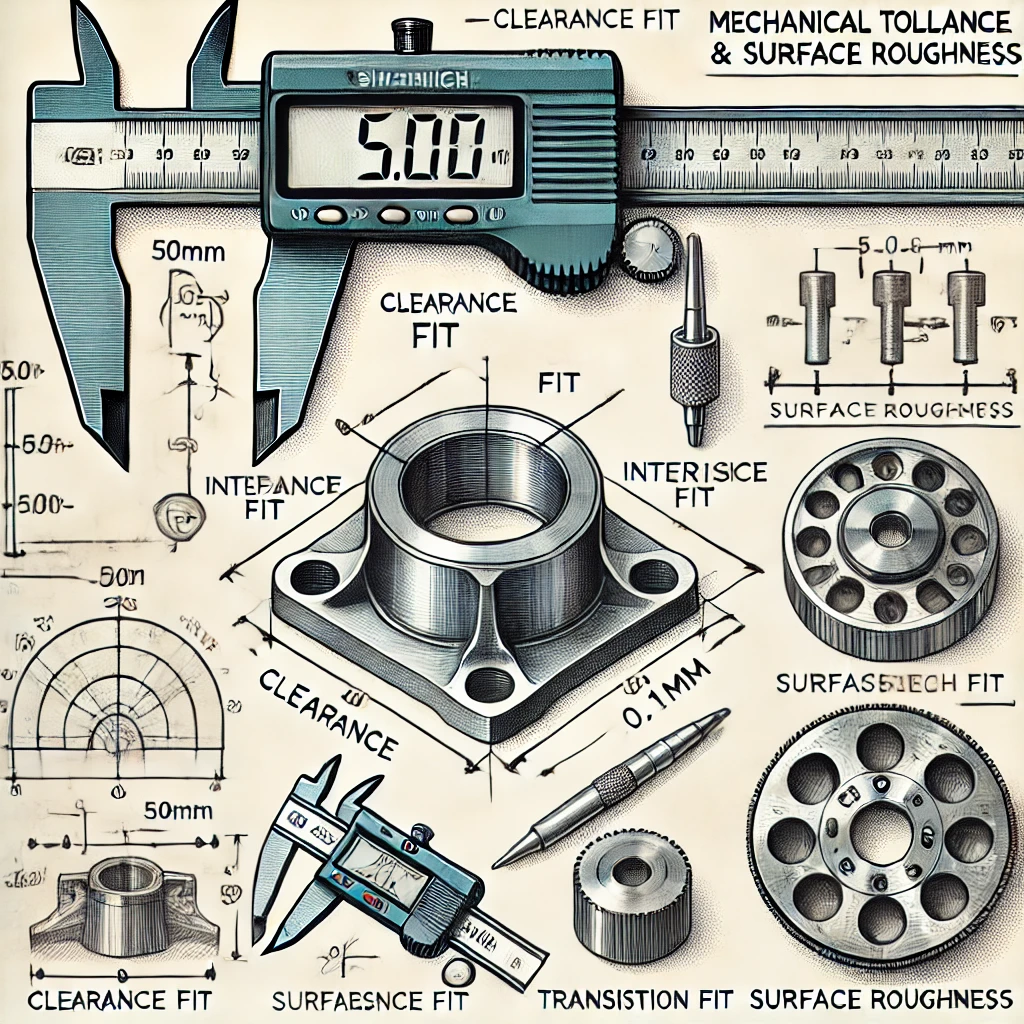
Dans l’industrie manufacturière, la précision dimensionnelle est un enjeu majeur pour garantir la qualité des pièces produites. Une dérive des cotes ou de la rugosité peut entraîner des non-conformités et des surcoûts importants. L’analyse des écarts permet d’identifier les dérives à temps et d’effectuer des corrections de réglages avant que la production ne soit affectée. Cet article explore les méthodes d’analyse des écarts, les outils de surveillance, et les stratégies de correction des réglages.
1. Comprendre l’Analyse des Écarts
1.1. Qu’est-ce qu’un écart en usinage ?
Un écart est une différence mesurable entre la cote nominale attendue et la réalité observée sur une pièce usinée. Il peut concerner plusieurs paramètres :
- Dimensions (longueur, diamètre, épaisseur…)
- Tolérances (jeux et ajustements)
- Rugosité (finitions de surface)
- Déformations (flexion, torsion)
Ces écarts peuvent être progressifs ou apparaître brutalement suite à une usure ou un dérèglement machine.
1.2. Pourquoi les écarts apparaissent-ils ?
Plusieurs causes peuvent provoquer des dérives dimensionnelles :
- Usure des outils : les arêtes tranchantes s’arrondissent, modifiant la force de coupe.
- Dilatation thermique : à cause des échauffements, les matériaux se dilatent et modifient les dimensions.
- Dérèglement des machines : désalignement progressif, jeux excessifs.
- Conditions ambiantes : variations de température et d’humidité qui affectent les matériaux et les machines.
2. Outils et Méthodes pour Détecter les Écarts
2.1. Utilisation de la métrologie
L’utilisation d’instruments de mesure permet d’identifier précocement les dérives :
- Micromètres et comparateurs pour mesurer les cotes.
- Rugosimètres pour contrôler l’état de surface.
- Machines à mesurer tridimensionnelles (MMT) pour un contrôle avancé.
2.2. Contrôle Statistique des Processus (SPC)
Le SPC est une méthode d’analyse qui permet d’anticiper les dérives en surveillant des tendances sur des échantillons réguliers. Il repose sur des outils comme :
- Les cartes de contrôle (Shewhart, X-bar R, X-bar S)
- Les indices de capabilités (Cp, Cpk)
- L’analyse de dérives par histogramme et boîte à moustaches
2.3. Surveillance par capteurs IoT
L’intégration de capteurs intelligents permet une détection en temps réel des dérives :
- Capteurs de vibrations pour identifier l’usure des outils.
- Capteurs de température pour surveiller l’échauffement.
- Systèmes de vision industrielle pour analyser la rugosité et les défauts.
3. Correction des Réglages Machine
3.1. Ajustement des paramètres de coupe
Si une dérive est identifiée, plusieurs ajustements peuvent être effectués :
- Augmenter ou réduire la vitesse de coupe.
- Modifier l’avance pour contrôler la rugosité.
- Changer le fluide de coupe pour limiter l’échauffement.
3.2. Maintenance Préventive et Prédictive
Une maintenance régulière prévient les dérives machine :
- Remplacement des outils avant qu’ils ne soient trop usés.
- Alignement périodique des axes.
- Contrôle de la tension des éléments de serrage.
3.3. Compensation automatique des dérives
Certaines machines modernes intègrent des systèmes de compensation automatique qui ajustent les paramètres en fonction des variations observées :
- Correction en boucle fermée basée sur la mesure des pièces.
- Algorithmes d’IA pour prévoir et compenser les dérives.
4. Bonnes Pratiques pour Réduire les Écarts
4.1. Former les opérateurs
Une formation approfondie permet aux techniciens de mieux comprendre et anticiper les problèmes.
4.2. Stabiliser l’environnement de production
- Maintenir une température et une humidité constantes.
- Limiter les vibrations parasites.
4.3. Utiliser des matériaux et outils de qualité
- Choisir des outils résistants à l’usure.
- Préférer des matières stables thermiquement.
L’analyse des écarts et la correction des réglages sont essentielles pour garantir une production stable et conforme aux exigences qualitatives. Grâce à une surveillance rigoureuse et des ajustements précis, il est possible de limiter les dérives et d’optimiser la précision des pièces usinées. L’utilisation combinée de la métrologie, du SPC et des technologies IoT permet d’améliorer la réactivité face aux dérèglements et de prévenir les non-conformités avant qu’elles n’impactent la production.
En intégrant ces notions à votre expertise technique, vous pourrez améliorer la précision, la qualité et la rentabilité de vos projets mécaniques.
Notre blog est une ressource complète pour tout ce qui concerne les fluides industriels. Nous vous encourageons à explorer nos articles, nos guides pratiques et nos ressources de formation pour approfondir vos connaissances et améliorer vos performances énergétiques. N’hésitez pas à nous contacter pour bénéficier de nos services d’ingénierie personnalisés ou pour trouver les produits dont vous avez besoin via notre site de commerce en ligne. Ensemble, nous pouvons aller plus loin dans l’apprentissage et réaliser des économies d’énergie significatives. Contactez-nous dès aujourd’hui à l’adresse suivante :
- Variation progressive des cotes, tolérances et rugosités en fabrication industrielle
- Tolérances en Mécanique : Comprendre les Différents Types et Leurs Applications
- Tolérances de Côtes et Rugosité en Mécanique : Maîtriser la Précision pour des Assemblages Fiables
- Tolérances de Côtes et Rugosité en Mécanique : Précision et Qualité en Ingénierie
- La Rugosité en Mécanique et en Mécanique de Précision : Guide Complet
- Tolérances en Mécanique et en Mécanique de Précision : Guide Complet
Lien pour achats :