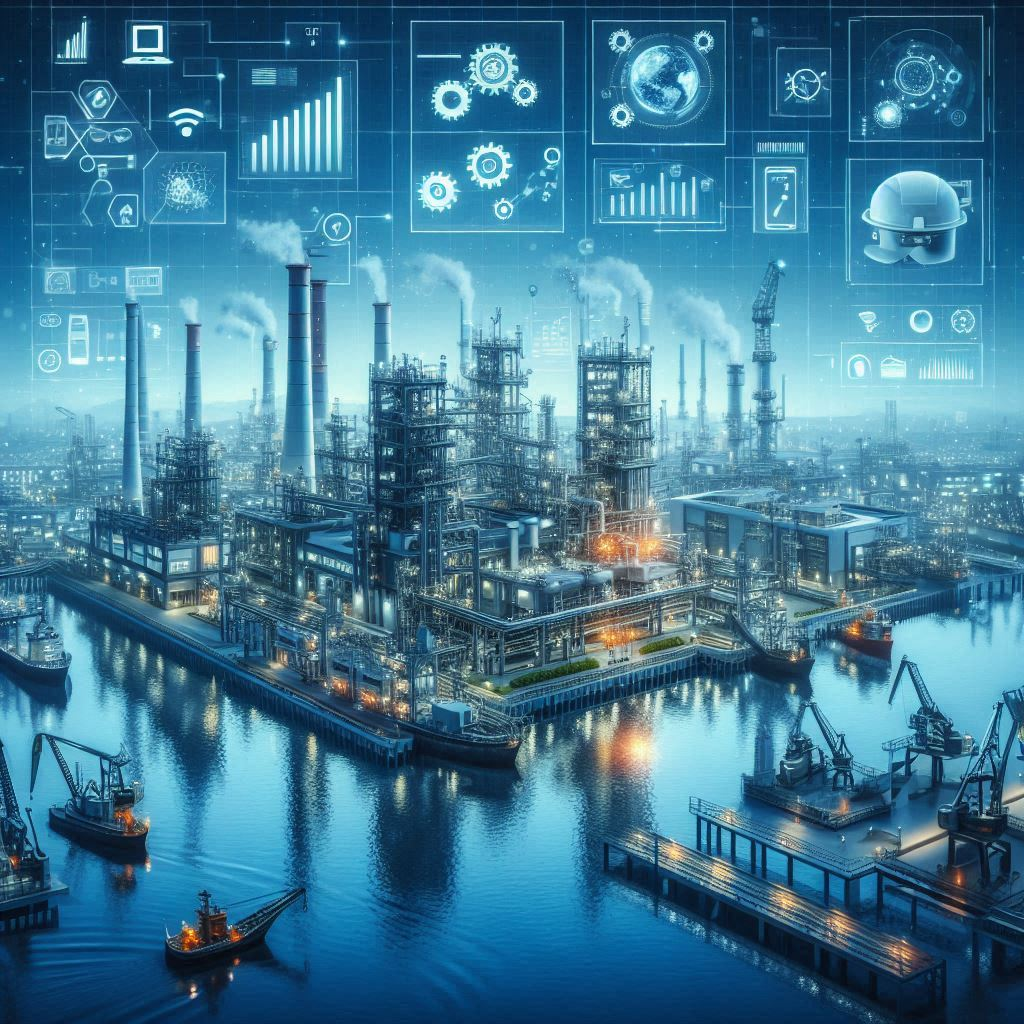
L’industrie du refroidissement process connaît une transformation majeure grâce à l’intégration de l’intelligence artificielle (IA) et du machine learning (ML). Ces technologies permettent de passer d’une approche de maintenance réactive ou préventive à une maintenance prédictive, révolutionnant ainsi la manière dont les groupes froids et les unités d’eau glacée sont gérés. Grâce à l’utilisation des données en temps réel provenant des capteurs IoT, l’IA est capable d’anticiper les pannes, d’optimiser les interventions de maintenance et de prolonger la durée de vie des équipements. Voici comment cela fonctionne.
1. Machine Learning pour Anticiper les Pannes
Le machine learning est au cœur de la maintenance prédictive. Il s’agit d’une branche de l’IA qui permet aux systèmes d’apprendre à partir des données historiques et en temps réel pour identifier des schémas indicatifs de problèmes futurs.
1.1. Collecte des Données des Capteurs
Les groupes froids et les unités d’eau glacée sont équipés de divers capteurs IoT qui mesurent des paramètres clés comme :
- Température : Température de l’eau glacée en entrée et sortie, température du compresseur, température d’évaporation.
- Pression : Pression d’aspiration et de refoulement du compresseur.
- Débit : Débit d’eau glacée, débit de réfrigérant.
- Vibrations : Vibration du compresseur et des ventilateurs, indicatives de déséquilibres ou d’usure mécanique.
- Humidité : Mesures d’humidité dans l’air pour les systèmes de refroidissement par air.
Ces données sont transmises en temps réel à une plateforme d’analyse pilotée par des algorithmes de machine learning.
1.2. Analyse des Données Historiques et en Temps Réel
Les modèles de machine learning utilisent les données historiques d’exploitation et les données en temps réel pour créer des prédictions sur l’état des équipements. Les techniques couramment utilisées incluent :
- Régression linéaire et logistique : Pour prédire les défaillances sur la base des tendances observées dans les données de température et de pression.
- Forêts aléatoires (Random Forest) et algorithmes de gradient boosting : Pour identifier des relations complexes entre différentes variables et améliorer la précision des prédictions.
- Réseaux neuronaux récurrents (RNN) et long short-term memory (LSTM) : Pour analyser les séries temporelles et détecter les changements progressifs dans les données, prédisant ainsi des pannes potentielles.
2. Modèles Prédictifs pour Évaluer la Durée de Vie des Composants
Le machine learning permet de développer des modèles prédictifs capables d’estimer la durée de vie restante des composants critiques, tels que les compresseurs, les échangeurs de chaleur et les pompes.
2.1. Modèles de Régression
Les modèles de régression analysent l’usure des composants en fonction de divers paramètres d’exploitation comme la température et la pression. Par exemple, une augmentation progressive de la température de refoulement du compresseur pourrait indiquer une baisse d’efficacité, liée à une usure des segments de piston ou à un encrassement de l’échangeur de chaleur.
- Exemple pratique :
- Un modèle de régression évalue la durée de vie restante du compresseur en fonction de l’évolution des vibrations et de la température de refoulement, suggérant une intervention avant qu’un problème ne se transforme en panne coûteuse.
2.2. Analyse de Fiabilité (RUL – Remaining Useful Life)
Les algorithmes de machine learning peuvent prédire la durée de vie restante (RUL) des composants en combinant des données historiques avec des données en temps réel. Cela permet aux équipes de maintenance de planifier les interventions avant que les pannes ne surviennent.
- Application :
- Utilisation d’un modèle RUL pour prédire la durée de vie restante d’un ventilateur dans une unité de refroidissement d’eau glacée, en fonction des tendances de vibration et des fluctuations de température.
Bon à savoir :
- Les modèles RUL peuvent réduire les temps d’arrêt imprévus jusqu’à 50 % et augmenter la durée de vie des équipements de 20 %.
3. Optimisation des Interventions de Maintenance
L’IA ne se contente pas de prédire les pannes ; elle aide également à optimiser le calendrier des interventions de maintenance, en proposant des recommandations basées sur l’analyse des données.
3.1. Priorisation des Interventions
Les systèmes basés sur l’IA peuvent évaluer le niveau de criticité des anomalies détectées et classer les interventions en fonction de leur impact potentiel sur la production. Par exemple, une anomalie dans le compresseur principal pourrait être priorisée par rapport à une baisse de performance d’un ventilateur secondaire.
- Exemple :
- Un modèle d’IA identifie une baisse de rendement du compresseur principal et alerte l’équipe de maintenance pour une inspection immédiate, réduisant ainsi le risque de panne prolongée.
3.2. Planification Dynamique de la Maintenance
L’IA peut ajuster dynamiquement le planning de maintenance en fonction des prévisions d’utilisation et des conditions de fonctionnement. Par exemple, si une période de forte demande de refroidissement est prévue, l’IA peut planifier une maintenance préventive avant cette période pour éviter des interruptions inattendues.
Astuce :
- L’intégration de l’IA dans la planification de la maintenance peut améliorer l’efficacité des interventions de 30 %, en optimisant l’utilisation des ressources humaines et matérielles.
4. Étude de Cas : Maintenance Prédictive d’une Usine de Production Alimentaire
Dans une usine de production alimentaire, un système de refroidissement process est équipé de capteurs IoT mesurant des paramètres critiques comme la température, la pression et les vibrations. Les données collectées sont analysées par un algorithme de machine learning, permettant d’anticiper les défaillances des compresseurs et des pompes de circulation.
4.1. Problème Rencontré
L’usine subissait des pannes récurrentes de compresseurs, entraînant des interruptions de la production et des pertes de produits périssables.
4.2. Solution Implémentée
Un modèle de machine learning a été déployé pour surveiller les données des capteurs et prédire les pannes potentielles. En utilisant les données de température et de vibration, l’algorithme a pu anticiper une augmentation de l’usure des segments de piston du compresseur.
4.3. Résultats Obtenus
- Réduction des pannes imprévues de 60 %.
- Diminution des coûts de maintenance de 25 % grâce à une planification proactive.
- Augmentation de la disponibilité des équipements de 15 %, améliorant ainsi la capacité de production.
L’application de l’IA et du machine learning dans la maintenance prédictive des groupes froids et des unités d’eau glacée représente une avancée majeure pour les industries cherchant à optimiser leurs processus et réduire les coûts d’exploitation. En anticipant les pannes et en optimisant les interventions, ces technologies permettent d’assurer une performance continue et fiable des systèmes de refroidissement, tout en minimisant les impacts environnementaux.
Les entreprises adoptant ces solutions peuvent non seulement améliorer leur efficacité opérationnelle, mais également prolonger la durée de vie de leurs équipements, tout en répondant aux exigences croissantes en matière de durabilité et de réduction de l’empreinte carbone. L’IA, en tant que catalyseur de l’industrie 4.0, s’affirme ainsi comme un outil incontournable pour la maintenance prédictive et l’optimisation des systèmes de refroidissement industriels.
Le refroidissement process et les groupes froids industriels sont essentiels pour garantir le bon fonctionnement des systèmes de production. Les innovations technologiques, notamment les systèmes de refroidissement avancés et les stratégies d’optimisation énergétique, permettent de relever les défis actuels de performance et de durabilité. En choisissant des solutions adaptées aux besoins spécifiques de chaque application, les industries peuvent améliorer leur efficacité, réduire leurs coûts opérationnels et minimiser leur impact environnemental, contribuant ainsi à une production plus verte et plus durable.
Notre blog est une ressource complète pour tout ce qui concerne les fluides industriels. Nous vous encourageons à explorer nos articles, nos guides pratiques et nos ressources de formation pour approfondir vos connaissances et améliorer vos performances énergétiques. N’hésitez pas à nous contacter pour bénéficier de nos services d’ingénierie personnalisés ou pour trouver les produits dont vous avez besoin via notre site de commerce en ligne. Ensemble, nous pouvons aller plus loin dans l’apprentissage et réaliser des économies d’énergie significatives. Contactez-nous dès aujourd’hui à l’adresse suivante :
- Guide pour choisir un groupe froid industriel
- Le Guide Ultime du Choix des Compresseurs Frigorifiques : Optimisation, Puissance et Régulation
- Installation optimale de groupes froids industriels : Pratiques essentielles et paramètres clés
- Guide : La mise en service initiale d’un groupe froid industriel
- Les Applications du Refroidissement Industriel dans Divers Secteurs
- Guide Pratique pour le Choix d’un Groupe Froid Industriel : Calculs, Installations, Méthodes, Besoins et Critères Essentiels
- Optimiser l’Efficacité Énergétique : Deux Méthodes Ingénieuses pour Récupérer la Chaleur d’un Groupe Froid Industriel
- Guide Pratique : Récupération de Chaleur sur Groupe Froid – Avantages et Mise en Œuvre
- Innovations et Stratégies Avancées dans le Refroidissement Industriel: Vers une Ère Durable et Efficace
- Optimisation Cruciale: Les Répercussions d’un Réseau Industriel Mal Équilibré sur la Performance et la Sécurité
- Optimisation du Dimensionnement des Tuyauteries : Préserver la Pression et Réduire les Pertes de Charge
- Calculs et dimensionnement, installation, optimisation et Maintenance des Groupes Froids Industriels : Guide Complet pour Calcul de Puissance, Facteurs de Correction, et Technologies de Contrôle
- La conception d’un système de refroidissement industriel (Industrial Cooling System)
- FAQ : Groupes Froids Industriels et au Refroidissement Process
- Questions / réponses fréquemment posées sur le thème du refroidissement de process, incluant l’eau glacée, le froid industriel, les groupes froids, et les groupes d’eau glacée
- Quelles sont les erreurs courantes à éviter lors du choix d’un groupe froid industriel pour le refroidissement de son process ?
- Refroidissement Industriel : L’Essentiel sur les Groupes Frigorifiques et les Groupes d’Eau Glacée
- FAQ : Groupes Froids Industriels et au Refroidissement Process
- Groupe Froid Industriel et Durabilité : Vers une Utilisation Plus Écologique et Économe en Énergie
- Comment Choisir le Meilleur Fabricant de Groupes Froids, la technologie, les options … : Guide Complet
Lien pour achats :