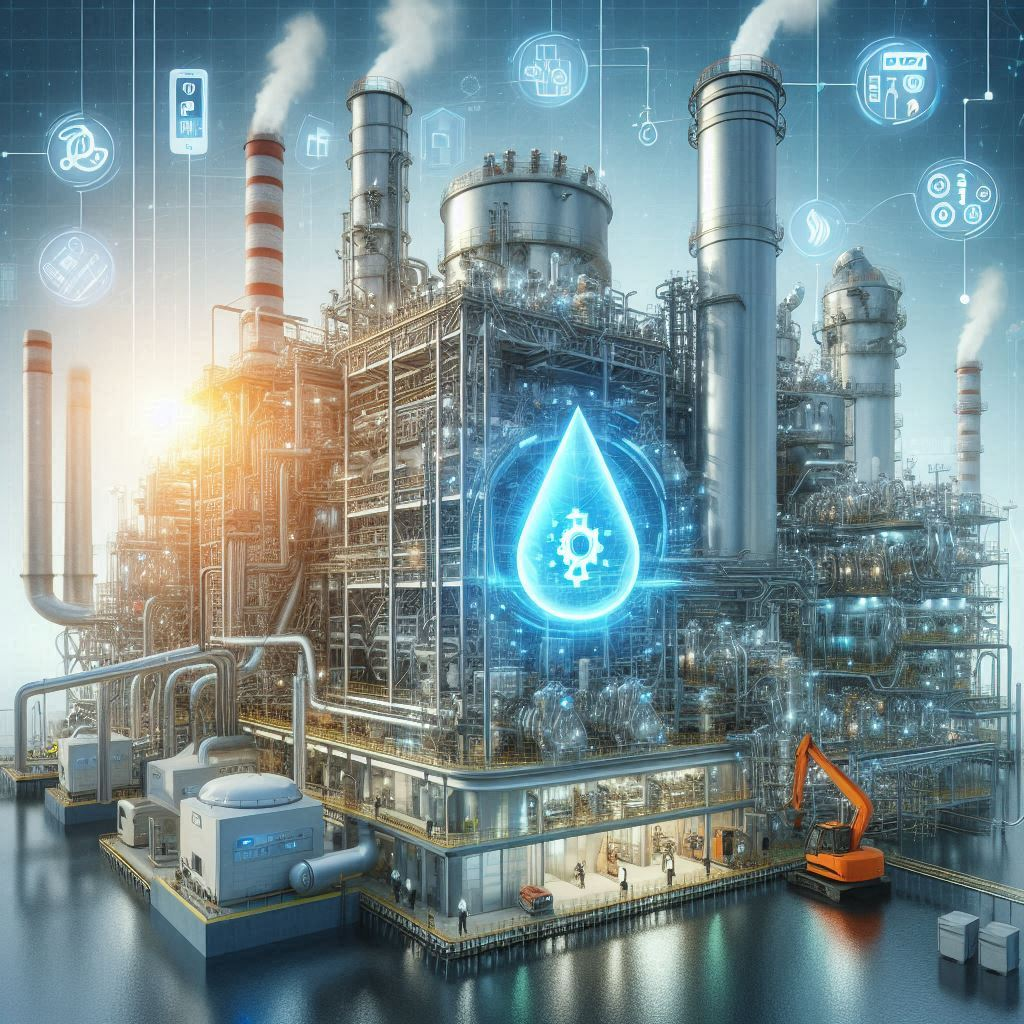
L’intégration des technologies IoT (Internet des Objets) et de l’Intelligence Artificielle (IA) dans le secteur du froid industriel représente une véritable révolution, apportant des bénéfices considérables tant au niveau de l’efficacité que de la durabilité. Voici les principaux avantages de ces innovations pour les systèmes de refroidissement industriel :
1. Optimisation de l’Efficacité Énergétique
- Surveillance Précise des Consommations : Les capteurs IoT collectent des données en temps réel sur les consommations d’énergie des systèmes de refroidissement. Cela permet d’identifier les points de perte et d’optimiser les réglages pour améliorer l’efficacité énergétique.
- Régulation Automatique : L’IA peut ajuster automatiquement les paramètres (température, pression, débit) en fonction des besoins de refroidissement, réduisant ainsi la consommation d’énergie. Par exemple, l’algorithme d’IA ajuste l’intensité du refroidissement en fonction des variations de la température ambiante et des charges thermiques.
2. Réduction des Coûts d’Opération
- Maintenance Prédictive : L’IA analyse les données collectées par les capteurs IoT pour prédire les pannes avant qu’elles ne surviennent. Cela permet d’intervenir de manière proactive, évitant les réparations coûteuses et minimisant les temps d’arrêt. Les coûts de maintenance sont ainsi réduits, et la durée de vie des équipements est prolongée.
- Optimisation de l’Utilisation des Ressources : En ajustant les opérations en temps réel, les entreprises peuvent minimiser le gaspillage des ressources, comme l’énergie ou les fluides de refroidissement, ce qui se traduit par des économies financières substantielles.
3. Amélioration de la Qualité des Produits et de la Sécurité
- Contrôle Précis des Conditions : Dans des secteurs critiques comme l’agroalimentaire ou la pharmaceutique, les variations de température peuvent compromettre la qualité des produits. Les technologies IoT assurent un suivi continu de la température, de l’humidité, et d’autres paramètres essentiels, garantissant ainsi des conditions optimales.
- Réaction Immédiate aux Anomalies : Grâce aux systèmes d’alerte automatique, toute déviation par rapport aux seuils définis est détectée instantanément. L’IA peut également proposer des solutions pour corriger ces anomalies, réduisant les risques de perte de qualité ou d’accidents.
4. Gestion Intelligente des Données
- Analyse de Données en Temps Réel : L’IoT collecte d’immenses quantités de données provenant de divers capteurs. L’IA les traite pour fournir des insights exploitables, comme l’identification des moments où les équipements sont les plus sollicités ou la détection des tendances de consommation énergétique.
- Tableaux de Bord Intuitifs : Les entreprises peuvent suivre l’état de leurs systèmes via des interfaces utilisateur simplifiées, facilitant la prise de décision. Ces tableaux de bord permettent de visualiser en un coup d’œil les performances des systèmes et de faire des ajustements rapidement.
5. Durabilité et Réduction de l’Impact Environnemental
- Gestion Efficace de l’Énergie : L’optimisation de la consommation d’énergie a un impact direct sur la réduction de l’empreinte carbone. En diminuant le gaspillage, les entreprises participent activement à la protection de l’environnement, tout en respectant les normes environnementales de plus en plus strictes.
- Recours aux Énergies Renouvelables : Les systèmes intelligents peuvent être programmés pour tirer parti des énergies renouvelables (comme l’énergie solaire ou éolienne) lorsque celles-ci sont disponibles, contribuant ainsi à une gestion énergétique plus durable.
6. Flexibilité et Scalabilité
- Adaptabilité aux Changements : Les solutions IoT et IA sont facilement modifiables en fonction des évolutions des besoins industriels. Qu’il s’agisse de l’ajout de nouveaux capteurs ou de l’amélioration des algorithmes, les systèmes peuvent évoluer avec l’entreprise.
- Scalabilité des Solutions : Ces technologies permettent aux entreprises de commencer avec des installations de petite échelle et de les faire évoluer progressivement. Cela réduit l’investissement initial tout en offrant des perspectives de croissance.
7. Amélioration de la Sécurité des Installations
- Prévention des Risques : Les capteurs IoT détectent des conditions dangereuses, telles que des variations de pression anormales ou des fuites de fluides frigorigènes. L’IA peut non seulement signaler ces risques, mais aussi déclencher des mesures de sécurité automatiques, comme l’arrêt des machines.
- Surveillance à Distance : Les équipes peuvent surveiller l’état des systèmes depuis n’importe quel endroit, réduisant ainsi le besoin de présence physique constante sur site. Cela améliore la sécurité des techniciens et la rapidité des interventions.
8. Prise de Décision Éclairée
- Rapports et Insights Précis : Les données analysées par l’IA fournissent des recommandations basées sur des modèles de performance, permettant aux managers de prendre des décisions stratégiques. Par exemple, savoir quand il est préférable de remplacer des équipements ou comment mieux planifier les ressources.
- Prévisions Précises : Les algorithmes de machine learning prédisent les besoins futurs en refroidissement en tenant compte des données historiques et des variables externes, comme les prévisions météorologiques. Cela permet de planifier et d’optimiser les opérations à l’avance.
Les technologies IoT et IA transforment le froid industriel en apportant des avantages indéniables en matière d’efficacité énergétique, de réduction des coûts, de qualité des produits, et de sécurité des installations. Elles permettent une surveillance continue, une maintenance proactive, et une gestion intelligente des ressources, offrant ainsi aux entreprises un avantage compétitif dans un contexte de plus en plus exigeant en matière d’innovation et de durabilité. Ces avancées technologiques sont essentielles pour répondre aux défis environnementaux actuels tout en maintenant une productivité optimale.
Notre blog est une ressource complète pour tout ce qui concerne les fluides industriels. Nous vous encourageons à explorer nos articles, nos guides pratiques et nos ressources de formation pour approfondir vos connaissances et améliorer vos performances énergétiques. N’hésitez pas à nous contacter pour bénéficier de nos services d’ingénierie personnalisés ou pour trouver les produits dont vous avez besoin via notre site de commerce en ligne. Ensemble, nous pouvons aller plus loin dans l’apprentissage et réaliser des économies d’énergie significatives. Contactez-nous dès aujourd’hui à l’adresse suivante :
- Guide pour choisir un groupe froid industriel
- Le Guide Ultime du Choix des Compresseurs Frigorifiques : Optimisation, Puissance et Régulation
- Installation optimale de groupes froids industriels : Pratiques essentielles et paramètres clés
- Guide : La mise en service initiale d’un groupe froid industriel
- Les Applications du Refroidissement Industriel dans Divers Secteurs
- Guide Pratique pour le Choix d’un Groupe Froid Industriel : Calculs, Installations, Méthodes, Besoins et Critères Essentiels
- Optimiser l’Efficacité Énergétique : Deux Méthodes Ingénieuses pour Récupérer la Chaleur d’un Groupe Froid Industriel
- Guide Pratique : Récupération de Chaleur sur Groupe Froid – Avantages et Mise en Œuvre
- Innovations et Stratégies Avancées dans le Refroidissement Industriel: Vers une Ère Durable et Efficace
- Optimisation Cruciale: Les Répercussions d’un Réseau Industriel Mal Équilibré sur la Performance et la Sécurité
- Optimisation du Dimensionnement des Tuyauteries : Préserver la Pression et Réduire les Pertes de Charge
- Calculs et dimensionnement, installation, optimisation et Maintenance des Groupes Froids Industriels : Guide Complet pour Calcul de Puissance, Facteurs de Correction, et Technologies de Contrôle
- La conception d’un système de refroidissement industriel (Industrial Cooling System)
- FAQ : Groupes Froids Industriels et au Refroidissement Process
- Questions / réponses fréquemment posées sur le thème du refroidissement de process, incluant l’eau glacée, le froid industriel, les groupes froids, et les groupes d’eau glacée
- Quelles sont les erreurs courantes à éviter lors du choix d’un groupe froid industriel pour le refroidissement de son process ?
- Refroidissement Industriel : L’Essentiel sur les Groupes Frigorifiques et les Groupes d’Eau Glacée
- FAQ : Groupes Froids Industriels et au Refroidissement Process
- Groupe Froid Industriel et Durabilité : Vers une Utilisation Plus Écologique et Économe en Énergie
- Comment Choisir le Meilleur Fabricant de Groupes Froids, la technologie, les options … : Guide Complet
Lien pour achats :