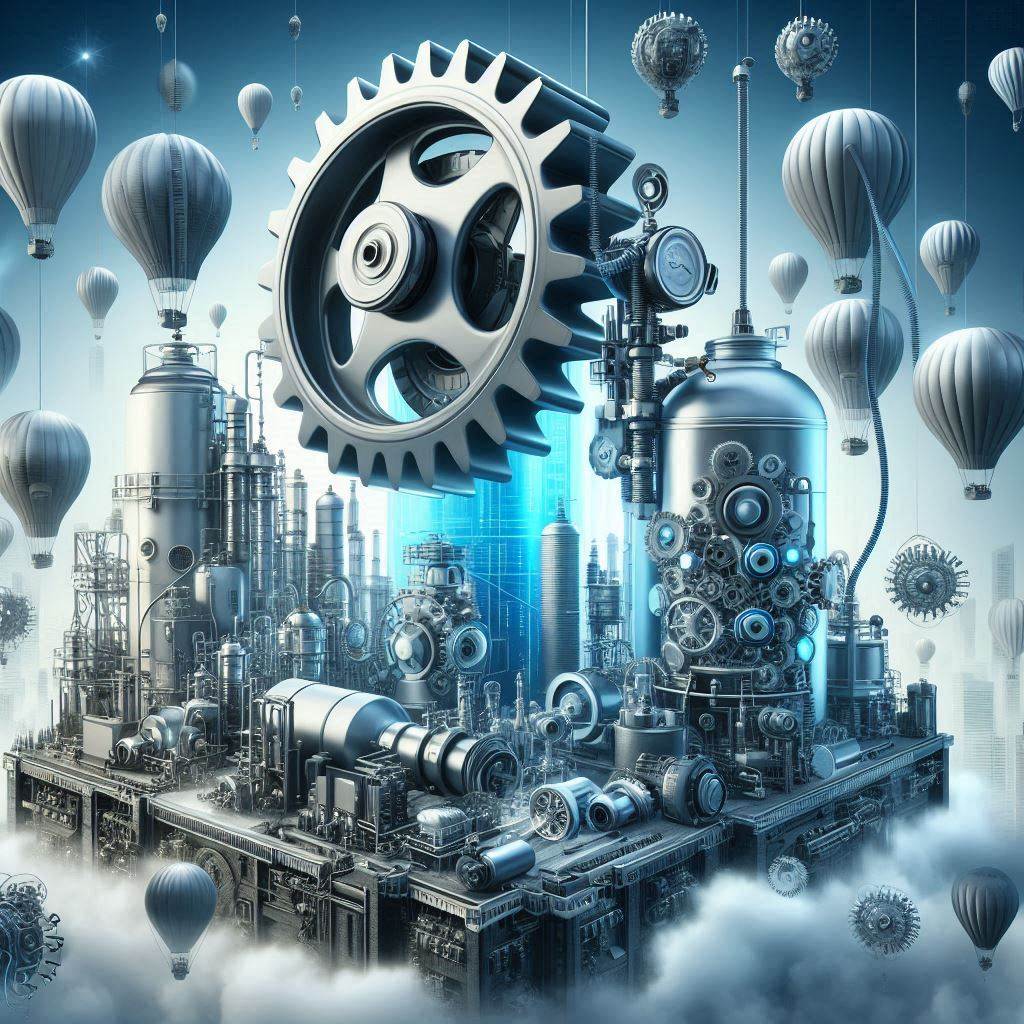
La conception d’un système d’air comprimé efficace et fiable suit un processus méthodique, impliquant plusieurs étapes clés. Voici un guide détaillé pour chaque étape, de l’analyse des besoins à la mise en service et aux tests.
1. Analyse des Besoins
Évaluation des Exigences en Matière de Débit, Pression et Qualité de l’Air :
- Débit d’Air : Mesurer le volume d’air nécessaire pour alimenter les équipements ou les processus de production. Cela inclut l’identification des pics de demande et des fluctuations dans l’utilisation.
- Pression de Travail : Déterminer la pression de travail requise pour chaque application spécifique. Assurer que la pression est suffisante pour les besoins des équipements sans dépasser les limites qui pourraient causer des fuites ou des dommages.
- Qualité de l’Air : Identifier les exigences de pureté de l’air, telles que les niveaux de particules, d’humidité et de contaminants (huile, bactéries, etc.). Des industries comme la pharmaceutique et l’alimentaire peuvent nécessiter un air de haute pureté.
2. Sélection des Équipements
Choix du Compresseur :
- Type de Compresseur : Sélectionner le type de compresseur (à piston, à vis, centrifuge, etc.) en fonction des besoins en débit et en pression.
- Compresseur à Vitesse Variable : Envisager l’utilisation de compresseurs à vitesse variable pour des économies d’énergie et une adaptation à la demande fluctuante.
Réservoirs de Stockage (Cuves) :
- Capacité : Dimensionner les réservoirs pour stocker suffisamment d’air comprimé et compenser les fluctuations de la demande.
- Positionnement : Placer les réservoirs pour optimiser la distribution de l’air comprimé et minimiser les pertes de pression.
Sécheurs et Filtres :
- Sécheurs : Choisir entre des sécheurs frigorifiques, à adsorption ou à membrane en fonction des exigences de déshumidification.
- Filtres : Installer des filtres à particules, à coalescence et à charbon actif selon les besoins en pureté de l’air.
Accessoires :
- Régulateurs de Pression : Maintenir une pression constante et prévenir les surpressions.
- Soupapes de Sécurité : Assurer la sécurité en relâchant l’excès de pression.
3. Conception du Réseau de Distribution
Planification des Conduites et des Raccords :
- Minimisation des Pertes de Charge : Utiliser des tuyaux de diamètre adéquat pour réduire les pertes de charge et assurer un débit constant.
- Matériaux des Tuyauteries : Sélectionner des matériaux résistants à la corrosion et à l’usure, comme l’acier inoxydable ou l’aluminium.
- Dispositifs de Raccordement : Prévoir des raccords rapides et des points de purge pour faciliter l’entretien et la maintenance.
Disposition des Conduites :
- Optimisation de l’Espace : Planifier le réseau de tuyauterie pour optimiser l’espace et faciliter l’accès pour la maintenance.
- Réduction des Vibrations : Utiliser des supports antivibrations pour réduire le bruit et l’usure des tuyaux.
4. Évaluation Économique
Analyse des Coûts Initiaux et Opérationnels :
- Coût d’Installation : Calculer le coût d’achat et d’installation des compresseurs, des réservoirs, des sécheurs, des filtres et des conduites.
- Coût de Fonctionnement : Estimer les coûts énergétiques et les dépenses liées à la maintenance régulière et aux réparations éventuelles.
- Retour sur Investissement (ROI) : Analyser le ROI en considérant les économies d’énergie potentielles, la réduction des temps d’arrêt et l’amélioration de l’efficacité opérationnelle.
5. Mise en Service et Tests
Installation :
- Montage des Équipements : Installer tous les composants selon les plans de conception, en respectant les recommandations des fabricants.
- Connexion des Conduites : Assembler le réseau de distribution de manière à minimiser les fuites et les pertes de pression.
Tests de Performance et Ajustements :
- Tests de Fuites : Vérifier l’étanchéité des connexions et des joints pour éviter les pertes d’air.
- Mesures de Débit et de Pression : Confirmer que le débit et la pression correspondent aux spécifications requises.
- Qualité de l’Air : Tester la pureté de l’air comprimé pour s’assurer qu’elle répond aux normes établies.
- Ajustements Fins : Ajuster les régulateurs, les sécheurs et les filtres pour optimiser les performances du système.
La conception d’un système d’air comprimé efficace implique une analyse détaillée des besoins, une sélection rigoureuse des équipements, une planification précise du réseau de distribution, une évaluation économique complète, et une mise en service suivie de tests rigoureux. En suivant ces étapes, il est possible de concevoir un système qui répond aux exigences spécifiques du client tout en garantissant une performance optimale et une rentabilité à long terme.
En somme, l’ingénierie des fluides industriels est une discipline importante et diversifiée qui joue un rôle clé dans de nombreuses industries. Elle nécessite une expertise technique et une connaissance approfondie des systèmes de circulation des fluides, de la thermodynamique, de la mécanique des fluides, de la régulation et du contrôle des processus, ainsi que de la sécurité.
Notre blog est une ressource complète pour tout ce qui concerne les fluides industriels. Nous vous encourageons à explorer nos articles, nos guides pratiques et nos ressources de formation pour approfondir vos connaissances et améliorer vos performances énergétiques. N’hésitez pas à nous contacter pour bénéficier de nos services d’ingénierie personnalisés ou pour trouver les produits dont vous avez besoin via notre site de commerce en ligne. Ensemble, nous pouvons aller plus loin dans l’apprentissage et réaliser des économies d’énergie significatives. Contactez-nous dès aujourd’hui à l’adresse suivante :
Guide Ultime pour Choisir le Compresseur d’Air Comprimé Idéal- Guide Pratique pour la Mise en Service des Compresseurs d’Air Comprimé : Astuces et Bonnes Pratiques
- FAQ sur l’Air Comprimé : Optimisez Votre Énergie, Votre Fiabilité et Votre Productivité
- FAQ : foire aux questions spécifiques sur les cuves d’air comprimé
- FAQ : Sécheurs d’Air Comprimé à Détente Directe
- FAQ : Sécheurs d’Air Comprimé à Masse Thermique
- FAQ : Sécheurs d’Air Comprimé par Adsorption
- Configurations de Montage pour Compresseurs d’Air Comprimé : Optimisation, Performance et Intégration
- Guide Complet : Pourquoi de l’Eau Apparaît Lors de l’Utilisation de l’Air Comprimé et Comment Résoudre Ce Problème
- Guide complet pour choisir et dimensionner un compresseur comprimé : Méthodes, Besoins et Critères Essentiels (piston-s, vis, palettes, centifuge, )
- Guide complet pour choisir et dimensionner un sécheur d’air comprimé : Méthodes, Besoins et Critères Essentiels
- Guide Avancé pour la Sélection des Filtres d’Air Comprimé : Approche Technique, Scientifique et Pédagogique
- Guide Pratique pour le Choix d’une Cuve d’Air Comprimé : Matériau, Pression, Durée de Vie et Capacité
- Guide de Choix pour Purgeurs d’Air Comprimé : Économie d’Énergie et Gestion des Fuites
- Guide Complet pour Choisir et Dimensionner un Réseau d’Air Comprimé : Méthodes, Besoins et Critères Essentiels
- Optimiser l’Énergie : Deux Approches Innovantes pour Récupérer la Chaleur d’un Compresseur d’Air Comprimé
- Optimisation du Réseau d’Air Comprimé : Les Clés d’un Dimensionnement Stratégique
- Choisir le Diamètre Idéal pour Votre Tuyau d’Air Comprimé selon pression : Un Guide Technique Approfondi
- L’Impact des Fuites d’Air Comprimé sur le Débit : Guide Pratique
- Traitement air comprimé / Optimisation de la Qualité de l’Air Comprimé : Guide Complet
- Pourquoi l’eau peut être un problème dans un réseau air comprimé ?
- Traitement écologique et la gestion des condensats d’air comprimé
- Maîtrisez l’Air Comprimé : 10 Astuces pour Optimiser son Utilisation et Réduire les Coûts dans Votre Entreprise
- Comment Réduire les Pertes d’Énergie dans Votre Système de Distribution d’Air Comprimé
- Guide pour Choisir le Sécheur d’Air Comprimé Idéal pour Votre Entreprise
- Sécurité de l’Air Comprimé : Risques, Prévention et Protection
- Guide Essentiel de l’Air Comprimé : Questions Clés Répondues
- Les causes courantes de panne des sécheurs d’air comprimé?
- Mesurer le point de rosée sous pression dans votre système d’air comprimé est crucial pour garantir la qualité de l’air et prévenir les problèmes liés à l’humidité
- Guide ultime pour réparer votre compresseur d’air : Défauts courants, remèdes efficaces et conseils de maintenance
- La sélection du bon raccord rapide air comprimé
- Optimisation Cruciale: Les Répercussions d’un Réseau Industriel Mal Équilibré sur la Performance et la Sécurité
- L’Air Comprimé : Le Pouvoir Invisible au Cœur des Technologies Avancées et des Applications Insolites
- Les Applications et Innovations des Systèmes d’Air Comprimé dans l’Industrie : Guide Complet
Lien pour achats :