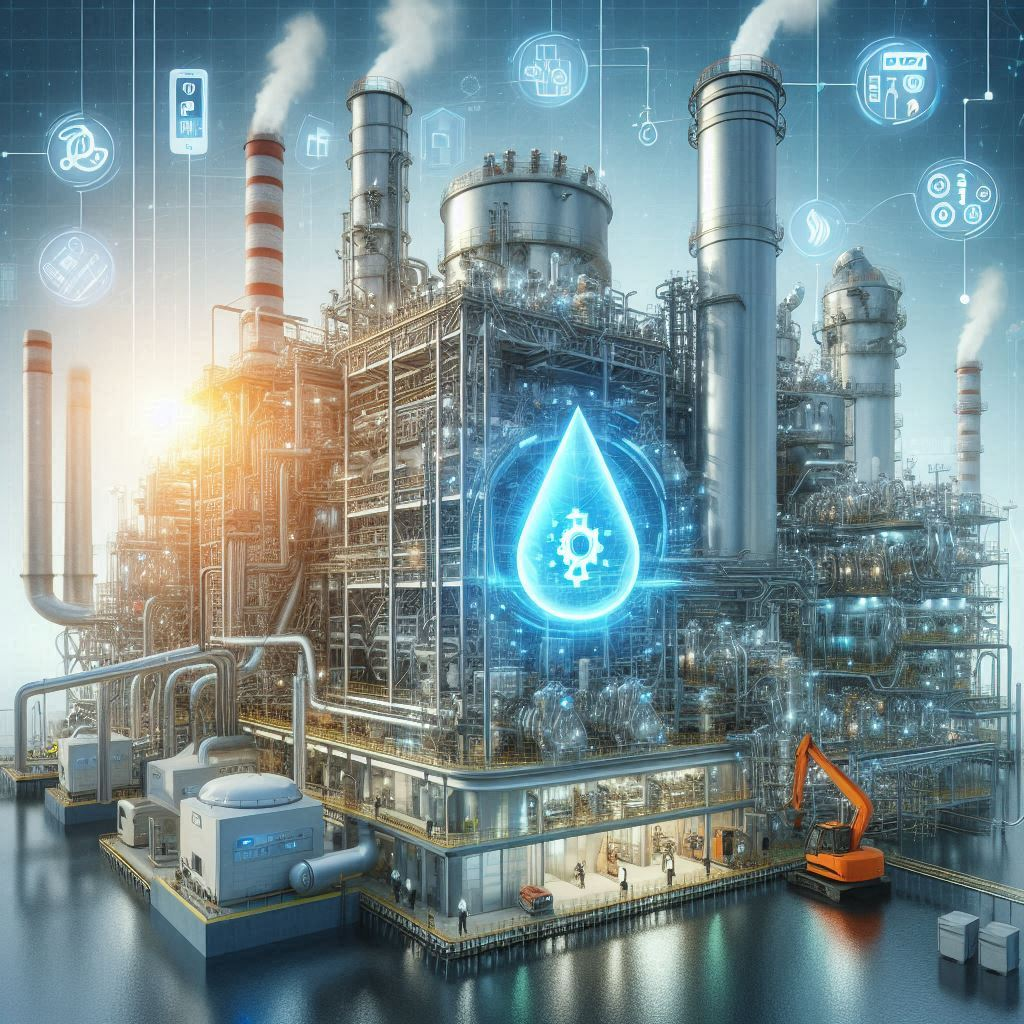
Dans le domaine du froid industriel et des installations de refroidissement process, la maintenance représente un poste de dépense majeur. L’intégration des technologies IoT (Internet des Objets) et de l’IA (Intelligence Artificielle) transforme les pratiques traditionnelles de maintenance, ouvrant la voie à des modèles prédictifs qui permettent de réduire considérablement les coûts et d’optimiser les opérations.
1. Les Défis des Systèmes de Refroidissement Process et Groupes Froids Industriels
Les systèmes de refroidissement sont essentiels dans de nombreux secteurs industriels (agroalimentaire, chimie, pharmaceutique, automobile) où un dysfonctionnement peut causer de graves conséquences, telles que des pertes de production, des dégradations de produits, ou des arrêts prolongés. Traditionnellement, les entreprises s’appuient sur des stratégies de maintenance corrective (réparation après panne) ou préventive (interventions planifiées), qui ont leurs limites :
- Maintenance Corrective : Coûteuse et risquée, car elle entraîne des arrêts imprévus et des perturbations majeures.
- Maintenance Préventive : Bien qu’elle soit planifiée, elle peut conduire à des interventions inutiles ou non optimisées, augmentant les dépenses sans certitude de bénéfices.
2. Le Concept de Maintenance Prédictive avec l’IoT et l’IA
La maintenance prédictive exploite les données collectées par les capteurs IoT installés sur les équipements pour anticiper les pannes avant qu’elles ne surviennent. L’IA analyse ces données en continu pour détecter les signes avant-coureurs de défaillances, permettant ainsi de planifier des interventions au moment optimal.
Principe de Fonctionnement :
- Collecte des Données : Des capteurs IoT mesurent des paramètres critiques tels que la température, la pression, les vibrations, le débit de fluide frigorigène, et les niveaux d’huile.
- Analyse en Temps Réel : L’IA traite ces données et identifie des anomalies ou des tendances indiquant une dégradation potentielle de l’équipement.
- Prédictions Précises : Des modèles de Machine Learning (apprentissage automatique) prédisent la probabilité de panne et estiment le moment idéal pour une intervention.
3. Avantages de la Maintenance Prédictive pour le Froid Industriel
- Réduction des Coûts de Maintenance : En évitant les interventions inutiles et en ciblant uniquement les composants qui en ont besoin, les coûts de maintenance sont significativement réduits.
- Diminution des Temps d’Arrêt : La maintenance prédictive permet de planifier les interventions lors des périodes de faible activité, réduisant ainsi les perturbations de la production.
- Allongement de la Durée de Vie des Équipements : Une surveillance continue permet d’identifier les dégradations à un stade précoce, prévenant les dommages qui peuvent réduire la longévité des machines.
- Optimisation de l’Utilisation des Ressources : Les équipes de maintenance peuvent se concentrer sur les tâches essentielles, améliorant leur productivité et réduisant la charge de travail liée aux urgences.
- Amélioration de l’Efficacité Énergétique : Un équipement en bon état consomme moins d’énergie, ce qui se traduit par une baisse des factures énergétiques et un impact environnemental réduit.
4. Technologies Utilisées dans la Maintenance Prédictive
Capteurs IoT : Des dispositifs connectés mesurent et transmettent des données en temps réel sur l’état des groupes froids. Voici quelques types de capteurs couramment utilisés :
- Capteurs de Température et Pression : Pour surveiller les conditions thermiques et assurer le bon fonctionnement du circuit de refroidissement.
- Accéléromètres pour la Surveillance des Vibrations : Utilisés pour détecter des déséquilibres ou des usures dans les compresseurs et les pompes.
- Détecteurs de Flux et de Débit : Pour vérifier que les fluides de refroidissement circulent correctement.
- Capteurs de Niveau d’Huile : Pour s’assurer que les niveaux sont adéquats, évitant ainsi l’usure excessive des composants mécaniques.
Analyse de Données par l’IA : L’IA et les algorithmes de Machine Learning interprètent ces données pour :
- Détecter des variations subtiles qui pourraient indiquer un problème futur.
- Créer des modèles qui s’améliorent au fil du temps pour des prédictions de plus en plus précises.
- Proposer des recommandations automatiques pour des interventions ou des réglages d’équipements.
5. Cas Concrets d’Application de la Maintenance Prédictive
- Industrie Agroalimentaire : Une entreprise de transformation alimentaire utilise des capteurs IoT pour surveiller ses chambres froides. L’IA détecte une augmentation progressive des vibrations du compresseur, signalant une usure anormale. Une intervention planifiée permet de remplacer les pièces défectueuses, évitant une panne qui aurait mis en péril des tonnes de produits alimentaires.
- Chimie et Pharmaceutique : Dans un site de production chimique, les variations de température dans les unités de refroidissement sont critiques. L’IA, analysant les données en temps réel, détecte des fluctuations inhabituelles de la pression de fluide frigorigène. Une maintenance ciblée est effectuée avant qu’une défaillance n’endommage les produits en cours de fabrication.
- Centres de Données : Les systèmes de refroidissement des data centers, essentiels pour maintenir une température optimale des serveurs, bénéficient de la maintenance prédictive. Les capteurs IoT surveillent les cycles de refroidissement, et l’IA ajuste les performances pour garantir la sécurité des infrastructures informatiques.
6. Impact sur l’Environnement et l’Efficacité Énergétique
Les systèmes de refroidissement sont gourmands en énergie, et leur impact environnemental est significatif. Grâce à l’IoT et à l’IA :
- Optimisation de la Consommation Énergétique : Les cycles de refroidissement sont ajustés en fonction des besoins réels, évitant les surconsommations.
- Réduction de l’Empreinte Carbone : Moins de pannes et une meilleure gestion de l’énergie se traduisent par une diminution des émissions de gaz à effet de serre.
- Gestion Responsable des Fluides Frigorigènes : Les fuites de fluides peuvent être détectées plus tôt, réduisant ainsi l’impact des gaz réfrigérants sur l’environnement.
7. Perspectives et Développements Futurs
Les solutions de maintenance prédictive continuent de s’améliorer avec l’intégration de nouvelles technologies. À l’avenir, on peut s’attendre à :
- Des Modèles de Prédiction de Plus en Plus Sophistiqués : L’IA continuera de s’améliorer grâce à l’apprentissage de volumes de données de plus en plus importants.
- Des Capteurs Encore Plus Précis : Les avancées dans les capteurs permettront de surveiller des paramètres jusque-là inaccessibles, augmentant la précision des diagnostics.
- Automatisation Complète : Les systèmes pourraient être capables de s’autocorriger, en ajustant automatiquement les composants pour prévenir des défaillances.
La maintenance prédictive transforme la gestion des groupes froids industriels et des installations de refroidissement process. Grâce à l’IoT et à l’IA, les entreprises peuvent anticiper les pannes, réduire les coûts de maintenance, optimiser l’efficacité énergétique, et prolonger la durée de vie de leurs équipements. Cela représente un investissement stratégique pour toute industrie cherchant à allier performance opérationnelle et développement durable.
Notre blog est une ressource complète pour tout ce qui concerne les fluides industriels. Nous vous encourageons à explorer nos articles, nos guides pratiques et nos ressources de formation pour approfondir vos connaissances et améliorer vos performances énergétiques. N’hésitez pas à nous contacter pour bénéficier de nos services d’ingénierie personnalisés ou pour trouver les produits dont vous avez besoin via notre site de commerce en ligne. Ensemble, nous pouvons aller plus loin dans l’apprentissage et réaliser des économies d’énergie significatives. Contactez-nous dès aujourd’hui à l’adresse suivante :
- Guide pour choisir un groupe froid industriel
- Le Guide Ultime du Choix des Compresseurs Frigorifiques : Optimisation, Puissance et Régulation
- Installation optimale de groupes froids industriels : Pratiques essentielles et paramètres clés
- Guide : La mise en service initiale d’un groupe froid industriel
- Les Applications du Refroidissement Industriel dans Divers Secteurs
- Guide Pratique pour le Choix d’un Groupe Froid Industriel : Calculs, Installations, Méthodes, Besoins et Critères Essentiels
- Optimiser l’Efficacité Énergétique : Deux Méthodes Ingénieuses pour Récupérer la Chaleur d’un Groupe Froid Industriel
- Guide Pratique : Récupération de Chaleur sur Groupe Froid – Avantages et Mise en Œuvre
- Innovations et Stratégies Avancées dans le Refroidissement Industriel: Vers une Ère Durable et Efficace
- Optimisation Cruciale: Les Répercussions d’un Réseau Industriel Mal Équilibré sur la Performance et la Sécurité
- Optimisation du Dimensionnement des Tuyauteries : Préserver la Pression et Réduire les Pertes de Charge
- Calculs et dimensionnement, installation, optimisation et Maintenance des Groupes Froids Industriels : Guide Complet pour Calcul de Puissance, Facteurs de Correction, et Technologies de Contrôle
- La conception d’un système de refroidissement industriel (Industrial Cooling System)
- FAQ : Groupes Froids Industriels et au Refroidissement Process
- Questions / réponses fréquemment posées sur le thème du refroidissement de process, incluant l’eau glacée, le froid industriel, les groupes froids, et les groupes d’eau glacée
- Quelles sont les erreurs courantes à éviter lors du choix d’un groupe froid industriel pour le refroidissement de son process ?
- Refroidissement Industriel : L’Essentiel sur les Groupes Frigorifiques et les Groupes d’Eau Glacée
- FAQ : Groupes Froids Industriels et au Refroidissement Process
- Groupe Froid Industriel et Durabilité : Vers une Utilisation Plus Écologique et Économe en Énergie
- Comment Choisir le Meilleur Fabricant de Groupes Froids, la technologie, les options … : Guide Complet
Lien pour achats :