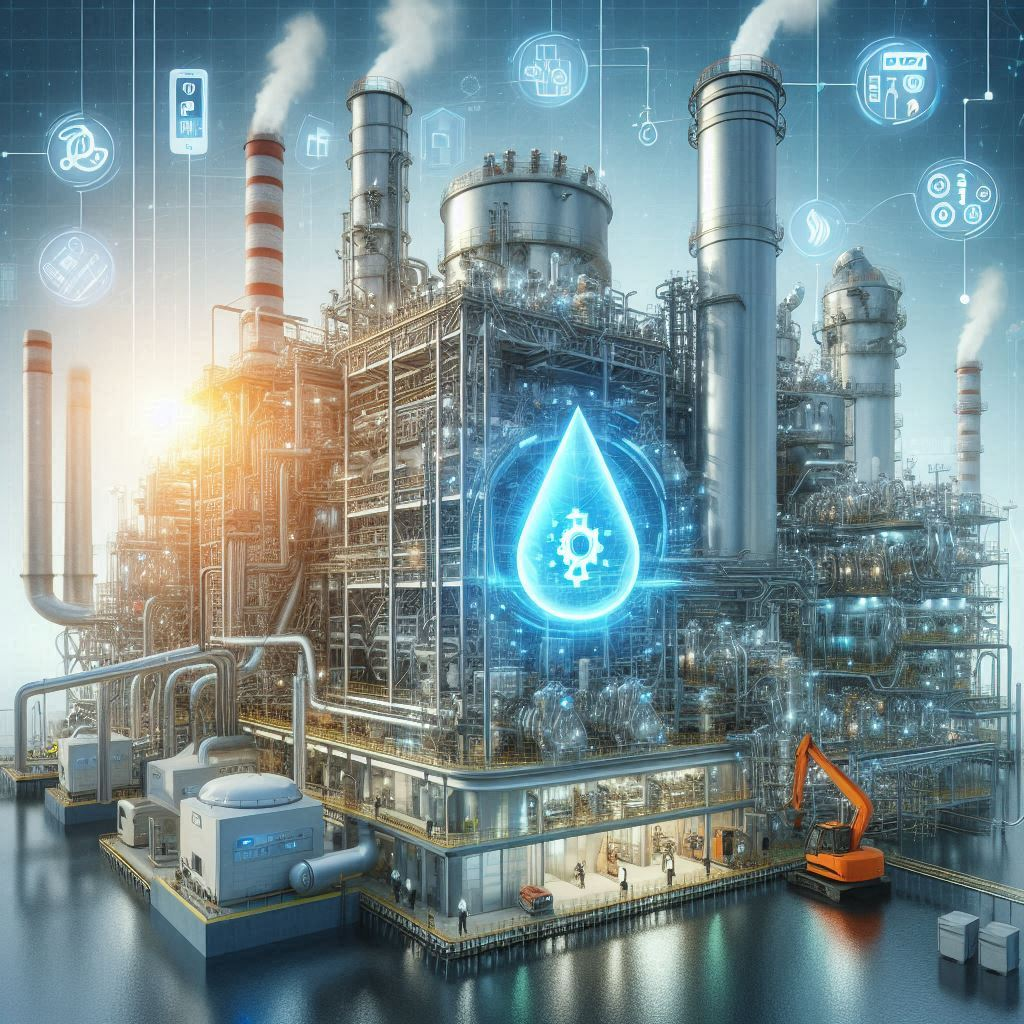
Les industries qui dépendent fortement des systèmes de refroidissement process et des groupes froids industriels font face à des défis constants en matière de maintenance. Deux approches principales se distinguent : la maintenance réactive et la maintenance prédictive. L’intégration de l’Internet des Objets (IoT) et de l’Intelligence Artificielle (IA) révolutionne cette dernière, offrant de nombreux avantages par rapport aux méthodes traditionnelles.
1. Définition des Approches de Maintenance
- Maintenance Réactive : Également appelée maintenance corrective, cette approche consiste à intervenir uniquement lorsqu’une panne ou un dysfonctionnement se produit. Autrement dit, la réparation est effectuée après qu’un problème a déjà impacté le système de refroidissement.
- Maintenance Prédictive : Basée sur l’analyse de données collectées en temps réel par des capteurs IoT, cette méthode vise à prévoir les pannes avant qu’elles ne surviennent. L’IA joue un rôle crucial en analysant les tendances et en générant des modèles prédictifs.
2. Fonctionnement de la Maintenance Réactive
La maintenance réactive repose sur une stratégie d’attente, ce qui signifie que les interventions ne sont effectuées que lorsque des problèmes se manifestent. Par exemple, un groupe froid industriel qui subit une panne doit être arrêté, ce qui entraîne des perturbations, des pertes de production, et des réparations coûteuses.
- Avantages :
- Simplicité : Moins de planification et de suivi sont nécessaires.
- Coûts initiaux réduits : Aucune infrastructure complexe de surveillance ou d’analyse n’est nécessaire.
- Inconvénients :
- Coûts élevés de réparation : Une panne complète peut causer des dommages importants nécessitant des pièces coûteuses et de longs délais de réparation.
- Temps d’arrêt imprévus : Les interruptions non planifiées de la production peuvent entraîner des pertes financières significatives.
- Durée de vie réduite des équipements : L’usure excessive due à l’absence de surveillance proactive peut raccourcir la durée de vie des machines.
3. Fonctionnement de la Maintenance Prédictive avec IoT et IA
La maintenance prédictive, quant à elle, repose sur une surveillance continue des équipements. Les capteurs IoT collectent des données telles que la température, la pression, les vibrations, et la consommation énergétique. L’IA analyse ces données pour anticiper les pannes potentielles, permettant ainsi des interventions ciblées avant que des dysfonctionnements graves ne se produisent.
- Avantages :
- Prévention des pannes : La détection précoce des signes de défaillance réduit considérablement les risques d’arrêt imprévu.
- Optimisation des coûts : En remplaçant les pièces avant qu’elles ne causent des dommages supplémentaires, les frais de réparation sont réduits.
- Efficacité énergétique : Une meilleure gestion des cycles de fonctionnement permet de réduire la consommation d’énergie.
- Augmentation de la durée de vie des équipements : Une surveillance proactive limite l’usure des systèmes de refroidissement.
- Planification efficace : La maintenance peut être planifiée de manière à minimiser l’impact sur la production, grâce à l’utilisation des périodes de faible activité.
- Inconvénients :
- Investissement initial : L’installation de capteurs IoT et le développement d’algorithmes d’IA nécessitent un investissement initial plus élevé.
- Formation requise : Les techniciens doivent être formés pour utiliser et interpréter les technologies avancées de surveillance et d’analyse.
4. Impact des Capteurs IoT sur la Maintenance Prédictive
Les capteurs IoT jouent un rôle essentiel dans la maintenance prédictive des groupes froids industriels et des systèmes de refroidissement process. Voici quelques exemples :
- Capteurs de Vibration : Ils détectent les changements dans les niveaux de vibration qui peuvent indiquer un désalignement des pièces mécaniques ou une défaillance des roulements.
- Capteurs de Température : Ils assurent que les températures sont maintenues dans des plages optimales, évitant ainsi les surchauffes qui pourraient causer des pannes.
- Capteurs de Pression : Ils surveillent les variations de pression dans les systèmes de réfrigération, permettant de détecter les fuites ou les anomalies de performance.
- Capteurs de Consommation Énergétique : Ils mesurent la consommation d’énergie en temps réel pour identifier des pics anormaux qui pourraient être le signe d’un dysfonctionnement.
5. Rôle de l’IA dans l’Analyse des Données Collectées
L’IA transforme les données collectées par les capteurs en informations exploitables. Les algorithmes de machine learning peuvent apprendre des tendances historiques et identifier les anomalies avant qu’elles ne conduisent à des pannes.
- Modélisation Prédictive : L’IA utilise des modèles pour prédire l’usure des composants et déterminer le moment optimal pour la maintenance.
- Analyse des Corrélations : En analysant les corrélations entre différents paramètres (par exemple, une augmentation de la température et des vibrations), l’IA peut identifier les causes profondes des problèmes.
- Optimisation des Opérations : L’IA ajuste automatiquement les paramètres de fonctionnement pour éviter des conditions de stress mécanique.
6. Études de Cas et Exemples Pratiques
- Industrie Pharmaceutique : Une installation de refroidissement pour la production de produits pharmaceutiques a intégré des capteurs IoT pour une surveillance continue. Grâce à la maintenance prédictive, ils ont pu réduire les arrêts non planifiés de 40 %, assurant une production continue et la qualité des produits sensibles à la température.
- Usine Agroalimentaire : Une usine de transformation alimentaire a utilisé des algorithmes d’IA pour prédire les défaillances de ses groupes froids. Cela a permis de réaliser des économies substantielles sur les coûts de réparation et de prolonger la durée de vie de leurs équipements de 15 %.
7. Quelle Approche Choisir ?
Bien que la maintenance réactive puisse sembler attrayante en raison de ses coûts initiaux plus bas et de sa simplicité, elle est risquée pour les installations critiques comme les systèmes de refroidissement industriel. La maintenance prédictive, bien que nécessitant un investissement initial plus important, offre des avantages significatifs en termes de réduction des coûts, d’augmentation de la durée de vie des équipements, et d’optimisation de l’efficacité énergétique.
L’intégration de l’IoT et de l’IA rend la maintenance prédictive non seulement réalisable mais aussi hautement rentable à long terme. Pour les industries qui souhaitent maximiser leurs performances tout en minimisant les risques et les coûts, l’avenir est clairement orienté vers une gestion proactive et intelligente des systèmes de refroidissement process et des groupes froids industriels.
Notre blog est une ressource complète pour tout ce qui concerne les fluides industriels. Nous vous encourageons à explorer nos articles, nos guides pratiques et nos ressources de formation pour approfondir vos connaissances et améliorer vos performances énergétiques. N’hésitez pas à nous contacter pour bénéficier de nos services d’ingénierie personnalisés ou pour trouver les produits dont vous avez besoin via notre site de commerce en ligne. Ensemble, nous pouvons aller plus loin dans l’apprentissage et réaliser des économies d’énergie significatives. Contactez-nous dès aujourd’hui à l’adresse suivante :
- Guide pour choisir un groupe froid industriel
- Le Guide Ultime du Choix des Compresseurs Frigorifiques : Optimisation, Puissance et Régulation
- Installation optimale de groupes froids industriels : Pratiques essentielles et paramètres clés
- Guide : La mise en service initiale d’un groupe froid industriel
- Les Applications du Refroidissement Industriel dans Divers Secteurs
- Guide Pratique pour le Choix d’un Groupe Froid Industriel : Calculs, Installations, Méthodes, Besoins et Critères Essentiels
- Optimiser l’Efficacité Énergétique : Deux Méthodes Ingénieuses pour Récupérer la Chaleur d’un Groupe Froid Industriel
- Guide Pratique : Récupération de Chaleur sur Groupe Froid – Avantages et Mise en Œuvre
- Innovations et Stratégies Avancées dans le Refroidissement Industriel: Vers une Ère Durable et Efficace
- Optimisation Cruciale: Les Répercussions d’un Réseau Industriel Mal Équilibré sur la Performance et la Sécurité
- Optimisation du Dimensionnement des Tuyauteries : Préserver la Pression et Réduire les Pertes de Charge
- Calculs et dimensionnement, installation, optimisation et Maintenance des Groupes Froids Industriels : Guide Complet pour Calcul de Puissance, Facteurs de Correction, et Technologies de Contrôle
- La conception d’un système de refroidissement industriel (Industrial Cooling System)
- FAQ : Groupes Froids Industriels et au Refroidissement Process
- Questions / réponses fréquemment posées sur le thème du refroidissement de process, incluant l’eau glacée, le froid industriel, les groupes froids, et les groupes d’eau glacée
- Quelles sont les erreurs courantes à éviter lors du choix d’un groupe froid industriel pour le refroidissement de son process ?
- Refroidissement Industriel : L’Essentiel sur les Groupes Frigorifiques et les Groupes d’Eau Glacée
- FAQ : Groupes Froids Industriels et au Refroidissement Process
- Groupe Froid Industriel et Durabilité : Vers une Utilisation Plus Écologique et Économe en Énergie
- Comment Choisir le Meilleur Fabricant de Groupes Froids, la technologie, les options … : Guide Complet
Lien pour achats :