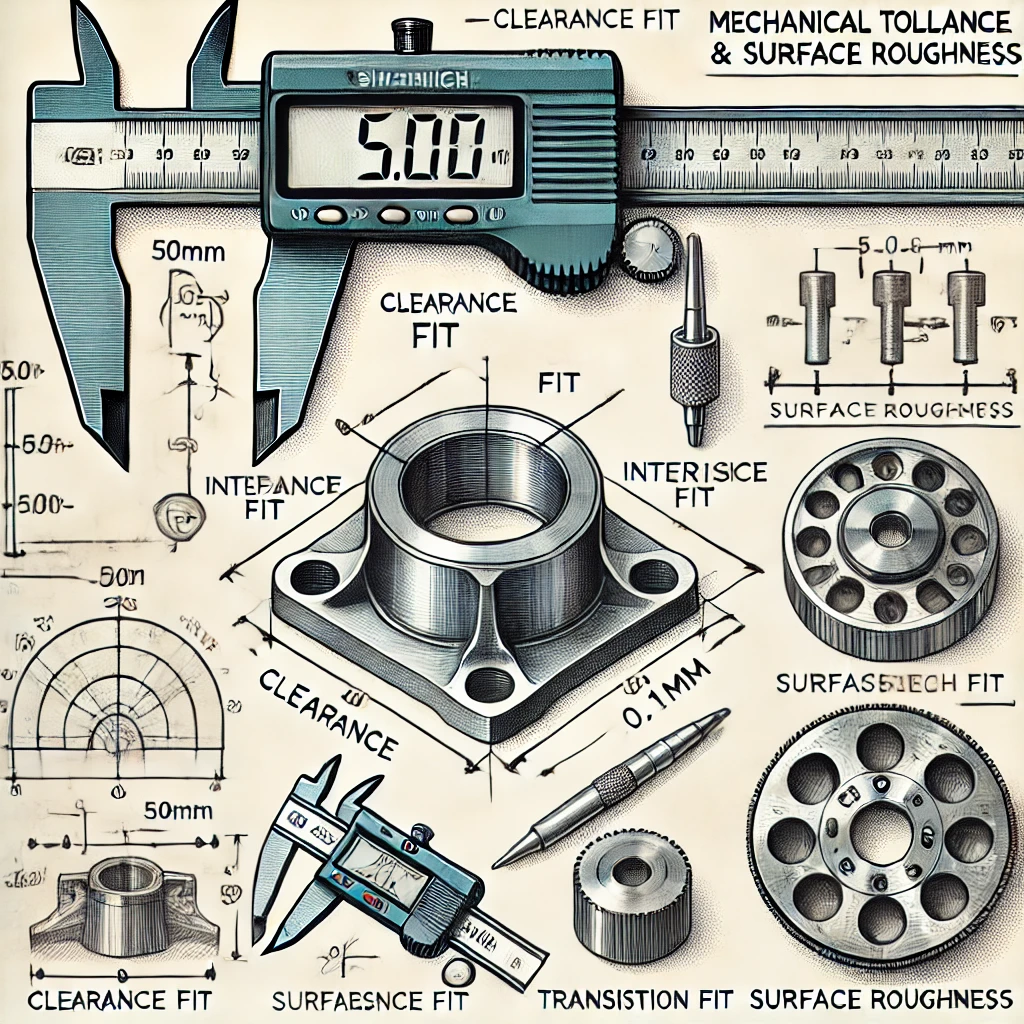
Dans l’industrie manufacturière, la stabilité dimensionnelle des pièces usinées repose sur de nombreux facteurs. Parmi eux, les conditions ambiantes jouent un rôle crucial mais souvent sous-estimé. L’humidité, la température et les vibrations ambiantes peuvent directement impacter la précision des machines-outils et provoquer des dérives de cotes. Une mauvaise maîtrise de ces paramètres peut engendrer des non-conformités, des pertes financières et des problèmes d’assemblage. Cet article explore en détail l’impact des conditions ambiantes sur les variations dimensionnelles et propose des solutions pour y remédier.
1. Influence de la Température Ambiante
La température a un effet direct sur la dilatation des matériaux, qu’il s’agisse de la pièce usinée, des outils de coupe ou même des structures des machines-outils.
1.1. Dilatation Thermique des Matériaux
Les métaux et autres matériaux utilisés en fabrication subissent une expansion thermique lorsqu’ils sont exposés à des températures élevées. Le coefficient de dilatation thermique (α) varie selon les matériaux et doit être pris en compte pour garantir des tolérances précises.
Exemple :
- L’acier possède un coefficient de dilatation d’environ 12 µm/m/°C. Une variation de température de 10°C peut ainsi entraîner une augmentation de 120 µm sur une pièce d’un mètre !
- L’aluminium, plus sensible, a un coefficient de 23 µm/m/°C, ce qui double l’effet par rapport à l’acier.
1.2. Effets sur les Machines et les Outils
- Les bancs de machines subissent également des variations dimensionnelles, affectant la précision de l’usinage.
- Une température non maîtrisée peut engendrer une dilatation des broches, modifiant le positionnement et les jeux des outils.
- Des variations thermiques peuvent générer des erreurs de positionnement pouvant aller jusqu’à plusieurs microns, impactant la répétabilité du processus.
Bon à savoir :
- Maintenir un atelier à température constante (idéalement autour de 20°C) minimise les effets thermiques.
- L’utilisation de fluide de coupe réfrigérant permet de réduire l’échauffement de la pièce et des outils.
- Des systèmes de compensation thermique intégrés aux machines modernes permettent de corriger en temps réel les variations dimensionnelles.
2. Impact de l’Humidité sur les Matériaux et les Machines
L’humidité de l’air influence directement les caractéristiques des matériaux et le comportement des équipements.
2.1. Corrosion et Oxydation
Une humidité excessive favorise la corrosion des pièces métalliques, altérant leur précision dimensionnelle.
Conséquences :
- Altération des dimensions due à l’oxydation progressive.
- Modification de l’état de surface, ce qui peut affecter la rugosité et l’ajustement des pièces.
- Perte de performance des guidages linéaires et des broches en raison de l’accumulation de rouille.
2.2. Gonflement des Matériaux
Certains matériaux, comme les composites ou les plastiques, absorbent l’humidité et se dilatent, entraînant des déformations incontrôlées.
Solutions :
- Maintenir un taux d’humidité stable entre 40% et 60% dans l’atelier.
- Stocker les matériaux sensibles dans des zones climatisées.
- Appliquer des revêtements protecteurs sur les pièces métalliques exposées à l’humidité.
3. Effets des Vibrations et des Variations de Charge
Les vibrations ambiantes et les variations de charge mécanique ont un impact direct sur la qualité d’usinage et la stabilité dimensionnelle des pièces.
3.1. Origine des Vibrations
Les vibrations peuvent être causées par :
- Le fonctionnement d’autres machines à proximité.
- Un mauvais équilibrage des outils de coupe ou des pièces usinées.
- Des oscillations dans les systèmes de transmission et les broches.
- Des fondations insuffisamment rigides sous les machines.
3.2. Conséquences sur la Qualité des Pièces
- Une usure accélérée des outils.
- Des micro-déplacements de la pièce en cours d’usinage, provoquant des écarts dimensionnels imprévus.
- Une augmentation de la rugosité des surfaces usinées.
- Des erreurs dans les alignements et les perçages.
Bon à savoir :
- L’installation d’amortisseurs de vibrations sous les machines réduit significativement ces effets.
- Les systèmes d’équilibrage dynamique permettent d’ajuster automatiquement les outils en rotation pour minimiser les déséquilibres.
- La mesure des vibrations en temps réel via des capteurs IoT permet d’anticiper les dérives et d’intervenir avant qu’un défaut ne se produise.
4. Stratégies pour Maîtriser les Effets des Conditions Ambiantes
4.1. Régulation Climatique de l’Atelier
- Installer un système de climatisation industrielle pour maintenir une température constante.
- Mettre en place des capteurs de température et d’humidité pour surveiller l’environnement de travail en temps réel.
- Assurer un flux d’air homogène pour éviter les variations locales de température.
4.2. Surveillance et Contrôle des Vibrations
- Vérifier régulièrement les fondations et supports des machines.
- Utiliser des matériaux amortissants pour minimiser les vibrations parasites.
- Mettre en place des contrôles périodiques de l’équilibrage des outils et des broches.
4.3. Métrologie et Compensation des Écarts
- Effectuer des mesures régulières des cotes des pièces pour détecter les dérives dimensionnelles.
- Utiliser des logiciels de compensation thermique intégrés aux commandes numériques.
- Planifier un entretien préventif pour limiter les effets de l’usure sur la précision des machines.
Les conditions ambiantes influencent directement la précision dimensionnelle en usinage. La température, l’humidité et les vibrations peuvent provoquer des variations non négligeables sur les cotes des pièces fabriquées. Une gestion rigoureuse de ces paramètres est indispensable pour garantir une production stable et conforme aux exigences de qualité.
Grâce aux avancées technologiques, notamment avec l’intégration des capteurs intelligents et des systèmes de supervision, il est aujourd’hui possible d’anticiper et de compenser ces effets avant qu’ils ne compromettent la qualité des productions. En mettant en place des stratégies adaptées, les industriels peuvent ainsi optimiser leurs procédés et réduire significativement le taux de rebuts et de retouches.
En intégrant ces notions à votre expertise technique, vous pourrez améliorer la précision, la qualité et la rentabilité de vos projets mécaniques.
Notre blog est une ressource complète pour tout ce qui concerne les fluides industriels. Nous vous encourageons à explorer nos articles, nos guides pratiques et nos ressources de formation pour approfondir vos connaissances et améliorer vos performances énergétiques. N’hésitez pas à nous contacter pour bénéficier de nos services d’ingénierie personnalisés ou pour trouver les produits dont vous avez besoin via notre site de commerce en ligne. Ensemble, nous pouvons aller plus loin dans l’apprentissage et réaliser des économies d’énergie significatives. Contactez-nous dès aujourd’hui à l’adresse suivante :
- Variation progressive des cotes, tolérances et rugosités en fabrication industrielle
- Tolérances en Mécanique : Comprendre les Différents Types et Leurs Applications
- Tolérances de Côtes et Rugosité en Mécanique : Maîtriser la Précision pour des Assemblages Fiables
- Tolérances de Côtes et Rugosité en Mécanique : Précision et Qualité en Ingénierie
- La Rugosité en Mécanique et en Mécanique de Précision : Guide Complet
- Tolérances en Mécanique et en Mécanique de Précision : Guide Complet
Lien pour achats :