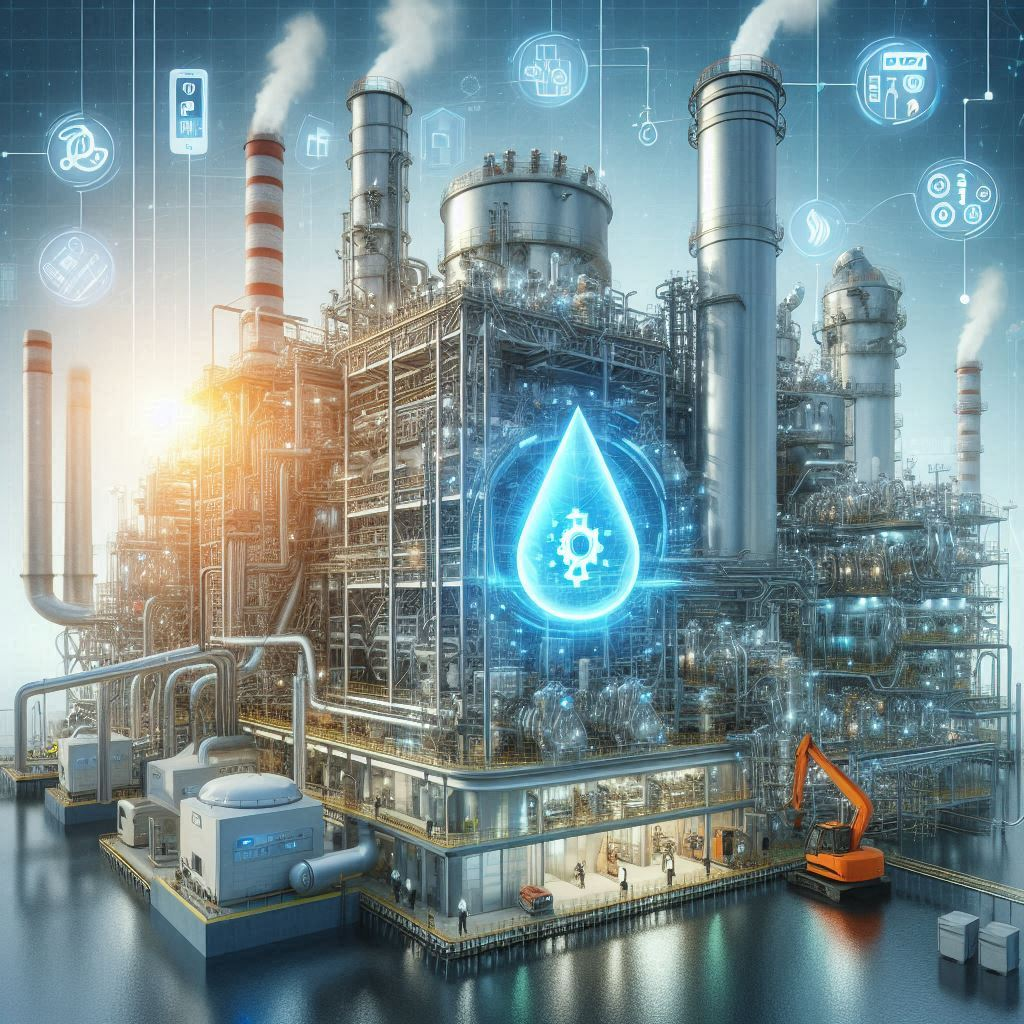
Les solutions basées sur l’IoT (Internet des Objets) et l’IA (Intelligence Artificielle) transforment le secteur du froid industriel en apportant des avantages significatifs en termes de précision, de capacité d’adaptation, et de gestion de grandes quantités de données. Voici les principales façons dont ces technologies révolutionnent ce domaine :
1. Précision et Efficacité
- Contrôle Temporel Avancé : Les capteurs IoT mesurent en continu des paramètres critiques tels que la température, l’humidité, et la pression dans les systèmes de refroidissement. Cette surveillance constante permet de maintenir des conditions optimales pour la conservation des produits sensibles, comme dans l’industrie alimentaire ou pharmaceutique.
- Régulation Automatisée : L’IA exploite les données collectées pour ajuster automatiquement les cycles de refroidissement, minimisant ainsi les écarts de température. Cela garantit une meilleure stabilité thermique, prévenant toute dégradation de la qualité des produits ou des substances traitées.
- Prédiction des Besoins : Grâce aux algorithmes de machine learning, l’IA peut anticiper les variations de charge thermique en analysant les schémas d’utilisation historiques. Cela permet de préparer les équipements à fonctionner à un niveau optimal tout en évitant le gaspillage d’énergie.
2. Adaptation Rapide aux Changements
- Réactivité Dynamique : Les systèmes de refroidissement équipés de l’IoT et de l’IA peuvent réagir instantanément aux variations des conditions extérieures ou des demandes de production. Par exemple, une augmentation soudaine de la température ambiante entraîne une régulation automatique de l’intensité de refroidissement pour maintenir les conditions requises.
- Flexibilité Opérationnelle : Ces technologies permettent d’adapter le fonctionnement des installations de manière fluide, garantissant un niveau de performance constant même en cas de fluctuations imprévues. Cela est particulièrement important dans les environnements de production où les conditions évoluent rapidement.
- Maintenance Prédictive : L’IA identifie les signes avant-coureurs d’une défaillance potentielle en analysant les anomalies détectées par les capteurs. Cela permet de programmer des interventions de maintenance avant qu’une panne ne survienne, limitant les interruptions et augmentant la durée de vie des équipements.
3. Gestion de Grands Volumes de Données
- Analyse et Optimisation : Les capteurs IoT génèrent une énorme quantité de données en temps réel. L’IA les traite pour identifier des tendances, proposer des optimisations énergétiques, et prévoir des scénarios. Cela permet aux gestionnaires de faire des choix éclairés basés sur des analyses précises.
- Visualisation Centralisée : Les plateformes de gestion utilisent les données collectées pour offrir une vue d’ensemble de l’état des systèmes de refroidissement, facilitant la prise de décision et la supervision des opérations à grande échelle.
- Optimisation Énergétique : En combinant les données des capteurs et les modèles prédictifs de l’IA, les entreprises peuvent ajuster la consommation d’énergie en temps réel, réalisant des économies significatives tout en limitant leur impact environnemental.
L’utilisation des technologies IoT et IA dans le froid industriel apporte une précision sans précédent, une capacité d’adaptation rapide aux changements, et une gestion efficace de grandes quantités de données. Ces innovations augmentent la fiabilité des systèmes, optimisent l’efficacité énergétique, et contribuent à des coûts opérationnels réduits, tout en garantissant la qualité et la sécurité des processus industriels.
Notre blog est une ressource complète pour tout ce qui concerne les fluides industriels. Nous vous encourageons à explorer nos articles, nos guides pratiques et nos ressources de formation pour approfondir vos connaissances et améliorer vos performances énergétiques. N’hésitez pas à nous contacter pour bénéficier de nos services d’ingénierie personnalisés ou pour trouver les produits dont vous avez besoin via notre site de commerce en ligne. Ensemble, nous pouvons aller plus loin dans l’apprentissage et réaliser des économies d’énergie significatives. Contactez-nous dès aujourd’hui à l’adresse suivante :
- Guide pour choisir un groupe froid industriel
- Le Guide Ultime du Choix des Compresseurs Frigorifiques : Optimisation, Puissance et Régulation
- Installation optimale de groupes froids industriels : Pratiques essentielles et paramètres clés
- Guide : La mise en service initiale d’un groupe froid industriel
- Les Applications du Refroidissement Industriel dans Divers Secteurs
- Guide Pratique pour le Choix d’un Groupe Froid Industriel : Calculs, Installations, Méthodes, Besoins et Critères Essentiels
- Optimiser l’Efficacité Énergétique : Deux Méthodes Ingénieuses pour Récupérer la Chaleur d’un Groupe Froid Industriel
- Guide Pratique : Récupération de Chaleur sur Groupe Froid – Avantages et Mise en Œuvre
- Innovations et Stratégies Avancées dans le Refroidissement Industriel: Vers une Ère Durable et Efficace
- Optimisation Cruciale: Les Répercussions d’un Réseau Industriel Mal Équilibré sur la Performance et la Sécurité
- Optimisation du Dimensionnement des Tuyauteries : Préserver la Pression et Réduire les Pertes de Charge
- Calculs et dimensionnement, installation, optimisation et Maintenance des Groupes Froids Industriels : Guide Complet pour Calcul de Puissance, Facteurs de Correction, et Technologies de Contrôle
- La conception d’un système de refroidissement industriel (Industrial Cooling System)
- FAQ : Groupes Froids Industriels et au Refroidissement Process
- Questions / réponses fréquemment posées sur le thème du refroidissement de process, incluant l’eau glacée, le froid industriel, les groupes froids, et les groupes d’eau glacée
- Quelles sont les erreurs courantes à éviter lors du choix d’un groupe froid industriel pour le refroidissement de son process ?
- Refroidissement Industriel : L’Essentiel sur les Groupes Frigorifiques et les Groupes d’Eau Glacée
- FAQ : Groupes Froids Industriels et au Refroidissement Process
- Groupe Froid Industriel et Durabilité : Vers une Utilisation Plus Écologique et Économe en Énergie
- Comment Choisir le Meilleur Fabricant de Groupes Froids, la technologie, les options … : Guide Complet
Lien pour achats :