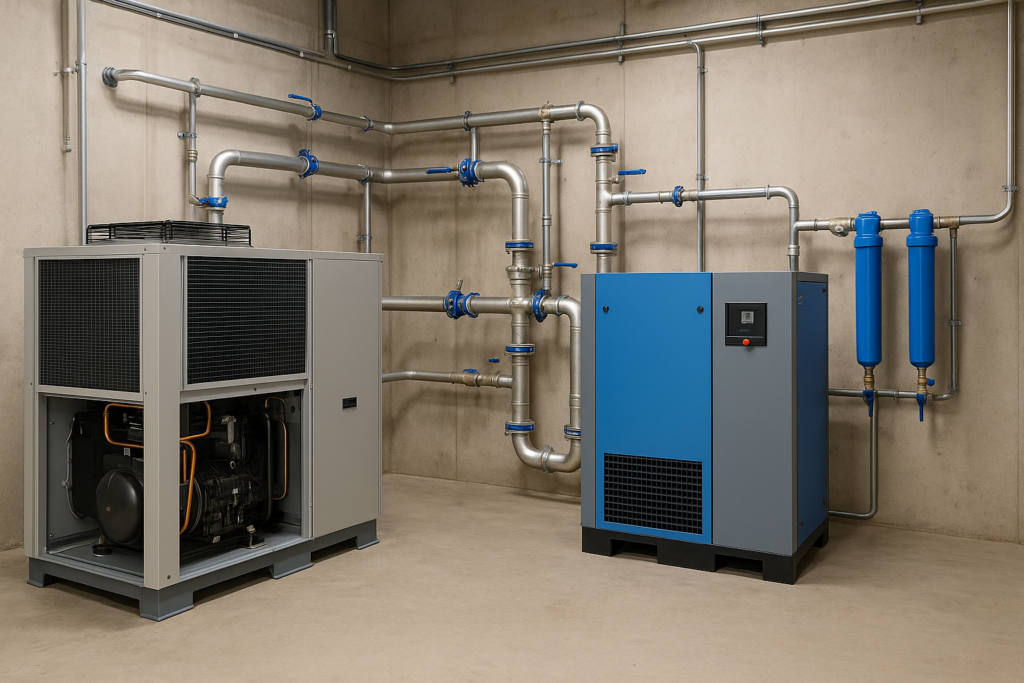
Optimiser le Dimensionnement d’un Groupe Froid : Fluide, Volume Utile et Accessibilité Technique
Dimensionner un groupe froid industriel ne se limite pas à calculer une puissance frigorifique. Pour garantir performance, fiabilité et facilité d’exploitation, il est essentiel de considérer des aspects souvent négligés :
- Nature du fluide frigorigène
- Différence entre volume utile et volume net de stockage
- Accessibilité et contraintes d’entretien
Cet article technique, pédagogique et optimisé SEO (environ 2000 mots) explore en profondeur ces trois dimensions, explique leur impact sur le rendement et la maintenance, puis propose des recommandations concrètes pour les intégrer dès la phase de conception.
1. 🧊 Nature du fluide frigorigène : un levier d’efficacité
1.1 Propriétés thermodynamiques variables
Les fluides couramment utilisés (R‑134a, R‑1234ze, R‑410A, R‑407C…) présentent des profils très différents en termes de :
- Point de pression de condensation et de vaporisation
- Chaleur latente, donc débit frigorifique pour un même volume
- Température & pression de fonctionnement
- Potentiel de réchauffement climatique (GWP)
1.2 Impact sur le COP et la puissance
- COP optimal selon le fluide : par exemple, le R‑1234ze offre un meilleur COP que l R‑134a à charge équivalente.
- La puissance d’un groupe froid donnée par le constructeur dépend du fluide : un même compresseur donnera plus ou moins de froid selon le fluide utilisé.
🎯 Lors du dimensionnement, commencez toujours par : copie de la courbe COP x Fluide x Charge x Delta‑T.
1.3 Contraintes réglementaires & environnementales
- Le R‑410A est de plus en plus limité dû à son GWP,
- Les fluides HFO (comme R‑1234ze) sont plus vertueux mais demandent des échangeurs adaptés,
- Vérifiez la compatibilité des joints, huile, bouclage avec le fluide choisi.
2. 📦 Volume utile vs volume utile effectif
2.1 Définitions
- Volume utile : capacité brute de la cuve (ex : 1000 L),
- Volume utile effectif : volume réellement disponible après déduction de la zone morte sous la pompe, du ballon, des circuits, etc.
2.2 Pourquoi est-ce essentiel ?
- Le ballon tampon doit lisser les charges, donc seule la capacité utile compte pour amortir les pics.
- Un volume mort de 20 % peut réduire drastiquement le tampon, entraînant des cycles thermiques précoces.
2.3 Comment le calculer
- Déterminer le volume total,
- Identifier la zone inaccessible ou destinée à la dilatation,
- Retirer les volumes liés à canalisations, siphons, colliers, etc.
➡️ Dimensionnement : prévoir 10–20 % de la charge horaire brute en volume utile effectif, pas brut.
3. 🔧 Accessibilité & entretien : penser à l’usage futur
3.1 Pourquoi anticiper l’usage humain ?
- Les gros groupes froids sont souvent replacés dans des locaux hors accès facile,
- L’entretien doit rester ergonomique, sécurisé, et nécessiter peu de démontages.
3.2 Cibles d’accessibilité à prévoir dès la conception
- Filtres déshydratants : accès direct, montage/démontage sans outil spécifique.
- Ventilateurs et échangeurs : accès facile pour nettoyage haute pression.
- Détendeurs & by‑pass : position pour intervention sans dépose d’enveloppes.
- Espace entre le groupe et la paroi : 1 m indispensable pour interventions sécurisées.
3.3 Retours d’expérience
- Surdimensionnement + cuve logée dans un local étriqué = interventions nécessitant permutation des groupes → trop peu de production.
- Filtres et ventilateurs inaccessibles → manque de nettoyage, performance chutée de 30 %.
4. ✅ Conseils d’ingénierie pour une conception rigoureuse
4.1 Sélection du fluide
Fluide | Avantage | Inconvénient |
---|---|---|
R‑134a | Usage classique | COP intermédiaire, GWP élevé |
R‑410A | Puissant | GWP important, limité réglementairement |
R‑1234ze | Bon COP, GWP bas | Nécessite conception dédiée |
Astuce : toujours croiser le fluide avec la courbe constructeur pour obtenir le COP réel attendu.
4.2 Dimensionnement spatial intelligent
- Vérifiez les zones techniques : tuyauterie, esprits de maintenance, tuyaux auxiliaires, etc.
- Appliquez les normes d’ergonomie, accessibilité, QHS.
- Prévoir un plan d’intervention avant la mise en service.
4.3 Vérification du volume net
- Faites un schéma 3D de la cuve et canalisations pour estimer les volumes morts.
- Intégrez les données à la régulation : point de déclenchement + délai tampon lié au volume utile.
5. 🧭 Processus final pour intégration
- Choisir le fluide selon performance, GWP, réglementation.
- Analyser COP en fonction de fluide + température de travail.
- Dimensionner tension, puissance, ballon selon volume utile net.
- Dessiner le layout et transmettre les contraintes d’accès et distances.
- Intégrer dans l’automate des zones de maintenance & interventions.
- Simuler la maintenance et organiser le plan d’action.
Le dimensionnement d’un groupe froid ne peut se limiter à calculer une puissance calorifique. Les choix techniques sur le fluide frigorigène, la précision du volume utile et la facilité d’accès pour l’entretien sont des facteurs déterminants dans la performance, la durabilité et la sécurité d’usage. En les intégrant de manière proactive dès la phase de conception, les ingénieurs garantissent des installations efficaces, fiables et rentables sur le long terme — tout en se prémunissant des pièges réglementaires et opérationnels.
En somme, l’ingénierie des fluides industriels est une discipline importante et diversifiée qui joue un rôle clé dans de nombreuses industries. Elle nécessite une expertise technique et une connaissance approfondie des systèmes de circulation des fluides, de la thermodynamique, de la mécanique des fluides, de la régulation et du contrôle des processus, ainsi que de la sécurité.
Notre blog est une ressource complète pour tout ce qui concerne les fluides industriels. Nous vous encourageons à explorer nos articles, nos guides pratiques et nos ressources de formation pour approfondir vos connaissances et améliorer vos performances énergétiques. N’hésitez pas à nous contacter pour bénéficier de nos services d’ingénierie personnalisés ou pour trouver les produits dont vous avez besoin via notre site de commerce en ligne. Ensemble, nous pouvons aller plus loin dans l’apprentissage et réaliser des économies d’énergie significatives. Contactez-nous dès aujourd’hui à l’adresse suivante :
Lien : Tuyauteries et Flexibles
Lien : Electricité et électricité industrielle
Lien: Robinetterie et tuyauterie
Lien : Échangeurs et transferts thermiques
Lien : Eau surchauffe (industrie et génie climatique)
Lien : Hydraulique et Graissage
Lien :Mesures Physique et appareils de mesures
Lien : Les sondes de mesure de température
Lien : outils de mesures (thermomètre, manomètres,…)
Lien : Matériaux en industrie (galva, acier, inox …)
Lien : Eau – filtration et traitement
Lien : Gazs réfrigérants (frigorifiques)
Lien : Filetages et taraudages
Lien : Unités de mesure et conversion
Lien: R.I.A. (Réseau Incendie Armé)
Lien : ATEX (Atmosphères Explosibles)
Lien : Agitation dans les Fluides Industriels
Lien : Le Chauffage Industriel : Un Processus Complexifié
Lien : L’Eau Glacée en Génie Climatique
Lien : Réaliser un Bilan Thermique en Génie Climatique
Lien : L’Isolation en Génie Climatique
Lien : Les Méthodes de Soudure et de Brasage : Comment Faire le Bon Choix »
Lien : Fixations Industrielles : La Clé de la Solidité et de la Sécurité
Lien : Les E.P.I. (Equipements de Protections Individuels)
0ien : Les E.P.C. (Equipements de Protection Collectifs)
Lien : Principaux de transfert thermique : la conduction, la convection et le rayonnement
Lien : Le Cercle Vertueux en Industrie : L’Écologie au Cœur des Fluides Industriels
Lien : Courroies Trapézoïdales en Industrie : L’Art de Transmettre la Puissance avec Précision
Lien : Optimisation de la Stabilité Industrielle : Lutte Efficace Contre les Vibrations des Machines
- La Gestion des Pièces Détachées en Industrie : Obsolescence, Durée de Vie et Stockage
- L’Impact de la Nature de la Surface et de la Couleur : Bilan Thermique et Transfert de Chaleur
- Comprendre les Classes de Protection IP : Un Guide Technique
- L’Art de l’Ingénierie en Mesures Physiques Industrielles : Optimisation, Contrôle et Dimentionnement des Fluides Industriels
- Innovation et Durabilité : L’Ingénierie des Fluides Industriels au Service de l’Économie Verte
- L’Énigme des Fluides Industriels : Explorons l’Inclassable
- Optimisation Énergétique dans l’Industrie : Réduire les Coûts liés aux Fluides Industriels
- Solutions Sur Mesure en Électrovannes pour Projets Spécifiques : Une Expertise Unique
- Vannes Motorisées: Standard ou Sur Mesure, Trouvez la Solution Adaptée pour Votre Application
- Guide Complet des Vannes Pneumatiques : Personnalisation, Qualité et Expertise
- Découvrez la Révolution Pneumatique : Les Vérins Sur Mesure
- Optimisation Pneumatique : Explorez Notre Gamme de Moteurs Pneumatiques
- Comment choisir le bon matériau pour vos équipements industriels : Une approche personnalisée
- Optimisation Cruciale: Les Répercussions d’un Réseau Industriel Mal Équilibré sur la Performance et la Sécurité
- Démystification des Moteurs Électriques: Un Guide Complet des Types, Avantages et Inconvénients
- Comprendre les éléments constitutifs des machines spéciales : Un guide technique pour les ingénieurs et techniciens de maintenance
- Impact Environnemental des Fluides Industriels et des Méthodes de Production
- L’évolution des systèmes de maintenance et la gestion des équipements industriels
- L’Évolution des Technologies dans les Systèmes Industriels : Air Comprimé, Groupes Froids et au-delà
- L’Importance de la Formation Continue pour les Techniciens des Fluides Industriels
- Tolérances de Côtes et Rugosité en Mécanique : Précision et Qualité en Ingénierie
- Méthodes Statistiques et Échantillonnage : L’Art d’Anticiper les Dérives Industrielles (SPC, …)
- Maîtriser l’Art du Filtrage Industriel : Comment Choisir, Lire et Entretenir les Filtres pour Optimiser Performance, Énergie et Durabilité
Lien pour achats :